Use gradient structure to improve the mechanical properties of metal materials
Due to the insufficient dislocation storage capacity of nano-metal materials, the material necks prematurely due to lack of work hardening during deformation, which leads to the tensile brittleness of nano-metal materials. In order to improve the material's work hardening ability and eliminate the local stress concentration in the nanocrystalline grains, materials scientists have designed a gradient structure, that is, a layer of nanocrystalline is covered on the coarse-grained matrix, and they are filled with transition-sized grains.
The advantage of this structure is that the coarse grains store dislocations and provide plastic deformation, while the nano grains can be used as a "second phase" to strengthen the material. However, this conceptual structure poses a severe challenge to the actual processing technology. For a while, materials scientists even thought that the gradient structure material could not be prepared. In 2011, Academician Lu Ke of the Shenyang Institute of Metals successfully prepared a gradient nano-metal Cu material, which showed super tensile properties, and published the results in the Science journal. For a time, there was a wave of heated discussions, and "Nature" magazine even commented that "results have been made in areas where success is impossible." Since then, gradient materials have been continuously synthesized and proved to have good mechanical properties. Now! The author takes you to sort out the results of gradient materials published in first-class journals in recent years.
In fact, in 2002, the scientist Yinmin Wang of Johns Hopkins University and others designed a "bimodal structure" in aluminum alloy. By controlling the grain size, the use of small nano grains to provide strengthening effect, the larger Nanocrystals or ultrafine crystals provide the ability to store dislocations, and realize the simultaneous improvement of strength-plasticity and toughness. This article can be used as the enlightenment of the gradient structure, but it is not difficult to find that the "bimodal organization" mechanism still improves the plastic toughness at the expense of strength, and essentially has not changed the contradictory relationship between strength-plasticity/toughness, but its design philosophy It is more ingenious. In practice, it is necessary to correctly grasp the "degree" of introducing a larger number of crystal grains. The advantage of this design concept is that the grains of different gradients can complement each other and give play to their respective strengths.
This article is the first report of the Lu Ke group on gradient nano-metal materials. In nano-metal materials, the dislocation slip required for plastic deformation of the material is suppressed, and grain boundary migration and diffusion creep are the main mechanisms. , These two mechanisms cannot fully satisfy the plastic deformation. Previous studies reported that if the stress concentration of nano-metal can be suppressed, its plasticity can be improved. They used surface grinding technology to successfully synthesize gradient nano-metal copper, the microstructure of which is that nano-crystalline grains are surrounded by coarse-grained grains, with transition-size grains in the middle. Tensile experiments show that gradient nano-metallic copper exhibits 10 times the tensile strength of coarse-grained copper, but its plasticity does not decrease, and the true tensile strain is maintained to exceed 100% without cracks. Through TEM and other characterization, they found that grain boundary migration accompanied by grain growth is the deformation mechanism of gradient nano-metal copper. Figure 2 shows the microstructure and tensile curve of the material. The unique inherent plasticity of the gradient NG structure provides potential for optimizing the comprehensive mechanical properties of bulk materials. Once the article was published, it aroused heated discussions in the scientific community. At first everyone thought that gradient nanomaterials were difficult to achieve in real processes. Later everyone started to follow suit. At the 2015 Material Society Fall Conference in the United States, the participating experts specially set up A branch to discuss "Gradient Nanostructured Materials".
This article is a review of gradient nanomaterials written by Academician Lu Ke by the journal "Science" in 2014. This article summarizes the reasons for the brittleness of nanometal materials at room temperature and the principle of using gradient structures to enhance toughness (Figure 2 ). The author will not repeat the introduction one by one here, and interested readers can consult this document.
The increase in metal strength comes at the expense of its ductility, that is, the process of homogeneous plastic deformation or refinement of coarse-grained metals into nano-crystalline grains follows the typical "banana-shaped" curve (blue line). The random mixing of coarse particles and nanoparticles also has similar strength-ductility constraints. However, the simultaneous enhancement of strength-ductility is achieved through a gradient nanoparticle (GNG) structure (red line).
After Academician Lu Ke published an article in "Science", Wei Yujie and others from the Institute of Mechanics of the Chinese Academy of Sciences introduced a gradient structure in high manganese steel, breaking the relationship of strong plasticity in material science. By twisting the high-strength twin-induced plasticity steel (TWIP steel), they synthesized a gradient nano-twin structure in the radial direction. Through tensile experiments, they found that the yield strength of the steel was increased by nearly 2 times, but the plasticity was not Decrease (see figure 4). The breaking of this strong plasticity constraint relationship is caused by the gradient twin structure formed during the stretching process after torsion. This paper also uses the finite element simulation calculation of crystal shaping to further clarify the mechanism of the gradient twin structure breaking the mutual restraint of strong plasticity and how torsion and stretching activate the twin system and form a gradient nano twin structure. This achievement has successfully applied the gradient structure to steel, which is commonly used in daily life and low-cost metal materials, which has important enlightenment significance.
Although nano-metal materials have many excellent properties, such as strength, hardness, shear resistance and other mechanical properties. However, nanocrystalline does not guarantee that the material has good plasticity and fatigue properties. Academician Lu Ke studied the fatigue properties of nano-gradient copper after studying the tensile properties. Research shows that compared with coarse-grained copper, the fatigue strength and fatigue life of nano-gradient copper are greatly improved, and the improvement of fatigue performance is mainly attributed to the surface layer of the material. The microscopic characterization experiment proved that cyclic deformation caused abnormal grain coarsening. This coarsening started from below the surface layer and grew to the top surface layer along the 45° direction of the surface layer. The top surface layer was where the fatigue cracks formed. The study also proposed a new type of dynamic recrystallization model.
The gradient structure of the material also has the advantage of maximizing its physical and mechanical properties while ensuring low cost. XiaoLei Wu and others from the Institute of Mechanics of the Chinese Academy of Sciences introduced a gradient structure in seamless steel through surface mechanical friction treatment. Its microstructure is characterized by a layer of coarse crystals sandwiched between two shaved layers, and the grains of the gradient layer gradually change from 0.5μm to 1μm. During the transition, the dislocation cells and sub-crystals in between are less than 100 nm, and the total thickness of the gradient layer is 120 μm. Through uniaxial tensile experiments, they found a unique work hardening phenomenon in gradient materials, resulting in high plasticity. The study found that under uniaxial stretching, the gradient structure can induce strain gradients and transform uniaxial stress into multiaxial stress. Axis stress. Therefore, dislocation accumulation and interaction occur within the grains, resulting in additional strain hardening and a significant increase in strain hardening rate. This unusual strain hardening is inherent to the gradient structure and does not exist in homogeneous materials. It provides a hitherto unknown strategy to develop strong and tough materials by constructing non-uniform nanostructures.
This article is another high-level paper on gradient nano-copper published by the academician Lu Ke. Through surface friction treatment, the sample was successfully synthesized, and its crystal grain gradually grew from 20nm on the surface to the centimeter level. Generally speaking, due to the crystal The driving effect of the boundary, the nanocrystalline grains will be coarsened during the plastic deformation process. As the grains grow, the coarsening effect gradually stops. In fact, in the coarse-grained materials, plastic deformation is generally used to refine the grains. The method. In this article, Lu Ke's group first conducted a stretching experiment, and proved by TEM and other means that the grains below 165nm will coarsen during the stretching process, that is, stretching induces softening. When the grain size is greater than 165 nm, hardening is induced. The constant hardness observed at a depth of 90 μm from the surface may also mean constant dislocation density and increased strain. This saturated dislocation density can be regarded as the maximum dislocation density stored in the metal from plastic deformation to high strain under certain deformation conditions.
The relationship between the microstructure and the grain size as a function of the depth from the surface; the relationship between the hardness and the depth after the sample is stretched
In this article, A K Soh and others of the University of Hong Kong combined finite element simulation and theoretical analysis to systematically study the effect of grain gradient on the plasticity of nanocrystalline materials. The study found that if the thickness of the gradient and the grain size of the uppermost phase are optimized, nanocrystals can have the plasticity of coarse grains and at the same time have higher strength. This paper establishes the relationship between the thickness fraction of the grain gradient region and the grain size of the uppermost phase, which provides a design basis for preparing nanocrystalline materials with a good balance of strength and ductility. It is worth mentioning that the model established in this paper has certain shortcomings. In the calculation, they assume that the deformation of nanocrystalline materials obeys power law hardening, but power law hardening is not sufficient to accurately describe the work hardening behavior of metals in the large strain stage. , Its model does not consider the grain growth process during the tensile test.
Link to this article: Use gradient structure to improve the mechanical properties of metal materials
Reprint Statement: If there are no special instructions, all articles on this site are original. Please indicate the source for reprinting:https://www.cncmachiningptj.com
PTJ® provides a full range of Custom Precision cnc machining china services.ISO 9001:2015 &AS-9100 certified.
Machining shop specializing in fabrication services for construction and transportation industries. Capabilities include plasma and oxy-fuel cutting, Tailored machining, MIG and Custom Aluminum Cnc Precision Milling Welding Jig Fixture, roll forming, assembly, Lathe machining stainless steel cnc machine shaft, shearing, and CNC Swiss Machining services. Materials handled include carbon and Passivation Stainless Steel Machining Cover Plate Parts.
Tell us a little about your project’s budget and expected delivery time. We will strategize with you to provide the most cost-effective services to help you reach your target,You are welcome to contact us directly ( sales@pintejin.com ) .
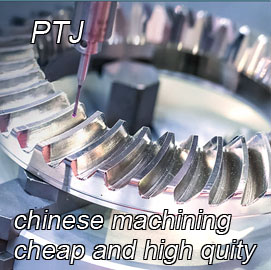
- 5 Axis Machining
- Cnc Milling
- Cnc Turning
- Machining Industries
- Machining Process
- Surface Treatment
- Metal Machining
- Plastic Machining
- Powder Metallurgy Mold
- Die Casting
- Parts Gallery
- Auto Metal Parts
- Machinery Parts
- LED Heatsink
- Building Parts
- Mobile Parts
- Medical Parts
- Electronic Parts
- Tailored Machining
- Bicycle Parts
- Aluminum Machining
- Titanium Machining
- Stainless Steel Machining
- Copper Machining
- Brass Machining
- Super Alloy Machining
- Peek Machining
- UHMW Machining
- Unilate Machining
- PA6 Machining
- PPS Machining
- Teflon Machining
- Inconel Machining
- Tool Steel Machining
- More Material