Application Of Laser Machining In Machinery Manufacturing
Application Of Laser Machining In Machinery Manufacturing
The core of laser processing technology is the interaction between the laser beam and the material. It is divided into laser thermal processing and photochemical reaction machining according to different machining methods. The former uses the thermal effect generated by the laser beam to perform processing operations, and the latter uses high density. High-energy photons initiate chemical reactions to complete processing. With the improvement of laser application technology, laser processing has become the main application technology of laser systems. It is widely used in the field of machinery manufacturing and plays an important role. |
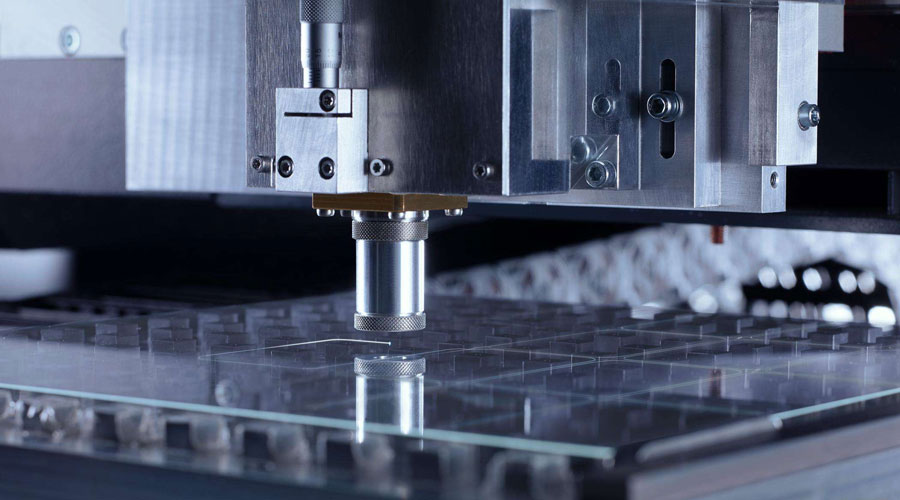
1.Characteristics of laser machining technology
Laser cutting is a modern technology that integrates intelligence and advancement, and integrates laser principles, CAD technology and numerical control technology. The principle of laser machining technology is to play a physical role on the surface of the material by virtue of the high energy density performance of the laser beam, and cause a series of morphological changes on the surface of the material.
Laser machining technology has the advantages of high accuracy and no pollution, which is unmatched and surpassed by other manufacturing machining technologies. In addition, laser machining technology also integrates a variety of disciplines such as electronics, materials, and engineering heat transfer, with a higher level of intelligence.
Compared with other machining technologies in mechanical manufacturing, laser machining wastes less material, has greater efficiency in large-scale production, and is more adaptable to processed materials.
It can be used for mechanical manufacturing of a variety of special materials, and for other traditional machining New materials that cannot be reached by technology are also processed using laser machining technology. The main features of laser machining technology in machinery manufacturing:
- (1) High power, the material can be melted or vaporized in a short period of time after absorbing the laser heat, and the material can be quickly changed even if the melting point of the material is high.
- (2) The laser head will not be in direct contact with the workpiece, so there will be no wear problems.
- (3) Not only machining operations on static workpieces, but also workpieces in motion, even if the material is sealed in other objects.
- (4) During the laser machining, the laser beam is controlled by the electronic computer, which can realize the precision machining of the machine, and the degree of automation is high.
- (5) Laser machining can realize mechanized control, and robots can be used instead of machining in environments where human operation is difficult.
2.Application of laser machining in machinery manufacturing
2.1 Material handling
Laser machining generally uses heat treatment and surface strengthening technology to process the material. These two technologies can quickly heat up the surface of the material and rapidly change its morphology when it approaches the melting point, thereby achieving the purpose of surface treatment. Laser machining technology is an extension of traditional heat treatment technology. After laser machining, the material has stronger fatigue resistance and corrosion resistance.
The service life has also been extended, and all aspects of the material's performance have been improved. The application of laser machining to the surface of workpieces has greatly improved the physical properties of materials, which is of great significance for improving the market competitiveness of products.
Laser technology can be used alone or combined with other technologies to create a new material machining mode. The combination of laser technology and CAD technology has opened a new field of mechanical manufacturing material machining. CAD technology uses a computer system to control the design process, complete the part modeling design work, and then use laser technology to process according to the designed modeling plan. The part model created with CAD technology has the characteristics of accuracy and directness, which can simplify the difficulty of manufacturing complex parts.
If problems occur during the design process, they can be modified at any time to ensure the integrity of the product. Mechanical manufacturing has extremely strict requirements on the parts themselves, and the requirements for precision are very strict. The machining of some complex curved surfaces is also difficult. The combined use of CAD technology and laser technology can easily solve this problem, reduce production difficulty, and also shorten R & D cycle to improve product production efficiency.
Punching and stamping is an important part of material machining. Common types of machining holes include oil holes, fastening holes, positioning holes, etc. Through-hole quality has a significant impact on part performance. The drilling effect of laser machining is better than that of traditional mechanical drilling, and the hole wall is smoother and rounder, as shown in Table 1. The curve of hole depth and hole diameter over time under laser machining is shown in Figure 1.
It can be seen that during the laser drilling process, the hole depth and hole diameter have increased significantly in the initial stage, and with the extension of time, The increase rate of all of them is slowed down. The reason for the slowdown is that the laser defocusing energy is reduced, and then the laser heat source is turned to the inside of the material. At this time, the laser proce
Link to this article: Application Of Laser Machining In Machinery Manufacturing
Reprint Statement: If there are no special instructions, all articles on this site are original. Please indicate the source for reprinting:https://www.cncmachiningptj.com/,thanks!
PTJ® provides a full range of Custom Precision cnc machining china services.ISO 9001:2015 &AS-9100 certified. 3, 4 and 5-axis rapid precision CNC machining services including milling, turning to customer specifications,Capable of metal & plastic machined parts with +/-0.005 mm tolerance.Secondary services include CNC and conventional grinding, drilling,die casting,sheet metal and stamping.Providing prototypes, full production runs, technical support and full inspection.Serves the automotive, aerospace, mold&fixture,led lighting,medical,bicycle, and consumer electronics industries. On-time delivery.Tell us a little about your project’s budget and expected delivery time. We will strategize with you to provide the most cost-effective services to help you reach your target,Welcome to Contact us ( sales@pintejin.com ) directly for your new project.
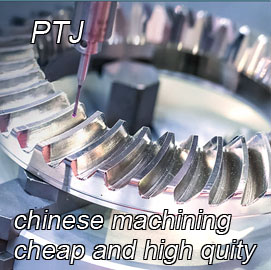
- 5 Axis Machining
- Cnc Milling
- Cnc Turning
- Machining Industries
- Machining Process
- Surface Treatment
- Metal Machining
- Plastic Machining
- Powder Metallurgy Mold
- Die Casting
- Parts Gallery
- Auto Metal Parts
- Machinery Parts
- LED Heatsink
- Building Parts
- Mobile Parts
- Medical Parts
- Electronic Parts
- Tailored Machining
- Bicycle Parts
- Aluminum Machining
- Titanium Machining
- Stainless Steel Machining
- Copper Machining
- Brass Machining
- Super Alloy Machining
- Peek Machining
- UHMW Machining
- Unilate Machining
- PA6 Machining
- PPS Machining
- Teflon Machining
- Inconel Machining
- Tool Steel Machining
- More Material