The Considerations For Drawing Die Design
The Considerations For Drawing Die Design
Stretching dies account for a very large proportion of the entire stamping die industry. Our common cups, the shell on the motor, and almost most products have more or less products that need to be stretched. The design of the mold is not to say that it can be calculated according to the conventional algorithm. There are too many processes full of variables, especially the stretching of some non-rotating bodies, which is prohibitive. Because there are too many factors to be considered in the design of the drawing die, such as the drawing coefficient, whether it reaches the limit of the material, the decision of the spring force, the direction of drawing, whether it is upward or downward, often cannot One-time molding requires many trials to achieve the desired result, and sometimes the mold may be scrapped. Therefore, accumulating experience in practice is of great help to the design of the drawing mold. In addition, the size of the cutting material also plays an important role in the trial production of the entire mold. So most of the time, when we design some irregular deep-drawn parts, we often reserve an empty step in the mold design stage. |
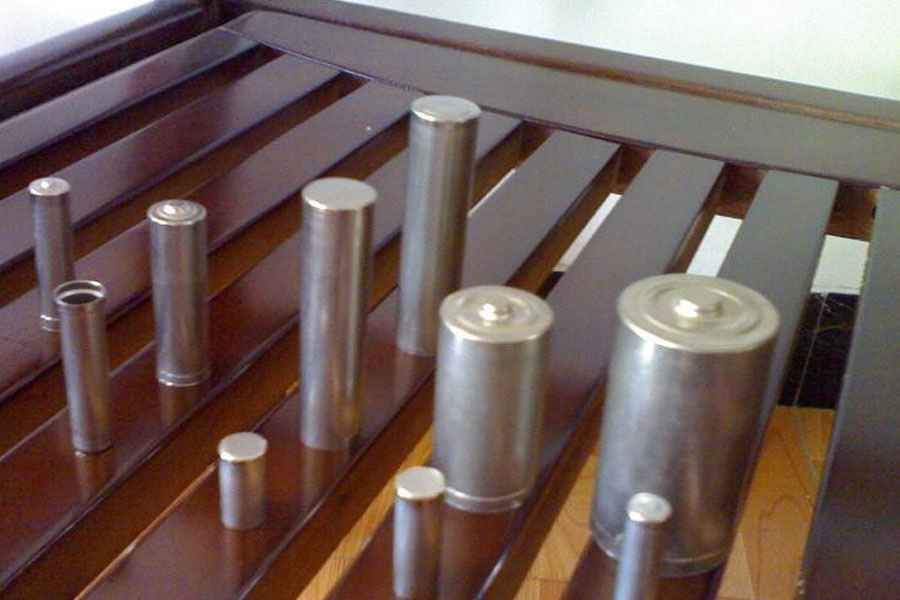
Stretching Material:
When the customer's requirements for the material are not very demanding, and repeated mold trials fail to meet the requirements, you can change to a material with good tensile properties and try again. A good material is half the success. For stretching, it must not be ignored. Cold-rolled thin steel sheets for drawing mainly include 08Al, 08, 08F, 10, 15, and 20 steels. The largest amount is 08 steel, which is divided into rimmed steel and killed steel. The rimmed steel is low in price and has good surface quality. The segregation is more serious and has a tendency of "strain aging". It is not suitable for parts that require high stamping performance and appearance requirements. Killed steel is better, with uniform performance but higher price. The representative brand is aluminum killed steel 08Al. Foreign steel has used Japanese SPCC-SD deep drawing steel, and its tensile properties are better than 08Al. When the customer's requirements for materials are not very demanding, and repeated mold trials fail to meet the requirements, they can change to another material and try again.
The Finish Of The Mold Surface.
When deep drawing is performed, the two sides of the die and the blank holder are not sufficiently ground, especially when drawing stainless steel plates and aluminum plates, drawing scars are more likely to occur, which can lead to tensile fractures in severe cases.
Determination Of Blank Size:
More wrinkles and less cracks are our principle. The blank positioning design should be correct. The blank diameter of the rotating body drawing part with simple shape will not be thinned. Although the material thickness changes, it is basically very similar to the original thickness. Closeness can be calculated based on the principle that the area of the blank and the area of the stretched part (if trimming must be added) are equal. However, the shape and process of stretched parts are often complicated, and sometimes they need to be thinned and stretched. Although there are many three-dimensional software that can calculate the unfolded material, its accuracy cannot meet the requirements of 100%.
Solution: sample. A product has to go through multiple processes, and the first process is generally a blanking process. First of all, it is necessary to carry out the calculation of the unfolded material, and have a general understanding of the shape and size of the blank, in order to determine the overall size of the blanking die. Do not process the convex and concave mold size of the blanking mold after the mold design is completed. First use wire cutting to process the blank (when the blank is larger, it can be milled by a milling machine and then clamped). After repeated experiments in the subsequent stretching process, the size of the blank is finally determined, and then the convex and concave molds of the blanking die are processed.
Experience 2: Invert the process, first try the drawing die, and then process the blanking edge size of the blank, which is half the effort.
Stretch coefficient
The stretching coefficient is one of the main process parameters in the calculation of the stretching process, and it is usually used to determine the sequence and number of stretching. There are many factors that affect the stretching coefficient m, including material properties, relative thickness of the material, stretching method (referring to whether there is a blank holder), stretching times, stretching speed, convex and concave die fillet radius, lubrication, etc. The calculation and selection principles of the tensile coefficient m are the key points introduced in various stamping manuals. There are many methods such as calculation, table look-up, calculation, etc., and I also choose according to the book. There is no new stuff. Please read the book. .
Experience 3: The relative thickness of the material, the stretching method (referring to whether there is a blank holder), and the number of stretching are not easy to adjust when repairing the mold. You must be cautious!! It is best to find a colleague when selecting the stretching coefficient m Again.
The choice of processing oil is very important. The way to distinguish whether the lubricating oil is suitable is when the product is taken out of the mold, if the product temperature is too high to be touched by hands, the choice of lubricating oil and the method of lubrication must be reconsidered, and the lubricating oil should be applied to the cavity. , Or put a film bag on the sheet.
Experience 4: When encountering tensile cracking, apply lubricating oil on the die (do not apply it on the convex die), and the workpiece is covered with a 0.013-0.018mm plastic film on the side of the die.
Workpiece Heat Treatment
Although it is not recommended, it is still necessary to say, During the stretching process, due to cold plastic deformation of the workpiece, cold work hardening occurs, which reduces its plasticity, increases deformation resistance and hardness, and the mold design is unreasonable. Intermediate annealing to soften the metal and restore plasticity.
Note: In the general process, the intermediate annealing is not necessary. After all, it is necessary to increase the cost. You must choose between increasing the process and increasing the annealing, and use it with caution! Annealing generally adopts low temperature annealing, that is, recrystallization annealing. There are two things to pay attention to when annealing: decarburization and oxidation. Here we mainly talk about oxidation. There is oxide scale after the workpiece is oxidized,
There are two disadvantages: thinning the effective thickness of the workpiece and increasing mold wear. When the company's conditions are not available, ordinary annealing is generally used. In order to reduce the generation of oxide scale, the furnace should be filled as much as possible during annealing. I have also used soil methods:
- - When there are few workpieces, it can be mixed with other workpieces (prerequisite: annealing process parameters should be basically the same)
- - Put the workpiece in the iron box and weld it to the furnace. In order to eliminate the oxide scale, pickling treatment should be carried out according to the situation after annealing. When the company's conditions are available, nitrogen furnace annealing can be used, that is, bright annealing. If you don't look closely, the color is almost the same as before annealing.
Experience 5: Add intermediate annealing process when dealing with metal with strong cold work hardening or when there is no other way to crack in the test mold.
A Few Points To Add
- 1. The size on the product drawing should be marked on one side as much as possible to make it clear whether the outer size or the inner cavity size is guaranteed, and the inner and outer dimensions cannot be marked at the same time. If the drawings provided by others have such problems, they should be communicated with them. If they can be unified, they should be unified. If they cannot be unified, they should know the assembly relationship between the workpiece and other parts.
- 2. For the last process, the size of the workpiece is outside, the die is the main, the gap is obtained by reducing the size of the punch; the size of the work piece is inside, the punch is the main, and the gap is obtained by increasing the size of the die;
- 3. The corner radius of the convex and concave molds should be designed as small as possible to bring convenience to the subsequent mold repair.
- 4. When judging the cause of the workpiece to crack, you can refer to it: the cracks caused by poor material quality are mostly jagged or irregular shapes, and the cracks caused by the process and the mold are generally relatively neat.
- 5. "More wrinkles, less cracks" According to this principle, adjust the flow of the material. The methods include adjusting the pressure of the blank holder, increasing the drawing bead, trimming the corner radius of the concave and convex mold, and cutting the process opening on the workpiece.
- 6. In order to ensure wear resistance and prevent tensile scratches, the concave-convex die holder ring must be quenched. It can also be hard-coated, surface TD treatment can also be used, and tungsten steel can be used as concave and convex molds when necessary.
Link to this article: The Considerations For Drawing Die Design
Reprint Statement: If there are no special instructions, all articles on this site are original. Please indicate the source for reprinting:https://www.cncmachiningptj.com/,thanks!
PTJ CNC shop produces parts with excellent mechanical properties, accuracy and repeatability from metal and plastic. 5 axis CNC milling available.Machining high-temperature alloy range inclouding inconel machining,monel machining,Geek Ascology machining,Carp 49 machining,Hastelloy machining,Nitronic-60 machining,Hymu 80 machining,Tool Steel machining,etc.,. Ideal for aerospace applications.CNC machining produces parts with excellent mechanical properties, accuracy and repeatability from metal and plastic. 3-axis & 5-axis CNC milling available.We will strategize with you to provide the most cost-effective services to help you reach your target,Welcome to Contact us ( sales@pintejin.com ) directly for your new project.
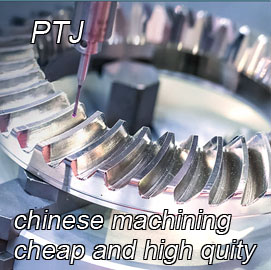
- 5 Axis Machining
- Cnc Milling
- Cnc Turning
- Machining Industries
- Machining Process
- Surface Treatment
- Metal Machining
- Plastic Machining
- Powder Metallurgy Mold
- Die Casting
- Parts Gallery
- Auto Metal Parts
- Machinery Parts
- LED Heatsink
- Building Parts
- Mobile Parts
- Medical Parts
- Electronic Parts
- Tailored Machining
- Bicycle Parts
- Aluminum Machining
- Titanium Machining
- Stainless Steel Machining
- Copper Machining
- Brass Machining
- Super Alloy Machining
- Peek Machining
- UHMW Machining
- Unilate Machining
- PA6 Machining
- PPS Machining
- Teflon Machining
- Inconel Machining
- Tool Steel Machining
- More Material