Titanium Alloy Material Grinding Skills
Titanium Alloy Material Grinding Skills
The machining of TC4 titanium alloy is very difficult. The comprehensive process of titanium and titanium alloy is very different from steel, aluminum alloy and many heavy metals in terms of crystal structure, physical properties and chemical properties. Alloy is a metal that is not easy to process. |
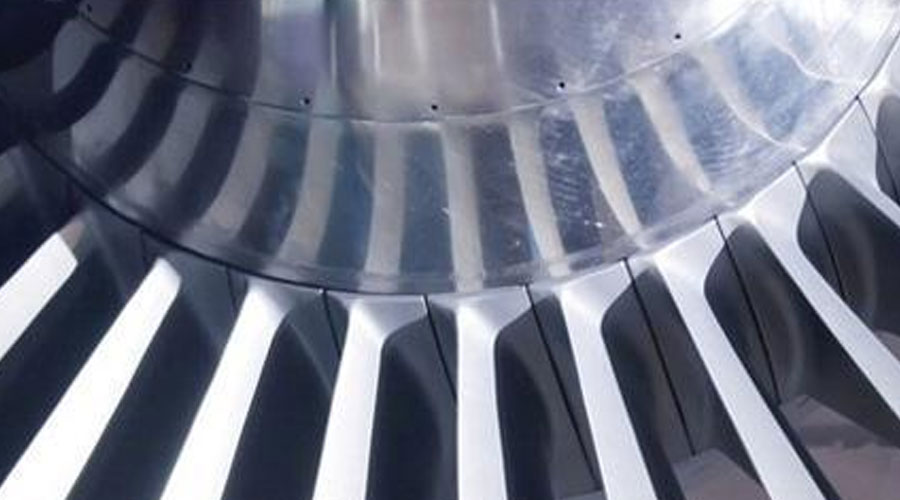
- (1) Due to the instability of its chemical composition. TC4 titanium alloy will undergo chemical reaction with oxygen and nitrogen under thermal deformation, and even with some oxygen-containing gas, the reaction will produce oxide scale attached to the workpiece surface, if the temperature is higher, reach 900 ℃ At the above time, scales attached to the surface of the workpiece will produce scales, so that oxygen and nitrogen elements are likely to penetrate into the metal and eventually form a surface getter layer. Higher hardness and lower plasticity are the characteristics of this getter layer.
- (2) The performance of cementite in the metallographic structure belongs to a complex Fe-C compound, and the Vickers hardness can be as high as HV1100, but the impact toughness is almost no.
- (3) The thermal conductivity is not high: if the thermal conductivity of titanium alloy is compared with other alloys such as aluminum alloy, it is only about 1/15 of that of aluminum alloy and about 1/5 of that of steel. Compared with aluminum alloy and steel, the thermal conductivity and thermal conductivity of titanium alloy are much lower, only about 1/15 of aluminum alloy, and about 2/7 of steel. The effect on the surface machining quality of some titanium alloy parts is Relatively large.
The main problems encountered in titanium alloy grinding
- (1) The bonding problem of the grinding wheel is serious. The titanium alloy adheres to the surface of the grinding wheel, and the bonding surface layer is like smoke. The main reason is that the adhesion material falls off during the grinding process. This will cause the abrasive particles to fall off along with the fracture, which will eventually seriously damage the grinding wheel.
- (2) The grinding force is larger and the grinding temperature is higher. During the grinding test of single abrasive particles, it was found that when grinding titanium alloys, the larger proportion is the sliding process, and the contact time of the abrasive particles and the workpiece is very short, during which very intense friction and The violent elastic and plastic deformation, then the titanium alloy is ground away into chips, which generates a lot of grinding heat, at this time the grinding temperature can reach up to almost 1500 ℃.
- (3) Grinding will produce layered squeeze chips, the main reason is the complex deformation. The band-shaped chips are mostly formed when white corundum grinding wheel (WA60KV) is used to grind 45 steel, and the layer-shaped crushed chips are formed when green silicon carbide grinding wheel (GC46KV) is used to grind titanium alloy.
- (4) Under high temperature conditions, the chemical activity of the machining TC4 titanium alloy is quite active, and it is easy to combine with oxygen, nitrogen, hydrogen and other elements in the air to form a violent reaction to form brittle and hard such as titanium dioxide, titanium nitride, titanium hydride Metamorphic layer, which leads to a decrease in the plasticity of TC4.
- (5) During the grinding process of titanium alloys, it is affected by difficult problems, mainly because the grinding heat transferred into the workpiece is difficult to be exported, and the workpiece is easily deformed, burned, and even some cracks appear. Therefore, the surface of the workpiece There will be varying degrees of roughness.
Solution
Suppression measures to solve grinding burns and cracks
There are some problems when machining TC4 titanium alloy with grinding wheels. The more serious problem is adhesion. Due to the high speed, the grinding force and temperature are relatively high, which will burn the surface and produce cracks. Ren Jingxin and others have done some experimental research to reduce such burns and cracks during machining. They feel that softer grinding wheels can be used, such as instead of corundum grinding wheels, instead of silicon carbide or cerium silicon carbide grinding wheels, corundum grinding wheels Resin adhesion, while the former uses ceramic adhesion. Also pay attention to the advance cnc machining parameters, for example, the speed of the grinding wheel should not be too fast, the experimental analysis should not exceed 20 meters per second, the grinding depth should not be too much, and should not exceed 0.02 millimeters. Within every minute, the grinding fluid must not only dissipate heat very well, but also emphasize its lubrication effect, which can effectively suppress the occurrence of sticking phenomenon. If it is dry grinding, the lubricant can be impregnated with solid lubricant Impregnated grinding wheel.
Grinding wheel bonding phenomenon in titanium alloy grinding and its restraining measures
Because in the grinding process of titanium alloy, there will generally be a higher grinding temperature and a larger normal force, so that severe plastic deformation will occur in the titanium alloy in the grinding zone, between the abrasive and the metal The adsorption effect caused by chemical or chemical adsorption; the reason for the transfer of the ground metal to the abrasive particles is the influence of the shear force, which leads to the bonding of the grinding wheel. Finally, the abrasive particles break, and when the grinding force exceeds the binding force between the abrasive particles, the abrasive particles and the bond will peel off from the grinding wheel.
High-speed and efficient grinding
Some scholars carried out high-speed and efficient grinding of TC4 titanium alloy materials. In the study, the rule that the grinding force per unit area and specific grinding energy are affected by the amount of grinding is analyzed. If the linear velocity vs. of the grinding wheel increases, the grinding force per unit area decreases significantly. However, when the table speed vw and the grinding depth ap increase, the grinding force per unit area increases. If the linear velocity vs. of the grinding wheel increases, the specific grinding energy will increase, but if the table speed vw and the grinding depth ap increase, the specific grinding energy will decrease.
Link to this article: Titanium Alloy Material Grinding Skills
Reprint Statement: If there are no special instructions, all articles on this site are original. Please indicate the source for reprinting:https://www.cncmachiningptj.com/,thanks!
PTJ CNC shop produces parts with excellent mechanical properties, accuracy and repeatability from metal and plastic. 5 axis CNC milling available.Machining high-temperature alloy range inclouding inconel machining,monel machining,Geek Ascology machining,Carp 49 machining,Hastelloy machining,Nitronic-60 machining,Hymu 80 machining,Tool Steel machining,etc.,. Ideal for aerospace applications.CNC machining produces parts with excellent mechanical properties, accuracy and repeatability from metal and plastic. 3-axis & 5-axis CNC milling available.We will strategize with you to provide the most cost-effective services to help you reach your target,Welcome to Contact us ( sales@pintejin.com ) directly for your new project.
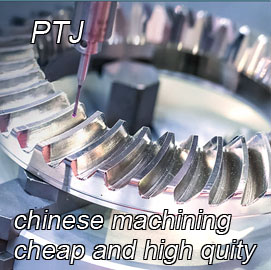
- 5 Axis Machining
- Cnc Milling
- Cnc Turning
- Machining Industries
- Machining Process
- Surface Treatment
- Metal Machining
- Plastic Machining
- Powder Metallurgy Mold
- Die Casting
- Parts Gallery
- Auto Metal Parts
- Machinery Parts
- LED Heatsink
- Building Parts
- Mobile Parts
- Medical Parts
- Electronic Parts
- Tailored Machining
- Bicycle Parts
- Aluminum Machining
- Titanium Machining
- Stainless Steel Machining
- Copper Machining
- Brass Machining
- Super Alloy Machining
- Peek Machining
- UHMW Machining
- Unilate Machining
- PA6 Machining
- PPS Machining
- Teflon Machining
- Inconel Machining
- Tool Steel Machining
- More Material