Laser additive manufacturing can improve the production process of 3D printed turbine blades
According to news on April 29, a team of German scientists used the FRM II neutron source to successfully analyze the residual stress of 3D printed nickel-chromium alloy specimens. In the future, it is expected to improve the production process of 3D printed turbine blades on the basis of this research.
The blades of gas turbines must withstand extreme conditions such as high temperature, high pressure and high centrifugal force during operation. In order to further improve efficiency, the combustion temperature is even higher than the melting point of the blade material. Therefore, the gas turbine blade is designed as a complex hollow structure in order to be cooled by air from the inside. However, ordinary manufacturing methods, such as casting and milling, cannot produce a blade with such a complex structure.
Laser additive manufacturing (3D printing) technology provides new possibilities for the manufacture of such blades. However, during the manufacturing process, the local high temperature generated by the laser and the rapid cooling of the melt will cause stress in the material. This will not only cause deformation, in the worst case, it may even lead to cracks. Therefore, the manufacturer must eliminate the residual stress through subsequent complicated heat treatment steps, which takes a lot of time and high cost.
Now, the German Federal Institute for Materials Research and Testing, together with researchers from the Technical University of Munich, Siemens Energy, and the University of Potsdam, have successfully measured the 3D printed 3D printed by non-destructive neutron diffraction using the FRM II neutron source located in Garching. Residual stress in nickel-based alloy structure. Related results were published in the recent "Journal of Applied Crystallography".
In this experiment, Siemens Energy used the polycrystalline nickel superalloy powder used to produce gas turbine components to print a lattice structure of a few millimeters in size, and deliberately omitted the usual post-production heat treatment process. Researchers from the Federal Institute of Materials Research and Testing have successfully achieved the correct alignment of the lattice structure in the neutron beam through non-destructive neutron diffraction, and correctly determined the residual stress field in the representative part of the structure.
This experiment proved that neutron diffraction can be used to analyze the residual stress in complex components. In the next step, the team hopes to study how to reduce this destructive stress. The main participant of the project, Dr. Tobias Fritch of the Federal Institute of Materials Research and Testing, said: “When the laser melts the superalloy powder, the more heat is applied locally, the greater the internal stress generated. . Temperature gradients can cause irregularities in the atomic lattice. Therefore, we must distribute the heat as evenly as possible during the printing process."
Link to this article:Laser additive manufacturing can improve the production process of 3D printed turbine blades
Reprint Statement: If there are no special instructions, all articles on this site are original. Please indicate the source for reprinting:https://www.cncmachiningptj.com/,thanks!
Sheet metal, beryllium, carbon steel, magnesium, 3D printing, precision CNC machining services for heavy equipment, construction, agriculture and hydraulic industries. Suitable for plastics and rare alloys machining. It can turn parts up to 15.7 inches in diameter. Processes include swiss machining,broaching, turning, milling, boring and threading. It also provides metal polishing, painting, surface grinding and shaft straightening services. The production range(include aluminum die casting and zinc die casting) is up to 50,000 pieces. Suitable for screw, coupling, bearing, pump, gearbox housing, drum dryer and rotary feed valve applications.PTJ will strategize with you to provide the most cost-effective services to help you reach your target,Welcome to Contact us ( sales@pintejin.com ) directly for your new project.
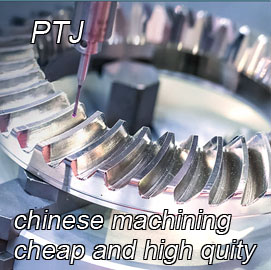
- 5 Axis Machining
- Cnc Milling
- Cnc Turning
- Machining Industries
- Machining Process
- Surface Treatment
- Metal Machining
- Plastic Machining
- Powder Metallurgy Mold
- Die Casting
- Parts Gallery
- Auto Metal Parts
- Machinery Parts
- LED Heatsink
- Building Parts
- Mobile Parts
- Medical Parts
- Electronic Parts
- Tailored Machining
- Bicycle Parts
- Aluminum Machining
- Titanium Machining
- Stainless Steel Machining
- Copper Machining
- Brass Machining
- Super Alloy Machining
- Peek Machining
- UHMW Machining
- Unilate Machining
- PA6 Machining
- PPS Machining
- Teflon Machining
- Inconel Machining
- Tool Steel Machining
- More Material