Multi Spindle Machining Of Precision Parts
Definition Of Multi-Spindle Cnc Machining
Multi-axis machining should be defined as multi-axis coordinated machining. At present, most of the controlled processing equipment can achieve up to five-coordinate linkage. There are many types of such equipment, and the structure types and control systems are different.
Multi-axis Cnc machining Center can control the linkage of more than 4 coordinate axes at the same time, combining functions such as CNC milling, CNC boring, and CNC drilling. After the workpiece is clamped at one time, the machining surface can be milled, bored, and drilled. Processing effectively avoids positioning errors caused by multiple installations, can shorten the production cycle, and improve processing accuracy.
Multi-spindle machining & machined parts customers looking for turnaround speed and cost efficiency choose PTJ Shop for one primary reason: complete confidence that PTJ will deliver multi-spindle machined products & components on schedule.
|
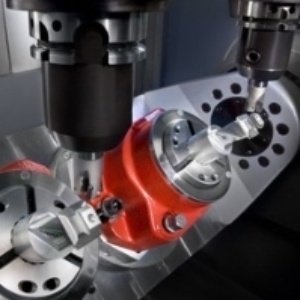
|
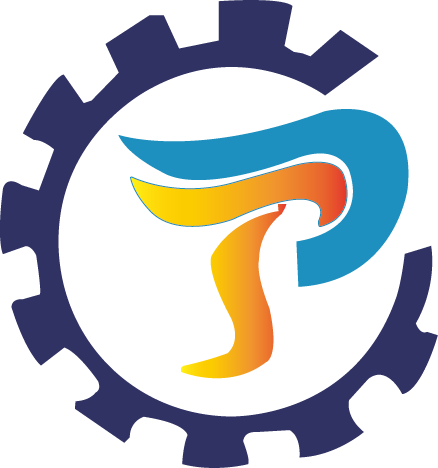
|
Multi-Spindle Machining Advantages
|
Customers have the choice of many multi-spindle screw machine companies, but they depend on PTJ Shop machining advantage for shortage-free delivery every day, year in and year out.
1.Reduce reference conversion and improve machining accuracy
The integration of multi-axis CNC machining process not only improves the effectiveness of the process, but because the parts only need to be clamped once in the entire machining process, the machining accuracy is more easily guaranteed.
2.Reduce the number of fixtures and minimized space requirements
Although the cost of a single device for a multi-axis CNC machining center is higher, due to the shortening of the process chain and the reduction in the number of equipment, the number of tooling fixtures, workshop floor space and equipment maintenance costs also decrease.
3.Shorten the production process chain and simplify production management
The complete processing of multi-axis CNC machine tools greatly shortens the production process chain, and because only the processing task is assigned to one job, it not only simplifies production management and scheduling, but also significantly improves transparency. The more complex the workpiece, the more obvious its advantages over traditional production methods with decentralized processes. At the same time, due to the shortening of the production process chain, the number of work in process must be reduced, which can simplify production management, thereby reducing the cost of production operations and management.
4.Shorten the development cycle of new products
For enterprises in the aerospace, automotive and other fields, some new product parts and molding dies have complex shapes and high precision requirements. Therefore, multi-axis CNC machining centers with high flexibility, high precision, high integration and complete machining capabilities can It can well solve the problems of precision and cycle of complex parts processing in the process of new product development, greatly shorten the development cycle and improve the success rate of new products.
View our full multi spindle equipment list here
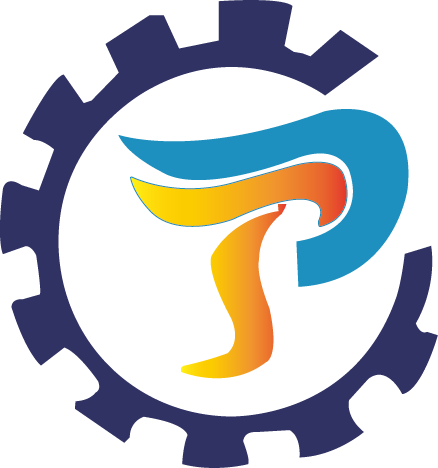
|
Major Multi-Spindle Machining Methods
|
To see for yourself how PTJ's multi-spindle screw machining capabilities can put supply chain concerns safely to rest on your next multi-spindle job, contact us to order a trustworthy cost estimate. The methods include:
▶ 3-axis cnc machining
▶ 4-axis cnc machining
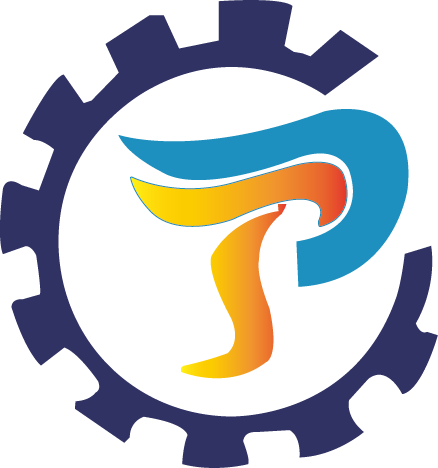
|
Certifications & Quality Machining
|
PTJ Shop meets or exceeds the quality standards of the world's most demanding industries with our state of the art equipment and trained professionals. A few of them include:
1.ISO 9001:2015 certified
2.Fully compliant with the exacting requirements of our customers
3.Compliance in DFARS materials sourcing requirements
4.Strict compliance with PPAP and Process FMEA for automotive customers
5.Skilled in KanBan and other customer driven quality and inventory management systems
6.ITAR Registered
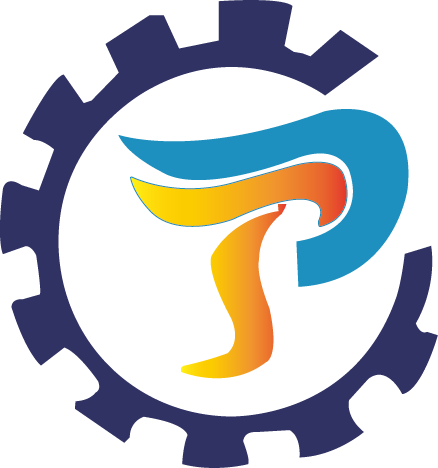
|
Common Custom Types of Multi Spindle Precision Machining
|