What is needed to automate the horizontal injection unit to handle tiny-sized inserts and molded parts?
Insert overmolding is a strict technology in injection molding, but in the initial stage, it is not often handled by robots. It usually requires manual assistance, especially for inserts with difficult geometric shapes. The robotics and proprietary technology at that time could not handle the blade well. The task of loading the blade into the tool is done manually (and sometimes still) by the operator of the work cell, especially for blades that are challenging for size, shape, or precise position and orientation requirements.
For many years, horizontal machine operators will wait for the mold to fully open, let the part fall, slide open the safety door, carefully position and manually load the insert into the mold, close the gate, and continue with the overmolding. This is an inefficient and labor-intensive method. The opening and closing of the gate lengthens the cycle time; and it is usually prone to wrong insertion direction. Vertical molding machines face similar challenges, but in this article, the editor of Xianji.com will focus on horizontal clamping mold machines, which are more common in molding workshops and are suitable for higher-volume inserts. Pieces formed. Moreover, because the design of top robots prefers horizontal machines, vertical presses have not experienced the benefits of such advancements in automation technology.
Time is a friend of technology, and robot technology has made great progress, especially for horizontal injection molding and top-entry linear robots. Today, most high-volume moldmakers for injection molding insert parts have used top-entry linear robots to automate the process, which simplifies the process, saves direct labor costs, and improves quality control.
However, for common overmolding applications that use "standard" size inserts and parts, and for miniature inserts and parts that are becoming more and more common in the miniaturization era of electronics, medical equipment, and micromechanical systems, and Not necessarily enough. Many of these inserts may only cost a penny. This scale poses greater challenges to both molders and robot suppliers.
Wittmann W822 robot with miniature plug-in EOAT. Most insert molding machines with high throughput use horizontal injection molding machines with top-entry robots.
Miniature size, huge challenge
On the microscopic scale (for example, less than 3 mm), due to the challenges of automatically handling such small inserts, it is still often necessary to manually (or not do it at all) manual overmolding. This means that part design usually defaults to a two-piece assembly, rather than an integrated one-piece overmolding. Why? Because molders and part designers do not always know the capabilities of the latest generation of injection molding robots, nor the ability of the supplier’s custom automation engineering team to manage and successfully implement such work cells.
Micro-applications may not be suitable for existing older-generation robots that are still "experiencing actions." However, today's most advanced linear robots have advanced technologies, such as higher precision (<1 mm) transmission systems, multi-axis precision servo motors and software control. Viewed from a distant workshop, today's high-tech top entry-level linear robots do not seem to be much different from earlier models 20 years ago. But in fact, they are more accurate, more programmable, more powerful, and easy to integrate with custom automation. Equally important, the custom automation engineering capabilities of some robot suppliers have been developed to match the more advanced robots they provide.
In addition, "workshop" equipment, sensors and quality control technology have also been improved and can be used for precise blade applications. An example is the use of more advanced but cost-effective modern vision sensors, proximity sensors and other technologies to ensure that the insert appears in the correct position and orientation with high accuracy. Combining it with advanced technology using insert feeder, escapement, end-of-arm tool (EOAT) technology, the work cell has become very efficient and cost-effective, even for the most challenging miniature inserts, It can also be overmolded.
It is essential that, in terms of project management, the molder can have confidence in the qualified main robot supplier to be responsible for the entire robot and automation work cell, so the molder does not have to go to a separate third-party integrator for special insertion. Forming applications. Managing a project with one supplier must be better than two managers, right?
Practical examples
Today, high-precision micro-insert molding has been successfully achieved on precision horizontal injection molding machines ranging from 15 tons to 165 tons. The mold has a "smart" design that aims to promote this type of tool before cutting the mold steel from the beginning. Application automation. Here are two illustrative examples of micro-insertion applications and the accompanying challenges:
Example project A is a polyetherimide (Ultem) electrical component less than 1 inch in length, with a cylindrical ceramic polymer insert that has a diameter of 1.25 mm (0.0492 inches). The mold has eight cavities, and the position tolerance of the insert in each cavity is 0.01 mm (0.0005 inches). The inserts must be aligned front to back.
The unit includes a 110-ton press, a top-entry linear robot and visual inspection to confirm the presence of the insert and the orientation of the substrate in the overmolded part. The robot places the parts on the exit conveyor, and the exit conveyor performs indexing step by step.
The challenges faced by the project include:
•Ensure the quality of the insert-that is, the insert is always within tolerance and is completely free from dust, dirt, specifications, static electricity or moisture.
• Make sure that the insert remains in the correct orientation when removed from the automatic batch feeding station before overmolding and before the mold is inserted, and is correctly placed in the cavity before closing the mold. The robot's integrated camera and vision sensor meet this requirement.
• Carefully calculate the thermal expansion of the mold steel, which may affect the tolerances of the cavity and micro inserts, thereby affecting the quality of the overmolded part. This is especially important when processing at such a small scale and high tolerances.
• Common insert application problems, such as the mold position on the platen must be completely horizontal, square and vertical. Even if the companion robot EOAT has a die-engagement alignment pin, this is required.
• Use high-quality stainless steel (instead of standard acetal, mild steel or rubber) to machine EOAT to very high tolerances (±0.0005 inches) so that "fingers" can grasp the overmolded part. It is also necessary to use a precision vacuum chamber in the EOAT to hold the blade. The EOAT and other parts of the feed table are special anodized or hardened materials for wear surfaces.
Example project:
B is another electrical component, the PBT has a cylindrical metal insert. The size of the insert is less than 2 mm, and it must be inserted in the front and back directions and the position tolerance is 0.03 mm (0.0012 in.) in 4 cavities. The vision sensor checks the orientation of the insert and its presence in the mold. In a 110-ton press, the cycle time is 15 seconds.
The challenges faced by this metal micro-insert overmolding project are very similar to those of Project A. One difference is that metal rather than ceramic inserts must be free of oxidation and coating to avoid the introduction of contaminants. On the other hand, ceramic inserts can be more abrasive, so special care must be taken when using hardened contact surfaces. Similarly, metal inserts are less fragile and heavier than ceramic inserts, so it may be easier to grasp and handle metal inserts, although it is not easy to handle rice-sized objects.
Many factors to control
Other common technical considerations for automatic handling of micro blades and parts include:
Static charge:
Even the smallest static charge can affect the plug-in and the parts, so testing must be done to determine whether the parts or plug-ins must be de-staticized or immersed in clean deionized air.
Environmental control:
If you manage in an environment where temperature, humidity, and air flow are controlled, you can handle such small-scale parts and plug-ins more consistently. Changes in ambient temperature may change the size of the blade, which is essential for precise tolerances. Humidity may have a negative effect on any hygroscopic polymer; airflow (such as from a nearby vent or doorway) may push small inserts or components into place. Well-designed housings and HEPA filters are often used to mitigate these risks and control particulate contamination.
Consistency and quality control of micro-inserts: The inserts must be very consistent, and the supplier has a high degree of quality control on the size, burrs, chips and other specifications to ensure the consistency of the insertion and processing.
Micro-part inspection:
Through testing, the requirements for vision cameras and simple vision sensors for the work unit can be determined. It is likely that more advanced vision technology is needed to complete tasks such as positioning, inspection, mold base confirmation and quality control after molding. The naked eye is usually not suitable for such small-scale inspections.
Micro EOAT gripper accuracy: Robotic and automated grippers and fingers have very high machining tolerances, and are usually made of special materials according to application needs.
Plug-in feeder:
This will not be your ordinary herb, various garden feeders; the design and construction materials of the feeder, strict tolerances and creative direction management with precise sensors will be carefully considered to confirm each step of the process .
Mold fixing and joining:
In order to help simplify the initial setup, the robot EOAT usually has a docking function to dock with the mold when positioning the micro plug-in. This also ensures consistent insertion and ejection. EOAT may not include ordinary mechanical grippers because the blade is small. Instead, a pneumatic tube on the EOAT can be used to place the microinsert in the cavity.
During the specification and design review phase of the project, experienced robot suppliers will be familiar with a large number of other details to optimize the insertion, demolding and handling of micro inserts and micro parts.
Automation supplier
Now, new robotics and automation technologies for micro-insert molding provide the possibility of plastic product design. This design was unheard of a few years ago, and even the 20-20 best vision, its size is difficult to achieve. Now, through insert molding/overmolding, the assembly of tiny parts can become more robust and durable, thereby reducing the need for assembly after molding and reducing the total number of parts in the finished product.
Therefore, encourage molders to contact your robot supplier, conduct interviews, and ask about possibilities. If possible, please let the customer’s product design/development expert sit in the same room with the qualified robot supplier and mold design manager; then discuss the feasible and infeasible methods in the injection molding machine, perform economic mathematical calculations and move forward. This is likely to be your competitive "advantage" in the market segment.
How do you choose such an advanced robot supplier for high-precision small or micro insert molding? Consider the following factors:
Customize the size and expertise of the automation engineering team: It is best to avoid using overseas resources, because you want to work with complex projects at home. Visit the robot supplier’s facility to prove its capabilities, size, scale, and scope.
Location and experience of on-site service support: Like the advantages of domestic custom automation projects, obtaining local/regional on-site “direct” service technical support is equally important for low-cost start-up, work unit commissioning and rapid response to future technologies. Support requirements are part of the "uptime" guarantee.
Successful implementation of American and local project management: The third layer of a successful high-tech automation project is a crucial project management factor. In fact, all key project elements should be carried out domestically and regionally, while avoiding the time lag of such complex, highly communication projects, communication problems and time zone challenges of foreign contacts.
Robot user programmability, functionality and circuit limitations: These micro-applications involve more than basic pick and place or ready-made automation. Therefore, entry-level linear robots must have all the latest technologies to be easily integrated with high-precision custom automation. The robot should be fully programmable by the end user and be able to achieve a position accuracy of 0.1 mm or higher. It should not require molders to purchase custom programs, nor should it be limited to limited preset subroutines, circuits, and I/O options. Robots with a modular mechanical design provide the flexibility required for special custom applications.
Link to this article: What is needed to automate the horizontal injection unit to handle tiny-sized inserts and molded parts?
Reprint Statement: If there are no special instructions, all articles on this site are original. Please indicate the source for reprinting:https://www.cncmachiningptj.com/,thanks!
3, 4 and 5-axis precision CNC machining services for aluminum machining, beryllium, carbon steel, magnesium, titanium machining, Inconel, platinum, superalloy, acetal, polycarbonate, fiberglass, graphite and wood. Capable of machining parts up to 98 in. turning dia. and +/-0.001 in. straightness tolerance. Processes include milling, turning, drilling, boring, threading, tapping, forming, knurling, counterboring, countersinking, reaming and laser cutting. Secondary services such as assembly, centerless grinding, heat treating, plating and welding. Prototype and low to high volume production offered with maximum 50,000 units. Suitable for fluid power, pneumatics, hydraulics and valve applications. Serves the aerospace, aircraft, military, medical and defense industries.PTJ will strategize with you to provide the most cost-effective services to help you reach your target,Welcome to Contact us ( sales@pintejin.com ) directly for your new project.
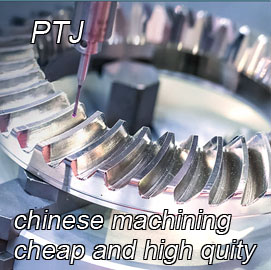
- 5 Axis Machining
- Cnc Milling
- Cnc Turning
- Machining Industries
- Machining Process
- Surface Treatment
- Metal Machining
- Plastic Machining
- Powder Metallurgy Mold
- Die Casting
- Parts Gallery
- Auto Metal Parts
- Machinery Parts
- LED Heatsink
- Building Parts
- Mobile Parts
- Medical Parts
- Electronic Parts
- Tailored Machining
- Bicycle Parts
- Aluminum Machining
- Titanium Machining
- Stainless Steel Machining
- Copper Machining
- Brass Machining
- Super Alloy Machining
- Peek Machining
- UHMW Machining
- Unilate Machining
- PA6 Machining
- PPS Machining
- Teflon Machining
- Inconel Machining
- Tool Steel Machining
- More Material