The Repair Technology Of Machining Center Electric Spindle
Electric spindle is a new technology that integrates machine tool spindle and spindle motor in the field of CNC machine tools in the past ten years. It is the "core" component of high-speed CNC machine tools, and its performance directly determines the high-speed processing performance of the machine tool.
Since the electric spindle is a high-speed precision component, regular maintenance is very necessary.
The motorized spindle is regularly maintained as follows:
- 1. The axial runout of the electric spindle is generally required to be 0.002mm (2μm), and it shall be checked regularly twice.
- 2. The radial runout of the cone hole in the electric spindle is generally required to be 0.002mm (2μm), and it shall be checked regularly twice.
- 3. The radial runout of the distal end (250mm) of the electric spindle core rod is generally required to be 0.012mm (12μm), and it shall be checked regularly twice.
- 4. The tightening force of the butterfly spring is required to be: 16-27KN (take HSK63 as an example) 2 regular inspections.
- 5. The extended distance is: 10.5±0.1mm (take HSK63 as an example to check 4 times regularly.
Analysis and treatment process of severe heat generation when the spindle rotates at high speed
The problem of heat and temperature rise during the operation of the electric spindle is always the focus of research. There are two main heat sources inside the electric spindle unit: one is the spindle bearing, and the other is the built-in main motor.
The problem that the electric spindle unit protrudes is the heat generated by the built-in main motor. Since the main motor is next to the main shaft bearing, if the heat dissipation problem of the main motor is not solved well, it will also affect the reliability of the machine tool. The main solution is to adopt a circulating cooling structure, which is divided into two types: outer circulation and inner circulation. The cooling medium can be water or oil, so that the motor and the front and rear bearings can be fully cooled.
The spindle bearing is the core support of the electric spindle and one of the main heat sources of the electric spindle. Current high-speed electric spindles mostly use angular contact ceramic ball bearings. Because ceramic ball bearings have the following characteristics:
- ①Because the ball is light in weight, the centrifugal force is small, and the dynamic friction torque is small.
- ②The thermal expansion caused by the temperature rise is small, so that the preload of the bearing is stable.
- ③Small elastic deformation, high rigidity and long life. Due to the high operating speed of the electric spindle, there are strict requirements on the dynamic and thermal performance of the spindle bearing. Reasonable pre-tightening force and good and sufficient lubrication are necessary conditions to ensure the normal operation of the spindle.
Using oil mist lubrication, the inlet pressure of the atomization generator is 0.25—0.3MPa, 20# turbine oil is selected, and the oil drop speed is controlled at 80—100 drops/min. While the lubricating oil mist fully lubricates the bearing, it also takes away a lot of heat. The lubricating oil distribution of the front and rear bearings is a very important issue and must be strictly controlled. The section of the air inlet is larger than the sum of the sections of the front and rear injection ports, and the exhaust should be smooth. The injection angle of each injection hole and the axis are at an angle of 15o, so that the oil mist can be sprayed directly into the bearing working area.
The main points of the maintenance process of the electric spindle
- 1. Measure static and dynamic radial runout and lift clearance and axial movement according to the damage of the electric spindle.
- 2. Use a self-made special tool to disassemble the electric spindle. Clean and measure the rotor swing and wear.
- 3. Optional bearings. The consistency error of the inner hole and outer diameter of each group of bearings must be ≤0.002——0.003mm, and the gap between the inner hole of the sleeve and the sleeve shall be 0.004—0.008mm; and the gap between the main shaft and the main shaft shall be 0.0025—0.005mm. In actual operation, it is better to use the thumbs of both hands to push the bearing into the sleeve. Too tight will cause the outer ring of the bearing to deform, and the bearing temperature will rise too high, and too loose will reduce the rigidity of the grinding head.
- 4. The cleaning of the bearing is an important part of ensuring the normal operation and service life of the bearing. Do not use compressed air to blow the bearing, because the hard particles in the compressed air will make the raceway rough.
- 5, tapered bearings or angular contact ball bearings must pay attention to the bearing installation direction, otherwise the rotation accuracy requirements will not be met. Special tools are used throughout the assembly process to eliminate assembly errors and ensure assembly quality.
- 6. When the inner hole of the sleeve is deformed, the roundness is out of tolerance, or the matching with the bearing is too loose, the local plating method can be used to compensate and then grind to the requirements, and this method can also be used at the journal.
- 7. The end faces of the round nuts, oil seal caps and other parts on the electric spindle are in close contact with the end faces of the inner and outer rings of the bearing. Therefore, the verticality of the threaded part and the end face is required to be very high. The coloring method can be used to check the contact. If the contact rate is less than 80%, the end face can be ground to make it meet the requirements of verticality. This work is very important. Its accuracy will affect the radial runout of the extension rod of the grinding machine spindle, thereby affecting the surface roughness of the ground workpiece.
- 8. After assembly, the electric spindle is adjusted axially (measured with a tension spring scale during adjustment), and static and dynamic radial runout and lifting clearance should be measured at the same time, until the assembly process requirements are met.
- 9. Under the actual operating conditions of the machine, eliminating the influence of factors such as assembly and thermal deformation during machine operation, at a certain speed, a dynamic balancer is used to dynamically balance the rotor.
Link to this article:The Repair Technology Of Machining Center Electric Spindle
Reprint Statement: If there are no special instructions, all articles on this site are original. Please indicate the source for reprinting:https://www.cncmachiningptj.com/,thanks!
3, 4 and 5-axis precision CNC machining services for aluminum machining, beryllium, carbon steel, magnesium, titanium machining, Inconel, platinum, superalloy, acetal, polycarbonate, fiberglass, graphite and wood. Capable of machining parts up to 98 in. turning dia. and +/-0.001 in. straightness tolerance. Processes include milling, turning, drilling, boring, threading, tapping, forming, knurling, counterboring, countersinking, reaming and laser cutting. Secondary services such as assembly, centerless grinding, heat treating, plating and welding. Prototype and low to high volume production offered with maximum 50,000 units. Suitable for fluid power, pneumatics, hydraulics and valve applications. Serves the aerospace, aircraft, military, medical and defense industries.PTJ will strategize with you to provide the most cost-effective services to help you reach your target,Welcome to Contact us ( sales@pintejin.com ) directly for your new project.
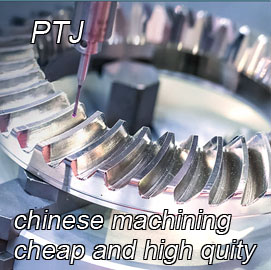
- 5 Axis Machining
- Cnc Milling
- Cnc Turning
- Machining Industries
- Machining Process
- Surface Treatment
- Metal Machining
- Plastic Machining
- Powder Metallurgy Mold
- Die Casting
- Parts Gallery
- Auto Metal Parts
- Machinery Parts
- LED Heatsink
- Building Parts
- Mobile Parts
- Medical Parts
- Electronic Parts
- Tailored Machining
- Bicycle Parts
- Aluminum Machining
- Titanium Machining
- Stainless Steel Machining
- Copper Machining
- Brass Machining
- Super Alloy Machining
- Peek Machining
- UHMW Machining
- Unilate Machining
- PA6 Machining
- PPS Machining
- Teflon Machining
- Inconel Machining
- Tool Steel Machining
- More Material