Magnesium Alloy Electronic Welding And Laser Welding
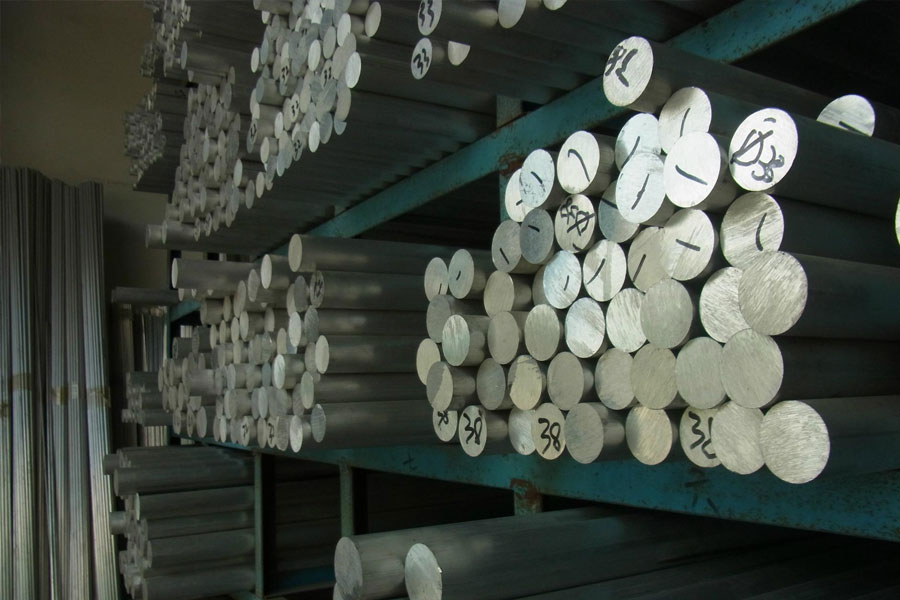
Electron beam welding
Magnesium alloys with Zn content ≤1% are rarely welded by electron beam. Generally, magnesium alloys that can be arc welded can also be electron beam welded, and their pre- and post-treatment processes are the same. During electron beam welding, magnesium vapor is immediately formed under the electron beam, and the molten magnesium flows into the small holes produced. Due to the high vapor pressure of magnesium alloys, the small holes produced are often larger than those of other metals, which are easy to be in the weld. Stomas are formed at the roots. Therefore, the process parameters should be carefully operated and controlled to prevent overheating from causing pores. In order to obtain a high-quality weld, the electron beam can swing slightly circularly and use a slightly defocused electron beam. It is best to add an appropriate amount of filler metal outside the joint, and the use of the same type of magnesium alloy integral or close-fitting gasket can reduce pores. AZ91C-T6 and AZ80A-T5 are suitable for electron beam welding.
laser welding
Laser welding is an advanced joining technology for magnesium alloy workpieces. Its advantages are: fast speed, low heat input, small deformation of the workpiece, and high joint strength. Compared with aluminum alloy, magnesium alloy has better laser absorption performance.
The laser beam can concentrate the density energy on a small spot, and input heat into the melting zone, which can minimize the heat-affected zone. Due to the large linear expansion coefficient of magnesium alloy, it is more suitable for laser welding. The laser beam is easy to control, very suitable for welding complex three-dimensional workpieces, and easy to automate. The strength of the wrought magnesium alloy laser welding seam is almost equal to that of the base metal. If the welding process parameters are well controlled, the pores and undercuts will be few.
When the 400W pulse YAG laser is used to weld AZ31B magnesium alloy, not only the weld deformation is small, the shape is round, there is no crack, and the back surface is evenly penetrated. The thermal effect of magnesium alloy laser welding is small and insignificant, the grain structure is fine and uniform, and the hardness of the joints does not change much, but the pulse width has a great influence on the performance of the welded joint. When the pulse width is 4.5ms, good welding results can be obtained , The tensile strength Rm of the joint can reach 95% of the base material.
Laser-argon arc hybrid welding
Laser-argon arc combined heat source welding was proposed by Eboo et al. in 1978 and has attracted the attention of the global welding community. The principle of low-power YAG laser-argon arc composite heat source welding magnesium alloy sheets (see picture). When using laser-TIG (tungsten inert gas) composite heat source to weld deformed magnesium alloys, good welds can be obtained without pores and cracks, etc. defect.
Under the same welding conditions, the penetration depth of composite heat source welding is 4 times that of laser welding and 2 times that of argon arc welding. The tensile strength Rm of the joint is 95% of the base metal, and the impact toughness is 113% of the base metal. The fatigue strength is equal to that of the base metal, and the welding speed is fast, up to 2000mm/min. Low-power laser-argon arc hybrid welding not only overcomes the respective shortcomings of laser welding and shield welding, but also significantly increases the penetration depth. It is an excellent joining technology for magnesium alloy workpieces.
At present, the power used in laser welding is generally 2kW-10kW, but there are also those with a power of 20kW. The high-power composite heat source usually uses a laser beam of about 2kW. However, because the magnesium alloy has a strong reflection effect on the laser, the energy is wasted during welding. . Studies have shown that the use of a 400W YAG laser and argon arc combined heat source not only achieves high-quality welding, but also saves energy and reduces equipment costs.
Link to this article: Magnesium Alloy Electronic Welding And Laser Welding
Reprint Statement: If there are no special instructions, all articles on this site are original. Please indicate the source for reprinting:https://www.cncmachiningptj.com/,thanks!
3, 4 and 5-axis precision CNC machining services for aluminum machining, beryllium, carbon steel, magnesium, titanium machining, Inconel, platinum, superalloy, acetal, polycarbonate, fiberglass, graphite and wood. Capable of machining parts up to 98 in. turning dia. and +/-0.001 in. straightness tolerance. Processes include milling, turning, drilling, boring, threading, tapping, forming, knurling, counterboring, countersinking, reaming and laser cutting. Secondary services such as assembly, centerless grinding, heat treating, plating and welding. Prototype and low to high volume production offered with maximum 50,000 units. Suitable for fluid power, pneumatics, hydraulics and valve applications. Serves the aerospace, aircraft, military, medical and defense industries.PTJ will strategize with you to provide the most cost-effective services to help you reach your target,Welcome to Contact us ( sales@pintejin.com ) directly for your new project.
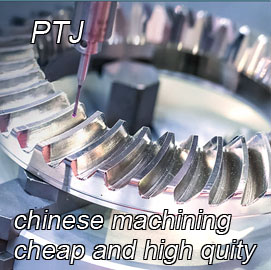
- 5 Axis Machining
- Cnc Milling
- Cnc Turning
- Machining Industries
- Machining Process
- Surface Treatment
- Metal Machining
- Plastic Machining
- Powder Metallurgy Mold
- Die Casting
- Parts Gallery
- Auto Metal Parts
- Machinery Parts
- LED Heatsink
- Building Parts
- Mobile Parts
- Medical Parts
- Electronic Parts
- Tailored Machining
- Bicycle Parts
- Aluminum Machining
- Titanium Machining
- Stainless Steel Machining
- Copper Machining
- Brass Machining
- Super Alloy Machining
- Peek Machining
- UHMW Machining
- Unilate Machining
- PA6 Machining
- PPS Machining
- Teflon Machining
- Inconel Machining
- Tool Steel Machining
- More Material