Process and technical points of passivation of stainless steel parts
Passivation is affected by the cleanliness of the parts and also by the choice of acid. Is the effect of nitric acid or citric acid the most? Xianji.com has translated and compiled some foreign materials.
The passivation process is tailored to the requirements of the application. The rendering shows a particularly large passivation line.
In fact, the process called "passivation" is just an improvement and enhancement of the naturally occurring process on most stainless steels. This process involves passivation, a chemically inert surface layer or film that is formed when stainless steel is exposed to an oxygen environment. The formation of this natural passive film can be affected or damaged by contaminants (dirt, oil, grease, compounds, scale) and the presence of free iron on the surface of the part. Therefore, a special workshop passivation process is designed to remove these contaminants to produce clean and corrosion-resistant stainless steel parts. This step is critical to the safety and performance of stainless steel parts and equipment, which is often necessary in the aerospace and medical industries and other industries.
Passivation standard
For many types of parts and industries, including many military specifications, ASTM standards A380 and A967 provide guidelines for good passivation practices. These standards detail acceptable methods and/or formulations for passivation of stainless steel and provide tests to measure the success rate of passivation. AMS2700C established acceptable aerospace passivation methods and/or formulations, practices and test protocols, and replaced AMS-QQ-P-35.
Passivation process
In all cases, cleaning is the first step in the passivation process, and it is believed that this cleaning may be performed in a separate production line or unit. The type of cleaning required depends on the contaminants, soil load, the degree of cleaning required, and the geometry of the part. Cleaning to remove deposited contaminants (such as dirt and grease) may involve wiping, vapor degreasing or spraying, or may involve immersion or non-immersion in ultrasound and/or agitation. The cleaner or cleaner should be suitable for the type of soil to be removed and should be handled in accordance with safety and environmental regulations. If descaling is required (to remove thick oxide film from heat treatment or welding, or to remove hot colorant), it may need pickling or electrolytic polishing, followed by thorough rinsing.
In a multi-station immersion passivation production line, the process usually starts with one or more cleaning tanks equipped with ultrasound and filtration, and possibly agitating or indexing rotation (if the geometry of the part or the soil load indicates this is advantageous). And water-based cleaners or cleaners. Parts should be placed in the form of baskets, fixtures, shelves or indexing equipment to ensure that in each process step, even in complex part geometries, the contact between the solution and all critical surfaces can be optimized.
The cleaning station is followed by one or more rinsing stations, which in turn can be equipped with mechanical actions, such as ultrasound, agitation, indexing and/or spraying, to promote good rinsing. Countercurrent flushing technology and automatic replenishment device can maximize water efficiency, save water and maintain consistency.
Nitric acid or citric acid?
Next is the acid phase of the passivation process. This step involves controlling the contact between cleaned stainless steel parts and dilute nitric acid or citric acid according to one of several possible formulations defined in specifications (such as ASTM A967 and AMS2700C). The purpose of this step is to remove free iron and impurities that may remain after the previous cleaning and rinsing steps have been successfully completed. The successful removal of free iron and exogenous materials helps to form a natural passivation film or layer on stainless steel, thereby enhancing its corrosion resistance.
If possible, the passivation step involves completely immersing the part in the passivation bath. The size of the bath should be able to move the solution around the entire load or within the entire load range, and the mobility of the solution can be further enhanced by recirculation and/or ultrasound. All equipment related to the passivation step should be compatible with the selected acid.
The concentration of acid, bath temperature and contact time are all proportional to the passivation formula and are critical to successful implementation of the specification. These process parameters can be manually or automatically monitored in such a system, and the data can be stored for a long time.
Nitric acid has always been the traditional acid of choice for this passivation step, although both ASTM A967 and AMS2700C allow the use of citric acid. In recent years, because citric acid is more friendly to nitric acid than nitric acid in terms of safety and environment, citric acid has been developed. Another exciting aspect of citric acid is that its cycle time can be shortened. As long as the citric acid passivation meets the specified specifications and buyer's requirements, including successful passivation test results, it can be considered acceptable. Now, some stores are expanding their capacity by setting up a passivation production line, which has both nitric acid and citric acid passivation tanks, and then special rinsing.
Regardless of the specified acid, equipment suitable for chemical substances (for personal protection and process protection) should be used in the passivation process, and the handling, storage and disposal of the selected acid must comply with federal, state and local regulations.
Rinse thoroughly
Immediately after the passivation bath, perform one or more rinsing. The rinsing can be sprayed or immersed, or can be used in combination, depending on the specifications, the geometry of the parts and the principle of water saving. Similarly, more rinsing fluid can provide excellent rinsing results in counterflow, while also saving water. Sometimes it may be necessary to perform a neutralization step (such as 5% sodium hydroxide) or a post-treatment step (usually sodium dichromate), and then rinse again. The final rinse solution should be added with "purified water", deionized water (DI) or reverse osmosis (RO) water is a good choice to prevent stains. The rinsed part should be dried immediately. In cases where particle counting is critical, the dryer can be equipped with a high-efficiency particulate air filter (HEPA),
Passivation equipment
The best equipment for batch immersion passivation is a manual or automatic production line consisting of a series of continuous tanks. Batch and production requirements will affect the size of the storage tank and the number of processing stations recommended to achieve production goals. The number of processes required also affects the number of process stations. For example, a continuous automated production line can be cleaned, pickled and passivated in one production line. Each production line is equipped with a dedicated rinsing solution, and each process is controlled by PLC in parallel or random operation as needed. . Many safety measures are also provided, including push-pull exhaust devices, housings, light curtains and/or auxiliary containment devices, as well as statistical process control, bar code and/or data management.
Passivation succeeded
The success of the passivation process is usually determined by inspection and/or testing. After passivation, rinsing, and drying are completed, the parts should be free of any surface defects (such as pitting, etching or frosting), nor should there be any stains that indicate the possibility of free iron. Parts can be subjected to free iron test after passivation as required according to the specified specifications or by the purchaser. These tests include water immersion, high humidity, salt spray or copper sulfate tests according to ASTM A967 and/or AMS2700C.
Link to this article:Process and technical points of passivation of stainless steel parts
Reprint Statement: If there are no special instructions, all articles on this site are original. Please indicate the source for reprinting:https://www.cncmachiningptj.com/,thanks!
3, 4 and 5-axis precision CNC machining services for aluminum machining, beryllium, carbon steel, magnesium, titanium machining, Inconel, platinum, superalloy, acetal, polycarbonate, fiberglass, graphite and wood. Capable of machining parts up to 98 in. turning dia. and +/-0.001 in. straightness tolerance. Processes include milling, turning, drilling, boring, threading, tapping, forming, knurling, counterboring, countersinking, reaming and laser cutting. Secondary services such as assembly, centerless grinding, heat treating, plating and welding. Prototype and low to high volume production offered with maximum 50,000 units. Suitable for fluid power, pneumatics, hydraulics and valve applications. Serves the aerospace, aircraft, military, medical and defense industries.PTJ will strategize with you to provide the most cost-effective services to help you reach your target,Welcome to Contact us ( sales@pintejin.com ) directly for your new project.
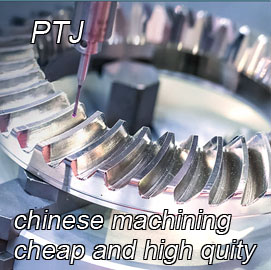
- 5 Axis Machining
- Cnc Milling
- Cnc Turning
- Machining Industries
- Machining Process
- Surface Treatment
- Metal Machining
- Plastic Machining
- Powder Metallurgy Mold
- Die Casting
- Parts Gallery
- Auto Metal Parts
- Machinery Parts
- LED Heatsink
- Building Parts
- Mobile Parts
- Medical Parts
- Electronic Parts
- Tailored Machining
- Bicycle Parts
- Aluminum Machining
- Titanium Machining
- Stainless Steel Machining
- Copper Machining
- Brass Machining
- Super Alloy Machining
- Peek Machining
- UHMW Machining
- Unilate Machining
- PA6 Machining
- PPS Machining
- Teflon Machining
- Inconel Machining
- Tool Steel Machining
- More Material