How to solve the problem of heat dissipation of electronic products?
It has been nearly two years since 5G entered the commercial stage, and the industry has begun to take shape. In July this year, data from the Ministry of Industry and Information Technology showed that my country has built the world's largest 5G independent networking network, opened 961,000 5G base stations, and the number of 5G terminal connections reached 365 million. Nearly 1,600 "5G+Industrial Internet" projects are in operation.
The 5G era has achieved high-frequency and high-speed transmission, but it will also bring greater power consumption and heat generation challenges for facilities and terminal equipment. For example, 5G mobile phones are upgraded in the direction of higher performance, higher screen quality, higher integration, lighter and thinner, and their comprehensive heat generation has increased significantly compared with 4G mobile phones. In terms of base stations, the power consumption of 5G base stations has reached a single station. 2~3 times of a single 4G base station.
Experiments have proved that the reliability of electronic components decreases by 10% every time the temperature of electronic components increases by 2°C. The accumulation of heat caused by the work of electronic products will cause electronic products to become hot, freeze, crash or even explode. Thermal management of electronic products has become the key to the industry's urgent need to solve.
However, the traditional single cooling solution can no longer meet the diversified cooling requirements of high-performance products. Taking 5G mobile phones as an example, the industry believes that the requirements for heat dissipation of 5G mobile phones are not ordinary heat dissipation upgrades, but need to achieve a comprehensive improvement through new heat dissipation materials and three-dimensional heat dissipation design.
So how should the thermal management industry continue to innovate and develop? What are the hottest thermal management materials and design schemes at the moment?
1. Discussion on the multi-material and three-dimensional combined heat dissipation method of electronic products
The temperature of the heat source is equal to the product of the ambient temperature plus the heating power and the heat transfer resistance. Chen Jiliang said that the current requirements for the temperature of electronic components have not changed, but the amount of heat generated has increased significantly. The intuitive demand is to reduce the heat transfer resistance.
Means to reduce thermal resistance include increasing thermal conductivity, increasing emissivity, reducing heat transfer distance, increasing area, and increasing flow rate. But the reality is cruel. Taking chips as an example, the power consumption is getting higher and higher, but the area and volume have not increased year-on-year.
"A single method can no longer meet the demand for heat conduction." He said that in terms of material means, the industry is pursuing materials with higher thermal conductivity and higher surface emissivity, but the progress of material technology cannot keep up with the rate of increase in heat generation; in structural means On the one hand, the industry pursues a larger area and larger space to dissipate heat, but this is contrary to the multi-functionality and compactness of products; in terms of strengthening methods, the industry pursues forced air cooling, indirect liquid cooling, immersion liquid cooling, etc. Technology, but in this way, it brings about cost increase, noise, vibration and other problems.
2. Reflections and breakthroughs in the design concept of thermal interface materials in the post-Moore era
"The design of thermal interface materials is a complex system of engineering, not just to improve thermal conductivity." Li Zhaoqiang said.
Take the chip as an example. The chip is developing towards integration and high power, and the barrier lake effect brings various hidden dangers and heat dissipation problems. Traditional heat conduction adopts the formula design of "resin + powder", but the thermal conductivity of resin is low, less than 0.5W/mK. In addition, the solution has a single heat conduction path, which has open circuit defects, and the material filling volume has risen to a bottleneck. "Using highly thermally conductive materials as the continuous phase and constructing oriented through heat conduction paths can add additional thermal management paths."
Breaking through the existing design ideas, Li Zhaoqiang proposed a chip and level system level overall plan, such as liquid metal, oriented carbon fiber materials, phase change materials, etc. "Using the same materials and disruptive designs can also achieve breakthrough results."
3. Industrialization and application of graphene thermal film
"Our graphene thermal film process flow includes the preparation, decomposition, coating, cutting, pretreatment, carbonization, graphene, calendering, filming, die cutting, and packaging of graphite oxide filter cake." Wang Hongchun said.
In the preparation of graphite oxide filter cake, graphite flakes are oxidized in a highly concentrated acid containing a strong oxidizer, and then subjected to processes such as pickling, water washing, and filtration to obtain graphite oxide filter cake. In the pre-dispersion link, the graphite oxide filter cake is mixed with water in a certain proportion, and then pre-dispersed by a mixer to obtain a completely exfoliated graphene oxide slurry.
He said that the graphene thermal film is better than the artificial graphite sheet, "The thermal conductivity and temperature uniformity of the graphene heat dissipation film are better than the same thickness of artificial graphite, and the mechanical properties of the graphene thermal film are also stronger."
4. Thermal management of lithium-ion battery power or energy storage system
In the field of lithium batteries, battery safety incentives will trigger the battery to generate heat. When the heat production rate is greater than the heat dissipation rate, the battery temperature will rise and cause a chain reaction of battery materials, resulting in thermal runaway.
Jiang Fangming believes that battery body factors and operating environment factors are long-term evolutionary factors, and are also the cause of some external stimuli. The analysis, detection and evaluation of their evolutionary laws is expected to achieve early warning of the safety state of the system.
In addition, in the process of gradual changes in the battery safety boundary, it is necessary to regularly update the control threshold and study the evolution of the internal safety state.
5. Nanomaterials: Get together to become "cool" and help prevent electronic products from overheating
A team of physicists at the University of Colorado at Boulder has solved a phenomenon in the nano field that makes them puzzling: why are some ultra-small heat sources gathered together so that they cool faster. This discovery will be published in the Proceedings of the National Academy of Sciences, and in the future can help electronic equipment in the technology industry reduce heat and increase operating speed.
This research started with an inexplicable phenomenon. In 2015, researchers experimented with metal strips many times thinner than hair on a silicon substrate. When they heated these metal strips with a laser, some strange changes occurred.
Their behavior is very abnormal. These nano-scale heat sources usually have very low heat dissipation efficiency, but if they are tightly wrapped together, they will cool down faster.
In the new study, the researchers used computer-based simulations to track the heat emitted from nanometer-sized strips. It was found that when the heat sources were put together, the energy vibrations generated by the heat sources would bounce back to each other, scatter the heat, and cool down the strips.
The results of the research lay the foundation for the design of next-generation ultra-small devices, such as microprocessors or quantum computer chips. Researchers believe that engineers can one day use this unusual behavior to better grasp the heat flow in small electronic devices.
6. Coating materials that dissipate heat through "sweat"
Electronic products usually use fans to cool down, but this method is noisy, consumes a lot of energy, and is not suitable for small electronic products such as mobile phones. A team of Chinese scientists has recently developed a heat dissipation coating for electronic products that can dissipate heat like sweat.
Metal-organic framework material is a new type of porous material that is very popular in recent years, and it has great application value in catalysis, energy storage and separation. The team of Professor Wang Ruzhu from the School of Mechanical and Power Engineering of Shanghai Jiaotong University published a study in the American Journal of Joule on the 22nd, saying that they were inspired by the sweating mechanism of mammals and found a metal-organic framework material called MIL-101(Cr). This material can store large amounts of water and release water vapor when heated to take away the heat.
In an experiment, the research team coated three 16-square-centimeter aluminum sheets with a thickness of 198 microns, 313 microns, and 516 microns, and heated them. The results showed that the uncoated aluminum sheet was heated to 60 degrees Celsius in 5.2 minutes, the thinnest coated aluminum sheet was heated to the same temperature in 11.7 minutes, and the thickest coated aluminum sheet took 19.35 minutes.
The research team also tested a micro computing device. Compared with the uncoated MIL-101 (Cr) heat sink, the heat sink coated with this material reduced the chip temperature of the device by 7 minutes after the computing device worked under high load for 15 minutes. Degrees Celsius.
The researchers pointed out that the material used in the experiment is less than 0.3 grams, but the biggest challenge to realize industrial applications is still the cost issue. Researchers call for strengthening relevant research and reducing the cost of metal organic framework materials.
Link to this article: How to solve the problem of heat dissipation of electronic products?
Reprint Statement: If there are no special instructions, all articles on this site are original. Please indicate the source for reprinting:https://www.cncmachiningptj.com/,thanks!
PTJ® provides a full range of Custom Precision cnc machining china services.ISO 9001:2015 &AS-9100 certified. 3, 4 and 5-axis rapid precision CNC machining services including milling, sheet metal to customer specifications,Capable of metal & plastic machined parts with +/-0.005 mm tolerance.Secondary services include CNC and conventional grinding, laser cutting,drilling,die casting,sheet metal and stamping.Providing prototypes, full production runs, technical support and full inspection.Serves the automotive, aerospace, mold&fixture,led lighting,medical,bicycle, and consumer electronics industries. On-time delivery.Tell us a little about your project’s budget and expected delivery time. We will strategize with you to provide the most cost-effective services to help you reach your target,Welcome to Contact us ( sales@pintejin.com ) directly for your new project.
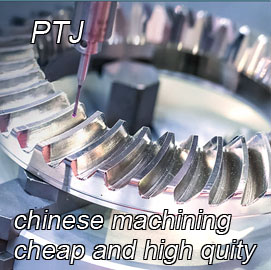
- 5 Axis Machining
- Cnc Milling
- Cnc Turning
- Machining Industries
- Machining Process
- Surface Treatment
- Metal Machining
- Plastic Machining
- Powder Metallurgy Mold
- Die Casting
- Parts Gallery
- Auto Metal Parts
- Machinery Parts
- LED Heatsink
- Building Parts
- Mobile Parts
- Medical Parts
- Electronic Parts
- Tailored Machining
- Bicycle Parts
- Aluminum Machining
- Titanium Machining
- Stainless Steel Machining
- Copper Machining
- Brass Machining
- Super Alloy Machining
- Peek Machining
- UHMW Machining
- Unilate Machining
- PA6 Machining
- PPS Machining
- Teflon Machining
- Inconel Machining
- Tool Steel Machining
- More Material