Program Features of CNC Turning Process and Optimization
Program Features of CNC Turning Process and Optimization
The characteristics of CNC turning processing technology are mainly discussed from the aspects of determining the positioning datum of parts processing, the requirements of CNC machining on the blank, the experience of process division, the selection of cutting tools and cutting parameters. For ease of understanding, examples are given in connection with actual processing in all aspects. In addition, it focuses on the optimization methods of numerical control programs, including the use of cycle programs, avoiding dry running of tool paths in the machining process, and applying subroutines. The differences between before and after optimization are compared through examples, showing the superiority of reasonable programs. Combining the actual processing experience on site, it provides a method to eliminate the tool marks and remove the thread burr during processing, and gives the processing procedure. |
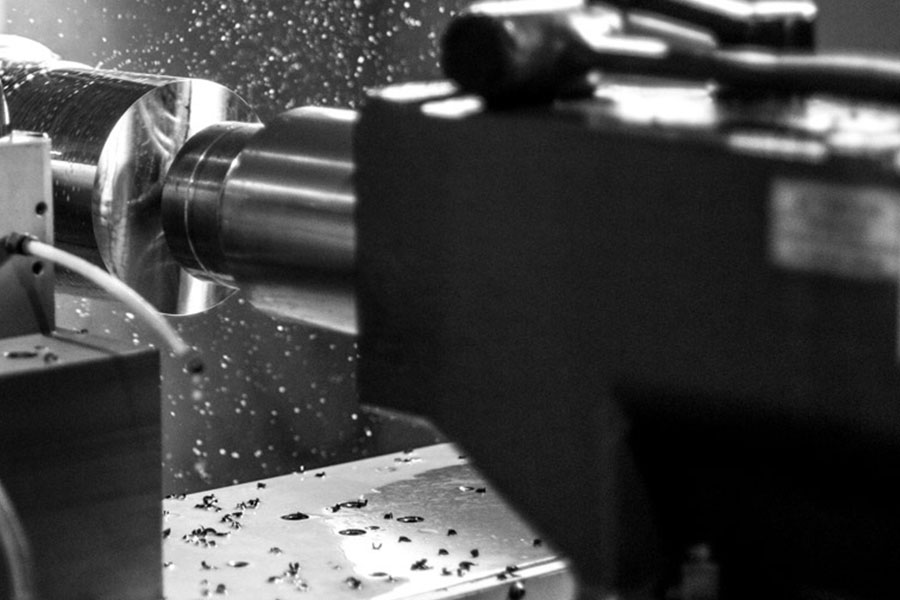
At present, the application of CNC cutting technology has entered a period of unprecedented rapid development and is moving towards high speed and efficiency. How to improve the processing efficiency of CNC machine tools has become a new topic before us. Understand the characteristics of CNC machining, determine a reasonable CNC machining process, and select
Choosing high-efficiency tools and preparing reasonable programs is the key to improving machining efficiency.
1.Features of CNC machining process
There are similarities and differences between the parts processed by CNC machine tools and the parts processed by ordinary machine tools. CNC machine tools are processed in strict accordance with the processing procedures
- The workpieces processed are usually more complicated than those processed by ordinary machine tools. Before the CNC machine tool is processed, the motion process of the machine tool, the process of the part, the shape of the tool, the cutting amount and the tool path must be programmed into the program, so the processing plan must be correctly determined before programming
- According to practical experience, the CNC machining process has the following characteristics.
1) There is an exact positioning datum.
During batch processing, in order to improve the processing efficiency, generally after the program is compiled and the first piece trial cut is completed, the program zero point is no longer changed. Therefore, it is required that the position of each part clamped on the machine tool must be determined by the machine tool. The default is the same as the first article position. Therefore, each part must have the same and exact positioning datum on the machine tool [3].For example: for turning short bar parts, this datum is generally on the end face of the chuck or on the steps of the three jaws; for turning slender parts (part of which needs to be clamped in the spindle hole during processing), this datum Generally, it is guaranteed by a step sleeve (see Figure 1); for special parts, it is necessary to find a specific way to clamp according to the shape of the part. In short, it is necessary to ensure that the coordinate of the Z axis of the part on the machine tool is constant during clamping.
2) There are certain requirements for the blank.
According to the characteristics of CNC machining and positioning, CNC machining also has certain requirements on the shape and size of the blank[4]. The margin of each part of the blank should be as consistent as possible, and it is best to keep the deviation within 2mm. In this way, in the CNC machining, not only the number of unnecessary empty passes can be reduced, and the machining efficiency can be improved, but also accidents such as hitting and crashing can be avoided.
3) Divide the process according to the tool.
In addition to following the general process principles, the CNC machining process should also be considered to give full play to the functions of the CNC machine tool used, and the process should be concentrated as much as possible. All processes should be completed as much as possible in one clamping. Because CNC tools play a pivotal role in CNC machining and are the key to high efficiency of CNC machine tools, processes are often divided according to the tools used. For processing the part shown, a total of 5 tools are required, namely, offset cutter, external groove cutter, face groove cutter, external thread cutter and drill bit. When machining, first use the offset cutter to set 111, thread outer diameter 100 and end face The steps (guaranteed size 18) are all processed, and then the tool is changed. This can reduce the number of tool changes, shorten the idle time, improve processing efficiency, and reduce unnecessary positioning errors.
4) The choice of tools and cutting parameters is very important.
The high efficiency of CNC machine tools depends to a large extent on the tool Only by choosing the right tool can the performance of the CNC machine tool be fully utilized. Nowadays, there are many types of domestic and imported CNC tools. Large tool companies generally indicate the blade brand, suitable materials and cutting parameters on the blade box. First of all, according to the processed parts;Select the type of blade based on the material and processing parts (such as outer circle, thread and face groove, etc.), and then select the specific blade according to rough and finish machining. After the insert is determined, the corresponding cutting parameters can be determined. For example: machining the outer circle of aluminum, the selected insert grade is CCGT120404FN -27, and its cutting parameters a = 1.0 ~ 10.0 mm, f = 0.1 ~ 0.75 mm, v = 100 ~ 300 m / min, then The machine speed n can be obtained from the formula n = 1 0000 v/d. The cutting parameters provided by the tool vendor are a range, from which to select a parameter that is most suitable for use, you also need to;According to the actual machining conditions, the best parameters can only be obtained from practice, so they must be determined through actual cutting tests.
2.Optimization of NC program
When machining parts on ordinary machine tools, the machining process is usually written on the machining process card. The operator processes the parts according to the "program" specified in the process card. The cutting parameters and tool paths are determined by the operator based on experience and regulations. However, when machining parts on a CNC machine tool, all the process and process parameters of the parts to be machined must be programmed in the form of codes and input into the machine tool to realize the machining of the parts. Therefore, the work of programming is very important. If the programming is reasonable, not only high-quality parts can be processed, but also the processing efficiency can be improved.
1) Adopt cycle program
Cycle programs are widely used in the programming of flat end faces, turning outer circles, drilling and boring, etc., which greatly simplifies the program structure, reduces the programming workload, and improves the processing efficiency.
2) Avoid dry running of tool path during machining.
The use of a cycle program in programming can certainly simplify the program, but it is not always good to use it. When the shape of the part has steps and the machining allowance is uneven, in order to avoid idling, the cycle program is generally not used [8]. The shape of the blank has been rough turned, and the 2 steps have a large axial margin. If the cycle program is used, a lot of empty passes will be generated; if the cycle program is not used, the two step faces with a large margin can be turned first according to the incoming material, and then the shape of the car will avoid empty passes and improve the processing efficiency. .
3) Application subroutine.
The application of subroutines in the program can simplify the main program [9], reduce programming workload and improve processing efficiency. Parts of the same series of length and diameter can share a subroutine. For the bottom surface of the inner hole of the part, the following subroutine can be used. The symbol of calling subroutine in the main program is M98PX0YYY, X is the number of subroutine calls, and 0YYY is the subroutine number.
- G0W -2.
- G1X0. F0.1
- G0X114. W2.
- G0W -2.
- G〇M99
4) The programming method to eliminate the tool marks.
When compiling a CNC program, you can use the programming method of the tool to take a long slash to eliminate the tool mark. In addition to the above optimization program method, there are some other programming skills, such as the application of a delay program, before a tool number Adding the program number can call the required tool at any time without being affected by the tool number in the program.
5) Deburring the thread.
The thread burr is removed by hand polishing with sandpaper on the general lathe, and the grooving knife can be used to automatically remove the burr through a program on the CNC lathe.
3.Conclusion
To sum up, there are many differences between CNC machining and ordinary machine tool machining. It has its own characteristics of processing technology, and there are many particularities and shortcuts in programming. Only by fully mastering and using them, can we really give full play to the high efficiency of CNC machine tools and make them better serve us.
Link to this article: Program Features of CNC Turning Process and Optimization
Reprint Statement: If there are no special instructions, all articles on this site are original. Please indicate the source for reprinting:https://www.cncmachiningptj.com/,thanks!
PTJ® provides a full range of Custom Precision cnc machining china services.ISO 9001:2015 &AS-9100 certified. 3, 4 and 5-axis rapid precision CNC machining services including milling, turning to customer specifications,Capable of metal & plastic machined parts with +/-0.005 mm tolerance.Secondary services include CNC and conventional grinding, drilling,die casting,sheet metal and stamping.Providing prototypes, full production runs, technical support and full inspection.Serves the automotive, aerospace, mold&fixture,led lighting,medical,bicycle, and consumer electronics industries. On-time delivery.Tell us a little about your project’s budget and expected delivery time. We will strategize with you to provide the most cost-effective services to help you reach your target,Welcome to Contact us ( sales@pintejin.com ) directly for your new project.
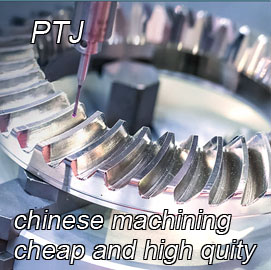
- 5 Axis Machining
- Cnc Milling
- Cnc Turning
- Machining Industries
- Machining Process
- Surface Treatment
- Metal Machining
- Plastic Machining
- Powder Metallurgy Mold
- Die Casting
- Parts Gallery
- Auto Metal Parts
- Machinery Parts
- LED Heatsink
- Building Parts
- Mobile Parts
- Medical Parts
- Electronic Parts
- Tailored Machining
- Bicycle Parts
- Aluminum Machining
- Titanium Machining
- Stainless Steel Machining
- Copper Machining
- Brass Machining
- Super Alloy Machining
- Peek Machining
- UHMW Machining
- Unilate Machining
- PA6 Machining
- PPS Machining
- Teflon Machining
- Inconel Machining
- Tool Steel Machining
- More Material