Avoid the difference in the sheet metal bending process
There are often some errors in the sheet metal bending process, so how to avoid it?
1. Avoid hiring unqualified people
Unless it's an entry-level position, don't hire unqualified people. Even so, the wrong entry-level personnel can cause headaches.
I have never been keen on human resources. Although your HR personnel may be highly qualified and touch every focus of the career, they rarely understand the nature of the work performed by the hired employee.
A bending machine operator is a good example. Many managers and human resources personnel believe that just put some tools into a machine that can move up and down (how difficult will this be?), so they are designated as entry-level minimum wage positions. However, the bending machine is the most complex machine in the sheet metal workshop, and it requires specialized knowledge. This is a difficult job.
Just because some applicants know some keywords does not mean they can find the bending machine when they arrive in the workshop. Ensure that the human resources department understands the transaction. Just like everything else in life; you get what you need, and for precision sheet metal processing, the shop needs to pay for skilled craftsmen.
2. Avoid all-inclusive teams
Of course, good teamwork can have a huge positive impact on your profits, but it must be done correctly. If you create a team of everyone from the bending department, you may get moderate results. It will push your press brake settings to the lowest common denominator. This will also stifle the creativity of technicians, and at least not quickly raise the bar for novice or inexperienced personnel. The bending machine department needs experienced people to lead, but this is not an equal team.
Or, try to combine people with specific skills with people with other manufacturing backgrounds. A diverse team can introduce many new perspectives. You may be surprised at what the team can accomplish. The best results may come from a team that includes the best candidates for each department. They are operators, programmers, engineers, or other people with specific skills.
3. Don't rely solely on technology
The bending technique improves almost every day. You may need offline programming and simulation, maybe a bending machine with the latest CNC and specifications that can be repeated down to micrometers. It is a mistake to only use all these techniques to avoid the need for skilled personnel. Don’t let yourself fall into “I don’t need expensive, skilled craftsmen anymore; the computer will go all out. This will hurt your bottom line.
Although the bending machine may repeat to within a micrometer, the sheet metal does not. The gauge tolerance is between 0.002 and 0.020 inches, which is just the difference in the thickness of the sheet metal itself. The inconsistency of grain size and orientation and batch-to-batch changes in material composition all play a role. Dealing with these issues still requires extensive knowledge of the use of sheet metal and plates, at least if you want to produce high-quality parts.
Technicians can quickly detect these changes and actively adjust the machine. This alone makes skilled operators and technicians good value for money.
4. Before designing, please consult a bending expert
It seems strange that many engineers, designers, and even operators still do not understand the difference between air forming, bottom bending and precision press forming, and how each shape forms an internal bending radius (see Figures 1 and 2).
During bottoming and embossing, the mold will punch the internal bending radius into the part, so the calculation of the bending allowance and the bending deduction is based on the nose radius of the punch. In air forming, the internal bending radius fluctuates as a percentage of the die width-about 16% for cold rolled steel and about 20% for stainless steel (hence the term "20% rule"). If the bend calculation is based on the wrong process, the part will be incorrect.
Designers, engineers, and programmers need to go to the workshop without judgment and ask the operator what method they use to form which material. You can then ask them to provide a list of the tools they have. For punches, you need to know the radius, angle and tonnage. For the mold, you need the width and angle.
Armed with this information, you can now design parts around these parameters. Then, on or in the work jacket, you can show the molding method and tool kit for the job at hand. Because you asked the operators what they did with which materials and tools, there should be no problem with the operator’s acceptance.
5. Avoid tool ignorance
Choose the tool according to the type of work you have and the style of the machine you have. There are four common types of tools: planers, precision planers, precision grinders and precision grinders.
Planer tools have been around for a long time and will continue to be produced for many years to come. They are very suitable for single-pole settings, bottom bends and embossing. However, they are not suitable for staged tool settings. These tools are produced by positioning on the XY axis, the length is on the XY axis, the maximum length is 40 feet, and the error on 10 feet is about 0.010 inches. Over the entire 40-foot tool, the maximum deviation is 0.040 inches in length.
Although the precision planer tool is planned to have a consistent profile, it is still the core of the planer tool. They suffered all the errors of American planer molds. For jobs that only require a tool set, they can still be used, but they are not very good tools for a staged setup.
The real fine grinding tool is only 36 inches long. Precision planing tools usually start at 10 to 12 feet or more, and then cut to length. Again, these tools are not good staging tools.
There are two other problems with long planing and precision planing tools when you cut them to the required length. First, when you cut them, you release the residual stresses, which increase bowing and twisting into the tool, making alignment difficult.
Second, you need to mark each cut so that the tool can be reassembled the way it was originally cut. For example, if you cut a long tool into two pieces, you can mark "1" near the cutting line of each piece. When reassembling them to bend larger parts, simply match the "1" on one segment with the "1" on the other segment. This also ensures that your tools face the same direction in the bending machine and avoids mismatch and alignment issues between the punch and die.
The precision grinder is a tool in the contour of the planer, but the tolerances are very strict when grinding toward the center. Like real precision ground bending machine tools, they are reversible, very suitable for segmented installation, and suitable for modern and older bending machines. Due to manufacturing accuracy (typical tolerances are between 0.0004 and 0.0008 inches), they are easy to mix and match, and tool orientation is not a problem. They are manufactured in parts or approximately 3 feet in length.
Like a precision ground planer, the brake tool of a true precision ground bending machine is also ground towards the center and manufactured with very strict tolerances. The punch and die contours of precision grinding tools are different from the punch and die contours of a planer, and they are more versatile.
You need fine grinding tools to get the most versatility from modern bending machines. Again, this is because they are milled towards the center point rather than from the XY coordinates. This allows these tools to be mixed and matched and face opposite directions in a single fixture. Depending on the brand and style of the tool, some tools can even be perfectly matched with other tool brands.
However, always keep in mind that you can only use a real precision ground planer or precision ground planer tool that is about 3 feet long. length. If they are longer and you need to cut them, they are planer tools, and if you try to increase the setting of the press brake, it will cause problems.
Short-term pain, long-term gain
These are just some of the things that may hurt your profits. Of course, there is more. They may be hurting you now. Some remedies may not be smooth sailing, but in the long run, you can avoid greater pain and greatly improve the morale of the store and the quality of the final product.
Link to this article: Avoid the difference in the sheet metal bending process
Reprint Statement: If there are no special instructions, all articles on this site are original. Please indicate the source for reprinting:https://www.cncmachiningptj.com/,thanks!
Sheet metal, beryllium, carbon steel, magnesium, 3D printing, precision CNC machining services for heavy equipment, construction, agriculture and hydraulic industries. Suitable for plastics and rare alloys machining. It can turn parts up to 15.7 inches in diameter. Processes include swiss machining,broaching, turning, milling, boring and threading. It also provides metal polishing, painting, surface grinding and shaft straightening services. The production range is up to 50,000 pieces. Suitable for screw, coupling, bearing, pump, gearbox housing, drum dryer and rotary feed valve applications.PTJ will strategize with you to provide the most cost-effective services to help you reach your target,Welcome to Contact us ( sales@pintejin.com ) directly for your new project.
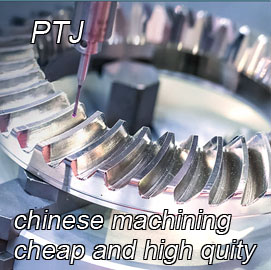
- 5 Axis Machining
- Cnc Milling
- Cnc Turning
- Machining Industries
- Machining Process
- Surface Treatment
- Metal Machining
- Plastic Machining
- Powder Metallurgy Mold
- Die Casting
- Parts Gallery
- Auto Metal Parts
- Machinery Parts
- LED Heatsink
- Building Parts
- Mobile Parts
- Medical Parts
- Electronic Parts
- Tailored Machining
- Bicycle Parts
- Aluminum Machining
- Titanium Machining
- Stainless Steel Machining
- Copper Machining
- Brass Machining
- Super Alloy Machining
- Peek Machining
- UHMW Machining
- Unilate Machining
- PA6 Machining
- PPS Machining
- Teflon Machining
- Inconel Machining
- Tool Steel Machining
- More Material