Analysis on the Development Status of Aluminum Profile Anodizing and Electrolytic Coloring Technology
Aluminum anodic oxide film has porosity and absorbability, which is the most ideal color carrier. Coloring can not only improve the decoration and corrosion resistance of the product, but also give the surface of aluminum products various functional characteristics and increase commercial value. At present, many oxide film coloring technologies have been developed, which can be roughly divided into chemical coloring and electrolytic coloring.
my country's electrolytic coloring technology began in the 1980s, and currently basically electrolytic coloring is based on single nickel salt, single tin salt or tin-nickel mixed salt. AC coloring is based on tin-nickel mixed salt and tin salt electrolytic coloring process. AC coloring is used to control the color depth, which is mainly controlled by voltage and time. This process has problems such as single color, poor stability and dispersibility of the coloring liquid, which have not been well resolved all the time. And some additives need to be added to improve the anti-impurity interference ability of the electrolytic coloring solution. DC coloring is dominated by single nickel salt, and single nickel salt injection coloring is to use commutation DC coloring to control the color depth, which is controlled by adjusting the waveform and time period; this process has stable bath, good coloring uniformity, and repeatability Good sex and stable color tone.
The treatment of wastewater produced by the surface treatment of aluminum profile anodizing has always been a concern for environmental protection. The wastewater mainly comes from the discharge of the washing tank. In order to reduce the consumption of chemicals and reduce the discharge of wastewater, the recycling of chemicals as much as possible will eventually achieve energy saving and emission reduction. the goal of.
Pros and cons
1. Tin salt coloring
Tin salt coloring is divided into single tin salt coloring and tin-nickel mixed salt coloring. During the coloring process of nickel-tin mixed salt, nickel ions are not deposited in the pores of the oxide film, but only play an auxiliary role, so tin—— Nickel salt coloring can also be called tin salt coloring.
Tin salt coloring is relatively simple to control compared to single nickel salt, and the equipment cost is lower, and it is widely used in oxidation horizontal production lines; but the SnSO4 in the tin salt coloring bath is very easy to oxidize to produce tetravalent tin precipitation; The tank solution is mixed with double salts, and nickel ions cannot be recovered. After washing, the wastewater is discharged to the wastewater treatment station for treatment, which increases the difficulty of wastewater treatment. Both of these two coloring methods need to add additives to keep the tank liquid clear and stable; when the production reaches a certain amount, the tank liquid is easy to be turbid, and the production needs to be stopped for regeneration and precipitation treatment to obtain a clear tank liquid, otherwise the tank liquid is turbid The product quality cannot be guaranteed. In the vertical production line, tin salt is used for coloring. Because the tank body is relatively deep, generally above 7 meters, the precipitation of tetravalent tin will cause the concentration of the tank solution to be uneven and present a gradient state, which is easy to produce obvious upper and lower color differences during coloring. The tin salt coloring has the defect of weather resistance, and gradually there are signs of fading with the increase of sunshine time.
2. Single nickel salt coloring by injection method
Adopting commutation direct current coloring, using H3BO3 as a buffer to stabilize the pH value of the bath solution. Through special positive and negative voltage waveforms, nickel ions are uniformly electrolytically resolved at the bottom of the anodic oxide film pores, and the coloring The aluminum alloy profile obtains a stable and uniform color.
The color depth is controlled by calculating the number of auxiliary waves. The dark material needs to be superimposed on the basic waveform with 1-N auxiliary waves that are the same or similar to the basic waveform to achieve the purpose of making the dark material.
The nickel ion content of the single nickel salt coloring process of the injection method is very high, and the amount of the surface of the profile after coloring is large. The direct discharge of the washing tank liquid is wasteful and pollutes the environment. The RO reverse osmosis principle method is used for recycling. The recovered wastewater can be directly discharged without harming the environment.
2. 1RO recovery principle of single nickel salt coloring by injection method
RO is a method in which when a pressure above the osmotic pressure of the solution (usually 10㎏/㎝2) is applied, the water in the coloring liquid is permeated through the semipermeable membrane, while the nickel ions are prevented from passing through and remain on the surface of the membrane, so that the solution Salts, ions, etc. are all retained on the membrane surface to achieve the purpose of separation.
2.2 Recycling process
The nickel recovery treatment system is used to reuse the nickel ions in the coloring tank. The tank liquid from the coloring tank is pressurized into the filter to remove particles and colloids in the water, and then enters the nickel recovery treatment system. The nickel ions in the tank liquid are exchanged, adsorbed, and enriched to obtain a higher concentration of nickel-containing recovery liquid, which is reused in the coloring tank. On the other hand, after the bath liquid is systematically processed, most of the impurities and nickel ions are removed, so that the water quality becomes better and can be reused in the production process. The whole system can realize dual recovery of waste water and nickel, which has good economic and environmental benefits. The treated water is directly reused in the washing tank for recycling. The recovery device effectively reduces the loss of nickel ions, reduces sewage charges for enterprises, creates economic benefits, improves product quality, and can meet the requirements of environmental protection and cleanliness.
After the recovery treatment, the nickel ion in the water is low, and the amount taken out in the RO2 production is very small, and it flows to the waste water station together with other production wastewater for unified treatment.
In actual production, all nickel sulfate is not used for the coloration of microporous nickel ion electrodeposition of the anodic oxide film, but more than 2/3 of the nickel sulfate is dissolved in clean water and discharged with the clean water from the profile; single nickel salt injection The coloring process does not use additives, and is equipped with an RO recovery device. The nickel salt can be recycled and used, with low loss and environmental protection. The installation of nickel recovery equipment, based on the annual output capacity of 6,000 tons of coloring materials of the vertical oxidation line, can reduce the discharge of nickel sulfate by about 15 tons per year.
Advantages: energy saving: 10-15μm oxide film can make uniform black material. Time-saving and high-efficiency: The coloring time of pure black material is 6-7 minutes, which is 2/3 time-saving than the traditional coloring time. Low loss: one coloring tank can be used for continuous and batch production including champagne material, bronze material and black material. And the color tone is stable, the reproducibility is good, the color is uniform, and the profile has good weather resistance.
Tin salt (or tin-nickel salt) has electrolytic coloring additives, and contains harmful organic reducing agents and complexing agents with different compositions and concentrations, which seriously affects the COD and BOD pollution indicators of the discharged water from wastewater treatment. The tin-nickel salt bath has both organic reducing agent complexing agent and nickel ions double pollution, and the complexing agent also affects the removal of nickel ions in the double salt. The composition of the single nickel salt bath solution is very simple, and there is no organic reducing agent complexing agent. The nickel ion removal is relatively simple and easy, and the degree of automation is improved. Therefore, single nickel salt discharge water treatment is more convenient than tin-nickel mixed salt, that is, environmental protection treatment measures are relatively simple.
Link to this article: Analysis on the Development Status of Aluminum Profile Anodizing and Electrolytic Coloring Technology
Reprint Statement: If there are no special instructions, all articles on this site are original. Please indicate the source for reprinting:https://www.cncmachiningptj.com/,thanks!
Sheet metal, beryllium, carbon steel, magnesium, 3D printing, precision CNC machining services for heavy equipment, construction, agriculture and hydraulic industries. Suitable for plastics and rare alloys machining. It can turn parts up to 15.7 inches in diameter. Processes include swiss machining,broaching, turning, milling, boring and threading. It also provides metal polishing, painting, surface grinding and shaft straightening services. The production range is up to 50,000 pieces. Suitable for screw, coupling, bearing, pump, gearbox housing, drum dryer and rotary feed valve applications.PTJ will strategize with you to provide the most cost-effective services to help you reach your target,Welcome to Contact us ( sales@pintejin.com ) directly for your new project.
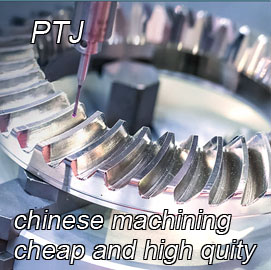
- 5 Axis Machining
- Cnc Milling
- Cnc Turning
- Machining Industries
- Machining Process
- Surface Treatment
- Metal Machining
- Plastic Machining
- Powder Metallurgy Mold
- Die Casting
- Parts Gallery
- Auto Metal Parts
- Machinery Parts
- LED Heatsink
- Building Parts
- Mobile Parts
- Medical Parts
- Electronic Parts
- Tailored Machining
- Bicycle Parts
- Aluminum Machining
- Titanium Machining
- Stainless Steel Machining
- Copper Machining
- Brass Machining
- Super Alloy Machining
- Peek Machining
- UHMW Machining
- Unilate Machining
- PA6 Machining
- PPS Machining
- Teflon Machining
- Inconel Machining
- Tool Steel Machining
- More Material