A new breakthrough in 3D printing!
With the continuous development and development of 3D printing, real-time monitoring and construction of diagnostics have become an important tool for producing high-quality parts, especially in emerging printing technologies such as liquid metal jetting (LMJ).
In LMJ, tiny molten metal droplets are ejected from nozzles at high speed to 3D print parts in layers, similar to inkjet printers in the consumer market. Unlike the laser-based metal 3D printing process, this technology does not require metal powder because it is dangerous to handle and waste materials. The diagnostics used to ensure high-quality LMJ printing now rely heavily on high-speed cameras, which require expensive equipment, can be difficult to set up, and generate large amounts of data. Although sufficient to evaluate test prints in a few seconds, it is not a viable solution for longer builds.
Researchers at Lawrence Livermore National Laboratory (LLNL) are trying to solve this problem with a new diagnostic tool that can determine the quality of metal droplets and monitor LMJ printing in real time. This method uses low-frequency electromagnetic near-field detection to capture the metal droplet dynamics. When combined with simulation, it only provides information about droplet characteristics based on signal amplitude and phase.
Researchers say that the ability to use only one parameter to characterize droplets significantly reduces the amount of necessary data, making long-term LMJ printing processing and feedback possible. This work was published online by the Journal of Applied Physics, and the editor selected it as a featured article.
"Our results show that the use of millimeter wave detection methods can be used to monitor liquid metal jets in situ," said lead author and LLNL engineer Tammy Chang. "This is exciting because it means that we can replace computationally expensive high-speed, high-resolution optical diagnostics to achieve real-time performance evaluation and feedback control to ensure high-quality printed metal parts."
Through this new technology, they discovered large-scale trends such as print changes and abnormalities at the nozzle, as well as the microscopic properties of the droplets, including size, position, and dynamics. Chang said the team used electromagnetic simulation to simulate droplet characteristics, allowing the team to understand the physical principles of electromagnetic scattering and how changes in the detected signal amplitude and phase affect droplet characteristics.
The researchers said that the result of this study is a "compact and non-invasive" diagnostic method that can distinguish droplets in the LMJ machine at a higher printing rate than before, and can detect other functions of the printing system. They concluded that the ability to capture droplet characteristics based on only one parameter ultimately shows the promise of a feedback system in which fast, real-time processing can be used to adjust print settings and ensure part quality.
LLNL engineer Andy Pascall, the co-author of the paper, said: "The clean ejection of a drop of ink is the key to good print quality." "High-speed camera is in our laboratory where we test new printing parameters. It works well in a large-scale environment, but it will never be used in production. Millimeter wave diagnostics is a huge improvement because it can be integrated into the printer, does not require optical access and provides data that can be analyzed in real time to determine whether high Quality droplets. This type of diagnosis will be very useful in a production environment."
In the future, researchers say that signal processing technology can be used to correlate optical and millimeter wave measurements and predict droplet characteristics based only on millimeter wave results. The processing work developed by LLNL researchers and their collaborators is currently under review.
This work is part of a three-year laboratory-guided research and development (LDRD) project, which aims to develop acoustic and electromagnetic monitoring methods for metal additive manufacturing. It supports LLNL's on-demand droplet liquid metal ejection work led by Pascall and physicist Jason Jeffries.
Laboratory staff scientist and non-destructive assessment team leader Joe Tringe designed the original basic concept of diagnosis, as well as a broader LDRD exploratory research project for acoustic and electromagnetic diagnosis of metal additive manufacturing.
Link to this article: A new breakthrough in 3D printing!
Reprint Statement: If there are no special instructions, all articles on this site are original. Please indicate the source for reprinting:https://www.cncmachiningptj.com/,thanks!
PTJ® provides a full range of Custom Precision cnc machining china services.ISO 9001:2015 &AS-9100 certified. 3, 4 and 5-axis rapid precision CNC machining services including milling, sheet metal to customer specifications,Capable of metal & plastic machined parts with +/-0.005 mm tolerance.Secondary services include CNC and conventional grinding, laser cutting,drilling,die casting,sheet metal and stamping.Providing prototypes, full production runs, technical support and full inspection.Serves the automotive, aerospace, mold&fixture,led lighting,medical,bicycle, and consumer electronics industries. On-time delivery.Tell us a little about your project’s budget and expected delivery time. We will strategize with you to provide the most cost-effective services to help you reach your target,Welcome to Contact us ( sales@pintejin.com ) directly for your new project.
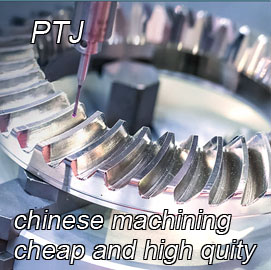
- 5 Axis Machining
- Cnc Milling
- Cnc Turning
- Machining Industries
- Machining Process
- Surface Treatment
- Metal Machining
- Plastic Machining
- Powder Metallurgy Mold
- Die Casting
- Parts Gallery
- Auto Metal Parts
- Machinery Parts
- LED Heatsink
- Building Parts
- Mobile Parts
- Medical Parts
- Electronic Parts
- Tailored Machining
- Bicycle Parts
- Aluminum Machining
- Titanium Machining
- Stainless Steel Machining
- Copper Machining
- Brass Machining
- Super Alloy Machining
- Peek Machining
- UHMW Machining
- Unilate Machining
- PA6 Machining
- PPS Machining
- Teflon Machining
- Inconel Machining
- Tool Steel Machining
- More Material