How much is a pound of superalloy?
At present, nearly 300,000 tons of superalloy materials are consumed annually in the international market, which are widely used in various fields. In 2018, the global superalloy market size was 12.163 billion US dollars, a year-on-year increase of 26.98% compared with the previous period; the superalloy market in the United States and Europe has become more mature, and the future market increase will mainly come from China. The current annual growth rate of the superalloy market in China Keep it at 20-30%.
Overview of superalloys
High-temperature alloys refer to metal materials based on Fe, Ni, and Co that have anti-oxidation and anti-corrosion properties above 600°C and can work for a long time under a certain stress. Figure 1 shows the development trend of high-temperature alloys in the world and the alloys developed in my country. High-temperature alloys are not only the fuel chambers, guides, turbine blades and turbine discs of aero engines, and other hot end parts, the key materials of high temperature parts of aerospace rocket engines, but also industrial High-temperature and corrosion-resistant component materials required by industrial sectors such as gas turbines, energy, and chemical industries are indispensable and important materials in the national economy.
At present, nearly 300,000 tons of superalloy materials are consumed in the international market each year. Figure 2 shows the distribution of the main consumption regions. The annual growth rate of the superalloy market in my country is maintained at 20-30%, and the world can produce aviation There are no more than 50 high-temperature alloy companies for aerospace, mainly in the United States, Britain, Japan, Germany, France, Russia and other countries. For example, the United States' GE, PW, Haynes Stellite, Inco Alloys International, Cannon-Muskegon, Westinghouse, Cabot Companies such as Martin Marietta, Standard Pressed Steel, Whittaker, Special Metal, Universal-Cyclops Steel, Howmet, Pratt & Whitney, Russia’s United Aircraft Company and Canada’s Mond Nickel Company have obvious oligarchic characteristics.
Since the successful trial of the first furnace of superalloy GH3030 in 1956, the research, production and application of superalloys in my country have experienced more than sixty years of development. At present, under the overall supervision of the National Development and Reform Commission, the Ministry of Industry and Information Technology, the China Nonferrous Metals Industry Association, and the National Defense Science and Industry Bureau, my country has formed some production bases and enterprises with advanced production equipment and a certain scale, such as , Steel Research Gona, Fushun Special Steel, Baosteel Special Steel, China Aviation Development, Wanhang Die Forging, Wanze Co., Ltd., Tunan Co., Ltd. have also formed a group of research institutes with independent innovation and R&D capabilities, such as Iron and Steel Research Institute of High Temperature Materials, Beijing Institute of Aeronautical Materials, Institute of Metal Research, Chinese Academy of Sciences, Beijing University of Aeronautics and Astronautics, University of Science and Technology Beijing, Northwestern Polytechnical University, etc.
According to the China Superalloy Handbook (2012), my country's superalloys are listed in a total of 194 grades, including 62 equiaxed nickel-based alloys, 43 nickel-based wrought alloys, 30 iron-based wrought alloys, and 20 intermetallic compounds. There are 5 ODS alloys and 3 powder metallurgy superalloys [3]. The largest proportion of the superalloy market in my country is deformed superalloys, about 70%, followed by cast superalloys, about 20%; in terms of matrix elements, nickel-based superalloys account for the largest proportion of the entire market. 80%, followed by nickel-iron-based superalloys, about 14%, and cobalt-based superalloys, about 6%.
Research Progress of my country's Superalloys
my country's superalloys have gone through the development process of imitation, imitation and creation combined with original creation. By absorbing the experience of developed countries and combining with my country's actual conditions for independent innovation, my country's superalloy system has been formed. The United States, Britain and other countries use their own alloy systems by companies or manufacturers, while my country is a unified system of the country, and the superalloy series and systems are formed in the order of alloy preparation methods, matrix elements, and strengthening methods. According to the preparation methods, there are deformed superalloys, cast superalloys (including equiaxed crystals, directional solidification columnar crystals and single crystal superalloys), powder metallurgy superalloys, dispersion strengthened superalloys, intermetallic high-temperature materials, and high-temperature alloy wires for welding. And high-temperature alloy-based self-lubricating materials, etc.; these different alloy series are further divided into iron-based, nickel-based, cobalt-based and chromium-based high-temperature alloys; under the same matrix, they are further divided into solid solution strengthening type and aging strengthening type [ 2].
At present, the main problems and shortcomings of my country's superalloys include: many metallurgical defects, such as black spots, white spots, carbide segregation, etc.; poor organization uniformity; high impurity element content, reducing strength and service life; high cost , The reuse rate is low.
On September 22-25, 2019, the 14th National Superalloy Annual Conference hosted by University of Science and Technology Beijing, Northeastern University and Daye Special Steel was held in Huangshi, Hubei, which focused on showing my country's recent achievements in superalloy research. The achievements include the development of deformed superalloy varieties and its residual stress control, research and development of cast superalloys, powder superalloy and powder purification technology, research and application progress of intermetallic compound-based high-temperature structural materials, etc.
1 Deformed superalloy
Wrought superalloys refer to superalloys produced through the casting-deformation process. The working range is -253—1320℃, including disks, plates, rods, wires, ribbons, tubes and other products, such as GH128, GH4169, etc., which are widely used in aerospace , Aviation, energy, petrochemical, nuclear power and other industrial fields. In recent years, wrought superalloys have achieved a lot of breakthroughs and application results in process flow, development of new alloys and new technologies.
Process flow
Domestic deformed superalloy smelting usually adopts vacuum induction + vacuum consumable double or vacuum induction + electroslag remelting + vacuum consumable triple smelting method. Through the water simulation and numerical simulation of the launder in the vacuum induction furnace, and the optimized design of the structure, the flow field distribution and temperature distribution in the launder can be improved, thereby improving the quality and cleanliness of the ingot。
High-temperature alloy ingots will produce serious component segregation during the solidification process. In order to reduce and improve component segregation and improve material uniformity, in addition to improving the smelting process, the most important technical measure is to carry out homogenization treatment. Heating for a long time promotes the diffusion and migration of solute element atoms, and minimizes the difference in element concentration between the dendrite stem and the dendrite. As the size of the ingot increases, the segregation will be affected by the solidification cooling rate and increase accordingly. The final homogenization temperature and time can be determined by comparing the secondary dendrite spacing and segregation coefficient under different homogenization systems.
In order to improve the blooming yield of GH4720Li alloy ingots and the quality level of bars, through a large number of thermal simulation compression tests, mathematical simulations and cracking criteria under different thermal deformation conditions are obtained and established, so as to optimize the forging process parameters, including step by step Reasonable distribution of cooling and fire deformation. Relevant studies have shown that after the rapid forging billet fully breaks the as-cast structure of the ingot, supplemented by diameter forging, the surface condition of the bar can be improved and the yield rate can be increased.
The GH4706 alloy super large turbine disk is the core hot-end rotating part of contemporary E/F-class heavy-duty gas turbines. The diameter of the forging exceeds 2000mm and the weight reaches 6t. It is one of the most critical parts that urgently need to be localized. The composition of the alloy is close to GH4169, and it is a Fe-Ni-based deformed high-temperature alloy strengthened by γ'phase and γ” phase. The die forging of turbine discs needs to realize both the hot forming of discs and the control of microstructure and properties. In 2013, the world’s largest 8*104t die forging hydraulic press (Figure 4) independently designed and developed by my country was put into production and successfully trial-produced GH4738 alloy turbine disc forgings with a diameter of 1500mm. The preparation of large-scale GH4706 alloy turbine disk provides a certain reference experience, but it still faces severe challenges.
The residual stress originates from the uneven plastic deformation inside the material during the preparation process, and is essentially the lattice distortion remaining in the material. The thermal deformation near the recrystallization temperature is difficult to form a high level of residual stress; even the residual stress formed during low-temperature forging or cooling after forging can usually be released in the subsequent high-temperature solution treatment. Therefore, high-temperature alloy disc forgings generally need to be rapidly cooled after solution treatment after forging to ensure that the γ'or γ” phase does not coarsen. Figure 6 shows the test depth and resolution corresponding to different residual stress testing techniques. For high-temperature alloy disc forgings, it is necessary to test and analyze the internal residual stress of 10mm or more from the surface layer, and the resolution is required to be mm level. Therefore, the main methods include neutron diffraction, contour method, and deep hole method ( deep-hole drilling) and ultrasound (ultrasonic).
Bi Zhongnan of the Central Iron and Steel Research Institute and others summarized the test methods for the internal residual stress of superalloy turbine disk forgings, and clarified the evolution law and mechanism of residual stress during the preparation process of solid solution, quenching, aging, and parts processing [6].
Ultrasonic testing is an important method of non-destructive testing. Ultrasonic waves emitted by the probe are used to propagate inside the workpiece. When there are discontinuous or inhomogeneous tissues with different acoustic properties from the matrix, changes in the propagation mode and information will occur at the interface , So as to provide qualitative and quantitative analysis basis for non-destructive testing and evaluation. Fan Xingyi, Lin Shiqian and others have fully studied the relationship between the grain size of the disc forging structure and the ultrasonic clutter to determine the main factors affecting the inspection structure and the appropriate inspection parameters.
New alloy
Wang Qingzeng, Chen Guosheng, Sun Wenru and others developed GH4169G alloy on the basis of the research of P strengthening and P and B compound strengthening mechanism. While maintaining the excellent comprehensive properties of GH4169 alloy, the use temperature was increased by 30℃ to reach 680°C; and the service life at 650°C is increased by more than 3 times; at the same time, the welding and thermal processing performance is equivalent to that of GH4169 alloy, which has broad application prospects.
GH4169D alloy is successfully developed on the basis of GH4169 alloy by reducing the content of Fe, adding solid solution strengthening elements W and Co, adjusting the content and ratio of Al and Ti, and appropriately increasing the content of Nb and adjusting the content of trace elements. The long-standing gap between the two most widely used superalloys in the world-GH4169 for 650°C and GH4738 for 750°C.
Significant progress has also been made in the development of high-performance turbine disk materials relying on the casting and forging process. High-performance deformed high-temperature alloy turbine disk materials such as GH4065, GH4079 and GH4975 have been developed successively, especially the comprehensive performance of GH4065 alloy has reached the level of powder metallurgy materials. It is expected to provide a mature and reliable solution for the selection of hot-end rotating parts of my country's advanced aero-engines.
On the basis of maintaining a certain amount of precipitation strengthened γ'phase, GH4282 alloy solves the cold working caused by the large amount of precipitation of γ'phase in the high-strength aging strengthened combustor alloy by controlling the structure, composition and precipitation kinetics of the γ'phase. And the problem of difficult welding, the alloy maintains excellent high-temperature strength and thermal stability in the range of 650-950℃, and at the same time, the welding and cold working properties are well balanced and optimized.
new technology
Our country has developed the nitride-strengthened superalloy NGH5011, and aims at the key physical chemistry of the nitrogen adsorption and dissolution on the surface, uniform diffusion in the matrix, and nitride precipitation at the reaction interface involved in the nitriding process of the endogenously dispersed nitride-strengthened alloy. The process carried out systematic research work.
The High Temperature Materials Research Institute of Central Iron and Steel Research Institute successfully prepared 3D-In718 alloy gas turbine disks and integral impellers using additive manufacturing technology. The density of the parts reached 99.9%, and the structure and performance were far better than those of castings. The tensile strength at room temperature and high temperature , Plasticity and durability can meet the standards of forgings.
In addition, the new casting and forging process technology of electroslag remelting continuous directional solidification smelting + 3D forging billet + isothermal forging has successfully prepared deformed FGH4096 alloy turbine disks.
2 casting superalloy
Casting superalloys have a wide range of composition, and are divided into three categories according to the use temperature: equiaxed crystal casting superalloys used at -253-650℃, such as K4169; equiaxed crystal casting used at 650-950℃ High-temperature alloys, such as K419; and directional solidification columnar crystal casting high-temperature alloys used at 950-1100°C, such as DD402. Aeroengine casings are typical equiaxed superalloy castings used under medium and low temperature conditions. Complicated structure, precise size, and thin-walled lightweight are the development trends. Therefore, the coordinated control of precision forming and solidification structure is a major issue that needs to be solved urgently. technical challenge.
Equiaxed nickel-based superalloys are mainly based on the γ phase, which is strengthened by adding Al, Ti, Nb and Ta to form a γ'phase or γ” phase with a volume fraction of up to 70%, and is strengthened with C, B and Zr As a grain boundary strengthening element in the grain boundary segregation or the formation of carbides or borides to improve the overall performance of the alloy. The development direction of the equiaxed crystal casting superalloy is mainly: according to alloying theory and metallurgical principles, combined with computer simulation technology design A new type of material with good comprehensive performance; for the purpose of different alloys, through the adjustment of the existing alloy composition to obtain excellent specific performance; improve and improve the alloy smelting process, improve the metallurgical quality of the alloy; improve the quality and quality of castings through new process technology Mechanical properties.
The traditional "experience trial and error" method is high cost, long cycle, and difficult. It will become a major trend to develop alloy composition design based on computational materials science, big data processing, machine learning, and high-throughput testing. Based on the electron vacancy theory, the number of bonding times and the d-orbital energy of alloying elements, the development and perfect phase calculation can simulate and predict the precipitation law of TCP phase in the alloy. How to establish the quantitative relationship between alloy composition and high performance is the current single crystal alloy The key to design. Fu Hengzhi, Jie Ziqi and others studied the melt solidification characteristics of K4169 superalloy, obtained the influence of melt overheating temperature on nucleation and undercooling, and further verified that melt overtemperature treatment can significantly refine the grain size, Improve the morphology and distribution of the precipitated phase, effectively reduce the segregation of alloying elements, thereby improving the comprehensive mechanical properties of the as-cast superalloy .
Using JMatPro, Thermal-calc and Panda software, the initial melting temperature, alloy density, phase composition and content of different components of nickel-based superalloys can be calculated more accurately, and the heat treatment window and paste interval can be predicted On this basis, formulate appropriate thermodynamic criteria and screen out alloy components that meet the requirements for experimental testing, which can save the development time and cost of the alloy.
Through casting molding simulation technology, it is possible to simulate the temperature field distribution during the filling process, so as to rationally design the riser and gating system, optimize the casting process parameters, and predict the defects such as shrinkage cavity, cold barrier, under-casting and shrinkage porosity and after cooling. The residual stress provides theoretical guidance for actual production. At present, the development of casting simulation technology is relatively mature. Typical commercial simulation software includes: ProCAST, MAGMA, AFSolid and PAM-CAST. Liu Baicheng and others proposed the use of computer technology to transform the foundry industry, carried out a lot of research in the field of macro and micro simulation simulation of the foundry process, and developed a series of numerical simulation software for engineering applications .
Common tissue simulation methods include: first principles, molecular dynamics, Monte Carlo, cellular automata, phase field method, finite element, etc. For example, coupling the crystal model of creep damage to the phase field model can realize the simultaneous simulation of the three stages of creep tissue evolution and performance, and obtain the creep tissue evolution process and creep curve, as shown in Figure 8. It provides a new way for superalloy creep simulation, which is conducive to the development of performance-oriented microstructure optimization simulation work.
Single crystal superalloy eliminates grain boundaries and has excellent high-temperature creep, oxidation and corrosion resistance. Its research and development began in the United States Pratt & Whitney in the 1970s, and the PWA1480 single crystal superalloy has been successful since the 1980s. Since its development and application, foreign single crystal alloys have developed rapidly, and the fourth generation of single crystal alloys was developed around 2000. From the first generation to the fourth generation of single crystal superalloys, the working temperature has been increased to 1827°C, which is much higher than the initial melting temperature (1280-1330°C). At the same time, the content of precious metal elements such as Re and Ru is increasing, and the cost is also increasing. Higher and higher.
The development of single crystal alloys in my country started relatively late, and most of them are based on imitation. In recent years, my country has made significant progress in the development and application of single crystal superalloys, and independently developed the third-generation single-crystal alloys DD33, DD9 and the fourth-generation single-crystal alloys DD91, DD15, etc., and already possesses new single-crystal superalloy materials. , New process independent research and development capabilities, especially under the guidance and promotion of military-civilian integration policies, a number of private enterprises related to superalloys have emerged, most of which focus on the production of single crystal superalloy master alloys and single crystal blades.
At present, the research on the composition design of single crystal superalloys is mainly concentrated in universities and research institutes in Britain, Germany, Japan and other countries, and the design space is getting smaller and smaller, and it is more and more difficult to improve the overall performance. Started to develop various "custom" alloys. For example, in order to reduce the Re content in the second-generation single crystal alloy, GE has developed René N515 alloy (1.5% Re) with performance close to René N5, and gradually replaced René N5 in aero-engine turbine blades.
Grain refinement can greatly improve the low-cycle fatigue performance of castings, reduce the dispersion of mechanical properties, and improve mechanical processing performance. The main mechanism is to promote nucleation and inhibit grain growth. Commonly used methods include thermal control method (FGP, Grainix method), kinetic method (mold stirring, electromagnetic vibration and pulse current, etc.), chemical method (refining agent) )Wait. Beijing Institute of Aeronautical Materials, Beijing University of Aeronautics and Astronautics, etc. have done a lot of analysis and research on the low-cycle fatigue, high-cycle fatigue, and creep properties of single crystal superalloys [9,10]. In addition, certain progress has also been made in some new processes such as anti-gravity casting technology and additive manufacturing.
3Powder superalloy
High-quality superalloy powder is the basis and guarantee for the development and production of advanced aero-engine powder turbine disks. At present, the preparation of superalloy powder mainly includes two methods: Ar aerosol method (AA powder) and plasma rotating electrode method (PREP powder). Zhang Guoqing’s research group from Beijing Institute of Aeronautical Materials and others have developed a series of Ar gas atomized superalloy powder preparation devices and technologies to prepare powdered superalloy turbine discs and other hot-end parts, as well as additive manufacturing for 3D printing. Provide raw materials. They have achieved certain results and experience in alloy atomization process, particle size control during powder making process, O content control, and non-metallic inclusion control.
4 Intermetallic compound-based superalloys
Intermetallic compounds are compounds composed of two or more metal elements or metal elements and metalloid elements in a certain atomic ratio. The coexistence of covalent bonds and metal bonds makes intermetallic compounds have a long-range ordered superlattice structure in a longer range. At high temperatures, the dislocation mobility of the intermetallic compound is relatively reduced, so that it has a higher high-temperature strength. The more typical ones are Ti-Al, Ni-Al, Nb-Si, which have excellent high temperature strength and low density, but also have low room temperature fracture toughness and poor high temperature oxidation resistance, which restrict their application. , Has also become the difficulty and focus of research in this field.
In recent years, my country has made important progress in the basic research and engineering application of intermetallic compound-based superalloy materials, represented by TiAl, Ti3Al, Ti2AlNb, and Ni3Al-based alloys, which have made significant progress in performance and technology, and have developed some New high-temperature structural materials with independent intellectual property rights have made important contributions to the development of high-performance aeroengines in my country. Nb-Si-based alloys have also made significant progress in the solidification process and basic research of anti-oxidation coatings, and are gradually approaching practical applications. For example, the important progress made in Ti-Al intermetallic compound superalloys includes: a new generation of high niobium content TiAl alloy composition design, structure and performance relationship research found new rules and mechanisms; second generation TiAl alloy engineering application breakthrough; Ti3Al and Ti2AlNb alloys have made significant progress, and their application scope has been continuously expanded.
Link to this article: How much is a pound of superalloy?
Reprint Statement: If there are no special instructions, all articles on this site are original. Please indicate the source for reprinting:https://www.cncmachiningptj.com
PTJ® provides a full range of Custom Precision cnc machining china services.ISO 9001:2015 &AS-9100 certified.
Machining shop specializing in fabrication services for construction and transportation industries. Capabilities include plasma and oxy-fuel cutting, Tailored machining, MIG and Custom Aluminum Cnc Precision Milling Welding Jig Fixture, roll forming, assembly, Lathe machining stainless steel cnc machine shaft, shearing, and CNC Swiss Machining services. Materials handled include carbon and Passivation Stainless Steel Machining Cover Plate Parts.
Tell us a little about your project’s budget and expected delivery time. We will strategize with you to provide the most cost-effective services to help you reach your target,You are welcome to contact us directly ( sales@pintejin.com ) .
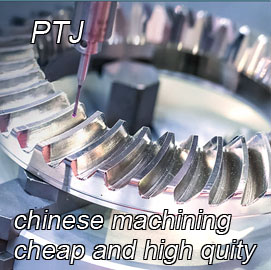
- 5 Axis Machining
- Cnc Milling
- Cnc Turning
- Machining Industries
- Machining Process
- Surface Treatment
- Metal Machining
- Plastic Machining
- Powder Metallurgy Mold
- Die Casting
- Parts Gallery
- Auto Metal Parts
- Machinery Parts
- LED Heatsink
- Building Parts
- Mobile Parts
- Medical Parts
- Electronic Parts
- Tailored Machining
- Bicycle Parts
- Aluminum Machining
- Titanium Machining
- Stainless Steel Machining
- Copper Machining
- Brass Machining
- Super Alloy Machining
- Peek Machining
- UHMW Machining
- Unilate Machining
- PA6 Machining
- PPS Machining
- Teflon Machining
- Inconel Machining
- Tool Steel Machining
- More Material