How Engineers Design Parts That Require Heat Treatment?
How Engineers Design Parts That Require Heat Treatment?
As a mechanical design engineer, when designing parts that require heat treatment, it is necessary to eliminate the casting stress of the material and improve the cutting performance, rigidity and wear resistance of the part. The heat treatment requirements for most parts are designed around the above three major aspects. Below we will introduce in detail the method for engineers to design parts that require heat treatment. |
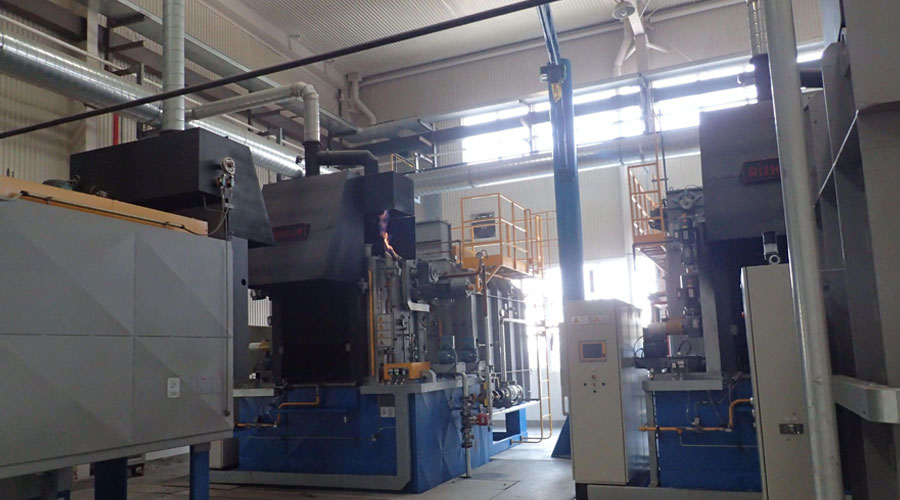
1.Annealing
After getting the casting blank, the first thing we need to do is annealing. The purpose of annealing is to eliminate the residual internal stress of the casting and improve the cutting performance of the part. Of course, some manufacturers do not perform annealing here. In order to save costs, they often extend the cooling time of the casting to remove part of the internal stress. This is also considered as A speculative way, but according to the regular method, the rough parts after casting must be annealed.
2. Enter The Rough Machining Process Of The Part
The rough machining process of the part does not have too strict requirements on the size of the part, so the factory uses large-volume cutting. During the large-volume cutting, the impact of the milling cutter on the part is used to form a certain degree of vibration treatment. A process of releasing stress, but this is also a process of generating stress again, subjecting the part to secondary annealing.
3.Second Annealing Treatment
Its purpose is also to stabilize the material structure, improve the cutting performance, and remove the internal stress of the part, because we need to ensure that the size and shape tolerances of the part after machining are stable, not constantly changing with time. In the actual process In the process, the dimensional accuracy and shape and position tolerances of the processed parts do change. This is one of the reasons why our country's high-precision machine tools are always poor, and even one of the most important reasons. The stability is too poor.
4.Semi-finished Parts
Because the semi-finish machining of the part is already a machining process with a small amount of cutting, the machining process usually does not generate excessive machining stress, but if the dimensional accuracy of the part is high and the form and position tolerances are strict, we are still strongly It is recommended to finish the part after leaving it for a period of time, so that the part can release part of the stress in a natural state to ensure that the final finished product is stable. Many people have not considered this process, and arrange the parts machining technology in a loop-by-loop manner. It looks very efficient, but in fact, the quality is not well guaranteed.
5. Parts Finishing Process
After being placed for a period of time, the material of the part has become relatively stable, and it appears to test the level of an operator in the finishing stage. In many cases, the precision of finishing does not simply come from the accuracy of the cnc machining machine, it may come from Your clamping method, especially for parts that are not very strong and rigid, pay special attention when clamping, do not use dead force to compress the workpiece. Once the workpiece has deformed, you will loosen it after machining the workpiece. When clamped, the workpiece will spring back to its original state immediately, and the machining accuracy will change at this time. Therefore, the clamping force is particularly important in the finishing process.
Link to this article: How Engineers Design Parts That Require Heat Treatment?
Reprint Statement: If there are no special instructions, all articles on this site are original. Please indicate the source for reprinting:https://www.cncmachiningptj.com/,thanks!
PTJ® provides a full range of Custom Precision cnc machining china services.ISO 9001:2015 &AS-9100 certified. 3, 4 and 5-axis rapid precision CNC machining services including milling, turning to customer specifications,Capable of metal & plastic machined parts with +/-0.005 mm tolerance.Secondary services include CNC and conventional grinding, drilling,die casting,sheet metal and stamping.Providing prototypes, full production runs, technical support and full inspection.Serves the automotive, aerospace, mold&fixture,led lighting,medical,bicycle, and consumer electronics industries. On-time delivery.Tell us a little about your project’s budget and expected delivery time. We will strategize with you to provide the most cost-effective services to help you reach your target,Welcome to Contact us ( sales@pintejin.com ) directly for your new project.
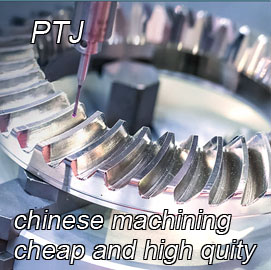
- 5 Axis Machining
- Cnc Milling
- Cnc Turning
- Machining Industries
- Machining Process
- Surface Treatment
- Metal Machining
- Plastic Machining
- Powder Metallurgy Mold
- Die Casting
- Parts Gallery
- Auto Metal Parts
- Machinery Parts
- LED Heatsink
- Building Parts
- Mobile Parts
- Medical Parts
- Electronic Parts
- Tailored Machining
- Bicycle Parts
- Aluminum Machining
- Titanium Machining
- Stainless Steel Machining
- Copper Machining
- Brass Machining
- Super Alloy Machining
- Peek Machining
- UHMW Machining
- Unilate Machining
- PA6 Machining
- PPS Machining
- Teflon Machining
- Inconel Machining
- Tool Steel Machining
- More Material