The Measures To Improve Stamping Dies Durability
Improving the durability of stamping dies is very important. Stamping dies are necessary process equipment in the stamping production process, which play a decisive role in improving product quality, extending product life, and improving production efficiency. Because the stamping die loses its working size due to frequent wear during the production process, it is difficult to meet the production requirements. Therefore, we need to know how to improve the durability of stamping dies.
1. Improve the design of stamping die
Whether the stamping die design is reasonable is the basis for improving the durability of the stamping die. Therefore, when designing the stamping die, effective measures should be taken to improve the durability of the stamping die. For example, the life of the design of the small hole punching die is often reflected in the punch of the small hole. For this type of stamping die, the length of the small punch should be shortened as much as possible in the design to increase the strength. At the same time, the method of guide sleeve should be used to strengthen the small punch for protection. In addition, in the design of the stamping die, factors such as the form of the die base, the fixing method and guiding form of the convex and concave die, the determination of the pressure center, and the rigidity of the upper and lower templates should be fully considered. Especially for the blanking die, the selection of the gap value has a great influence on the durability. When designing, the gap of the stamping die should be selected reasonably, and the gap value should not be too small, otherwise it will affect the service life and durability of the stamping die. Practice has proved that, without affecting the quality of the stamping parts, a proper enlargement of the gap can greatly improve the durability of the stamping die, sometimes even several times or tens of times.
2. Correctly choose stamping die materials
Different stamping die materials have different strength, toughness and wear resistance. Under certain conditions, the use of advanced materials can increase durability several times. Therefore, in order to improve the durability of stamping dies, good materials must be selected.
3. Reasonably carry out forging and heat treatment of stamping die parts
While selecting high-quality stamping die materials, reasonable forging and heat treatment are required for materials of the same material and different properties, which is one of the main ways to improve the durability of stamping dies. For example, during quenching, if the production is overheated during heating, it will not only make the work piece too brittle, but also easily cause deformation and cracking during cooling, which will reduce the durability. Therefore, when manufacturing stamping dies, the heat treatment process must be reasonably mastered.
Toolox material is a quenched and tempered steel directly pre-hardened by the steel plant. No heat treatment is required. With proper surface treatment (such as nitriding), the high toughness of Toolox matrix material and the high hardness of the upper surface layer can achieve excellent Effect.
4. Reasonably arrange the stamping die manufacturing process and ensure the processing accuracy
The processing accuracy of the stamping die has a great influence on the durability of the stamping die. For example, due to the uneven assembly gap in the punching die, the die will often be broken under the action of shearing force and affect the life of the stamping die. At the same time, the surface finish of the stamping die is too low, which will also reduce the durability of the stamping die. Therefore, during processing, full attention must be paid to the size of the hole spacing, the perpendicularity of the punch to the fixed plate supporting surface during assembly, the uniform spacing of the stamping dies, and the guiding accuracy level of the guide sleeve and the guide post. The higher the manufacturing and assembly precision and the higher the surface roughness of the working part, the higher the durability of the stamping die.
5. Choose the correct press
In order to improve the durability of the stamping die, a press with higher precision and higher rigidity should be selected, and the stamping tonnage should be more than 30% greater than the punching force. Normally, the use of a servo punch can correspondingly increase the life of the mold by more than several tens of times.
6. Reasonable use and maintenance of stamping dies
In order to improve the durability of stamping dies, operators must use and maintain stamping dies rationally. Stamping dies should be repaired frequently, and defective dies should not be used.
Link to this article :The Measures To Improve Stamping Dies Durability
Sheet metal, Copper Milling, carbon steel,online laser cutting service, 3D printing, precision CNC machining services for heavy equipment, construction, agriculture and hydraulic industries. Suitable for plastics and rare alloys machining. It can turn parts up to 15.7 inches in diameter. Processes include swiss machining,broaching, turning, milling, boring and threading. It also provides metal polishing, painting, surface grinding and shaft straightening services. The production range(include aluminum die casting and zinc die casting) is up to 50,000 pieces. Suitable for screw, coupling, bearing, pump, gearbox housing, drum dryer and rotary feed valve applications.PTJ will strategize with you to provide the most cost-effective services to help you reach your target,Welcome to Contact us ( sales@pintejin.com ) directly for your new project.
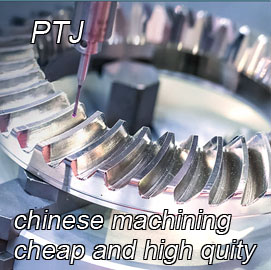
- 5 Axis Machining
- Cnc Milling
- Cnc Turning
- Machining Industries
- Machining Process
- Surface Treatment
- Metal Machining
- Plastic Machining
- Powder Metallurgy Mold
- Die Casting
- Parts Gallery
- Auto Metal Parts
- Machinery Parts
- LED Heatsink
- Building Parts
- Mobile Parts
- Medical Parts
- Electronic Parts
- Tailored Machining
- Bicycle Parts
- Aluminum Machining
- Titanium Machining
- Stainless Steel Machining
- Copper Machining
- Brass Machining
- Super Alloy Machining
- Peek Machining
- UHMW Machining
- Unilate Machining
- PA6 Machining
- PPS Machining
- Teflon Machining
- Inconel Machining
- Tool Steel Machining
- More Material