Workpiece Reversing Mechanism in CNC Processing Machines
The workpiece reversing mechanism in Computer Numerical Control (CNC) processing machines represents a critical innovation in modern manufacturing, enabling enhanced precision, efficiency, and automation in the production of complex parts. CNC machining, a subtractive manufacturing process, relies on computer-controlled tools to remove material from a workpiece to achieve desired geometries. The ability to reverse or reposition the workpiece during machining operations is essential for accessing multiple sides of a part, reducing setup times, and improving overall productivity. This article provides a comprehensive exploration of workpiece reversing mechanisms, their types, applications, technical principles, historical development, and future trends, aiming to serve as an authoritative resource for engineers, researchers, and industry professionals.
Introduction to CNC Machining and Workpiece Manipulation
CNC machining encompasses a variety of processes, including milling, turning, drilling, and electrical discharge machining (EDM), all controlled by pre-programmed software that dictates tool and workpiece movements. The workpiece, often referred to as the blank or stock, is the raw material from which the final part is crafted. In traditional manual machining, operators manually repositioned workpieces to machine different surfaces, a process prone to errors and inefficiencies. The advent of CNC technology introduced automation, precision, and repeatability, but early CNC systems still required manual intervention for workpiece reorientation.
The workpiece reversing mechanism addresses this limitation by automating the process of flipping, rotating, or repositioning the workpiece within the CNC machine. These mechanisms are integral to multi-axis CNC systems, robotic workholding solutions, and advanced fixturing technologies. By enabling seamless access to multiple workpiece faces without manual intervention, reversing mechanisms enhance the capability to produce complex geometries, reduce setup times, and minimize human error, thereby improving throughput and part quality.
This article delves into the technical foundations of workpiece reversing mechanisms, their classifications, operational principles, and their role in various CNC machining processes. It also examines the challenges associated with their implementation, such as mechanical backlash, alignment precision, and compatibility with different machine types. Through detailed comparisons, historical context, and forward-looking insights, the article aims to provide a thorough understanding of this critical aspect of CNC technology.
Historical Context of Workpiece Manipulation in Machining
Early Machining and Manual Repositioning
The history of workpiece manipulation in machining predates CNC technology, tracing back to the Industrial Revolution when mechanized tools began replacing handcrafting. Early lathes and milling machines required operators to manually reposition workpieces to access different surfaces. For example, in a manual lathe, a cylindrical workpiece might need to be unclamped, flipped, and reclamped to machine its opposite end. This process was time-consuming, labor-intensive, and susceptible to misalignment, leading to dimensional inaccuracies.
The introduction of numerical control (NC) in the 1940s and 1950s marked a significant advancement. NC machines used punched tapes to control tool movements, reducing the need for constant operator intervention. However, workpiece repositioning remained largely manual, as early NC systems lacked the sophistication to automate complex fixturing or reorientation tasks. Operators still needed to stop the machine, adjust the workpiece, and recalibrate the setup, which disrupted workflow and limited productivity.
Emergence of CNC and Automated Workholding
The transition from NC to CNC in the 1960s, driven by the integration of digital computers, revolutionized machining. CNC systems allowed for more precise control of tool paths, spindle speeds, and feed rates, enabling the production of intricate parts with tight tolerances. Concurrently, advancements in workholding technology began to address the limitations of manual repositioning. Hydraulic and pneumatic chucks, vises, and fixtures improved the speed and reliability of securing workpieces, but the need for automated repositioning persisted.
The development of multi-axis CNC machines in the 1970s and 1980s introduced new possibilities for workpiece manipulation. Three-axis milling machines, which could move tools along the X, Y, and Z axes, were followed by four- and five-axis systems that added rotational axes (A and B). These additional axes allowed the tool or workpiece to rotate, reducing the need for manual repositioning. However, for parts requiring access to all six sides or complex internal features, fully automated reversing mechanisms became essential.
Evolution of Workpiece Reversing Mechanisms
By the 1990s, CNC manufacturers began integrating dedicated workpiece reversing mechanisms into their systems. These mechanisms ranged from simple rotary tables to sophisticated robotic arms and pallet changers. The rise of flexible manufacturing systems (FMS) further emphasized the importance of automation, as manufacturers sought to minimize downtime and maximize machine utilization. Workpiece reversing mechanisms became a cornerstone of FMS, enabling continuous production with minimal human intervention.
Today, workpiece reversing mechanisms are a standard feature in advanced CNC systems, particularly in industries such as aerospace, automotive, and medical device manufacturing, where precision and efficiency are paramount. The integration of sensors, feedback systems, and Industry 4.0 technologies has further enhanced the capabilities of these mechanisms, allowing for real-time monitoring, adaptive control, and predictive maintenance.
Technical Principles of Workpiece Reversing Mechanisms
Fundamental Concepts
A workpiece reversing mechanism is designed to reorient the workpiece within the CNC machine to expose different surfaces or features to the cutting tool. This reorientation can involve rotation, flipping, or translation, depending on the machine’s configuration and the part’s geometry. The mechanism must ensure precise alignment, secure clamping, and minimal disruption to the machining process.
The primary components of a workpiece reversing mechanism include:
-
Workholding Device: This secures the workpiece during machining and reorientation. Common workholding devices include chucks, vises, fixtures, and pallets.
-
Actuation System: This drives the movement of the workpiece, using motors, hydraulic or pneumatic actuators, or mechanical linkages.
-
Control System: This interfaces with the CNC controller to execute programmed reorientation commands, ensuring synchronization with tool movements.
-
Feedback System: This monitors the position and orientation of the workpiece, using sensors or encoders to detect deviations and ensure accuracy.
The operation of a reversing mechanism is governed by G-code and M-code, the programming languages used in CNC machining. G-code controls the movement of the tool and workpiece, while M-code manages auxiliary functions, such as activating the reversing mechanism or engaging a clamping device.
Kinematics of Workpiece Reorientation
The kinematics of workpiece reversing involve the coordinated movement of the workpiece along one or more axes. In a typical setup, the workpiece is mounted on a rotary table or fixture that can rotate around a specific axis (e.g., A-axis for rotation about the X-axis). For more complex reorientations, multi-axis systems may combine linear translations (X, Y, Z) with rotations (A, B, C).
The precision of these movements depends on the machine’s drive system, which typically includes servo motors, ball screws, and linear guides. Backlash, the mechanical play between components, can affect accuracy, particularly in operations requiring axis reversals (e.g., milling a circular feature). Modern CNC systems mitigate backlash through closed-loop control, where feedback from linear encoders or optical sensors corrects positional errors in real time.
Types of Workpiece Reversing Mechanisms
Workpiece reversing mechanisms can be classified based on their design, actuation method, and application. The following sections describe the main types, their operational principles, and their suitability for different CNC processes.
Rotary Tables
Rotary tables are among the most common workpiece reversing mechanisms, used primarily in milling and drilling operations. A rotary table is a precision platform that rotates the workpiece around a single axis, typically the A-axis (horizontal rotation) or C-axis (vertical rotation). The table is mounted on the machine’s worktable and driven by a servo motor or hydraulic actuator.
Key Features:
-
Degrees of Freedom: Single-axis rotation, with some models offering indexing for precise angular positioning.
-
Applications: Machining cylindrical parts, gears, and components requiring features on multiple radial surfaces.
-
Advantages: High precision, compact design, and compatibility with standard CNC mills.
-
Limitations: Limited to single-axis rotation, requiring additional mechanisms for multi-sided machining.
Trunnion Tables
Trunnion tables are advanced rotary tables that provide two rotational axes, typically A and B, allowing the workpiece to tilt and rotate. They are commonly used in five-axis CNC machines, where the ability to access five out of six sides of a prismatic workpiece is critical.
Key Features:
-
Degrees of Freedom: Dual-axis rotation (A and B), often combined with linear X, Y, Z movements.
-
Applications: Aerospace components, turbine blades, and complex molds requiring multi-angle machining.
-
Advantages: Enables continuous five-axis machining, reducing setup times and improving surface finish.
-
Limitations: Higher cost and complexity compared to single-axis rotary tables.
Pallet Changers
Pallet changers are automated systems that swap workpieces between a machining area and a loading station. The workpiece is mounted on a pallet, which is transferred into the machine by a shuttle or robotic arm. Pallet changers are widely used in high-volume production, where minimizing downtime is critical.
Key Features:
-
Degrees of Freedom: Linear translation for pallet exchange, with optional rotation for workpiece reorientation.
-
Applications: Automotive parts, consumer electronics, and mass-produced components.
-
Advantages: Enables continuous machining by allowing operators to load/unload pallets offline.
-
Limitations: Requires significant floor space and investment in automation infrastructure.
Robotic Arms
Robotic arms are versatile workpiece reversing mechanisms that can handle complex reorientation tasks. Integrated with CNC machines, robotic arms can flip, rotate, or reposition workpieces with high precision, often using custom end-effectors (grippers or fixtures).
Key Features:
-
Degrees of Freedom: Six or more, depending on the robot’s design.
-
Applications: Flexible manufacturing systems, complex assemblies, and parts with irregular geometries.
-
Advantages: High flexibility, adaptability to different workpiece sizes, and integration with Industry 4.0 systems.
-
Limitations: High initial cost, complex programming, and potential for reduced precision in heavy-duty applications.
Custom Fixtures with Actuated Clamps
Custom fixtures with actuated clamps are designed for specific workpieces, incorporating mechanisms to rotate or flip the part within the fixture. These fixtures are often used in specialized applications, such as machining large or irregularly shaped components.
Key Features:
-
Degrees of Freedom: Varies based on fixture design, typically one or two axes of rotation.
-
Applications: Large aerospace structures, heavy machinery components, and unique prototypes.
-
Advantages: Tailored to specific parts, ensuring optimal clamping and accessibility.
-
Limitations: Limited reusability and high design/fabrication costs.
Comparison of Workpiece Reversing Mechanisms
The following table compares the main types of workpiece reversing mechanisms based on key criteria, providing a reference for selecting the appropriate mechanism for specific CNC applications.
Mechanism |
Degrees of Freedom |
Primary Applications |
Advantages |
Limitations |
Typical Cost Range |
---|---|---|---|---|---|
Rotary Table |
1 (A or C axis) |
Cylindrical parts, gears, radial features |
High precision, compact, cost-effective |
Limited to single-axis rotation |
$5,000–$20,000 |
Trunnion Table |
2 (A and B axes) |
Aerospace, molds, turbine blades |
Enables five-axis machining, reduces setups |
High cost, complex setup |
$20,000–$100,000 |
Pallet Changer |
Linear + optional rotation |
Automotive, electronics, high-volume parts |
Continuous operation, offline loading |
Large footprint, high initial investment |
$50,000–$200,000 |
Robotic Arm |
6+ |
Flexible manufacturing, complex geometries |
High flexibility, Industry 4.0 integration |
High cost, complex programming |
$30,000–$150,000 |
Custom Fixture |
1–2 (custom) |
Large/unique parts, prototypes |
Tailored to specific parts, optimal clamping |
Limited reusability, high design cost |
$10,000–$50,000 |
Notes:
-
Costs are approximate and vary based on manufacturer, specifications, and customization.
-
Applications reflect common use cases but are not exhaustive.
-
Advantages and limitations are generalized and may vary by specific implementation.
Operational Principles and Integration with CNC Systems
Workflow of Workpiece Reversing
The operation of a workpiece reversing mechanism follows a structured workflow, integrated with the CNC machining process:
-
Design and Programming:
-
A CAD model of the part is created, specifying all features and machining operations.
-
CAM software generates G-code, including commands for workpiece reorientation (e.g., M-code to activate a rotary table or pallet changer).
-
The toolpath accounts for the workpiece’s new orientation after each reversal, ensuring continuity in machining.
-
-
Machine Setup:
-
The workpiece is secured in the reversing mechanism (e.g., clamped on a rotary table or mounted on a pallet).
-
Tools are installed in the spindle or tool changer, and the machine is calibrated to the workpiece’s initial position.
-
The reversing mechanism is zeroed or homed to establish a reference point for movements.
-
-
Machining and Reorientation:
-
The CNC machine executes the programmed toolpath, machining accessible surfaces.
-
When a reversal is required, the CNC controller activates the reversing mechanism (e.g., rotating the table or swapping pallets).
-
Sensors verify the new orientation, and the machine resumes machining.
-
-
Inspection and Finishing:
-
After machining, the part is inspected for dimensional accuracy using tools like coordinate measuring machines (CMM).
-
Any discrepancies caused by reversing errors (e.g., misalignment) are addressed through adjustments or reprogramming.
-
Control Systems and Feedback
Modern workpiece reversing mechanisms rely on sophisticated control systems to ensure precision and reliability. The CNC controller, typically a programmable logic controller (PLC) or dedicated microprocessor, coordinates the reversing mechanism with tool movements. Feedback systems, such as optical encoders or torque sensors, monitor the mechanism’s performance and detect anomalies, such as excessive load or positional errors.
Closed-loop control is critical for high-precision applications, as it allows the system to correct deviations in real time. For example, if a rotary table overshoots its target angle due to backlash, the controller can adjust the motor’s position based on encoder feedback. Advanced systems may also incorporate adaptive control, where the machine adjusts parameters (e.g., feed rate) based on real-time data, optimizing performance for varying workpiece materials or geometries.
Integration with Multi-Axis Machining
Workpiece reversing mechanisms are most effective in multi-axis CNC systems, where they complement the machine’s ability to move tools or workpieces along multiple axes. In a five-axis milling machine, for instance, a trunnion table can tilt the workpiece to expose angled surfaces, while the spindle adjusts its orientation to maintain optimal cutting conditions. This synergy reduces the need for multiple setups, enabling the production of complex parts in a single operation.
The integration of reversing mechanisms with multi-axis systems requires careful programming to avoid collisions between the tool, workpiece, and machine components. CAM software simulates the entire machining process, including reversals, to identify potential issues and optimize toolpaths. Additionally, the machine’s kinematic model—defining the relationships between axes—must account for the reversing mechanism’s movements to ensure accurate positioning.
Applications of Workpiece Reversing Mechanisms
Aerospace Industry
The aerospace industry demands parts with complex geometries, tight tolerances, and high-strength materials, such as titanium and Inconel. Workpiece reversing mechanisms, particularly trunnion tables and robotic arms, are critical for machining components like turbine blades, engine casings, and structural frames. For example, a five-axis CNC mill with a trunnion table can machine a turbine blade’s airfoil surfaces and mounting features in a single setup, reducing cycle time and ensuring dimensional consistency.
Automotive Industry
In automotive manufacturing, workpiece reversing mechanisms support high-volume production of engine components, transmission gears, and chassis parts. Pallet changers are widely used in CNC machining centers, allowing continuous operation while operators load and unload workpieces offline. This automation is essential for meeting the industry’s demand for cost-efficiency and scalability.
Medical Device Manufacturing
Medical devices, such as orthopedic implants and surgical instruments, require precision and biocompatibility. Workpiece reversing mechanisms enable the machining of complex features, such as threaded holes or contoured surfaces, on small, intricate parts. Robotic arms are particularly valuable in this sector, as they can handle delicate workpieces and adapt to varying part designs.
Consumer Electronics
The production of consumer electronics, including smartphone housings and laptop chassis, relies on CNC machining for high-precision components. Pallet changers and rotary tables facilitate the machining of multiple features (e.g., ports, buttons, and camera cutouts) in a single operation, supporting the industry’s need for rapid prototyping and mass production.
Heavy Machinery and Energy
In heavy machinery and energy sectors, workpiece reversing mechanisms are used to machine large components, such as wind turbine hubs and oil rig fittings. Custom fixtures with actuated clamps are often employed to handle oversized workpieces, ensuring secure clamping and precise reorientation during machining.
Challenges and Limitations
Mechanical Backlash and Precision
Mechanical backlash, the play between moving components, can compromise the accuracy of workpiece reversing mechanisms. In operations involving axis reversals (e.g., milling a circular feature), backlash may cause positional errors, leading to defects like cutter chatter or gouging. While modern CNC systems use ball screws and closed-loop control to minimize backlash, older machines or poorly maintained systems may struggle with precision.
Alignment and Calibration
Ensuring precise alignment during workpiece reversal is a significant challenge, particularly for complex parts with tight tolerances. Misalignment can result from improper fixturing, wear in the reversing mechanism, or errors in the machine’s kinematic model. Regular calibration and maintenance are essential to mitigate these issues, but they increase operational costs.
Compatibility with Machine Types
Not all CNC machines are compatible with advanced workpiece reversing mechanisms. For example, a basic three-axis mill may lack the structural rigidity or control capabilities to support a trunnion table or robotic arm. Retrofitting older machines with reversing mechanisms can be costly and may not yield the desired performance improvements.
Cost and Complexity
The implementation of workpiece reversing mechanisms, particularly pallet changers and robotic arms, requires significant investment in hardware, software, and training. Small and medium-sized enterprises (SMEs) may find the cost prohibitive, limiting their ability to adopt advanced automation. Additionally, the complexity of programming and maintaining these systems can strain resources, especially in facilities with limited technical expertise.
Safety Considerations
Automated workpiece reversing mechanisms introduce safety risks, such as collisions between the workpiece, tool, or machine components. Operators must be trained to monitor the system and intervene if anomalies occur. Modern CNC machines incorporate safety interlocks and collision detection systems, but these features may not be present in older or hobbyist-grade equipment.
Advances in Workpiece Reversing Technology
Industry 4.0 and Smart Manufacturing
The integration of workpiece reversing mechanisms with Industry 4.0 technologies is transforming CNC machining. Sensors embedded in reversing mechanisms collect data on position, torque, and vibration, enabling real-time monitoring and predictive maintenance. Machine learning algorithms analyze this data to optimize machining parameters, detect potential failures, and improve overall equipment effectiveness (OEE).
Additive-Subtractive Hybrid Systems
Hybrid manufacturing systems, combining additive (3D printing) and subtractive (CNC machining) processes, are gaining traction. Workpiece reversing mechanisms play a crucial role in these systems, allowing the workpiece to be reoriented for both additive deposition and subtractive finishing. For example, a robotic arm can flip a partially printed part to machine its underside, ensuring a smooth surface finish.
Modular and Reconfigurable Systems
Modular workpiece reversing mechanisms, such as interchangeable rotary tables or quick-change pallets, offer flexibility for manufacturers handling diverse part types. These systems can be reconfigured to accommodate different workpiece sizes or machining requirements, reducing setup times and improving adaptability in dynamic production environments.
Enhanced Feedback and Control
Advances in feedback systems, such as high-resolution optical encoders and laser-based positioning, have improved the precision of workpiece reversing mechanisms. These systems enable sub-micron accuracy, critical for applications like semiconductor manufacturing and precision optics. Additionally, adaptive control algorithms adjust the mechanism’s behavior in response to material variations or tool wear, enhancing reliability.
Case Studies and Practical Examples
Case Study 1: Aerospace Turbine Blade Manufacturing
A leading aerospace manufacturer implemented a five-axis CNC milling machine with a trunnion table to produce turbine blades. The trunnion table allowed the workpiece to be tilted and rotated, enabling the machining of complex airfoil surfaces and mounting features in a single setup. The system reduced setup time by 60% and improved dimensional accuracy by 25%, resulting in significant cost savings and faster delivery times.
Case Study 2: Automotive Engine Block Production
An automotive supplier adopted a pallet changer system for CNC machining centers producing engine blocks. The pallet changer enabled continuous operation, with operators loading and unloading pallets offline while the machine processed workpieces. The system increased throughput by 40% and reduced labor costs by 20%, demonstrating the value of automation in high-volume production.
Case Study 3: Medical Implant Machining
A medical device manufacturer used a robotic arm to handle small, intricate implants during CNC machining. The robotic arm flipped the workpieces to access multiple surfaces, eliminating the need for manual repositioning. The system achieved a 30% reduction in cycle time and improved part consistency, critical for meeting stringent regulatory standards.
Future Trends and Research Directions
Artificial Intelligence and Machine Learning
The integration of artificial intelligence (AI) and machine learning (ML) into workpiece reversing mechanisms holds significant potential. AI-driven systems can optimize reorientation sequences, predict maintenance needs, and adapt to unexpected variations in workpiece geometry. For example, an ML algorithm could analyze historical machining data to recommend the most efficient reversing strategy for a given part.
Miniaturization and Micro-Machining
As industries like electronics and medical devices demand smaller, more precise components, workpiece reversing mechanisms must evolve to support micro-machining. Miniaturized rotary tables and robotic grippers, combined with high-resolution feedback systems, will enable the production of sub-millimeter features with unprecedented accuracy.
Sustainability and Energy Efficiency
Sustainability is a growing concern in manufacturing, driving research into energy-efficient workpiece reversing mechanisms. Lightweight materials, low-friction actuators, and regenerative braking systems can reduce the energy consumption of these mechanisms, aligning with global efforts to minimize industrial carbon footprints.
Collaborative Robotics
Collaborative robots (cobots) are emerging as a cost-effective solution for workpiece reversing in SMEs. Unlike traditional robotic arms, cobots are designed to work alongside human operators, offering flexibility and ease of programming. Future developments may see cobots integrated with CNC machines for seamless workpiece handling and reorientation.
Conclusion
Workpiece reversing mechanisms are a cornerstone of modern CNC machining, enabling the automation, precision, and efficiency required to produce complex parts across diverse industries. From rotary tables to robotic arms, these mechanisms have evolved significantly since the advent of CNC technology, driven by advancements in control systems, feedback technologies, and Industry 4.0 integration. While challenges like backlash, alignment, and cost persist, ongoing innovations in AI, hybrid manufacturing, and sustainable design promise to further enhance their capabilities.
This comprehensive exploration of workpiece reversing mechanisms underscores their critical role in advancing manufacturing. By providing detailed technical insights, comparative analyses, and forward-looking perspectives, this article aims to serve as a valuable resource for professionals seeking to understand and leverage these mechanisms in their operations. As CNC machining continues to evolve, workpiece reversing mechanisms will remain at the forefront of efforts to achieve greater automation, precision, and productivity in the production of tomorrow’s technologies.
Reprint Statement: If there are no special instructions, all articles on this site are original. Please indicate the source for reprinting:https://www.cncmachiningptj.com/,thanks!
PTJ® provides a full range of Custom Precision cnc machining china services.ISO 9001:2015 &AS-9100 certified. 3, 4 and 5-axis rapid precision CNC machining services including milling, turning to customer specifications,Capable of metal & plastic machined parts with +/-0.005 mm tolerance.Secondary services include CNC and conventional grinding, drilling,die casting,sheet metal and stamping.Providing prototypes, full production runs, technical support and full inspection.Serves the automotive, aerospace, mold&fixture,led lighting,medical,bicycle, and consumer electronics industries. On-time delivery.Tell us a little about your project's budget and expected delivery time. We will strategize with you to provide the most cost-effective services to help you reach your target,Welcome to Contact us ( sales@pintejin.com ) directly for your new project.
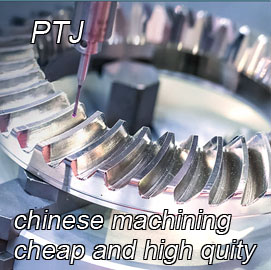
- 5 Axis Machining
- Cnc Milling
- Cnc Turning
- Machining Industries
- Machining Process
- Surface Treatment
- Metal Machining
- Plastic Machining
- Powder Metallurgy Mold
- Die Casting
- Parts Gallery
- Auto Metal Parts
- Machinery Parts
- LED Heatsink
- Building Parts
- Mobile Parts
- Medical Parts
- Electronic Parts
- Tailored Machining
- Bicycle Parts
- Aluminum Machining
- Titanium Machining
- Stainless Steel Machining
- Copper Machining
- Brass Machining
- Super Alloy Machining
- Peek Machining
- UHMW Machining
- Unilate Machining
- PA6 Machining
- PPS Machining
- Teflon Machining
- Inconel Machining
- Tool Steel Machining
- More Material