Predicting Hard Oxidation Processes
Predicting Hard Oxidation Processes
The remaining size of the part is due to the thickness of the hard oxide film. Therefore, if aluminum parts need to be further processed or parts that need to be assembled later, a certain machining allowance should be left in advance, and the specified clamping location should be reserved. |
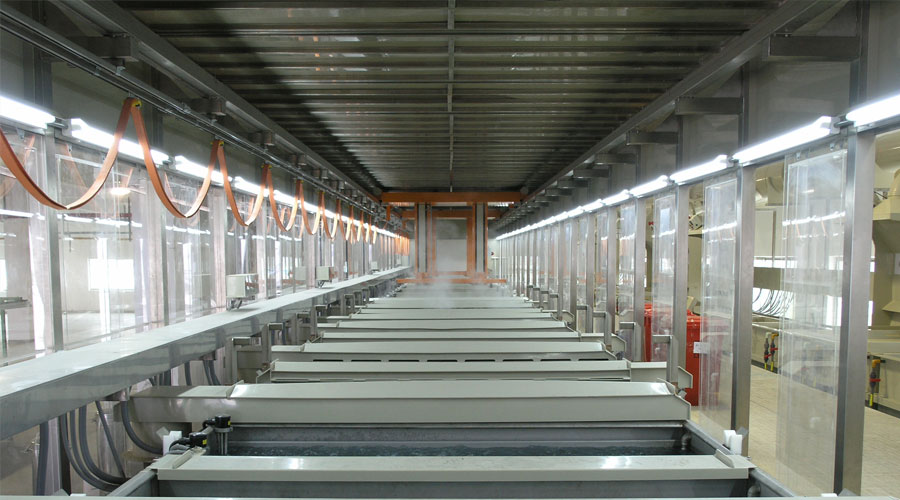
The maximum thickness of the obtained anodized film can reach about 250 microns, and a micro-hardness oxide film of 1500 kg / mm2 can be obtained on pure aluminum, while a micro-hardness oxide film of 400-600 kg / mm2 can be obtained on aluminum alloy. . Since the oxide film layer formed by hard anodization has a high resistance, it will directly affect the oxidation of the current intensity. In order to obtain a thicker oxide film, it is necessary to increase the external voltage.
The purpose is to eliminate the effect of large resistance and keep the current density constant. However, when the current is large, intense heating will occur. A large amount of heat is emitted, which causes the temperature of the electrolyte around the part to rise sharply. The temperature rise will accelerate the dissolution of the oxide film and prevent the oxide film from becoming thick.
- A. Special fixtures Design and manufacture special fixtures for parts of different shapes and the specific requirements of the parts after oxidation. During the oxidation process, hard anodized parts must withstand high voltage and high current. Make sure that the fixture and parts can maintain excellent contact. Otherwise, breakdown or burned parts will be caused by poor contact. Part of the problem.
- B. Since the size of the part is changed during hard anodizing, the possible thickness and dimensional tolerance of the oxide film must be predicted in advance during mechanical processing, and then the actual size of the part before anodizing is determined so that it can meet the requirements after processing Tolerance range. Generally, the size of the part is increased by about half of the thickness of the oxide film. Part size allowance Due to the high thickness of the hard oxide film, if aluminum parts need to be further processed or parts that need to be assembled later, a certain machining allowance must be left in advance, and the specified clamping location must be reserved.
- C. The surface finish after this treatment can appear flatter than the original, and for parts with higher original finish, often after this treatment, the surface finish of the part is changed after hard anodizing. For rougher surfaces, the displayed surface is smoother and brighter, with a decrease of about 1 to 2 levels. E. Sharp rounding All edges of aluminum and aluminum alloys should be chamfered, and the radius of the chamfer y circle should not be less than 0.5 mm. The processed parts are not allowed to have sharp angles, burrs, and other sharp edges and corners. Because of hard oxidation, the anodizing time is generally long, and the oxidation (A1 + O2 → A12O3 + Q) is an exotherm in itself reaction.
And because the edges and corners of general parts are often the parts where the current is concentrated, these parts are the most likely to cause local overheating of the parts and burn the parts. Generally speaking, if the temperature decreases, the wear resistance of the anodic oxide film of aluminum and aluminum alloy will increase, which is caused by the decrease in the dissolution rate of the electrolyte to the film, in order to obtain a higher hardness oxide film.
We have to master the hard anodizing treatment in the temperature range of ± 2 ℃. The effect of temperature on the film layer The electrolyte temperature has a great effect on the wear resistance of the oxide film.
Link to this article: Predicting Hard Oxidation Processes
Reprint Statement: If there are no special instructions, all articles on this site are original. Please indicate the source for reprinting:https://www.cncmachiningptj.com/,thanks!
PTJ® provides a full range of Custom Precision cnc machining china services.ISO 9001:2015 &AS-9100 certified. 3, 4 and 5-axis rapid precision CNC machining services including milling, turning to customer specifications,Capable of metal & plastic machined parts with +/-0.005 mm tolerance.Secondary services include CNC and conventional grinding, drilling,die casting,sheet metal and stamping.Providing prototypes, full production runs, technical support and full inspection.Serves the automotive, aerospace, mold&fixture,led lighting,medical,bicycle, and consumer electronics industries. On-time delivery.Tell us a little about your project’s budget and expected delivery time. We will strategize with you to provide the most cost-effective services to help you reach your target,Welcome to Contact us ( sales@pintejin.com ) directly for your new project.
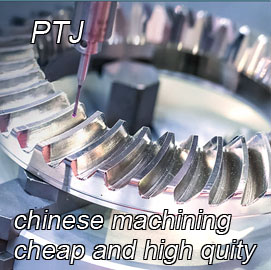
- 5 Axis Machining
- Cnc Milling
- Cnc Turning
- Machining Industries
- Machining Process
- Surface Treatment
- Metal Machining
- Plastic Machining
- Powder Metallurgy Mold
- Die Casting
- Parts Gallery
- Auto Metal Parts
- Machinery Parts
- LED Heatsink
- Building Parts
- Mobile Parts
- Medical Parts
- Electronic Parts
- Tailored Machining
- Bicycle Parts
- Aluminum Machining
- Titanium Machining
- Stainless Steel Machining
- Copper Machining
- Brass Machining
- Super Alloy Machining
- Peek Machining
- UHMW Machining
- Unilate Machining
- PA6 Machining
- PPS Machining
- Teflon Machining
- Inconel Machining
- Tool Steel Machining
- More Material