The Features And Operation Of Flat Welding And Vertical Welding
What Is Flat Welding
Flat welding refers to the welding process in which the welding place is at a horizontal position or at a small angle of inclination, the welding rod is located on the workpiece, and the welder looks down on the workpiece. This welding position belongs to the most easily welded position among all welding positions.
What Are The Characteristics Of Flat Welding
- ① The molten electrode of the welding rod can easily enter the molten pool by the blow of the arc and its own power, forming a natural transition.
- ②The slag and molten iron are not easy to disperse. Thicker welding rods and larger currents are allowed to form a larger molten pool. In the molten pool, the molten slag and liquid metal react evenly and produce a good crystalline structure. , Because the liquid slag and metal are not easy to flow, it is easy to control the shape and size of the weld to achieve beautiful and high-quality.
- ③Because the welding is performed from the top view, the operation is simple, which is convenient for beginners to practice and master, and the welder is easy to operate and not easy to fatigue.
- ④ The maximum welding current can be used when the thickness of the weldment allows, so the work efficiency is high and the application is wide.
- ⑤Molten slag and molten iron are likely to be mixed together and become unclear, or the slag will form defects such as slag inclusion and pores.
- ⑥ Due to improper selection of welding specifications such as welding current and groove form, as well as improper operation of the method and angle of the strip, it is easy to cause weld bumps and incomplete penetration when welding the first layer of bead. Therefore, double-sided welding is often used for flat welding of butt welds, that is, after the front side is welded, the root of the back side is grooved with a wind shovel or carbon arc gouging and then the back side weld is welded.
- ⑦When single-sided welding requires double-sided forming, the first layer is prone to uneven penetration and poor back forming, and the remaining layers are easier to grasp.
Operation Points Of Flat Welding
- 1. According to the thickness of the plate, a larger diameter electrode and a larger welding current can be used.
- 2. When welding, the welding rod and the weldment form an angle of 60-80°, and the separation of slag and liquid metal is controlled to prevent the slag from appearing in advance.
- 3. When the plate thickness is less than or equal to 6mm, the butt flat welding generally has a type I groove, and the front welding seam should be short-arc welding with a φ3.2-4 electrode, and the penetration depth can reach 2/3 of the plate thickness; before the back is sealed , It is not necessary to clean the roots (except for important structures), but the slag must be cleaned up and the current can be larger.
- 4. If there is unclear mixing of slag and molten pool metal in butt flat welding, the arc can be elongated, the electrode can be tilted forward, and the molten slag can be pushed to the back of the molten pool to prevent slag inclusion.
- 5. When welding horizontally inclined welds, upslope welding should be used to prevent slag inclusion and molten pool from moving forward to avoid slag inclusion.
- 6. When using multi-layer and multi-pass welding, pay attention to the number of welding passes and welding sequence, and each layer should not exceed 4-5mm.
- 7. For flat-angle welded joints of T type, corner joint, and overlap joint, if the thickness of the two plates is different, the angle of the welding rod should be adjusted to deflect the arc to one side of the thick plate, so that the two plates are heated evenly.
- 8. The correct choice of shipping method
For workpieces with a thickness of less than 6mm, the welding is generally carried out without grooves. For butt flat welding without grooves, the straight line method is used for the front weld, and the reverse side weld also adopts the straight line method. In order to ensure penetration, the current can be larger, and the speed of transporting the strip will increase accordingly.
For open-groove butt flat welding, multilayer welding or multilayer multi-pass welding can be used, and the bottom welding adopts a straight line, and the diameter of the electrode and the welding current are smaller. In multi-layer welding, the remaining layers of the weld bead should be linear, zigzag or crescent-shaped as required. In multi-layer and multi-pass welding, the method of linear transport is adopted.
For T-shaped joints, corner joints, and lap joints with smaller weld foot sizes, single-layer welding can be used, and straight or oblique zigzag, oblique circular strips can be used. When the size of the welding foot is large, multi-layer welding or multi-layer multi-pass welding is generally adopted. The first layer adopts the straight-line striping method, and the remaining layers can use the oblique ring and zigzag-shaped strips. For multi-layer and multi-pass welding, linear strips are generally used. For boat-shaped welds, in order to ensure the penetration of the roots, the operation points are similar to those of open groove butt flat welding.
What Is Vertical welding
Vertical welding refers to welding from top to bottom or bottom to top along the joint. The welding position where the weld inclination angle is 90° (vertical upward) and 270° (vertical downward) is called the vertical welding position. The welding performed at the vertical welding position is called vertical welding.
What are the characteristics of vertical welding
- 1. The molten pool metal and molten slag fall due to their own weight and are easy to separate.
- 2. When the temperature of the molten pool is too high, the molten pool metal is easy to drip down to form defects such as weld bead, undercut, slag inclusion, etc., and the weld is uneven.
- 3. The root of the T-joint weld is easy to form incomplete penetration.
- 4. The degree of penetration is easy to grasp.
- 5. Welding productivity is lower than flat welding.
Operation Points Of Vertical Welding
1. Maintain the correct welding rod angle;
2. In production, vertical vertical welding is commonly used, and vertical vertical welding requires special welding rods to ensure the quality of the weld. The welding current for vertical up welding is 10-15% smaller than that for flat welding, and a smaller electrode diameter (<φ4mm) should be used
3. Use short arc welding to shorten the distance from the droplet to the molten pool.
4. Use the correct shipping method.
- (1) T-groove butt joint (usually used for thin plates) when vertical welding is performed, linear, zigzag, crescent-shaped strip welding is commonly used, and the maximum arc length is not more than 6mm.
- (2) When opening other forms of groove butt butt vertical welding, the first layer of weld is often welded by broken, crescent-shaped and triangular-shaped strip welding with small swing. Later, each layer can be used for crescent or zigzag striping.
- (3) During vertical welding of T-shaped joints, the welding rod should have proper residence time on both sides and top corner of the welding seam, and the swing range of the welding rod should not be greater than the width of the welding seam. The operation of the welding rod should be similar to that of other vertical welding with grooves.
- (4) When welding the cover layer, the surface shape of the weld is determined by the method of transportation. Crescent-shaped strips can be used for welding seam surfaces with higher requirements; zigzag strips can be used for flat surfaces (the concave shape in the middle is related to the pause time).
Link to this article: The Features And Operation Of Flat Welding And Vertical Welding
Reprint Statement: If there are no special instructions, all articles on this site are original. Please indicate the source for reprinting:https://www.cncmachiningptj.com/,thanks!
PTJ® provides a full range of Custom Precision cnc machining china services.ISO 9001:2015 &AS-9100 certified. 3, 4 and 5-axis rapid precision CNC machining services including milling, sheet metal to customer specifications,Capable of metal & plastic machined parts with +/-0.005 mm tolerance.Secondary services include CNC and conventional grinding, laser cutting,drilling,die casting,sheet metal and stamping.Providing prototypes, full production runs, technical support and full inspection.Serves the automotive, aerospace, mold&fixture,led lighting,medical,bicycle, and consumer electronics industries. On-time delivery.Tell us a little about your project’s budget and expected delivery time. We will strategize with you to provide the most cost-effective services to help you reach your target,Welcome to Contact us ( sales@pintejin.com ) directly for your new project.
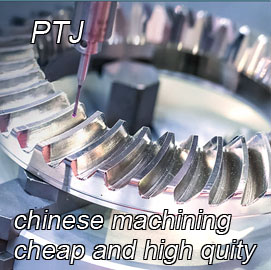
- 5 Axis Machining
- Cnc Milling
- Cnc Turning
- Machining Industries
- Machining Process
- Surface Treatment
- Metal Machining
- Plastic Machining
- Powder Metallurgy Mold
- Die Casting
- Parts Gallery
- Auto Metal Parts
- Machinery Parts
- LED Heatsink
- Building Parts
- Mobile Parts
- Medical Parts
- Electronic Parts
- Tailored Machining
- Bicycle Parts
- Aluminum Machining
- Titanium Machining
- Stainless Steel Machining
- Copper Machining
- Brass Machining
- Super Alloy Machining
- Peek Machining
- UHMW Machining
- Unilate Machining
- PA6 Machining
- PPS Machining
- Teflon Machining
- Inconel Machining
- Tool Steel Machining
- More Material