How to identify the welding method?
In most people’s minds, welding is just a welder’s stabbing with a welding rod. It belongs to a very ordinary type of work, even a very hard and undecent job, but anyone who knows a little about the welding industry will do it. Know that welding is not so simple.
What is welding?
Welding refers to a way of connecting two materials. A more scientific explanation is: a method of making the atoms of two materials reach the distance between atoms by heating or pressing or both.
If you have studied physics in junior high school, you will know that the atomic gravity of the distance between atoms is huge. Too close will cause repulsion, and a little farther will be attractive. The active atoms make the atom and the atom reach the distance between atoms through irregular movement, thus forming a welding. Therefore, welding is an irreversible connection method, which is somewhat different from riveting and bonding.
Through the concept, you will know that welding is very extensive. Therefore, ceramics can be welded to steel, plastics can be welded, etc. Of course, not every material can be welded. Similarly, not every welding method is Suitable for all materials.
recognition methods
⑴Identification of welding method (manual welding or automatic welding)
The welding method (manual welding or automatic welding) is easier to identify. In most cases of automatic welding, there is no welding wave image. If the welding wave shown in the figure below appears, it is also automatic welding.
The welding seam of liquefied gas cylinders is generally automatic welding. The butt joint ring welds of pipes with double-wall single projection or double-wall double projection transillumination are generally manual welding.
⑵Recognition of welding type (single-side welding or double-side welding)
As shown in the left figure below, the root of single-sided welding should be formed, with internal excess height or overhead welding to form an internal recess. Therefore, the recognition of single-sided welding mainly depends on whether there is a narrower root image in the weld image. If there is, it is single-sided welding.
Double-sided welding is welded on both sides, and the reinforcement on both sides is wider, as shown in the figure below, there is no narrow root image.
⑶ Welding position (flat welding, vertical welding, horizontal welding, overhead welding)
① Welding:
The welding plate is placed horizontally, and the position where the welding rod (or wire) is welded vertically downward is called flat welding.
Most automatic welding is flat welding, no welding wave. The welding wave of manual flat welding is large, similar to water ripples. Please refer to the picture of the appearance of the weld.
② Vertical welding:
the welding plate is placed vertically on the ground, the welding bead runs vertically, and the welding position where the welding rod (or wire) is roughly horizontally aligned with the welding bead for welding is called vertical welding. Vertical welding is mostly manual welding, welding from bottom to top, the arc of welding wave is small. When welding, the welding rod swings from side to side, sometimes forming two welding waves on the left and right. See the picture of weld appearance.
③Horizontal welding:
the welding plate is placed vertically on the ground, the welding bead runs horizontally, and the welding position where the welding rod (or wire) is roughly horizontally aligned with the welding bead for welding is called horizontal welding. Horizontal welding is manual welding, welding from left to right or from right to left,
Especially when covering the surface, first weld the lower weld bead and then weld the upper weld bead to form a weld groove along the longitudinal direction of the weld seam. The corresponding weld groove image will appear on the film. Refer to the weld appearance diagram.
④ Overhead welding:
The welding plate is placed horizontally, and the position where the welding rod (or wire) is welded vertically upward is called overhead welding.
Overhead welding is manual welding, which is the most difficult position to weld. If the fusion welding metal can't get up, you will stay. The arc of the welding wave is also small, which is often difficult to distinguish from vertical welding in terms of images. Generally, the surface of the weld is sometimes uneven, and single-sided welding is prone to concave defects, which can be judged.
Introduction to Overhead Welding
Welding characteristics:
1. The molten metal falls due to gravity, and the shape and size of the molten pool should not be controlled.
2. It is difficult to transport the strip, and the surface of the weldment is not suitable for welding.
3. Defects such as slag inclusion, incomplete penetration, weld bead and poor weld formation are easy to appear.
4. The molten weld metal splashes and spreads, which can easily cause scalding accidents.
5. The efficiency of overhead welding is lower than that of other positions.
Key points of welding:
1. Overhead welding of butt welds.
When the thickness of the weldment is less than or equal to 4mm, use type I grooves and use φ3.2mm welding rods with moderate welding current; when the welding thickness is greater than or equal to 5mm, multi-layer and multi-pass welding should be used.
2. The welding seam of T-shaped joint is overhead welding.
When the welding foot is less than 8mm, single-layer welding should be used, and when the welding foot is larger than 8mm, multi-layer and multi-pass welding should be used.
3. According to the specific situation, adopt the correct shipping method:
(1) When the size of the welding foot is small, the linear or linear reciprocating type is used to complete the single-layer welding; when the size of the welding foot is large, the multi-layer welding or multi-layer multi-pass welding can be used, and the first layer should be used Straight line transport, other layers can choose oblique triangle or oblique ring transport method.
(2) No matter which kind of transportation method is adopted, the weld metal should not be too much every time it passes to the molten pool.
How to distinguish between flat welding, vertical welding, horizontal welding, overhead welding and their welding characteristics during film evaluation
Introduction to flat welding
Welding characteristics:
1. The weld metal mainly relies on its own weight to transition to the molten pool.
2. The shape and metal of the molten pool are easy to maintain and control.
3. For welding metals with the same thickness, the welding current in the flat welding position is larger than that in other welding positions, and the production efficiency is high.
4. The slag and molten pool are prone to mixing, especially when welding flat fillet welds, the slag is easy to lead and form slag inclusion.
*It is not easy to distinguish the slag of acid welding rod from the molten pool; the two of alkaline welding rods are relatively clear; the HG20581 standard clearly states that acid welding rods cannot be used in Class II and III vessels.
5. Improper welding parameters and operations can easily lead to defects such as weld bead, undercut, and welding deformation.
6. When the back side of single-side welding is freely formed, the first weld is prone to uneven penetration procedures and poor back molding.
Key points of welding:
1. According to the thickness of the plate, a larger diameter electrode and a larger welding current can be used.
2. When welding, the welding rod and the weldment form an angle of 60~80°, and the separation of slag and liquid metal is controlled to prevent the slag from appearing in advance.
3. When the plate thickness is less than or equal to 6mm, the butt flat welding generally has a type I groove, and the front welding seam should be short-arc welding with a φ3.2~4 electrode, and the penetration depth can reach 2/3 of the plate thickness; before the back is sealed, It is not necessary to clean the roots (except for important structures), but the slag must be cleaned up and the current can be larger.
4. If there is unclear mixing of slag and molten pool metal in butt flat welding, the arc can be elongated, the electrode can be tilted forward, and the slag can be pushed to the back of the molten pool to prevent slag inclusion.
5. When welding horizontally inclined welds, upslope welding should be used to prevent slag inclusion and molten pool from moving forward to avoid slag inclusion.
6. When using multi-layer and multi-pass welding, pay attention to the number of welding passes and welding sequence, and each layer should not exceed 4~5mm.
7. For flat-angle welded joints of T type, corner joint, and overlap joint, if the thickness of the two plates is different, the angle of the welding rod should be adjusted to deflect the arc to one side of the thick plate, so that the two plates are heated evenly.
8. The correct choice of shipping method
(1) When the welding thickness is ≤6mm, type I groove butt flat welding, when double-sided welding is adopted, the front welding seam adopts a straight line, which is slightly slower; the back welding seam also adopts a straight line, and the welding current is slightly larger. , Faster.
(2) When the thickness of the plate is ≤6mm, when opening other forms of grooves, multi-layer welding or multi-layer multi-pass welding can be used. The first layer of bottom welding should use small current electrode, small standard current, straight line or sawtooth. Shape transport bar welding. For filling layer welding, a larger diameter electrode and short arc welding with larger welding current can be selected.
(3) When the size of the leg of the flat fillet welding of the T-joint is less than 6mm, single-layer welding can be used, and the linear, oblique ring or zigzag-shaped transport method can be used; when the size of the leg is larger, multi-layer welding or multi-layer welding should be used. Multi-pass welding, bottom welding adopts linear strip transportation method, and the filling layer can choose oblique sawtooth or oblique circular strip transportation.
(4) In general, multi-layer and multi-pass welding should be welded by the straight-line transport method.
Introduction to vertical welding
There are two vertical welding operation methods: one is to apply welding from bottom to top, which is called vertical welding; the other is to apply welding from top to bottom, which is called vertical welding. At present, the most widely used in production is welding from bottom to top, and this method is the focus in practice.
1. The essentials of upward vertical welding operation
l) When welding, you should choose a smaller diameter electrode (2.5mm~4mm) and a smaller welding current (10%~15% smaller than flat butt welding), so that the volume of the molten pool is small and the cooling and solidification is fast, which can reduce and prevent The molten metal trickles down.
2) Using short arc welding, the arc length is not greater than the diameter of the electrode, the arc blowing force is used to hold the molten pool, and the short arc operation is conducive to the droplet transfer.
3) The working angle of the electrode is 90°, and the forward inclination angle is -10~-30°, that is, the electrode is inclined in the opposite direction of the welding direction, so that the arc blowing force produces an upward thrust on the molten pool to prevent the molten metal from dripping down.
4) For the convenience of right-handed operation and observation of the molten pool, the welder's body should not be directly facing the weld, but slightly to the left.
2. Downward vertical welding method
The downward vertical welding method is only suitable for the welding of thin plates and less important structures. Because the downward vertical welding is more prone to sinking than the upward vertical welding of molten metal and slag, the weld is prone to defects such as slag inclusion and pores. The downward vertical welding method is characterized by fast welding speed. The welding depth is shallow, the melting width is narrow, it is not easy to burn through, the weld seam is beautifully formed, and the operation is simple, but it requires heat training to master the operating skills. The main points of operation are as follows:
l) The welding current should be moderate to ensure good fusion;
2) When welding, make the welding rod perpendicular to the surface of the weldment and use the direct method to strike the arc. Use a large forward inclination angle of the welding rod, about 30~40°, and use the arc blowing force to hold the molten pool to prevent the molten pool from dripping;
3) Use the straight-line strip method to avoid lateral swing as much as possible, but sometimes it can also be slightly lateral swing to facilitate good fusion of both sides of the weld with the base metal. For the vertical downward welding method, it is better to use a special electrode for vertical downward welding with higher slag viscosity. In addition to the use of AC welding power sources, ordinary DC arc welding power sources should be welded by the DC reverse connection method.
Link to this article: How to identify the welding method?
Reprint Statement: If there are no special instructions, all articles on this site are original. Please indicate the source for reprinting:https://www.cncmachiningptj.com/,thanks!
PTJ® provides a full range of Custom Precision cnc machining china services.ISO 9001:2015 &AS-9100 certified. 3, 4 and 5-axis rapid precision CNC machining services including milling, sheet metal to customer specifications,Capable of metal & plastic machined parts with +/-0.005 mm tolerance.Secondary services include CNC and conventional grinding, laser cutting,drilling,die casting,sheet metal and stamping.Providing prototypes, full production runs, technical support and full inspection.Serves the automotive, aerospace, mold&fixture,led lighting,medical,bicycle, and consumer electronics industries. On-time delivery.Tell us a little about your project’s budget and expected delivery time. We will strategize with you to provide the most cost-effective services to help you reach your target,Welcome to Contact us ( sales@pintejin.com ) directly for your new project.
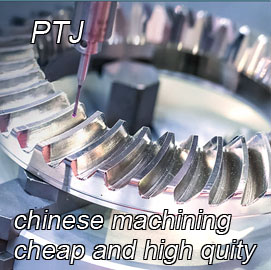
- 5 Axis Machining
- Cnc Milling
- Cnc Turning
- Machining Industries
- Machining Process
- Surface Treatment
- Metal Machining
- Plastic Machining
- Powder Metallurgy Mold
- Die Casting
- Parts Gallery
- Auto Metal Parts
- Machinery Parts
- LED Heatsink
- Building Parts
- Mobile Parts
- Medical Parts
- Electronic Parts
- Tailored Machining
- Bicycle Parts
- Aluminum Machining
- Titanium Machining
- Stainless Steel Machining
- Copper Machining
- Brass Machining
- Super Alloy Machining
- Peek Machining
- UHMW Machining
- Unilate Machining
- PA6 Machining
- PPS Machining
- Teflon Machining
- Inconel Machining
- Tool Steel Machining
- More Material