Additive manufacturing can customize various parts for aviation and medical
Additive manufacturing (AM) is a technology for producing highly customized products from almost any material. Due to design flexibility, 3D printed metal parts can be produced for a variety of applications from aerospace to medical.
However, AM's unique design has obstacles.
Newly printed metal parts require additional processing steps to remove structural supports. The rough surface finish and unreliable dimensional accuracy may not meet the standards of precision parts (such as mating surfaces and threaded holes). Since additive manufacturing does not require complexity, and parts do not have to conform to conventional orthogonal shapes, custom parts may also have shapes that make workpiece clamping particularly challenging.
Why use metal for additive manufacturing?
AM is an ideal process for metals because it does not require traditional tools to manufacture metal parts, without considering many geometric constraints, and allows parts to be merged to achieve a more efficient design. This makes a variety of metal alloys ideal materials for aerospace, automotive and medical applications, and increases the productivity of injection molding, and expands the possibilities of creative industries such as construction.
Metals that are particularly suitable for welding and casting are ideal for 3D printing. Conversely, metals that are difficult to cut or costly to machine are also ideal for additive manufacturing. Some commonly used metals suitable for 3D printing include titanium, aluminum, stainless steel and tool steel, inconel, copper and tungsten.
Titanium is popular in aerospace and medical applications due to its light weight. Using the internal lattice structure, the implant can be designed to accommodate bone ingrowth. On the other hand, steel can be used to print solid parts that can withstand extreme environments (such as combustion or high holding pressure). These and other metals can be printed from powder or molten wire.
Various techniques can be used to perform Metal AM, including selective laser sintering (SLS) for powder beds, laser metal deposition (LMD) for powders or wires, and wire directed energy deposition (WDED).
SLS has gained popularity by using "stacking" technology to make smaller parts with more complex designs, which uses a CO2 laser to melt metal powder on a descending tray in a sealed inert gas environment along the X and Y axis. When the pallet is lowered before the next pass of the laser, the rollers keep it flat.
WDED uses a laser to melt the welding wire injected through a nozzle, usually in a sealed gas enclosure. Compared with SLS, this method can obtain a higher deposition rate, but the resolution is lower. WDED is popular in applications that require simpler parts and in applications where conventional manufacturing techniques are slow or expensive, such as in the aerospace and automotive fields.
Through this technology, AM can save a lot of cost and time for difficult-to-manufacture parts, while also being able to manufacture more complex parts in smaller batches.
Metal 3D printing usually requires additional processing steps
3D printing metal parts is generally not a solution for manufacturers seeking mass production of parts. AM is ideal for small batch production, which emphasizes sheer quantity customization and unique design. Unfortunately, even a high degree of design flexibility can cause its own problems.
The printed metal parts will not be exposed from the surface of the machine and are usually made in a unique shape, so supporting structures are needed to help keep the parts upright and stable during the printing process. As a result, in order to remove the support structure and perform a surface polishing procedure, additional processing steps are required.
Renishaw's Canadian additive manufacturing business manager Mark Kirby said that removing the support frame may require manual processes such as band saws, and certain parts may require deburring, especially for applications that may not require machining.
"The irony is that the only thing we don't machine is to polish certain medical parts, such as skull plates." Kirby said. "We will do a lot of manual work to smooth it out."
If there are holes in the part, it is usually better to drill holes afterwards instead of punching holes to prevent rough surfaces from appearing in these negative spaces, and these rough surfaces usually appear at the time of improper measurement.
Although Kirby recommends printing with certain non-critical hole features with good fiducial points, any larger or particularly precise hole may be more valuable than its value.
Kirby explained that if the printing hole is not in the correct position, it may require time-consuming manual repair. "I might have to spirally interpolate it, then place it in the center where it needs to be placed, and so on. If I just drill holes, it should be in the right position."
In addition, the printed holes may be inconveniently placed on the part, and it is difficult to reach the machine tool during the finishing process.
Parts with unconventional shapes can bring other challenges when machining. In the finishing process, the parts may need to be fixed at different angles, requiring the manufacturer to fully understand where the workpiece will be associated with the cutting tool and how to interface with the worktable of the machining center.
Fixtures and vises are usually the preferred fixture solution, but this choice is not effective for 3D printed parts with complex geometries.
For more complex and delicate parts, soft jaws are a good solution because their contour can fit the part more precisely. These soft jaws can be 3D printed by themselves. Kirby found these solutions effective, but smaller printed parts (such as medical parts) are usually not designed to withstand the load tolerances of machining.
These limitations must be kept in mind when considering processing technology and appropriate fixture solutions.
Depending on the adding process, it may first be necessary to cut the fully printed metal 3D part from its base or backplane. Certain materials are very hard and abrasive, making manual band saw operation dangerous, wasteful and expensive. In this case, wire EDM or EDM is a good choice.
Brian Pfluger, Makino's EDM product line manager, said that EDM can be used as a single pass operation of parts, with extremely high repeatability and accuracy, and can be used for part removal and surface finishing. Compared with manual band saw operation, options such as Wire EDM can greatly reduce waste, and the possibility of damaging components is much smaller.
"Using Wire EDM, you can keep the final consistency of the part within about ten microns for final grinding, milling or part processing," Pfluger said. "When parts are cut, they will be more consistent and you can eliminate scrap."
Compared with traditional machining and surface finishing options, EDM is an excellent solution. It can produce oblique holes, profiled features, and finish the surface of parts with variable thicknesses.
"Every Wire EDM machine has so-called adaptive power control," Pfluger explained. Due to the dynamic change of material thickness, variable thickness is very laborious. The machine generator must be able to see, perceive and react to it. Otherwise, it will lead to disconnection. "
Usually, granular materials (such as powder) will be filtered out, but larger powder bags will destroy the system, beyond the range that the adaptive power control can compensate, and cause wire breakage, which will reduce the machine's operating speed and damage process. These cavities are stacked in hollow spaces designed as 3D parts.
When the flushing nozzle crosses this cavity, the fluid flow loses pressure, the efficiency is reduced, the pressure drops and turbulence is generated. Floating particles can damage the EDM wire. Larger diameter wires or using different types of wires can withstand a longer time, but many wire EDM machines can also automatically rethread.
Sinker EDM is another option, which specializes in smaller features that require higher accuracy and better surface finish. Sinker EDM is ideal for the production of sharp inner corner radii or blind holes that are difficult to machine.
Big Kaiser workplace product manager John Zaya explained that if Wire or Sinker EDM does not seem to be an ideal solution, hybrid machine tools include both additives and processing capabilities.
"Theoretically, what you can do is to 3D print the parts onto a plate, and then assemble them into 3D printed parts, and then the machine will enter or enter the processing mode. Then the actual cutting tools, subtractive cutting tools, will be used, And final processing of the workpiece."
In a hybrid machine, the parts are held firmly in the same fixture during both operations, thereby eliminating the trouble of positioning parts for precise machining.
Fixture solutions for metal additive manufacturing
Zaya believes that work management is one of the most important elements in the additive manufacturing process and must be considered in every step of the production process. To ensure that the part is manufacturable, considerations of size, shape and material must be included, as they are related to the fixture solution of any machine that the part will use.
Zaya said: "Through preliminary consultation with manufacturing engineers, you can avoid many problems that may occur in the production line."
Zaya went on to say that with some pre-planning, it is possible to determine whether to palletize parts onto a fixed plate or to consider special installation geometries in the design of the workpiece so that the clamping knobs can be connected after the parts are removed from the printer. To the part.
Michael said that one way to handle metal 3D printed parts is to use a 5-axis machine tool and clamp at least 1/8 inch of material, or use a dovetail, or place some positioning pins directly on the workpiece. "Basically, you can finish processing the entire machine at once, then turn it over and clean the other side."
In situations where such forward-looking solutions cannot be used (for example due to highly complex geometries or sensitive designs), soft jaws are the key. However, this method requires attention to the contour of the part and the radius of the soft jaw.
Gaunce recommends that the radius of the soft jaw be slightly smaller than the radius of the part to ensure the correct grip and clamp it at two points. Zaya added that this requires understanding how 3D printing works.
Zaya said: "When you put the workpiece in the soft jaws and the surface finish of the workpiece is very rough, it will be positioned on the'high point' of the feature." "You may not get a complete connection, and only Register in some of these areas."
When pre-designing the retention feature, the design of the part can make the retention simpler and more reliable. Zaya explained that positioning holes and fastening features can be pre-printed into workpieces or castings, while compression plates or recessed areas for fixtures or bolts can be printed into larger parts. "Pre-plan the design of the workpiece to include the clamping position or the tool position, which is very beneficial for preparing for subsequent operations."
In the worst case, the parts are particularly fragile and fragile, and there is no vise or clamp to safely complete the work. In addition, the creative team can propose particularly unique solutions for thin or small workpieces with adhesives.
Renishaw and the University of Waterloo recently collaborated to design a device for aligning the human hip joint during surgery. Due to the unique design and generative design of the part, the team nicknamed the part "Cobra". On the part, four pins need to be machined in order to install the retroreflector for the medical procedure. It is important not to deform the parts during processing.
In order to fix the part on its bottom plate, a series of pads were 3D printed and screwed to the board. Apply special glue to the backing plate to fix the parts in place.
Kirby explained: “The glue is activated by ultraviolet light to keep the parts in a non-deformed state.” “When I put the parts in a pile of glue and cured, I probably knew the position of the parts, within 1 mm. After that, we The most suitable probe must be used."
When exposed to ultraviolet light, the glue can be cured in only 90 seconds, effectively sticking the titanium part in place.
For manufacturers who want to solve the unique challenges in part design and manufacturing, metal additive manufacturing is a tool in the toolbox, but it is necessary to find an appropriate way to fix these parts for final finishing and post-processing.
Link to this article: Additive manufacturing can customize various parts for aviation and medical
Reprint Statement: If there are no special instructions, all articles on this site are original. Please indicate the source for reprinting:https://www.cncmachiningptj.com/,thanks!
Sheet metal, beryllium, carbon steel, magnesium, 3D printing, precision CNC machining services for heavy equipment, construction, agriculture and hydraulic industries. Suitable for plastics and rare alloys machining. It can turn parts up to 15.7 inches in diameter. Processes include swiss machining,broaching, turning, milling, boring and threading. It also provides metal polishing, painting, surface grinding and shaft straightening services. The production range is up to 50,000 pieces. Suitable for screw, coupling, bearing, pump, gearbox housing, drum dryer and rotary feed valve applications.PTJ will strategize with you to provide the most cost-effective services to help you reach your target,Welcome to Contact us ( sales@pintejin.com ) directly for your new project.
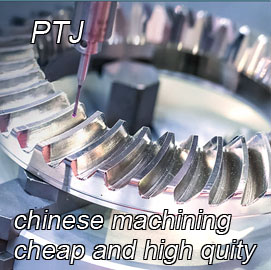
- 5 Axis Machining
- Cnc Milling
- Cnc Turning
- Machining Industries
- Machining Process
- Surface Treatment
- Metal Machining
- Plastic Machining
- Powder Metallurgy Mold
- Die Casting
- Parts Gallery
- Auto Metal Parts
- Machinery Parts
- LED Heatsink
- Building Parts
- Mobile Parts
- Medical Parts
- Electronic Parts
- Tailored Machining
- Bicycle Parts
- Aluminum Machining
- Titanium Machining
- Stainless Steel Machining
- Copper Machining
- Brass Machining
- Super Alloy Machining
- Peek Machining
- UHMW Machining
- Unilate Machining
- PA6 Machining
- PPS Machining
- Teflon Machining
- Inconel Machining
- Tool Steel Machining
- More Material