What are the tips for cleaning the twin screw extruder?
Twin-screw extruders (TSEs) have long been the machine of choice for compounding machines due to their superior performance and customizability. They can handle almost all resins and combine different additives and fillers to achieve different particle sizes and shapes with different properties.
Although there are countless combinations of possible end products, certain methods of obtaining these products can also cause pollution problems and low flow or low pressure in many areas throughout the barrel. In a continuous process like extrusion, contamination can have an adverse effect. Compared with other processes, purging in extrusion is often more challenging, and TSE faces greater challenges because the system is more complex than a single screw extruder.
This article will study some specific challenges of purging in twin-screw extrusion. Conversion, pollution, screw pushing and extended downtime are the four biggest processing problems that engineers face in compound plants.
Tip 1: Do not use production resins, recycled materials or additives to purge the extruder:
Production resins are not designed to clean machines, nor are they a substitute for commercial cleaning compounds. Cleaning the extruder with the next resin or recycled material is very time-consuming, wasteful and does not help at all in removing color and carbon pollution. David Krueger, a process engineer at Asahi Kasei Plastics North America (APNA), is committed to the development of composite materials. He knows that this seemingly cost-saving decision will actually backfire. In the past work, I have seen many processors try to use low melting point polyethylene to replace engineering resins, including nylon, styrene and ABS. These resins inevitably decompose and form large amounts of carbon deposits. You can try using fillers to help clean the barrel, but if the base resin tends to form carbon, this will happen no matter what filler carbon you use.
Lenny Gutierrez, Asaclean's cleaning expert and sales representative, has been committed to solving the problem of compound contamination for many years. He added that twin screw end users are very concerned about customers' product specifications. Any possible process changes, especially contamination from previously run or accidentally degraded materials, may disrupt the process and cause production delays due to non-standard products. Kruger pointed out that another headache is trying to eliminate unpredictable downtime with production resin. Even if you exclude the contamination issue from the discussion, if you are using resin or regrind, the replacement time will be very different. If olefins are synthesized, it may take 20 minutes to clean the drum. If other resins are used, such as styrene and nylon, increased carbon deposits may lead to longer cleaning times. It may take 3-4 hours to clean the barrel. Clearing the compound allows you to have continuous conversion time, no matter what you are synthesizing.
When you use reground or original resin for cleaning, these materials will form another layer on the existing resin, color deposits, or carbonized materials in the barrel and on the screw. Over time, these layers can become additional sources of pollution, making purification more difficult. Once your machine resumes production, the carbonized material will eventually break and contaminate your product. Twin screw extruders cannot withstand material or carbon contamination. Fortunately, these problems can be easily avoided by choosing a cleaning compound that suits your specific needs.
Tip 2: Ask yourself the following questions to choose the best cleaning compound for you:
The introduction of a cleaning program can easily help the mixing plant reduce downtime by 50% to 75%. However, when cleaning twin-screw extrusion equipment, there is no “one size fits all” process or solution for purging compounds. Carbon can accumulate in the dead corners of the machine: mixing zones, molds, downstream equipment, etc. These are low flow areas and will need to be treated with chemical purification compounds. However, if you need frequent maintenance, you may also need a powerful cleaner.
Without the correct cleaning agents and procedures, you run the risk of increasing the scrap rate. However, determining the appropriate level of purge compound is not only to eliminate color and carbon pollution, but also involves the impact on your profits. Taking a holistic approach will help you increase efficiency and profitability. When you contact a purification expert for a free consultation, there are a few key things they need to consider in order to select the correct grade and quantity to select the best purification compound for your system. Some of these issues include:
• What is the size of the extruder?
• What kind of resin are you using?
• What is your processing temperature?
• What is the intended use of the purification compound?
• What problems are you currently experiencing?
The answers to these questions are crucial in order to make an informed decision and the best course of action. Using the correct cleaning compound can effectively eliminate all contamination, increase uptime and productivity, and help you maximize operating efficiency. If you understand the impact of these problems, you have the ability to choose the right solution to effectively clean your extruder.
Mechanical and chemical cleaning types can help twin screw processors maintain their machine contamination. The mechanical cleaning compound does an excellent job of safely scrubbing the surface of the screw and barrel. However, the cleaning performance is mainly limited to the surface through which the substance flows under considerable pressure. For twin-screw machines that use simple screw types and mixing elements, mechanical purge can work perfectly.
However, for proper cleaning in low-pressure areas (such as near vents) or hard-to-reach areas (found on more complex spiral mixing elements), chemical cleaning will bring better results. Chemical cleaning compounds achieve cleaning by measuring the chemical reactions involved in the machine during immersion. The gas produced by the chemical reaction quickly enters the hard-to-reach areas. These areas can be considered low pressure or low flow (usually called dead zone or dead spot), otherwise it may not be directly physically scrubbed through the mechanical stage. Gutierrez explained that understanding how the material flows in a specific screw type and identifying the high and low pressure flow paths can help the processor decide which type of purge is best for a specific twin screw setting.
President and General Manager Charlie Martin noted that Leistritz Extrusion has conducted extensive testing to determine the removal method that is best for its customers. In order to determine the most ideal purification technology, various TSEs have been studied, with the goal of determining the minimum amount of purification material and the minimum purification time required. The analysis methods are: flood feeding (feeding hopper, TSE screw determines the feeding speed); metering feeding (separate feeder and TSE screw with independent rpm); and plug feeding (introducing the purge charge intermittently) TSE). When cleaning the system, it is usually the fastest and most efficient to feed the plugs, requiring significantly less material and thus becoming significantly cleaner.
With these suggestions in mind, the purge procedure of the extrusion process will vary according to the grade you use. If you are not sure how to clean the extruder most effectively, it is best to contact your purge compound supplier directly.
Tip 3: Implement preventive cleaning:
Many processors only use cleaning agents when absolutely necessary. However, the use of this removal strategy will result in reduced profits and efficiency. This usually happens when processors are running within tight deadlines or when their purging budgets are limited. APNA's Krueger also pointed out that sometimes processors will push their limits because they think their screws are "self-cleaning." Self-cleaning screws will not significantly remove contaminants.
Krueger explained that even if the twin screw is designed to "self-wipe", the screw design will not have any significant impact on the removal of contaminants. Due to shearing, a lot of heat is generated, and contamination occurs anyway. If your factory is dealing with any of the above two situations, please consider working with a cleaning expert to conduct a cost savings analysis to show management the cost of this decision.
Adopting preventive purge practices can not only save your equipment from downtime, but also reduce scrap rates, customer rejection rates and production line downtime. You can't wait until the last minute to start cleaning the compound, because by then you are already plagued by contamination problems or color streaks. Experts agree that conversion is the biggest problem facing composite manufacturers. If you need faster conversion, clearing the compound is easy. Regular use of cleaning agents can prevent contamination.
Usually, only one to two buckets of compound with cleaning ability are needed to prevent contamination. Preventive cleaning saves time and money by effectively using capacity and prevents unplanned downtime. There are three main benefits of implementing a preventive maintenance plan and cleaning process in your factory:
• Prevent color accumulation and carbon pollution;
•Reduce excessive cleaning time and material waste at the end of production operation;
• Limit the frequency of screw pushing in, and minimize the time and effort required to pull out and manually clean the screw.
Tip 4: Make sure you are optimizing the screw thrust to facilitate disassembly:
If conversion is the biggest challenge for the mixer, then the screw thrust is close behind. Sometimes, product changes require you to replace a screw component. If the screw is not in the ideal disassembly condition, this may be time-consuming. Asaclean has several large composite customers who use several resins or the same resin with different additives. Usually, mixing different resins requires different screw designs, or the mixer needs to pull the screw to ensure that the processed resin will not be mixed. In essence, most polymers tend to adhere to the surface of the screw, and these layers not only pose challenges for screw cleaning, but also for screw removal.
A typical mixer might have to tighten the screws four to five times a week. Those who produce color masterbatch may pull screws every day. Some factories may have duplicate screws, but these screws may cost tens of thousands of dollars in additional capital expenditures. For most mixers, pulling the screws and cleaning them may be the only option to go back to production. This process can be labor intensive, and the cost is unbelievably high, because downtime can cost 1,000 to 1,200 dollars per hour.
Weddell added that the material accumulated on the screw machine is difficult to remove. You can choose the grade that does not require the use of an oven, a wire brush, or a fire to clean the screws. These secondary processes also increase the possibility of damage or accidental destruction of expensive screw assemblies.
There are three main reasons for pressing screws to press:
• They may need compounds to ensure 100% no cross-blending of polymers;
• Replacement requires a different screw design;
•Serious pollution cannot be removed by normal cleaning.
Tip 5: Know your screw design and mixing area and pay close attention to the machine settings:
TSE is modular and offers unlimited combinations of screw sections and different mixing areas, which also exacerbates some of the cleaning challenges. In order to maintain a consistent melt temperature, melt flow, mixing and shearing, many machine settings and mixing factors need to be paid close attention to. This leaves a lot of room for pollution. In rows with additional feed streams, the margin of error will increase exponentially. Once the contamination begins, it is almost impossible to stop it without active intervention (usually by pushing a screw or using a cleaning agent).
Both twin-screw and single-screw extrusion are faced with the common challenges of low-pressure extrusion processes. These processes do not have the same pressure and turbulence control options as the injection molding process. Many twin-screw machines also rely on proper ventilation to help achieve proper mixing, fusion, or chemical reactions required for the final product. Gutierrez pointed out that in these specific mixing areas, these vents can provide lower pressures and may lead to more difficult product proper removal.
In order to maximize cleaning performance, please follow the machine settings recommended by the supplier. Settings are very important. Without the correct settings, your clearing compound will not activate properly and will reduce your benefits. Using the correct settings will activate the best cleaning power for your chemical cleaning.
Tip 6: Super engineering resins and heat-sensitive resins need special attention :
When compounding agents create new resins that can withstand more extreme conditions, they need to be careful to avoid contamination. For "super engineering" resins, such as PEEK, polyetherimide, polysulfone, etc., scrapping and downtime have a destructive effect on profitability. Jerry Weddell, a cleaning business manager, said that a common challenge he faces when using compounds is temperature changes. For super engineering resins, you need to use grades designed for the challenge. Some scores are as high as 790f, but this is not all. We always recommend that you convert to resin in a lower processing temperature range.
Gutierrez added that low-temperature resins have similar concerns about carbon. He said that when dealing with heat-sensitive resins such as PVC or EVOH, attention should be paid to degradation and pollution. These resins are easily degraded. It is important to control the process temperature, because high temperatures can cause degradation, and low temperatures can cause excessive shear. Since there are fewer heat-sensitive materials, the polymer remaining in the machine will degrade for a long time, but in the case of PVC, the degradation will happen immediately. This is a very serious processing problem.
In order to work effectively, the cleaning compound does require heat and sealing, so it is important to get enough heat for good cleaning, but not to burn any resin remaining in the barrel. It is important to perform the initial purge at the processing temperature of the resin. Do not increase the temperature inside the barrel until you are sure that all the PVC has been removed. When it comes to heat-sensitive materials, you do need to take additional steps, but using this method can be very effective in cleaning them.
Tip 7: Seal the machine with a heat-stable compound every time it shuts down :
In addition to regular preventive maintenance cleaning, you should also use a heat-stable cleaning compound to shut down and seal it temporarily or for a long time, especially on weekends or holidays. During shutdowns without purging, oxidation can occur, which can cause pollution, delay start-up and extend machine downtime. These purification levels create an "air-tight" environment in the barrel and promote further cleaning during shutdowns.
Kruger explained that idle production lines usually require a warehouse temperature of around 200 degrees Celsius (392 degrees Fahrenheit). When using conventionally processed resin seals, oxidation problems usually occur during start-up. This is one of the most avoidable processing problems in your extrusion plant. If you are not running around the clock, then a good shutdown cleanup will be a good solution.
Link to this article: What are the tips for cleaning the twin screw extruder?
Reprint Statement: If there are no special instructions, all articles on this site are original. Please indicate the source for reprinting:https://www.cncmachiningptj.com/,thanks!
3, 4 and 5-axis precision CNC machining services for aluminum machining, beryllium, carbon steel, magnesium, titanium machining, Inconel, platinum, superalloy, acetal, polycarbonate, fiberglass, graphite and wood. Capable of machining parts up to 98 in. turning dia. and +/-0.001 in. straightness tolerance. Processes include milling, turning, drilling, boring, threading, tapping, forming, knurling, counterboring, countersinking, reaming and laser cutting. Secondary services such as assembly, centerless grinding, heat treating, plating and welding. Prototype and low to high volume production offered with maximum 50,000 units. Suitable for fluid power, pneumatics, hydraulics and valve applications. Serves the aerospace, aircraft, military, medical and defense industries.PTJ will strategize with you to provide the most cost-effective services to help you reach your target,Welcome to Contact us ( sales@pintejin.com ) directly for your new project.
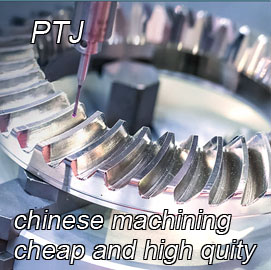
- 5 Axis Machining
- Cnc Milling
- Cnc Turning
- Machining Industries
- Machining Process
- Surface Treatment
- Metal Machining
- Plastic Machining
- Powder Metallurgy Mold
- Die Casting
- Parts Gallery
- Auto Metal Parts
- Machinery Parts
- LED Heatsink
- Building Parts
- Mobile Parts
- Medical Parts
- Electronic Parts
- Tailored Machining
- Bicycle Parts
- Aluminum Machining
- Titanium Machining
- Stainless Steel Machining
- Copper Machining
- Brass Machining
- Super Alloy Machining
- Peek Machining
- UHMW Machining
- Unilate Machining
- PA6 Machining
- PPS Machining
- Teflon Machining
- Inconel Machining
- Tool Steel Machining
- More Material