The Advantages And Development Mileage Of Japanese Machine Tool Industry
Japan is a well-known machine tool power in the world. Japanese machine tool technology is almost impossible to compete in the world. Its domestic brands such as Mazak, Fanuc, Okuma, and Amada are all outstanding in the machine tool industry. Japan is the third country in the world to establish a machine tool industry and realize industrialization after the United States and Germany. In 1889, with the establishment of the Ikegai Iron Factory, Japan began to produce the first machine tool.
Up to now, Japan's machine tool industry has reached the world's top level, with many top machine tool manufacturers, such as Yamazaki Mazak (MAZAK), Amada Manufacturing Co., Ltd., Okuma Machine Tool and so on. These machine tool manufacturers master the world's top machine tool inventions and technologies. In addition to having multiple manufacturers, these manufacturers have different characteristics in different fields and strong heterogeneity, which makes it possible for Japan to achieve a "monopoly" in the manufacturing field. Yamazaki Mazak is characterized by high speed and high precision; Amada Manufacturing is characterized by reasonable mechanical structure, efficient and pollution-free operation, and advanced technology with simulation automation to provide users with the most simplified machining guarantee; the characteristics of Okuma machine tools It is characterized by good rigidity, high cutting efficiency, high precision, long life, convenient operation, and the realization of electromechanical integration, etc., which can meet different types of work for machining.
Why Is The Japanese Machine Tool Industry So Powerful? How Did It Develop So Fast?
First of all, Japan is a very good learning nation. After coming out of the feudal empire, they did not start from scratch on their own, but introduced a large number of advanced technology and equipment, including the purchase of advanced machine tools from Germany, the United States and other countries for anatomical analysis and analysis. Hire foreign machine tool experts as consultants and guides to develop and produce domestic machine tools, so as to gain the fastest mastery of advanced machine tool technology. Not only professional technology, but also management experience. After decades of imitating, Japan has incorporated its own national characteristics into industrial management and technological inventions. This way, the machine tool industry with a strong “Yamato nation” mark is very Conducive to their own national identity. With the support of the people, there will be development prospects. More importantly, Japan has an almost crazy pursuit of technological innovation: Japan is the mother machine with the highest precision in the global ultra-precision machining field. AHN15-3D free-form surface diamond machining machine from Jtket, Japan, this equipment is mainly used for ultra-precision turning and grinding of various optical lenses and blue lens molds. The performance of this machine tool has reached 30nm component forming accuracy and 1nm-level ra surface roughness. Only in terms of machining accuracy, it is nearly 8 times higher than the LODTM and DTM-3 of LLNL in the United States and the OAGM2500 of CUPE in the United Kingdom. Even though such ultra-high-precision machine tools are costly to build and have not extensive application scenarios, Japan is still tirelessly searching for the limits of accuracy. How can such a machine tool industry that pursues limits and extremes not make the world feel terrified. Not all countries can achieve such meticulous and extreme.How Did Japanese Machine Tools Develop
Have you heard of the famous "Toshiba Machine Tool Incident in Japan". To put it simply, during the Cold War, Japan violated the "Batumi Treaty" and used civet cats for princes to export a batch of CNC machine tools to the former Soviet Union that were explicitly prohibited by this treaty, which was later exposed. And this equipment is nothing but a high-precision CNC machine tool for machining marine propellers. After the former Soviet Union received these high-precision machine tools, the high-precision machining level of heavy industrial equipment such as submarines has been greatly improved, especially the quietness level of nuclear submarines has been greatly improved, and this has made the United States exhausted all the efforts made by the United States for decades. . What I noticed is that Japan was able to produce high-end machine tools during the Cold War. With so many years of technological development, Japanese machine tools are now in a leading position in the world. Its domestic brands such as Mazak, Fanuc, Okuma and Amada are all outstanding in the machine tool industry. Take the Japanese "Canglong" submarine as an example. It is a large diesel-electric submarine with low-noise navigation performance and adopts many perfect noise reduction measures. By the way, let’s give everyone a popular science, what are the main noises of submarines? The noise mainly comes from the submarine's internal machinery and propellers. For example, in the frequency range of 10 cycles per second, 90% of the noise comes from the rotating propeller-that is, the propeller. Therefore, it is necessary to produce advanced propellers that have low vortex noise and are difficult to detect by the opponent's sonar. "Canglong" uses a single-shaft, large skew, seven-blade, high-curvature propeller.What Is The Difficulty Of Machining This Kind Of Propeller?
It is because its blade side angle is relatively large. The so-called side skew angle is the angle between the centerline of the hub and the centerline of the blade. Theoretically, as long as the skew angle is greater than forty degrees, the water pressure fluctuation on the back of the propeller will be reduced by half. Therefore, the large skew propeller is much more ideal than ordinary propellers for suppressing the generation of cavitation. Not to mention that the side slope angle used on the submarine is larger, which can reach more than forty degrees, the machining is more precise, and the material is more advanced and complex. Therefore, to process this kind of propeller, it is necessary to use a nine-axis linkage CNC milling machine.
How Powerful Is This Machine Tool?
In the machine tool industry, CNC machine tools are generally divided into standards by the number of axes. Below three axles are low gears, three to five axles are medium and high grades, and above five axles are high gears. Generally, five-axis can handle most products, and nine-axis is a high-end equipment. for example: The diameter of our ordinary hair strands is usually 60 microns, and an ultra-high precision machine tool can have a machining accuracy of 0.01-0.001 microns, that is, it can reach or close to the nanometer level, which is so small that it can't be distinguished by the naked eye. At the same time, the precision of ultra-high precision machine tools is 1000 times higher than that of ordinary CNC machine tools. The above is about why the Japanese machine tool industry is so powerful? The answer to how Japanese machine tools developed, and the enlightenment from the development of the Japanese machine tool industry: machine tools are a symbol of the level of manufacturing in a country, and advanced CNC machining equipment is an important strategic material for any country! A good machine tool requires the common progress of the entire industry chain. At the same time, the entire machine tool industry also needs to have a reasonable layout to achieve specialized division of labor. To put it in the vernacular, each component must perform its own duties, and each component must have a clear division of labor. At the same time, the research and development of the core technology of machine tool equipment, without decades of concentrated research, is unlikely to have substantive results. It takes a long process to know whose technical strength is not accumulated in one or two days. And if China wants to start "Made in China", it also needs this kind of extreme pursuit.Link to this article: The Advantages And Development Mileage Of Japanese Machine Tool Industry
Reprint Statement: If there are no special instructions, all articles on this site are original. Please indicate the source for reprinting:https://www.cncmachiningptj.com/,thanks!
PTJ® provides a full range of Custom Precision cnc machining china services.ISO 9001:2015 &AS-9100 certified. 3, 4 and 5-axis rapid precision CNC machining services including milling, sheet metal to customer specifications,Capable of metal & plastic machined parts with +/-0.005 mm tolerance.Secondary services include CNC and conventional grinding, laser cutting,drilling,die casting,sheet metal and stamping.Providing prototypes, full production runs, technical support and full inspection.Serves the automotive, aerospace, mold&fixture,led lighting,medical,bicycle, and consumer electronics industries. On-time delivery.Tell us a little about your project’s budget and expected delivery time. We will strategize with you to provide the most cost-effective services to help you reach your target,Welcome to Contact us ( sales@pintejin.com ) directly for your new project.
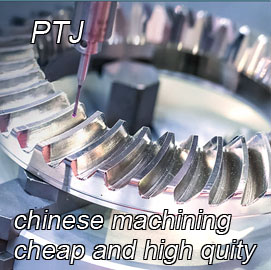
- 5 Axis Machining
- Cnc Milling
- Cnc Turning
- Machining Industries
- Machining Process
- Surface Treatment
- Metal Machining
- Plastic Machining
- Powder Metallurgy Mold
- Die Casting
- Parts Gallery
- Auto Metal Parts
- Machinery Parts
- LED Heatsink
- Building Parts
- Mobile Parts
- Medical Parts
- Electronic Parts
- Tailored Machining
- Bicycle Parts
- Aluminum Machining
- Titanium Machining
- Stainless Steel Machining
- Copper Machining
- Brass Machining
- Super Alloy Machining
- Peek Machining
- UHMW Machining
- Unilate Machining
- PA6 Machining
- PPS Machining
- Teflon Machining
- Inconel Machining
- Tool Steel Machining
- More Material