How to use shielding gas during laser welding?
Laser welding is mainly for the welding of thin-walled materials and precision parts. It can realize spot welding, butt welding, stitch welding, sealed welding, etc., with high aspect ratio, small weld width, small heat-affected zone, small deformation, and fast welding speed. The welding seam is smooth and beautiful. It does not need to be processed or simply processed after welding. The welding seam is of high quality, without air holes, can be accurately controlled, the focus is small, the positioning accuracy is high, and it is easy to realize automation. So, how to use the shielding gas correctly during laser welding?
Types of protective gas
Commonly used shielding gases for laser welding mainly include N2, Ar, He, and their physical and chemical properties are different, and therefore their effects on the weld are also different.
1.Nitrogen N2
The ionization energy of N2 is moderate, higher than that of Ar and lower than that of He. Under the action of laser, the ionization degree is average, which can reduce the formation of plasma cloud and increase the effective utilization rate of laser. Nitrogen can chemically react with aluminum alloy and carbon steel at a certain temperature to produce nitrides, which will increase the brittleness of the weld, reduce the toughness, and will have a greater adverse effect on the mechanical properties of the weld joint. Therefore, it is not recommended to use nitrogen. Aluminum alloy and carbon steel welds are protected.
The nitride produced by the chemical reaction between nitrogen and stainless steel can increase the strength of the weld joint, which will help improve the mechanical properties of the weld. Therefore, nitrogen can be used as a shielding gas when welding stainless steel.
2.Argon Ar
The ionization energy of Ar is relatively low, and the ionization degree is high under the action of laser, which is not conducive to controlling the formation of plasma cloud and will have a certain impact on the effective utilization of laser. However, the activity of Ar is very low, and it is difficult to chemically interact with common metals. The cost of Ar is not high. In addition, the density of Ar is higher, which is beneficial to sink to the top of the weld pool, and can better protect the weld pool, so it can be used as a conventional shielding gas.
3.Helium He
The ionization energy of He is high, the ionization degree is very low under the action of laser, and the formation of plasma cloud can be well controlled. The laser can act on metal very well, and the activity of He is very low, and it basically does not chemically react with metal. It is a good shielding gas for welding seams, but the cost of He is too high. Generally, mass production products will not use this gas. He is generally used for scientific research or products with very high added value.
The important role of welding shielding gas
From a technical point of view, only by changing the composition of the shielding gas, the following five important effects on the welding process can be produced:
(1) Improve the welding wire deposition rate Compared with the traditional pure carbon dioxide, the argon-rich gas mixture usually brings higher production efficiency. The argon content should exceed 85% to achieve jet transition. Of course, to increase the welding wire deposition rate requires the selection of appropriate welding parameters. The welding effect is usually the result of multiple parameters. Inappropriate welding parameter selection will usually reduce the welding efficiency and increase the post-weld slag removal work.
(2) Controlling the spatter and reducing the low ionization potential of the argon gas after welding to improve the stability of the arc, and correspondingly reduce the spatter. The recent new welding power technology has controlled the spatter of CO2 welding. Under the same conditions, if the mixed gas is used, the spatter can be further reduced and the welding parameter window can be enlarged.
(3) Control the welding seam formation, reduce the excessive welding CO2 welding seam tends to protrude outwards, leading to excessive welding and increasing welding cost. The argon gas mixture is easy to control the welding seam formation and avoid the waste of welding wire.
(4) Increase the welding speed. By using argon-rich gas mixture, even if the welding current is increased, the spatter can still be controlled very well. The advantage brought by this is the increase in welding speed, especially for automatic welding, which greatly improves production efficiency.
(5) Control of welding fume. Under the same welding operating parameters, the argon-rich mixture greatly reduces welding fume compared to carbon dioxide. Compared with investing in hardware equipment to improve the welding operation environment, the use of argon-rich gas mixture is an additional advantage to reduce source pollution.
In summary, it can be seen that by selecting a suitable welding shielding gas, the welding quality can be improved, the total welding cost can be reduced, and the welding efficiency can be improved. At present, in many industries, argon gas mixtures have been widely used, but due to herd reasons, most domestic enterprises use 80% Ar+20% CO2. In many applications, the shielding gas does not give the best results. Therefore, choosing the best gas is actually the easiest way to improve the level of product management for a welding enterprise on the way forward. The most important criterion for selecting the best shielding gas is to be able to meet the actual welding needs to the greatest extent. In addition, a proper gas flow rate is a prerequisite to ensure welding quality, and too much or too small flow rate is not conducive to welding.
Typical products
(1) Stargold binary argon mixed gas Stargold argon-rich mixed gas is characterized by stable welding arc, stable welding process, bright surface after welding, no spatter, and no need for polishing after welding.
In some auto parts industries, due to the presence of oxide scale on the surface of the weld, painting or electrophoresis after welding cannot be attached to the oxide scale. Reducing gas reactivity can help reduce the production of these surface oxide scales. As shown in Figure 1. Using stargold5, the weld surface is clean and bright without splashing.
(2) Robostar is a ternary mixed gas suitable for automatic welding process, with strong penetration capability, high welding efficiency, suitable for multiple droplet transfer modes, and high joint fatigue strength. Especially suitable for the automotive industry. Robostar is the best choice to solve the problem when there is excess stress at the weld foot of the joint due to the uneven transition of the weld metal to the base metal surface caused by the convex surface of the weld, which causes the fatigue strength to decrease. As shown in Figure 2, the transition from the weld to the base metal is smooth and there is no stress concentration.
(3) Compared with CO2, Stargon's ternary gas mixture can increase welding speed by 20%-30% and reduce smoke and dust by 50%-100%. It is a very environmentally friendly protective gas. It is suitable for all kinds of droplet transfer forms, the welding process is stable, and the weld seam is formed well.
Link to this article: How to use shielding gas during laser welding?
Reprint Statement: If there are no special instructions, all articles on this site are original. Please indicate the source for reprinting:https://www.cncmachiningptj.com/,thanks!
PTJ® provides a full range of Custom Precision cnc machining china services.ISO 9001:2015 &AS-9100 certified. 3, 4 and 5-axis rapid precision CNC machining services including milling, sheet metal to customer specifications,Capable of metal & plastic machined parts with +/-0.005 mm tolerance.Secondary services include CNC and conventional grinding, laser cutting,drilling,die casting,sheet metal and stamping.Providing prototypes, full production runs, technical support and full inspection.Serves the automotive, aerospace, mold&fixture,led lighting,medical,bicycle, and consumer electronics industries. On-time delivery.Tell us a little about your project’s budget and expected delivery time. We will strategize with you to provide the most cost-effective services to help you reach your target,Welcome to Contact us ( sales@pintejin.com ) directly for your new project.
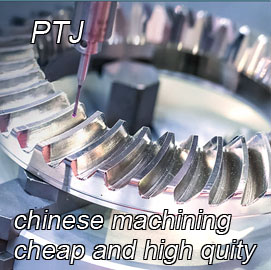
- 5 Axis Machining
- Cnc Milling
- Cnc Turning
- Machining Industries
- Machining Process
- Surface Treatment
- Metal Machining
- Plastic Machining
- Powder Metallurgy Mold
- Die Casting
- Parts Gallery
- Auto Metal Parts
- Machinery Parts
- LED Heatsink
- Building Parts
- Mobile Parts
- Medical Parts
- Electronic Parts
- Tailored Machining
- Bicycle Parts
- Aluminum Machining
- Titanium Machining
- Stainless Steel Machining
- Copper Machining
- Brass Machining
- Super Alloy Machining
- Peek Machining
- UHMW Machining
- Unilate Machining
- PA6 Machining
- PPS Machining
- Teflon Machining
- Inconel Machining
- Tool Steel Machining
- More Material