One article to understand the main players in the domestic 3D printing field
What is 3D printing?
3D printing is another term for additive manufacturing. It is an emerging manufacturing technology that builds physical objects by stacking materials layer by layer based on digital models. Additive manufacturing can save manufacturing materials and processing time, produce a variety of shapes, and realize individualization and customization of manufacturing. Additive manufacturing has realized the transformation of manufacturing methods from equivalent materials, subtractive materials to additive materials, and has changed the traditional manufacturing process, production lines, factory models, and industrial chain combination. It is considered to be a highly representative disruptive technology in the manufacturing field.
In order to seize opportunities for additive manufacturing technology and industrial development, many countries and regions have listed it as a key development direction and formulated relevant plans and supporting policies.
The 3D printing industry can be divided into 3D printing materials, 3D printing equipment, 3D printing services, and 3D printing applications according to the upper, middle and lower reaches. According to the 3D printing materials, it can be divided into two categories: metal 3D printing and non-metal 3D printing; according to the difference in application, it can be divided into industrial-grade 3D printing and special printing.
In this industry map, we split the entire 3D printing industry into two major categories: metal 3D printing and non-metal 3D printing, and take the relevant printing technology and application scope as sub-items to take stock of the corporate structure of the entire market.
Metal 3D printing
1. Metal 3D printing materials
Different from ordinary materials, 3D printing materials need to be prepared using unique technologies to meet the special requirements of 3D printing products and 3D printing equipment for materials. Depending on the 3D printing technology used and the purpose of the manufactured parts, the required materials are also different.
Metal 3D printing materials are mainly metal powders, and the main materials include cobalt-based alloys, stainless steel, tool steel, die steel, nickel-based alloys, titanium and titanium alloys, and various aluminum alloys.
According to relevant data analysis reports, the scale of 3D composite printing materials in the future market will continue to increase, and the application of metal materials will also increase year by year. It is estimated that composite materials are expected to reach 111 million US dollars in 2022, and the market size of 3D printing metal materials will also reach 8 Billion US dollars, the R&D and production of metal materials will have a broader market space.
In the field of metal 3D printing materials, some companies only provide professional materials for specific fields. For example, "Aviation Matt", the main business is the research and development and production of aerospace metal 3D printing powder materials, with an annual production capacity of at least 1,000 tons; and "Rongtian Aviation Equipment" is an agent of aviation 3D printing metal powders from the United States and Europe. .
More manufacturers are producing general-purpose metal powder products. For example, "Nalian Materials" produces base alloys, stainless steel, tool steel, die steel, nickel-based alloys, titanium and titanium alloy metal powder materials that are suitable for SLM, EBM, DED and other technologies. In addition, some of them are equipped with printing equipment and materials. The company will be discussed below.
2. Metal 3D printing equipment
The mainstream metal 3D printing technologies now include laser selective melting (SLM), laser near net shaping (LENS) and electron beam selective melting (EBSM) technology, direct energy deposition (DED) technology, and electron beam fuse deposition (EBDM).
(1) Laser selective melting (SLM)
SLM is currently the most common technology in metal 3D printing and its working principle is: the computer converts the three-dimensional data of the object into layered cross-sectional 2D data and transmits it to the printer. During the printing process, the setting is laid on the substrate with a squeegee. Layer-thick metal powder, the focused laser scans according to the pre-planned path and process parameters under the control of the scanning galvanometer. The metal powder is melted under the irradiation of the high-energy laser and solidified rapidly to form a metallurgical bonding layer. When the printing task of one layer is finished, the substrate is lowered by a height of the slice layer thickness, and the squeegee continues to carry out powder leveling, laser scanning processing, and this process is repeated until the entire part is printed.
The advantage of this technology is that it can be widely used in the mass production of metal parts with complex shapes, and most metal powders are suitable for this technology, including titanium alloys, aluminum alloys, high temperature alloys, copper alloys, cobalt-chromium alloys, stainless steel, high-strength Steel, die steel, etc., the obtained parts are nearly 100% dense.
(2) Other metal 3D printing technology
LENS (Laser Engineered Net Shaping) is a laser cladding deposition technology based on synchronous powder feeding. The laser beam moves according to a preset path under the control; at the same time, the powder nozzle delivers the metal powder directly to the laser spot , Make it solidify in the order from point to line and line to surface, so as to complete the printing work of one layer of cross-section, so that layer by layer is superimposed to produce a nearly-net-shaped part entity. Printers using this technology are usually mixed with corresponding CNC milling units.
Electron beam selective melting (EBSM/EBM) is a process of manufacturing 3D metal parts by layer-by-layer deposition using electron beam scanning and melting powder materials in a vacuum environment. Compared with SLM technology, the processing efficiency is higher and the cost is lower, but the technology The difficulty is relatively higher.
Non-metallic 3D printing
1. Non-metallic 3D printing materials
There are currently more than 1,000 materials that can be used for 3D printing, most of which are non-metallic materials. Non-metal 3D printing mainly uses polymer materials, including synthetic polymer materials, such as polylactic acid (PLA), polyethylene glycol (PEG), polyethylene terephthalate-1,4-cyclohexane Dimethanol ester (PETG), poly-hydroxyvalerate (PHBV), polybutanediol succinate (PBS), polycaprolactone (PCL) and photosensitive resin, etc.; thermoplastic polymer materials, such as PC, ABS-M30i, nylon, PEEK, etc.; natural polymer materials, such as alginate, collagen, fibrinogen, gelatin, extracellular matrix, agarose, dextran, glucose, sucrose, chitosan, etc.
The processor will select materials with different properties according to different 3D printing technical characteristics and application product requirements. In the market, there are also many companies specializing in the development and production of 3D printing materials.
At present, FDM (Fused Deposition Modeling) is the lowest cost and most widely used 3D printing technology on the market. The FDM process uses filamentous materials and can be processed in a variety of materials, including polycarbonate and engineering plastics. And the mixed materials of the two, etc. Therefore, there are also companies that develop materials specifically for FDM companies.
In addition to the FDM process, DLP and SLA technologies are also two important processes in non-metal 3D printing (the specific technical description will be expanded later), and the consumables they use are photosensitive resins. The manufacturing process difficulty and cost of these materials are relatively high, and high-quality liquid photosensitive resin still depends on imports and needs to be imported from abroad. In addition to these mainstream materials, there are also companies that have set their sights on specialty materials
2. Non-metallic 3D printing equipment
The mainstream non-metal 3D printing technologies now include: fusion molding (FDM), three-dimensional light curing molding technology (SLA), digital light projection technology (DLP), non-metal laser powder sintering (SLS).
(1) Deposition molding method (FDM)
Fused Deposition Modeling (FDM, Fused Deposition Modeling) is a process that extrudes filamentous materials such as thermoplastics, wax or metal fuses from a heated nozzle, and fixes them according to the predetermined trajectory of each layer of the part. Rate of melt deposition. The main purpose is the manufacture of plastic parts, wax patterns for casting, samples or models. However, compared with several other processes, the machining accuracy is low and the time is longer.
FDM does not use lasers, is simple to use and maintain, and has low cost. It can meet the DIY requirements of consumer-level customers, as well as the low-cost parts manufacturing and model manufacturing requirements of enterprises. In addition to consumer desktop printers, more companies are targeting the FDM industrial 3D printing market.
(2) Three-dimensional light curing (SLA) and digital light processing (DLP)
The working principle of three-dimensional light curing (SLA) is to use a laser beam to outline the shape of the first layer of the object on the surface of the liquid resin, and then the production platform is lowered a certain distance (between 0.05-0.025mm), and then the cured layer is immersed in the liquid resin In, so repeatedly. The resin used is photosensitive resin, which will form a solid state after being irradiated with a laser beam.
The consumables used in digital light processing (DLP) technology are light-curable resins, just like SLA. The biggest difference between DLP and SLA is that DLP uses the digital light source of the projector, while SLA uses the laser head. Because of this, DLP scans one piece, and SLA shaping can only rely on one laser point.
Compared with FDM, the main advantage of light curing technology is higher accuracy and faster speed.
At present, 3D printing companies are still facing the dilemma of higher costs and more difficult profitability. A large part of the reason is that the printing speed is difficult to keep up, and the efficiency is low. As a result, printing solutions that take into account accuracy and increase speed have begun to attract more and more attention, and some companies have innovated the traditional light curing technology to achieve the goal of faster speed.
(3) Other non-metallic 3D printing technologies
SLS is called powder sintering in the industry, and its available materials include polymers, metals, ceramics, gypsum, nylon and other powder materials.
In nylon 3D printing, "Huashu Hi-Tech" is the leading company with more than 280 employees, including more than 40% of R&D personnel. The company has applied for more than 100 patents and obtained nearly 100 patent authorizations. At the same time, it is researching and developing metal 3D printing. Equipment and polymer 3D printing materials such as nylon. In addition, the company is also involved in the field of metal 3D printing.
The 3DP process is similar to the SLS process, using powder materials such as ceramic powder and metal powder. The difference is that the material powder is not connected by sintering, but the cross section of the part is "printed" on the material powder through the nozzle with an adhesive (such as silica gel).
3D printing service
Speaking of 3D printing services, here we divide them into two categories. One is 3D printing supply chain companies, which provide post-processing services for 3D printing, and provide related software (including control systems) and related solutions for 3D printing production. Solutions; the other category does not produce the materials and printer products required for 3D printing, but provides solution design, direct printing services, and trading platforms.
(1) Software and system solution providers
The 3D printing production line not only requires 3D printing hardware products, but also requires the cooperation of software systems. Most 3D printing equipment manufacturers will develop or re-develop related software systems by themselves. There are still professional manufacturers on the market that provide related solutions.
(2) 3D printing post-processing
Post-processing of 3D printing is an important step of 3D printing. The directly printed items are only semi-finished products. Some of the surface will be rough and need to be polished, some need to be sprayed and colored; metal products need to be annealed, aired, and cured. After post-processing, the 3D printed product can finally be delivered to the customer.
3D printing applications
The application of 3D printing is very wide, and the most popular one is medical 3D printing.
Medical 3D printing has billions of dollars in imagination. From tiny cell tissues to large-volume bones, these are the "battlefields" of the future of 3D printing.
In medical 3D printing, firstly, a computer is used to build a three-dimensional model, the data is transmitted to the printer, and the printer prints the sections layer by layer, and finally the sections are glued together to complete the shaping.
We can divide medical 3D printing into two parts from the difficulty of landing:
Orthopedic implants, oral restorations, customized prostheses, surgical guides, and internal implants. This kind of non-biological 3D printing technology is more mature, closer to the clinic, and has clear application scenarios. It is the main segmentation game for players. road;
The 3D printing of cell tissues and even organs has a long way to develop technology. It is an advanced stage of medical 3D printing. There are only five domestic players on the water.
(1) The most eye-catching section is orthopedic implants
Public data shows that orthopedic implants account for 93% of the entire implant market. It is estimated that the market size of orthopedic implants will reach 29 billion yuan in 2022. At present, domestic companies have already approved some products for the market, and there are also successful cases of cooperating with hospitals for surgery.
Domestically, it is mainly concentrated on metal and polymer materials. Internationally, most foreign manufacturers use hydroxyapatite and polylactic acid composite materials, and some orthopedic auxiliary devices use gypsum or resin materials.
Usually we have some dimensions to evaluate the technical level of orthopedic implants: material wear resistance and biocompatibility, porosity, friction coefficient, rotational mobility (dispersed stress), hinge mechanism (anti-dropping and easy implantation), Weight-bearing method (extent of wear), richness of patch (richness of bone defect treatment plan), surgery and revision strategy, etc.
(2) The invisible braces on the tuyere are the result of 3D printing
Another subdivision of 3D printing is digital oral restoration. Now the technology can make dental implants, dentures, orthodontic products, etc., and can also achieve the treatment and repair of related joint disorders.
Invisible orthodontics is in the forefront of investment. The amount of orthodontics has exploded in recent years. The gross profit margin of clinics is usually 50%-75%. The invisible braces used in invisible orthodontics are the result of 3D printing.
3D printing can bring users personalized and precise orthopedics. The scanner can grasp the digital oral conditions and establish a personalized 3D digital model of the mouth, thereby producing "tailor-made" invisible braces. According to Ping An Securities Dental Report, there were about 2.06 million orthodontic cases in China in 2017, and at 12,000 yuan per case, the size of the Chinese orthodontic market is around 25 billion.
For denture factories, 3D printers can not only realize artificial replacement, but also improve production efficiency and quality. There are more than 4,000 denture factories across the country. With the upgrading of the industry and the acceleration of import substitution, more 3D printers will enter the denture factory in the future, and the market size is expected to exceed 1 billion in the next five years.
What plagued dentists in the past is that the contours of the initial design are always difficult to match the final restoration, and 3D printing has solved this problem well. The 3D printed target restoration guide can visually present the restoration blueprint, and the restoration printed according to the guide can achieve high accuracy, so that "ideal" and "reality" can be agreed.
Some companies are good at three-dimensional data collection, provide hospitals with pre-surgery planning plans, and use visual images to simulate surgery to help doctors better operate and drill.
(3) The world's first 3D printed heart was born
On April 15 this year, researchers from Tel Aviv University in Israel announced that they had successfully 3D printed the world's first "complete" heart. The news made a global sensation. Overnight, "3D printed organs" seemed to be within reach, and the shortage of organ transplant donors no longer seemed to be a problem.
However, calm down and we will find that this "heart" is small and not the size of a human; the vascular system is incomplete and the capillaries are not printed; this "heart" does not yet have the function of pumping blood.
Although there is still some distance from a truly transplantable heart, the birth of this heart still caused a huge sensation. why? The answer is that it is related to the construction technology of tissue engineering.
The construction of classical tissue engineering first requires two types of materials-seed cells and scaffold materials. The stent material, as the name suggests, plays the role of "support". It provides a place for seed cells to grow and perform biological functions, and it needs to have the construction properties that mimic natural tissues. The seed cell is the unit that connects and grows into the required tissues and organs on the scaffold material.
What kind of scaffold material is non-toxic, non-immunogenic, has good biocompatibility, suitable biodegradability, and is suitable for cell growth? How to obtain pluripotent stem cells and differentiate them into the required seed cells? How to maintain the cell viability of the tissues and organs obtained? How to functionalize the printed organization/device? These are the questions facing scientists and companies.
After solving some of these problems, researchers from Tel Aviv University printed out a "complete" heart with cells, blood vessels, ventricles, and atria. This also means that the simpler structure of the ears, trachea, blood vessels and other tissues and organs can be completely reproduced. Non-rejection tissue transplantation may come first.
FDM and light curing are currently the mainstream printing technologies, and the above-mentioned "heart" is printed under the FDM technology. The advantage of light curing technology is that it is easy to form, but it is prone to toxicity problems.
In addition to technology, the difficulties in the industrialization of cell printing include ethics and even risk control. The society's acceptance of such products and the possible risks of viruses in the production process also restrict the development of the industry to a certain extent.
It is reported that the businesses currently provided by enterprises are mostly: the customization and sale of biological 3D printers; the customization and sale of other consumables such as biological inks; and the printing services of biological simulation models. At present, the printing of degradable tissue engineering scaffolds in the industry is relatively mature, and 3D printing of cells, tissues, and organs is mostly in the scientific research application stage.
In the short term, the realistic landing scenario for biological (cell) 3D printing is to print a single-function tissue for in vitro drug testing, virological testing, and even cosmetics and health care products. Looking further, it means that organ transplantation should eventually be realized for the benefit of mankind.
With the increasing maturity of technology, the production of 3D printed products may no longer be the biggest problem. The common problem faced by industry players is actually the issue of policy approval.
Since medical 3D printing products may be directly used in the human body, and the products are customized according to the patient's condition, each patient's condition will be different, so its approval is very strict and cautious, and the relevant policies lag behind the technology. .
3D printed products did not have applicable evidence collection standards in the past. Customized products have led to a high cost of obtaining evidence, and each body part needs to apply for a medical device certificate, which is extremely costly.
The latest development is that in July this year, the country introduced a new policy, which is expected to bring a cardiotonic agent to medical 3D printing.
This new policy is the "Regulations on the Supervision and Management of Customized Medical Devices (Trial)", which stipulates the specifications for the filing management, design and processing, use management, and supervision and management of customized medical devices, which will be implemented on January 1 next year.
Throughout the entire 3D printing market, its application range is very wide, from medical to industrial to consumer, you can see the figure of 3D printing.
The medical field includes the manufacture of medical surgical guides, medical implants, dental models and related orthodontic equipment, metal crowns and other objects;
In terms of industry, there are industrial product design and development, complex small metal precision parts, aerospace complex metal components, aircraft large and complex metal components, engineering plastic parts for aerospace, automotive, home appliances and other fields of parts manufacturing, and wax mold production for casting And building construction;
In the consumer field, it includes hand-made production, jewelry design and production, creative product production and production, and food production.
Link to this article: One article to understand the main players in the domestic 3D printing field
Reprint Statement: If there are no special instructions, all articles on this site are original. Please indicate the source for reprinting:https://www.cncmachiningptj.com
PTJ® provides a full range of Custom Precision cnc machining china services.ISO 9001:2015 &AS-9100 certified.
Machining shop specializing in fabrication services for construction and transportation industries. Capabilities include plasma and oxy-fuel cutting, Tailored machining, MIG and Custom Aluminum Cnc Precision Milling Welding Jig Fixture, roll forming, assembly, Lathe machining stainless steel cnc machine shaft, shearing, and CNC Swiss Machining services. Materials handled include carbon and Passivation Stainless Steel Machining Cover Plate Parts.
Tell us a little about your project’s budget and expected delivery time. We will strategize with you to provide the most cost-effective services to help you reach your target,You are welcome to contact us directly ( sales@pintejin.com ) .
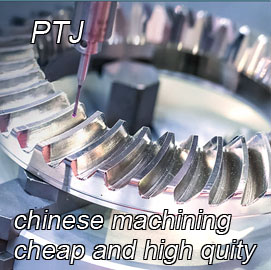
- 5 Axis Machining
- Cnc Milling
- Cnc Turning
- Machining Industries
- Machining Process
- Surface Treatment
- Metal Machining
- Plastic Machining
- Powder Metallurgy Mold
- Die Casting
- Parts Gallery
- Auto Metal Parts
- Machinery Parts
- LED Heatsink
- Building Parts
- Mobile Parts
- Medical Parts
- Electronic Parts
- Tailored Machining
- Bicycle Parts
- Aluminum Machining
- Titanium Machining
- Stainless Steel Machining
- Copper Machining
- Brass Machining
- Super Alloy Machining
- Peek Machining
- UHMW Machining
- Unilate Machining
- PA6 Machining
- PPS Machining
- Teflon Machining
- Inconel Machining
- Tool Steel Machining
- More Material