Add additional functions of die-casting machine to meet the needs of die-casting process
Introduction: As the basic technical equipment of die-casting, die-casting machine has a great impact on product quality, production cost, production efficiency, etc. during the production process.
With the continuous improvement and refinement of die-casting technology, the impact of various functions of die-casting machine Demand is constantly increasing. At present, the differences in the accuracy, stability, and main functions of the die-casting machine of equipment manufacturers will gradually shrink. The sales market is becoming more and more competitive. , Convenient additional functions, can be loved by the majority of users, and avoid falling into the vicious competition of price wars.
The following will make a simple statement based on some application requirements in production practice, some of which may also be applied to individual die-casting machines. The purpose of listing is to hope that our die-casting machine manufacturers can meet the needs of users. Actively respond so that our die-casting equipment can better serve the die-casting process.
1. First reset of ejector system
1.1 First reset signal confirmation
In die-casting production, we often encounter molds where the ejector rod must be reset before the mold is closed. Most of these molds adopt the form of reset rods, relying on threaded connections and using the ejection cylinder of the equipment to achieve this function; practical applications In the process, the thread of the reset rod is damaged, which causes the ejector plate of the die not to be returned, and the ejector plate of the die-casting machine has returned, and the equipment starts to close the mold after receiving the mold clamping signal, causing damage to the mold.
In order to avoid such problems, after discussion and communication with the equipment manufacturer, a confirmation interface for the mold ejection reset signal was added to the control program of the die casting machine. At the same time, the mold manufacturer set a travel switch on the ejector plate of the mold. After the ejector plate of the mold is reset, the travel switch is triggered, and the signal of this switch is input to the control system of the die-casting machine for confirmation before the mold clamping is allowed, which realizes the safe operation of the mold from the hardware.
1.2 Quick connection
In addition to the above-mentioned method of adding confirmation signals, the problem of mold resetting first can also be solved mechanically; the failure problem of first resetting is the problem of connection failure from the root cause. As the frequent replacement of molds in die-casting production affects production efficiency, various companies are seeking quick replacement of die-casting molds, especially the quick connection of reset rods. If the ejection system on the die-casting machine and the ejection system of the mold are connected quickly and reliably, the replacement time of the mold will be greatly reduced, and the reliable operation of the first reset is also guaranteed. Individual manufacturers have tried to adopt this method; however, due to the problem of the coordination standard between equipment and molds, there is no unified standard structure at present, and equipment manufacturers are required to continuously improve this function.
2. Injection position and speed
2.1 Confirmation of the actual quick press start point
In the die-casting process, the fast press start position is a crucial parameter. After we set the fast press start switch, does the fast press start point of the equipment really meet the requirements of our process design? Are the process parameters correct? It is difficult to confirm on existing equipment.
In order to solve this problem, we have made some improvements in the design of the die casting machine control program through communication with the equipment manufacturer; when the fast press is about to start, the injection cylinder automatically stops moving, and the molten metal is taken out after the molten metal is cooled for processing judgment.
2.2 Measurement of slow injection speed
Slow injection speed generally refers to the forward speed of the punch within the distance from the start of movement to the start of fast pressure (some equipment is divided into slow speed and one fast speed); its function is to move the punch at a slower speed. The molten metal advances to the vicinity of the inner gate and allows the gas in the pressure chamber to be smoothly discharged [1] to avoid or reduce the entrainment of gas in the molten metal; as we all know, the value of the slow injection speed is mainly related to the fullness of the pressure chamber. However, the value of this slow injection speed is not displayed on the general die casting machine, and the adjustment of the slow injection speed is also very inconvenient. The slow injection speed in actual production is often ignored; different molds are produced on the same die casting machine. The slow injection speed (the slow injection speed is never adjusted!).
For a die-casting machine with a screen display, is it possible to realize the measurement and display of the slow injection speed without increasing the cost? Since the commonly used slow injection speed is between 0.1-0.4m/s[2], the slow injection progress time is about 1s, and the response time of the inductive switch is about 0.1ms. The error caused by the inductive switch speed measurement is used to measure The value has little effect and has certain feasibility; the specific method is:
As shown in Figure 1, when the sensing rod on the injection cylinder is separated from the return hammer limit switch, the control computer of the die-casting machine starts timing, and when the sensing rod is separated from the quick-press start switch, it stops timing; the distance measurement time is obtained from the scale Read the distance between the two switches on the ruler and input it into the computer to calculate the average speed of slow injection. The slow injection speed obtained by this measurement method can fully meet the requirements of the die-casting process.
3. Safety
3.1 Human body induction
In the die-casting production, the operator is squeezed and squeezed to death from time to time. The accidents are due to personnel violations. However, in terms of the safety of the die-casting machine, shouldn't our equipment manufacturer do anything? ! With reference to the requirement that a safety grating must be installed on the stamping equipment, whether a human body sensing device can also be installed on the moving template of the die-casting machine, once the human body in the clamping interval is sensed, the clamping must be stopped. In order to realize this kind of safety scheme, the technicians of die-casting equipment manufacturers need to use more brains.
3.2 Telescopic front safety door
In die-casting production, it is often encountered that there is a long core-pulling cylinder on one or both sides of the mold, which causes the front and rear safety doors to not be closed normally, which brings great safety hazards to the normal production of die-casting, especially Safety accidents caused by forced production when the front safety door cannot be closed normally are not uncommon. Under the general environment where the State Administration of Work Safety has repeatedly ordered and emphasized safe production, qualified units will move the safety door by themselves. No conditions can only be "sighing at the door." ; In fact, for die casting machine manufacturers, there is no need to increase the cost too much. The front safety door bracket can be made into a telescopic structure. If necessary, the safety door can be moved a certain distance to deal with those special molds, and then it can be restored. To the original location.
4. Other
4.1 Nitrogen pressurization technology
Die-casting machines generally use nitrogen energy storage devices for energy storage. For ordinary die-casting machines, fast pressure accumulators and booster accumulators require nitrogen pressure ranging from 6.0 to 13Mpa, especially for fast pressure accumulators. The pressure is high, and sometimes it is urgent to inflate after the production adjustment, and the pressure of the nitrogen bottle is insufficient, which will cause the equipment to stop and wait. In order to change this situation and make full use of the nitrogen in the gas cylinder, it is recommended that the die casting machine manufacturer can attach a set of nitrogen The pressurization device uses the pressure of the hydraulic system of the die-casting machine as power to complete the pressurization work of filling nitrogen.
4.2 Pre-installed internal spraying/air blowing control system
The good spraying effect of mold lubricant is the key factor to obtain good casting surface quality. Due to the structure of the casting, after part of the mold core is pulled out, the core forming part is hidden in the lining mold or a certain slider block, and the coating cannot be sprayed. In order to improve the spraying effect of this type of core, some manufacturers have proposed the concept of internal spraying.
At the same time, in the die-casting production process, with the long-term use of the mold, there are often aluminum chips and burrs between the sliding core slider and the slide on the die-casting mold. If these aluminum chips and burrs cannot be removed in time, they will As a result of the deformation of the slider and the size of the die-casting parts cannot meet the actual requirements, some manufacturers have proposed to add a blowing device to the mold insert to solve the problem of automatically cleaning the slider .
The above two problems are urgently needed to be solved in die casting production practice. Due to the control procedures of die casting machines, it is very difficult for die casting plants to solve them; if equipment manufacturers come to solve them, then these two problems can be combined into one. To solve the problem, there is no need to increase the cost too much, just reserve the control interface for internal spraying and configure the corresponding electromagnetic reversing valve.
4.3 WiFi networking of die casting machine
Today, when the Internet is highly developed, WiFi has become an indispensable standard in our lives. We can make good use of Internet technology to develop a simple and easy-to-use die-casting machine networking management software to query each device in real time on the network Production status, order completion status and real-time process management; even die-casting machine manufacturers can remotely diagnose, debug, and repair the die-casting machine through Internet technology, and the technicians of the die-casting machine manufacturer can stay at home It can serve customers all over the world; at the same time, as a die-casting company, it can also spend less cost to enjoy more high-quality and convenient after-sales service.
5. Provide necessary data for die casting machine
In modern society, it is impossible to compete without the necessary awareness of confidentiality, but it is necessary to provide data related to the user’s use; Data such as injection speed is not easy to obtain, resulting in extremely limited applications, which restricts the development and progress of die-casting technology; the general status of die-casting technology is that there is experience but no theory, and it stays at the stage of empiricism for a long time.
The cross-sectional view of the die-casting machine frame in the mold work area is a drawing that is not provided in the manual of each die-casting machine manufacturer. Everyone seems to be used to it; however, if the actual mold design only considers the impact of the template size and the distance between the tie rods, it is for some special structures. The mold will cause hidden dangers such as interference between the mold and the rack rail.
Most of the above-mentioned ideas and suggestions are some additional functions with low cost, convenient and practical. We hope to provide some ideas and suggestions for our die-casting equipment manufacturers to produce more and better die-casting equipment to serve our die-casting production.
Link to this article: Add additional functions of die-casting machine to meet the needs of die-casting process
Reprint Statement: If there are no special instructions, all articles on this site are original. Please indicate the source for reprinting:https://www.cncmachiningptj.com/,thanks!
PTJ® provides a full range of Custom Precision cnc machining china services.ISO 9001:2015 &AS-9100 certified. 3, 4 and 5-axis rapid precision CNC machining services including milling, sheet metal to customer specifications,Capable of metal & plastic machined parts with +/-0.005 mm tolerance.Secondary services include CNC and conventional grinding, laser cutting,drilling,die casting,sheet metal and stamping.Providing prototypes, full production runs, technical support and full inspection.Serves the automotive, aerospace, mold&fixture,led lighting,medical,bicycle, and consumer electronics industries. On-time delivery.Tell us a little about your project’s budget and expected delivery time. We will strategize with you to provide the most cost-effective services to help you reach your target,Welcome to Contact us ( sales@pintejin.com ) directly for your new project.
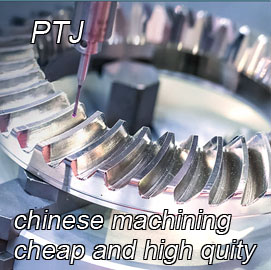
- 5 Axis Machining
- Cnc Milling
- Cnc Turning
- Machining Industries
- Machining Process
- Surface Treatment
- Metal Machining
- Plastic Machining
- Powder Metallurgy Mold
- Die Casting
- Parts Gallery
- Auto Metal Parts
- Machinery Parts
- LED Heatsink
- Building Parts
- Mobile Parts
- Medical Parts
- Electronic Parts
- Tailored Machining
- Bicycle Parts
- Aluminum Machining
- Titanium Machining
- Stainless Steel Machining
- Copper Machining
- Brass Machining
- Super Alloy Machining
- Peek Machining
- UHMW Machining
- Unilate Machining
- PA6 Machining
- PPS Machining
- Teflon Machining
- Inconel Machining
- Tool Steel Machining
- More Material