The Application Of Industrial Robot Machining Loading And Unloading
The Application Of Industrial Robot Machining Loading And Unloading
This article first introduces the composition, application significance and characteristics of industrial robot machining loading and unloading applications, and detailed analysis of the rigidity and accuracy of industrial robots in industrial robot machining loading and unloading applications, as well as the rapid recovery problems after collisions and failures. The problem is analyzed in detail and the key solving techniques are analyzed. Namely, terminal load automatic identification technology and dynamic torque feedforward technology, collision detection technology, zero point recovery technology, and finally the future development trend of human-machine collaboration and information fusion is proposed. |
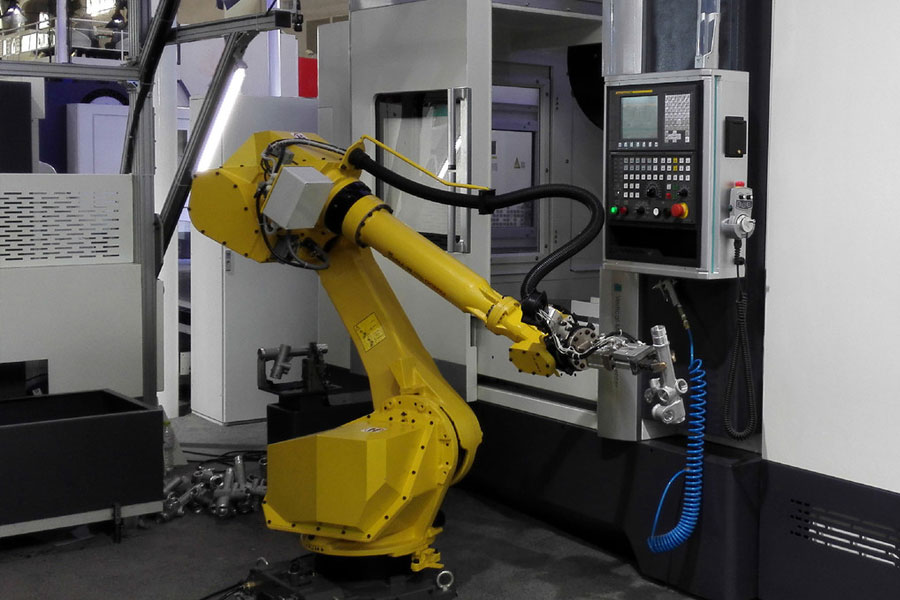
With the popularity of CNC machine tools, more and more users hope that the loading and unloading of CNC machine tools will be automated. On the one hand, it will increase the number of workers to take care of the machine tools, reduce personnel costs, and improve production efficiency and quality on the one hand. The large-scale application of industrial robots originated in the automotive industry. With the saturation of automotive industry applications, the general industry has become increasingly aware of robots. Since the 1990s, industrial robots in general fields have been used more and more widely, such as welding, palletizing, spraying, loading and unloading, polishing and grinding are common applications in general industries. This article focuses on the loading and unloading system of industrial robot machining.
The industrial robot machining loading and unloading system is mainly used for the loading of processing units and automatic production lines to be processed blanks, the unloading of processed workpieces, the transfer of workpieces between machine tools and machine tools, and the turnover of workpieces to realize turning, milling, and grinding. Automatic processing of metal cutting machine tools such as cutting and drilling.
The close integration of robots and machine tools has not only improved the level of automated production, but also improved the production efficiency and competitiveness of the factory. Mechanical processing of loading and unloading requires repeated and continuous operations, and requires consistency and accuracy of operations, while the processing process of parts in general factories needs to be continuously processed by multiple machine tools and multiple processes. With the increase in labor costs and the competitive pressure brought by the increase in production efficiency, the degree of automation of processing capabilities and flexible manufacturing capabilities have become the barriers to the improvement of factory competitiveness. The robot replaces manual loading and unloading operations, and realizes an efficient automatic loading and unloading system through automatic feeding bins, conveyor belts, etc., as shown in Figure 1.
One robot can correspond to the loading and unloading operations of one or more machine tools according to the requirements of the processing technology. In the robot one-to-many loading and unloading system, the robot completes the picking and placing of blanks and processed parts in different machine tools, which effectively improves the use efficiency of the robot. The robot can perform reciprocating operations on the linear layout of the machine tool assembly line through the rails installed on the ground, which minimizes the occupation of factory space, and can flexibly adapt to different operating procedures of different batches of products. The switching robot can continuously operate in harsh environments. , 24-hour operation, fully liberate factory production capacity, shorten delivery time, and improve market competitiveness.
1 The characteristics of industrial robot machining loading and unloading applications
- (1) High-precision positioning, fast handling and clamping, shorten the operation cycle, and improve the efficiency of the machine tool.
- (2) Robot operation is stable and reliable, effectively reducing unqualified products and improving product quality.
- (3) Continuous operation without fatigue, reducing the idle rate of machine tools, and expanding factory production capacity.
- (4) The high level of automation improves the precision of single product manufacturing and speeds up the mass production efficiency.
- (5) Highly flexible, quick and flexible to adapt to new tasks and new products, and shorten the delivery time.
2 Problems in the application of industrial robot machining and loading and unloading
2.1 Stiffness and accuracy issues
The machining robot is different from the general handling and grabbing robots. It is an operation that directly contacts the processing tools. Its motion principle must consider both rigidity and accuracy. The tandem robot has high repeat positioning accuracy, but due to the comprehensive factors of processing, assembly, rigidity, etc., the trajectory accuracy is not high, which has a greater impact on applications such as grinding, polishing, deburring, and cutting in the machining field. Therefore, the rigidity of the robot and the accuracy of the robot trajectory are the main problems faced by the machining robot.
2.2 Collision problem
Most of the machining robots work together with turning, milling, planing, and grinding machine tools. When the robot is performing machining, special attention should be paid to the problem of interference and collision between the dead zone and the workpiece. Once a collision occurs, both the machine tool and the robot need to be re-calibrated, which greatly increases the time for fault recovery, resulting in a loss of output, and in severe cases, it may also cause damage to the equipment. The perception before or after the collision is the main problem facing the safety and stability of machined robots. It is particularly important for machining robots to have area monitoring and collision detection functions.
2.3 Quick recovery problem after failure
The position data of the robot is fed back through the motor encoder of the drive shaft movement. Due to long-term operation, the mechanical structure, encoder battery, cable and other components will inevitably cause the zero position (reference position) of the robot to be lost. After the zero position is lost, the robot will store it. The program data will have no practical meaning. At this time, if the zero position cannot be restored accurately, the robot's job recovery workload is huge, so the zero position recovery problem is also particularly important.
3 Key solutions
3.1 End load automatic identification technology and dynamic torque feedforward technology
The automatic end load identification technology can identify the mass, center of mass and inertia of the end load of the robot. These parameters can be used in the robot dynamics feedforward, adjusting the servo parameters and speed planning, which can greatly improve the robot trajectory accuracy and high dynamic performance.
The dynamic torque feedforward technology is based on the traditional PID control and adds the torque feedforward control technology. This function can use the robot dynamics model and friction model to calculate the optimal driving force or torque when planning the trajectory path according to the static information such as the robot and the real-time dynamic information such as speed and acceleration, and the calculated value is transmitted as the feedforward value. Give the controller to compare with the preset value of the motor in the current loop, so as to obtain the best torque, drive the high-speed and high-precision movement of each axis, and then make the end TCP obtain higher trajectory accuracy.
3.2 Collision detection technology
This technology is based on robot dynamics modeling. When the robot or the end load of the robot collides with peripheral equipment, the robot can detect the extra torque generated by the collision. At this time, the robot stops automatically or goes in the opposite direction of the collision with low speed. Run to avoid or reduce the loss caused by collision.
3.3 Zero point recovery technology
Ordinary zero-point calibration methods, after the zero-mark alignment is completed, there will still be certain errors. The size of the error depends on the processing quality of the zero-mark and the attitude of the operator, and this part of the error cannot be eliminated by improving the processing requirements and performing operation training. . Using this technology, when the robot loses the zero point, the robot is moved to the vicinity of the zero point, so that the grooves or scribe lines can be fully aligned. At this time, read the motor encoder value to determine the compensation amount, so that the robot can accurately restore the zero position.
4 Future development direction
4.1 Human-machine collaboration
At present, most of the applications of industrial robots are in workstations or assembly lines, and there is no contact and cooperation with humans. In the future, the cooperation between humans and robots will be a very important development direction for more complex production processes. The key issues that industrial robots need to solve to achieve human-machine collaboration are how to perceive human operations, how to interact with humans, and the most important thing is how to ensure the safety mechanism of human-machine collaboration. While realizing human-machine cooperation and ensuring human safety, it is also necessary to fully consider the production rhythm, which will be an important trend. In recent years, some human-machine collaborative robots have appeared, but under the condition of ensuring safety, the beat is relatively slow, and the stability needs to be improved. More importantly, it is faster to integrate with application scenarios and find suitable application scenarios. Land development and promotion.
4.2 Information Fusion
In the future, smart factories will integrate the Internet of Things, sensors, robots, and big data. Industrial robots, as one of the most important basic equipment, must not only effectively interact with multi-sensors, but also communicate with higher-level systems such as MES. The system conducts information exchange. Based on the Internet of Things and big data, the upper level performs process data extraction, process program optimization, or remote diagnosis and maintenance of equipment, and issues instructions to industrial robots to complete the entire intelligent control process. Therefore, the information fusion of industrial robots will be a very important development trend.
Link to this article: The Application Of Industrial Robot Machining Loading And Unloading
Reprint Statement: If there are no special instructions, all articles on this site are original. Please indicate the source for reprinting:https://www.cncmachiningptj.com/,thanks!
PTJ CNC shop produces parts with excellent mechanical properties, accuracy and repeatability from metal and plastic. 5 axis CNC milling available.Machining high-temperature alloy range inclouding inconel machining,monel machining,Geek Ascology machining,Carp 49 machining,Hastelloy machining,Nitronic-60 machining,Hymu 80 machining,Tool Steel machining,etc.,. Ideal for aerospace applications.CNC machining produces parts with excellent mechanical properties, accuracy and repeatability from metal and plastic. 3-axis & 5-axis CNC milling available.We will strategize with you to provide the most cost-effective services to help you reach your target,Welcome to Contact us ( sales@pintejin.com ) directly for your new project.
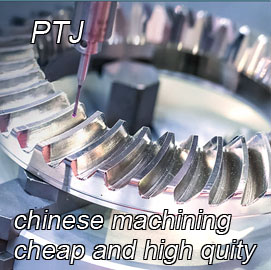
- 5 Axis Machining
- Cnc Milling
- Cnc Turning
- Machining Industries
- Machining Process
- Surface Treatment
- Metal Machining
- Plastic Machining
- Powder Metallurgy Mold
- Die Casting
- Parts Gallery
- Auto Metal Parts
- Machinery Parts
- LED Heatsink
- Building Parts
- Mobile Parts
- Medical Parts
- Electronic Parts
- Tailored Machining
- Bicycle Parts
- Aluminum Machining
- Titanium Machining
- Stainless Steel Machining
- Copper Machining
- Brass Machining
- Super Alloy Machining
- Peek Machining
- UHMW Machining
- Unilate Machining
- PA6 Machining
- PPS Machining
- Teflon Machining
- Inconel Machining
- Tool Steel Machining
- More Material