Brief introduction of polishing equipment and its working principle
The polishing machine equipment is a kind of electric tool. The polishing machine equipment is composed of basic elements such as a base, a polishing plate, a polishing fabric, a polishing cover and a cover.
Introduction:
The motor is fixed on the base, and the taper sleeve for fixing the polishing disc is connected with the motor shaft by screws. The polishing fabric is fastened on the polishing disk by the ferrule, and the motor is started by the switch on the base, and then the sample can be pressed by hand to polish on the rotating polishing disk. The polishing liquid added in the polishing process can flow into the square plate beside the polishing machine equipment through the drain pipe in the plastic plate fixed on the base. The polishing cover and cover can prevent dirt and other sundries from falling on the polishing fabric when the machine is not in use and affecting the use effect.
working principle
The key to the operation of the polishing machine is to try to get the maximum polishing rate in order to remove the damage layer generated during polishing as soon as possible. At the same time, the polishing damage layer should not affect the final observed tissue, that is, it will not cause false tissue. The former requires the use of coarser abrasives to ensure a greater polishing rate to remove the polished damage layer, but the polishing damage layer is also deeper; the latter requires the use of the finest material, so that the polishing damage layer is shallower but polished The rate is low.
The best way to solve this contradiction is to divide the polishing into two stages. The purpose of rough polishing is to remove the polished damage layer. This stage should have the maximum polishing rate. The surface damage caused by rough polishing is a secondary consideration, but it should be as small as possible; the second is fine polishing (or final polishing). Its purpose is to remove surface damage caused by rough polishing and minimize polishing damage. When polishing machine equipment, the grinding surface of the sample and the polishing disk should be absolutely parallel and evenly pressed on the polishing disk. Take care to prevent the sample from flying out and creating new wear marks due to excessive pressure. At the same time, the sample should be rotated and moved back and forth along the radius of the turntable to avoid local abrasion of the polishing fabric too fast. In the polishing process, the micro-powder suspension should be continuously added to keep the polishing fabric at a certain humidity. Too much humidity will weaken the effect of polishing wear marks, causing the hard phase in the sample to appear embossed and non-metallic inclusions in steel and graphite phase in cast iron to produce "tailing"; when humidity is too low, friction and heat will cause the sample When the temperature rises, the lubrication effect is reduced, the grinding surface loses its luster, and even black spots appear, and the light alloy will damage the surface. In order to achieve the purpose of rough polishing, the rotation speed of the turntable is required to be low, preferably not more than 600r/min; the polishing time should be longer than the time required to remove the scratches, because the deformed layer must be removed. After rough polishing, the grinding surface is smooth, but dull and dull. There are even and fine wear marks under the microscope, which need to be eliminated by fine polishing.
The speed of the turntable can be appropriately increased during the fine polishing, and the polishing time is appropriate to throw away the damaged layer of the rough polishing. After fine polishing, the polished surface is bright as a mirror, and no scratches can be seen under the bright field of the microscope, but the wear marks can still be seen under the phase contrast illumination. The polishing quality of the polishing machine has a serious impact on the structure of the sample, which has gradually attracted the attention of relevant experts. In recent years, a lot of research work has been done on the performance of polishing machine equipment at home and abroad, and many new models and a new generation of polishing equipment have been developed. The original manual operation is developing into a variety of semi-automatic and fully automatic Polishing machine equipment.
Link to this article: Brief introduction of polishing equipment and its working principle
Reprint Statement: If there are no special instructions, all articles on this site are original. Please indicate the source for reprinting:https://www.cncmachiningptj.com/,thanks!
Sheet metal, beryllium, carbon steel, magnesium, 3D printing, precision CNC machining services for heavy equipment, construction, agriculture and hydraulic industries. Suitable for plastics and rare alloys machining. It can turn parts up to 15.7 inches in diameter. Processes include swiss machining,broaching, turning, milling, boring and threading. It also provides metal polishing, painting, surface grinding and shaft straightening services. The production range(include aluminum die casting and zinc die casting) is up to 50,000 pieces. Suitable for screw, coupling, bearing, pump, gearbox housing, drum dryer and rotary feed valve applications.PTJ will strategize with you to provide the most cost-effective services to help you reach your target,Welcome to Contact us ( sales@pintejin.com ) directly for your new project.
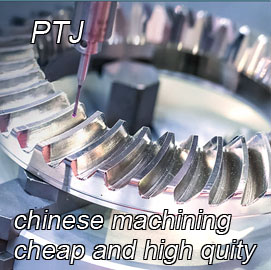
- 5 Axis Machining
- Cnc Milling
- Cnc Turning
- Machining Industries
- Machining Process
- Surface Treatment
- Metal Machining
- Plastic Machining
- Powder Metallurgy Mold
- Die Casting
- Parts Gallery
- Auto Metal Parts
- Machinery Parts
- LED Heatsink
- Building Parts
- Mobile Parts
- Medical Parts
- Electronic Parts
- Tailored Machining
- Bicycle Parts
- Aluminum Machining
- Titanium Machining
- Stainless Steel Machining
- Copper Machining
- Brass Machining
- Super Alloy Machining
- Peek Machining
- UHMW Machining
- Unilate Machining
- PA6 Machining
- PPS Machining
- Teflon Machining
- Inconel Machining
- Tool Steel Machining
- More Material