Difference Between Cylindrical Milling Cutter And End Milling Cutter
Difference Between Cylindrical Milling Cutter And End Milling Cutter
Milling cutters are rotary tools with one or more teeth for milling. We are more commonly used to process planes on horizontal milling machines, 45-degree chamfered milling cutters, and the cutter teeth are distributed on the circumference of the milling cutter is a cylindrical milling cutter. Cylindrical milling cutters are divided into straight teeth and helical teeth according to tooth shape, and coarse teeth and fine teeth according to the number of teeth. |
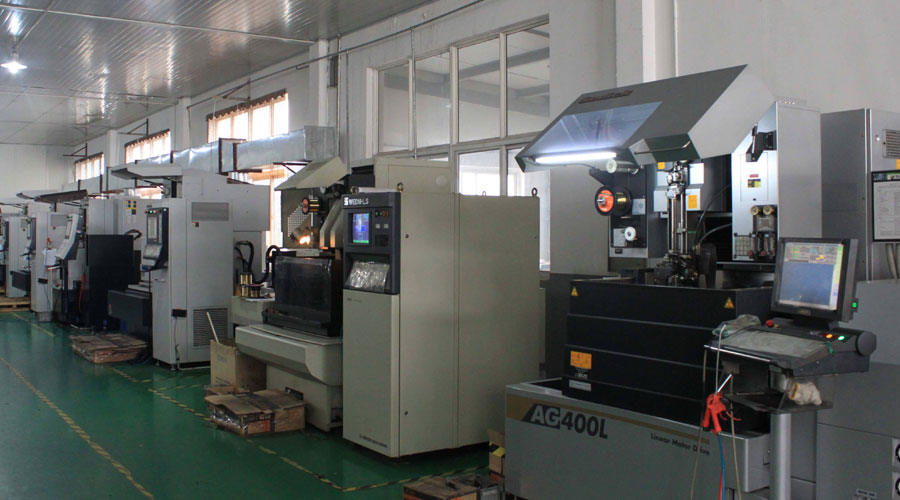
The helical-tooth coarse-tooth milling cutter has few teeth, high tooth strength, large chip space, and is suitable for rough machining. The fine-tooth milling cutter is suitable for finishing. Multiple milling cutters can be combined for wide-plane milling, and the left and right staggered spiral teeth must be combined.
Cylindrical milling cutters have high productivity. Milling cutters rotate continuously during milling and allow higher milling speeds, so they have higher productivity. During continuous cutting and milling, each tooth is continuously cutting, especially in end milling. The milling force fluctuates greatly, so vibration is unavoidable. When the frequency of the vibration is the same or multiple of the natural frequency of the machine tool, the vibration is the most serious.
In addition, when high-speed cnc milling, the cutter teeth have to undergo periodic cold and hot impact, which is prone to cracks and chipping, which reduces the durability of the tool. Multi-tool multi-edge cutting milling cutters have many teeth and a large total cutting edge length, which is conducive to improving the durability and productivity of the tool, and has many advantages.
However, there are two problems in the following: one is that the cutter teeth are prone to radial runout, which will cause the cutter teeth to have unequal load and uneven wear, affecting the quality of the processed surface; the second is that the chip clearance space of the cutter teeth must be sufficient Otherwise it will damage the cutter teeth. Different milling methods According to different machining conditions, in order to improve the durability and productivity of the tool, you can choose different milling methods, such as upside down milling, down milling or symmetrical milling, asymmetric milling, etc.
In addition to cylindrical milling cutters, end milling cutters are also more commonly used. So, what is the difference between a cylindrical milling cutter and an end milling cutter? The most direct difference is that the cylindrical milling cutter is worn on the tool holder, and the end mill can be used by directly inserting it into the taper hole of the spindle. End mills are used to process grooves and stepped surfaces. The teeth are on the circumference and the end surface. Generally, the feed cannot be axially fed. When the end mill has teeth passing through the center end, it can feed axially.
In addition, the use range and requirements of high-speed steel end mills are relatively wide, and even if the choice of cutting conditions is slightly inappropriate, there will not be too many problems. Although hard alloy end mills have good wear resistance during high-speed cutting, they are not as widely used as high-speed steel end mills, and the cutting conditions must strictly meet the requirements of the tool.
Link to this article: Difference Between Cylindrical Milling Cutter And End Milling Cutter
Reprint Statement: If there are no special instructions, all articles on this site are original. Please indicate the source for reprinting:https://www.cncmachiningptj.com/,thanks!
PTJ® provides a full range of Custom Precision cnc machining china services.ISO 9001:2015 &AS-9100 certified. 3, 4 and 5-axis rapid precision CNC machining services including milling, turning to customer specifications,Capable of metal & plastic machined parts with +/-0.005 mm tolerance.Secondary services include CNC and conventional grinding, drilling,die casting,sheet metal and stamping.Providing prototypes, full production runs, technical support and full inspection.Serves the automotive, aerospace, mold&fixture,led lighting,medical,bicycle, and consumer electronics industries. On-time delivery.Tell us a little about your project’s budget and expected delivery time. We will strategize with you to provide the most cost-effective services to help you reach your target,Welcome to Contact us ( sales@pintejin.com ) directly for your new project.
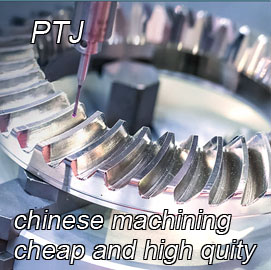
- 5 Axis Machining
- Cnc Milling
- Cnc Turning
- Machining Industries
- Machining Process
- Surface Treatment
- Metal Machining
- Plastic Machining
- Powder Metallurgy Mold
- Die Casting
- Parts Gallery
- Auto Metal Parts
- Machinery Parts
- LED Heatsink
- Building Parts
- Mobile Parts
- Medical Parts
- Electronic Parts
- Tailored Machining
- Bicycle Parts
- Aluminum Machining
- Titanium Machining
- Stainless Steel Machining
- Copper Machining
- Brass Machining
- Super Alloy Machining
- Peek Machining
- UHMW Machining
- Unilate Machining
- PA6 Machining
- PPS Machining
- Teflon Machining
- Inconel Machining
- Tool Steel Machining
- More Material