Talking about the development and application of automobile casting process and casting technology
At present, the production technology of automobile castings in developed countries in the European and American automobile industries is advanced, with good product quality, high production efficiency and low environmental pollution. Casting raw and auxiliary materials have been serialized and standardized, and the entire production process has been mechanized, automated, and intelligent. These countries generally use digital technology to improve the level of casting process design.
The casting rejection rate is about 2% to 5%, and a transnational service system has been established and network technical support has been implemented. In contrast, although the output of automobile castings in my country is relatively large, most of them are black castings with low added value and technical content, and relatively simple structure, which is far behind the foreign level. This article mainly discusses the development direction of automobile castings and automobile technology from the development needs of automobile energy saving and environmental protection.
Casting is one of the oldest metal forming methods. About 15% to 20% of auto parts are castings produced by different casting methods. These castings are mainly key components of the power system and important structural components.
1. The development direction of automobile castings
1.1 Integrated design of automobile castings
With the increasing requirements for energy conservation and environmental protection of automobiles and reduction of production costs, we will make full use of the advantages of casting to realize the casting of integrated parts through reasonable design and structural optimization of several parts formed by stamping, welding, forging and casting. Forming can effectively reduce the weight of parts and reduce unnecessary processing processes, thereby achieving lightweight and high-performance parts.
Figure 1 shows the integrated axle housing developed by FAW Group to replace the new products of welded axle housings and cast axle housings with half-axle sleeves to realize the integrated casting of castings and make full use of the advantages of casting. At present, the main form of common cast monolithic axle housing is to press seamless steel pipes at both ends of the axle housing as half-axle sleeves, and fix them with pins to form the axle housing assembly. In order to further improve the strength and rigidity of the axle housing and simplify the process, FAW Group has developed an integrated axle housing in which the axle sleeves (the parts on both sides of the axle housing in Figure 1) are directly cast on the axle housing. Processing is difficult, cost reduction is more, axle housing structure tends to be simple, and axle housing rigidity is better, can be made into complex and ideal shape, wall thickness can be changed, ideal stress distribution can be obtained, and its strength and rigidity are both large , Work reliably. Due to the integration of the axle sleeve, the size of the casting has been significantly increased. The length of the casting is 2 258 mm, and its single piece weight exceeds 200 kg. In view of the characteristics of this integrated casting, the company has established a dedicated production line to ensure production.
The development trend of integration of automobile castings is more obvious in the development of non-ferrous alloy castings. In order to make full use of the characteristics of the casting process that can achieve the production of complex structure castings, integrated design of high-pressure castings such as door inner panels, seat frames, instrument panel frames, front-end frames and firewalls have emerged. The dimensions are significantly larger than those currently produced. For castings, a die casting machine with a tonnage of 4 000 to 5 000 tons or even greater is required for production.
1.2 Lightweight of automobile castings
On the premise of ensuring the strength and safety of the car, reduce the curb weight of the car as much as possible to achieve light weight, thereby improving the power of the car, reducing fuel consumption, and reducing exhaust pollution. For every 100 kg reduction in vehicle kerb weight, fuel consumption per 100 kilometers can be reduced by 0.3 to 0.6 L. If the vehicle weight is reduced by 10%, fuel efficiency can be increased by 6% to 8%. With the need for environmental protection and energy saving, the lightweight of automobiles has become the trend of the world's automobile development, and the lightweight of automobile castings has also become one of the important development directions of automobile castings.
1.2.1 Lightweight design of automobile castings
Due to the need for the overall safety factor of castings, equal thickness design is one of the main design methods for automotive castings. However, the main disadvantage of the equal-thickness design is the inability to give full play to the structural performance and result in an increase in the weight of the casting. Use CAE analysis, topology optimization and other methods to optimize the design of parts so that the stress values of various parts of the parts are close, that is, the wall thickness of each part is inconsistent, and the parts with small forces are thinned or unnecessary to reduce the parts. the weight of. Considering that casting forming can realize the forming of complex structure castings, various irregular shaped cross-sections can be realized. When designing, use CAE or topology optimization to perform stress analysis on components. According to the force distribution, the shape of the part and the material thickness of the specific part are determined. By reinforcing, digging holes and thickening the castings, the weight of the parts can be greatly reduced.
1.2.2 Light alloy automobile castings
The use of light alloy materials such as aluminum and magnesium is currently the main weight reduction measure for automobile manufacturers in various countries. The density of aluminum is only 1/3 of that of steel, and it has excellent corrosion resistance and ductility. Magnesium has a lower density, only 2/3 of that of aluminum, and has excellent fluidity under high-pressure casting conditions. The specific strength (strength to mass ratio) of aluminum and magnesium is quite high, which plays a decisive role in reducing self-weight and improving fuel efficiency. The increasing competitiveness of the US automobile industry in the past two years is closely related to its large-scale adoption of aluminum-magnesium structural castings and integrated castings.
The new 5 series launched by the German BMW company is equipped with the latest generation of magnesium-aluminum composite inline six-cylinder engine block, the weight is reduced by 10 kg compared with the previous generation, which greatly improves the performance and fuel economy. However, it should be noted that the price of raw materials for light alloys such as aluminum and magnesium is much higher than that of steel materials, which limits its wider application in the automotive industry. However, despite the relatively high price of raw materials, the current consumption of magnesium and aluminum castings for bicycles has been increasing year after year. On the one hand, technological progress has made up for the increase in costs. On the other hand, market competition has forced automakers to reduce profits and adopt more light alloys. However, to greatly increase the amount of light alloys and reduce the purchase price of magnesium and aluminum ingots, the development of advanced forming technology is one of the keys.
1.2.3 High performance of automotive casting materials
Improving the performance of the material so that the parts of unit weight can withstand higher loads is one of the methods to effectively reduce the weight of castings. Bracket type structural castings account for a large proportion of automobile castings, so the development of its castings has become one of the focuses of attention. Through heat treatment and other measures, the microstructure of the material is changed, thereby improving the strength, rigidity or toughness of the parts, which can effectively reduce the weight of the parts.
Austempered ductile iron not only has higher strength than ordinary cast steel materials, but also has a lower density than steel. Its density is 7.1 g/cm3, while the density of cast steel is 7.8 g/cm3, which is a widely recommended material in recent years. . It adopts austempered ductile iron, which is 10% lighter than steel castings under the same size of castings. Dongfeng Motor Corporation has carried out a lightweight verification work on a certain type of commercial vehicle using austempered ductile iron instead of steel castings, and redesigned 14 suspension parts in expert forums based on the high strength characteristics of austempered ductile iron. Table 1 shows the lightweight effect after the replacement of austempered ductile iron materials, the total weight is reduced by nearly 40%, and the effect is significant. It should be noted that the lightweight effect in Table 1 is not only caused by material substitution, but also includes the contribution of lightweight design. Generally speaking, the material replacement of automobile castings often accompanies the lightweight design of the parts.
In aluminum alloy and magnesium alloy castings, high-strength and high-toughness materials are also used to replace them. On the basis of the original light alloy weight reduction, high-performance materials are used to further reduce weight. General Motors of the United States uses high-performance AE44 alloy instead The original aluminum alloy uses high-pressure casting to produce the sub-frame, further reducing the weight of the aluminum alloy by 6 kg.
1.3 Digitalization of automobile casting development
The comprehensive combination of automobile casting development and digital technology can significantly improve the level of casting technology and shorten the product design and trial production cycle. At present, digital manufacturing technology has been widely used in the development of automobile castings. In the stage of casting structure design and casting process design, three-dimensional design software such as Pro/E, CATIA, and UG has been widely used, and some advanced casting companies have realized paperless design. Software such as MAGMA, ProCAST and Huazhu CAE have been widely used to simulate the solidification process, microstructure, composition segregation and material properties of automobile castings. It can also analyze the velocity field, concentration field, temperature field and phase in the casting process. Simulation of fields, stress fields, etc., can ensure that the process plan is optimized before mass production.
In order to meet the needs of rapid development of automobile castings, based on the design and development of CAD/CAE, RP (rapid prototyping technology) has been widely used for rapid trial production of automobile castings. After obtaining the original CAD/CAE data, the layer-by-layer method is adopted to obtain the prototype of the casting or the prototype of the mold required to form the casting by bonding, sintering or sintering. The former can be trial-produced casting samples by investment casting, plaster casting and other methods, while the latter can be used directly as a mold to make sand cores, and the castings can be poured through core assembly modeling. In addition, the powder laser sintering method (SLS) can be used to directly complete the production of sand cores and sand molds, so as to obtain the sand molds required for trial production of castings. For outer molds with relatively simple structures, CNC machine tools can also be used to process CAM with machinable plastics to obtain the core box and pattern required for trial production of castings, or directly process the sand block to obtain the sand mold of the outer mold directly.
Generally speaking, digital technology has penetrated all links of casting design, development and trial production, effectively improving the development speed and efficiency of castings. The main problem at present is that the digital technologies of design, analysis, and rapid manufacturing are independent of each other. When the development process is transformed from one stage to another, quite tedious data conversion work is also required. It is hoped that in the future, a unified data interface platform can be developed for the digital technology applied in all aspects of casting development, and standardized data conversion standards can be established to achieve seamless data conversion between different software, so as to further increase the development speed of castings.
2. The development direction of automobile casting technology
2.1 Production technology of thin-walled complex structure castings
With the development of the automobile industry and the demand for energy saving and emission reduction, the weight of automobile parts is becoming increasingly lighter. Through thin-walled design, weight reduction is an important development direction of engine cylinder blocks. Take FAW Casting Co., Ltd. for FAW-Volkswagen's production of cast iron cylinder blocks as an example. The early-produced 06A cylinder block has a wall thickness of 4.5mm ± 1.5 mm, and the EA111 cylinder block has a wall thickness of 4 mm ± 1 mm. The currently mass-produced EA888Evo2 cylinder block has a wall thickness 3.5 mm ± 0.8 mm, the next-generation EA888Gen.3 cylinder block product structure is more complex, its wall thickness is only 3mm ± 0.5 mm, it is currently the thinnest gray cast iron cylinder block. Although there are problems with broken cores, floating cores, and large wall thickness fluctuations in mass production, by controlling the quality of sand cores and molding sand, the widely used horizontal pouring process can still meet the production requirements of EA888Evo2 cylinders. But it cannot meet the production requirements of EA888Gen.3 cylinder block, so the whole core assembly vertical casting process must be adopted.
In view of the 3 mm thin wall characteristics of the cylinder body, the core assembly vertical casting process puts forward stringent requirements on both core making and core assembly. The core-making center can realize highly intelligent and automated core-making production. The whole process from the addition of raw sand and resin, sand mixing, core making, core repair, assembly, coating and drying to modeling and core assembly can be fully automated, so that the core making quality and assembly quality of the sand core, namely the dimensional accuracy and The coating drying quality has been stably guaranteed, thereby avoiding quality and size risks caused by human factors, and adapting to the needs of mass production of cylinder cores. It can effectively solve the problem of unstable and high scrap rate in mass production. At the same time, due to the improvement of the dimensional accuracy of the sand core, it also greatly reduces the cleaning workload and cost, and can effectively ensure the 3mm wall thickness requirement.
2.2 Manufacturing technology of aluminum-magnesium alloy large-scale structural parts
With the increasing requirements for energy saving, environmental protection, and reduction of component costs, large-scale aluminum-magnesium alloy structural castings have become an important development trend, and their manufacturing technology has also become a current development focus. At present, the main production technologies for large-scale aluminum-magnesium alloy structural parts include high-pressure casting, squeeze casting and low-pressure casting. Due to the high production efficiency of high-pressure casting and good product quality, it has become the main production process at present. The development of its manufacturing technology is mainly focused on the easy entrainment of gas during the high-pressure casting process, and the formation of pores inside the castings, which cannot improve the problem of heat treatment.
The German Fulai company has developed a vacuum suction casting process. Its working principle is shown in Figure 4. The entire die-casting process is carried out under high vacuum (less than 30 mbar). The molten metal passes through the mold, the pressure chamber and the suction pipe in a vacuum state and is sucked from the furnace by the suction pipe without oxidation, and the vapor of the release agent is also discharged by the vacuum system. The main features of the above-mentioned vacuum negative pressure suction casting process are: when quantitative pouring is started, the entire system is in a high vacuum state; in the quantitative pouring process, the gas in the cavity and the molten metal can be effectively discharged; during the pouring process There is no oxidation of the metal melt; there is no heat loss during the pouring process, and a lower pouring temperature can be used for pouring, and the non-disturbed laminar flow filling can be carried out under real-time monitoring. The above process has been successfully applied to the mass production of automobile structural castings of the Auto Expert Forum, providing advanced forming methods and processes for the application of high-quality light alloy castings.
The Swiss company Buhler has developed a dual-circuit vacuum system for the production of structural castings. This production technology is called the production technology of structural parts, as shown in Figure 5. The use of structural parts production technology can increase the speed of vacuuming, thereby obtaining stable production conditions and significantly improving the quality of die castings. As shown in Fig. 5, the air extraction port of one circuit in the dual-circuit vacuum system is arranged at the upper end of the pressure chamber, and is mainly used to extract air in the pressure chamber. It starts when the injection punch moves forward to seal the pouring port, and closes when the punch is about to seal the suction port. The other circuit setting is the same as that of the traditional vacuum process, and is mainly used to extract air from the cavity. At present, this technology has been successfully applied to the manufacture of aluminum alloy integrated shock towers, door inner panels and body rails of passenger cars.
2.3 Precision casting forming technology of castings
Generally speaking, the precision casting of automobile castings mainly refers to lost foam and investment casting technology. With the development of automobile casting forming technology, casting precision forming refers to a type of casting forming method. Castings produced by this type of forming method can be used directly without cutting or less cutting. With the increasing requirements for the dimensional accuracy of castings, precision casting technology has developed rapidly in recent years, and a series of new casting methods such as precision sand casting, lost foam casting, controlled pressure casting, and pressure casting have emerged. The Cosworth casting method is a method developed by the United Kingdom that uses zirconium sand core assembly and electromagnetic pump to control the pouring. It has been successfully used in the mass production of aluminum alloy cylinder blocks, and many process variants have appeared, such as the use of low-pressure pouring instead of electromagnetic Processes such as pump pouring. This type of casting method can produce aluminum alloy cylinders with a wall thickness of 3.5 to 4.0 mm, which is the current representative process of precision sand casting.
Since the lost foam casting process was invented in 1965, the main automotive castings produced are cylinder blocks, cylinder heads, intake and exhaust pipes and other products, and have formed large-scale production. Since the introduction of lost foam casting technology in the 1990s in the 20th century, my country has begun to take shape and has been promoted by the state as the most widely used high and new technology to transform the traditional foundry industry. At present, there are three investment precision casting processes in my country: sodium silicate shell, composite shell and silica sol shell. Among them, the surface quality of the casting used in the production of silica sol shell for automobile products can reach Ra 1.6 μm, and the dimensional accuracy can reach CT4. Grade, the minimum wall thickness can be 0.5~1.5 mm. Dongfeng Motor Precision Casting Co., Ltd. adopts the silica sol + water glass composite shell making process to produce complex structure integrated castings, which significantly reduces production costs. The development trend of investment casting technology molding process is that castings are getting closer and closer to the final product, and the complexity and quality of the products are getting higher and higher. The application of CAD, CAM and CAE has become the main technology of product development, and professional cooperation Began to show up.
Process methods such as vacuum casting, oxygen-filled die casting, semi-solid metal rheological or thixotropic die casting developed on the basis of high-pressure casting technology are designed to eliminate casting defects, improve internal quality, and expand the application range of die castings. During the squeeze casting process, the melt is filled and solidified under pressure, which has the advantages of smoothness, no metal splash, less metal liquid oxidation loss, energy saving, safe operation and reduction of casting holes and other defects. It is used in aluminum alloy subframes, etc. The development and application of high-performance aluminum alloy castings have been widely used.
The continuous growth of automobile output urgently requires the development of casting production in the direction of high quality, excellent performance, near net shape, multiple varieties, low consumption and low cost. Because about 15% to 20% of the parts of a complete vehicle are castings. This requires the casting industry to continuously apply various new technologies and new materials to improve the overall level of casting. The precision casting forming technology of castings can meet the above-mentioned requirements of automobile castings, and its application will also cover different casting production processes of automobile castings.
3. Conclusion
In order to adapt to the increasingly stringent requirements of environmental protection regulations, automobiles are developing in the direction of lighter weight. For every 10% reduction in vehicle weight, fuel consumption can be reduced by 5.5%, fuel economy can be increased by 3% to 5%, and emissions can be reduced by about 10%. The application of aluminum-magnesium and other non-ferrous alloy castings, the development of large-scale complex structure integrated castings, and the widespread application of casting precision forming technology are the main ways to achieve lightweight automotive castings. Therefore, it is required to realize the research and development and production of automobile castings by means of high-performance casting materials and extensive application of automation equipment on the basis of the extensive use of digital technology to meet the needs of the modern automobile industry.
Link to this article: Talking about the development and application of automobile casting process and casting technology
Reprint Statement: If there are no special instructions, all articles on this site are original. Please indicate the source for reprinting:https://www.cncmachiningptj.com/,thanks!
PTJ® provides a full range of Custom Precision cnc machining china services.ISO 9001:2015 &AS-9100 certified. 3, 4 and 5-axis rapid precision CNC machining services including milling, sheet metal to customer specifications,Capable of metal & plastic machined parts with +/-0.005 mm tolerance.Secondary services include CNC and conventional grinding, laser cutting,drilling,die casting,sheet metal and stamping.Providing prototypes, full production runs, technical support and full inspection.Serves the automotive, aerospace, mold&fixture,led lighting,medical,bicycle, and consumer electronics industries. On-time delivery.Tell us a little about your project’s budget and expected delivery time. We will strategize with you to provide the most cost-effective services to help you reach your target,Welcome to Contact us ( sales@pintejin.com ) directly for your new project.
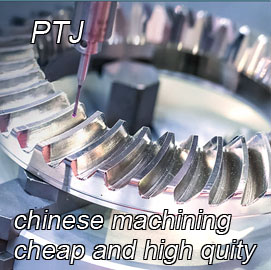
- 5 Axis Machining
- Cnc Milling
- Cnc Turning
- Machining Industries
- Machining Process
- Surface Treatment
- Metal Machining
- Plastic Machining
- Powder Metallurgy Mold
- Die Casting
- Parts Gallery
- Auto Metal Parts
- Machinery Parts
- LED Heatsink
- Building Parts
- Mobile Parts
- Medical Parts
- Electronic Parts
- Tailored Machining
- Bicycle Parts
- Aluminum Machining
- Titanium Machining
- Stainless Steel Machining
- Copper Machining
- Brass Machining
- Super Alloy Machining
- Peek Machining
- UHMW Machining
- Unilate Machining
- PA6 Machining
- PPS Machining
- Teflon Machining
- Inconel Machining
- Tool Steel Machining
- More Material