Application of SKP-27 Quick-Drying Silica Sol in Precision Casting
Precision casting, also known as investment casting or lost-wax casting, is a manufacturing process used to create complex, high-precision metal components with excellent surface finish and dimensional accuracy. This technique has been employed for centuries, evolving from ancient artisanal methods to a sophisticated industrial process integral to industries such as aerospace, automotive, medical, and power generation. The process involves creating a wax pattern, coating it with a refractory material to form a ceramic shell, melting out the wax, and pouring molten metal into the resulting cavity to produce a near-net-shape component.
A critical component in modern precision casting is the binder used to form the ceramic shell. Silica sol, a colloidal dispersion of amorphous silica particles in water, has become a preferred binder due to its ability to produce smooth, high-strength molds capable of withstanding high temperatures. Among the various silica sol formulations, SKP-27 quick-drying silica sol stands out for its enhanced properties, particularly its rapid drying characteristics, which significantly improve production efficiency. This article explores the application of SKP-27 quick-drying silica sol in precision casting, detailing its composition, properties, advantages, and impact on the casting process, supported by comparative analyses and case studies.
Composition and Properties of SKP-27 Quick-Drying Silica Sol
SKP-27 is a polymer-reinforced, fast-drying silica sol specifically engineered for precision casting applications. Its composition includes a high concentration of silica (SiO₂) particles, typically ranging from 25–30% by weight, dispersed in an aqueous medium. The sol is stabilized with alkali ions, such as sodium or potassium, to maintain a pH between 9 and 10, ensuring colloidal stability. The addition of organic polymers enhances the gelation process, reducing drying time while maintaining the structural integrity of the ceramic shell.
Key Physical and Chemical Properties
-
Particle Size: SKP-27 features silica particles with an average diameter of 10–20 nm, contributing to its low viscosity and excellent coating properties.
-
Viscosity: The sol exhibits a kinematic viscosity of approximately 4–6 mPa·s at 25°C, facilitating uniform coating during shell-building.
-
Density: Typically 1.15–1.20 g/cm³, ensuring adequate suspension of refractory materials in the slurry.
-
Gelation Time: Enhanced by polymer additives, SKP-27 achieves gelation in 2–4 hours under controlled conditions, compared to 12–24 hours for traditional silica sols.
-
Thermal Stability: The sol forms shells capable of withstanding temperatures up to 2000°C, suitable for casting high-temperature alloys.
These properties make SKP-27 particularly suited for applications requiring rapid production cycles and high-quality surface finishes, such as turbine blades, medical implants, and intricate automotive components.
Role of Silica Sol in Precision Casting
In precision casting, silica sol serves as the primary binder in the shell-building process. The process begins with the creation of a wax pattern, which is dipped into a slurry composed of silica sol and refractory materials, such as zircon, alumina, or fused silica. After coating, the layer is sprinkled with coarse refractory sand (stucco) and allowed to dry. This dipping and drying cycle is repeated multiple times to build a multi-layered ceramic shell, typically consisting of 4–8 layers, depending on the casting requirements.
The drying phase is critical, as it determines the shell’s strength and dimensional stability. Traditional silica sols, such as S-830 or S-1430, rely on slow evaporation of water, leading to drying times of 12–24 hours per layer. This extended drying period increases production time and energy costs, limiting throughput in high-volume manufacturing. SKP-27 addresses these challenges by incorporating quick-drying agents that accelerate gelation and reduce drying time by over 50%, enabling faster shell production without compromising quality.
Comparison of SKP-27 with Traditional Silica Sols
The following table compares the properties and performance of SKP-27 with conventional silica sols used in precision casting:
Property |
SKP-27 Quick-Drying Silica Sol |
S-830 Silica Sol |
S-1430 Silica Sol |
---|---|---|---|
SiO₂ Content (%) |
25–30 |
28–30 |
28–30 |
Particle Size (nm) |
10–20 |
10–15 |
12–18 |
Viscosity (mPa·s) |
4–6 |
5–7 |
6–8 |
pH |
9–10 |
9–10 |
9–10 |
Drying Time per Layer (h) |
2–4 |
12–24 |
10–20 |
Shell Strength (MPa) |
4.5–5.0 |
3.5–4.0 |
3.8–4.2 |
Thermal Stability (°C) |
Up to 2000 |
Up to 1800 |
Up to 1900 |
Defect Rate (%) |
<4.5 |
>11.7 |
~8.0 |
Source: Adapted from industry studies and technical data sheets.
The table highlights SKP-27’s superior drying speed and reduced defect rate, which contribute to its widespread adoption in precision casting.
Advantages of SKP-27 in Precision Casting
The application of SKP-27 quick-drying silica sol offers several advantages over traditional binders, transforming the efficiency and quality of the precision casting process. These benefits are discussed in detail below.
1. Reduced Drying Time
The most significant advantage of SKP-27 is its ability to reduce drying time per shell layer to 2–4 hours, compared to 12–24 hours for conventional silica sols. This reduction is achieved through the incorporation of organic polymer additives that accelerate the gelation process. By shortening the drying cycle, SKP-27 enables manufacturers to produce ceramic shells in less than 26 hours for a typical four-layer shell, compared to 52 hours with traditional methods. This efficiency translates to higher throughput, reduced energy consumption, and lower production costs.
2. Enhanced Shell Strength
SKP-27 produces ceramic shells with a green strength of approximately 4.5–5.0 MPa, significantly higher than the 3.5–4.0 MPa achieved with S-830 silica sol. This increased strength reduces the risk of shell cracking during dewaxing and casting, improving the yield of defect-free components. The high strength is attributed to the uniform distribution of silica particles and the reinforcing effect of polymer additives, which enhance the bonding between refractory particles.
3. Improved Surface Finish
The fine particle size and low viscosity of SKP-27 result in a smooth, dense slurry that coats wax patterns evenly, minimizing surface imperfections. Castings produced with SKP-27 shells exhibit surface roughness values as low as Ra 3.2 µm, reducing the need for post-casting machining or polishing. This is particularly beneficial for applications requiring high aesthetic or functional surface quality, such as medical implants and turbine blades.
4. Lower Defect Rates
Studies have demonstrated that SKP-27 reduces casting defect rates to below 4.5%, compared to over 11.7% for S-830 silica sol. Common defects, such as porosity, inclusions, and surface pockmarks, are minimized due to the sol’s stability and insensitivity to environmental conditions. The stable colloidal dispersion prevents slurry degradation, ensuring consistent shell quality over extended production runs.
5. Environmental Benefits
SKP-27 is formulated to be environmentally friendly, with low volatile organic compound (VOC) emissions and no reliance on hazardous chemicals like ammonium chloride or hydrochloric acid. The elimination of these pollutants aligns with global environmental regulations and reduces the ecological footprint of precision casting operations. Additionally, the sol’s water-based composition enhances workplace safety by minimizing exposure to toxic fumes.
6. Versatility Across Alloys
SKP-27’s high thermal stability makes it suitable for casting a wide range of alloys, including stainless steel, carbon steel, high-temperature alloys (e.g., nickel-based superalloys), aluminum, and copper. Its ability to withstand temperatures up to 2000°C ensures compatibility with demanding applications, such as aerospace components and power generation equipment.
Process Optimization with SKP-27
The integration of SKP-27 into the precision casting process requires careful optimization of several parameters, including slurry composition, drying conditions, and shell-building techniques. This section explores the key considerations for maximizing the benefits of SKP-27.
Slurry Preparation
The slurry is prepared by mixing SKP-27 with refractory powders, such as zircon, alumina, or mullite, in a controlled powder-to-liquid ratio (typically 2:1 to 3:1). To enhance slurry performance, auxiliary additives are incorporated:
-
Suspending Agents: Prevent settling of refractory particles, ensuring uniform coating.
-
Wetting Agents: Improve slurry adhesion to wax patterns, reducing bubbles and voids.
-
Defoamers: Eliminate air entrapment, enhancing shell density.
-
Mineralizing Agents: Promote gelation and strengthen the shell matrix.
The slurry’s viscosity and density must be monitored regularly, as changes in water content or SiO₂ concentration can affect coating quality. For SKP-27, a viscosity of 15–25 seconds (measured with a #4 Zahn cup) is optimal for dipping.
Drying Conditions
The drying process is influenced by environmental factors such as temperature, humidity, and air velocity. SKP-27’s quick-drying properties are optimized under the following conditions:
-
Temperature: 22–25°C (±1.5°C) to promote uniform evaporation without causing thermal stress.
-
Relative Humidity: 40–60% to balance drying speed and shell integrity.
-
Air Velocity: 0.5–1.0 m/s to facilitate moisture removal without disrupting the slurry coating.
Hot air drying systems with controllable humidity are commonly used to achieve these conditions, reducing drying time while maintaining shell quality. Infrared thermometers can be employed to monitor shell dryness, ensuring a temperature difference of ≤1°C between the shell’s surface and core, indicating complete drying.
Shell-Building Techniques
SKP-27 supports both manual and automated shell-building processes. In automated systems, such as catenary lines, the sol’s stability and rapid drying enable continuous operation, producing shells in as little as 6–8 hours for surface layers and 4–6 hours for backup layers. The number of layers depends on the casting’s size and complexity, with smaller components requiring 4–5 layers and larger ones needing 6–8 layers.
Dewaxing and Casting
After shell formation, the wax is removed using steam autoclaving at 150–200°C, leaving a cavity for molten metal. SKP-27 shells maintain structural integrity during dewaxing, minimizing cracks and distortion. The shells are then fired at 1000–1200°C to enhance strength and remove residual wax, preparing them for casting. The high thermal stability of SKP-27 ensures the shell withstands the impact of molten metal, producing castings with dimensional tolerances of CT4–CT6.
Case Studies: SKP-27 in Industrial Applications
The practical benefits of SKP-27 have been demonstrated in various industries. Below are detailed case studies highlighting its application in aerospace, medical, and automotive sectors.
Case Study 1: Aerospace Turbine Blades
Industry: Aerospace
Component: Nickel-based superalloy turbine blades
Challenge: Producing turbine blades with complex internal cooling channels and thin walls (1–2 mm) requires shells with high strength, thermal stability, and precision. Traditional silica sols resulted in long drying times and high defect rates, increasing costs.
Solution: A leading aerospace manufacturer adopted SKP-27 for shell production. The sol’s quick-drying properties reduced the shell-building cycle from 84 hours to 24 hours, while its fine particle size ensured a smooth surface finish (Ra 3.2 µm). The defect rate dropped from 12% to 3.8%, and the yield of defect-free blades increased by 15%.
Outcome: The use of SKP-27 reduced production costs by 20% and enabled the manufacturer to meet stringent delivery schedules, enhancing competitiveness in the aerospace market.
Case Study 2: Medical Implants
Industry: Medical
Component: Stainless steel hip implants
Challenge: Hip implants require exceptional surface quality and biocompatibility, with no surface defects or porosity. Conventional silica sols produced shells with inconsistent drying, leading to surface pockmarks and a 10% rejection rate.
Solution: A medical device manufacturer implemented SKP-27, leveraging its low viscosity and uniform coating properties. The drying time per layer was reduced to 3 hours, and the shell strength reached 4.8 MPa. Post-casting inspection revealed a surface roughness of Ra 2.8 µm and a defect rate below 4%.
Outcome: The improved surface quality eliminated the need for extensive polishing, reducing production time by 25% and ensuring compliance with medical standards.
Case Study 3: Automotive Gears
Industry: Automotive
Component: Alloy steel transmission gears
Challenge: High-volume production of gears demands rapid shell-making to meet tight delivery schedules. Traditional silica sols required 48–60 hours for shell production, limiting throughput.
Solution: An automotive parts supplier integrated SKP-27 into an automated catenary line. The sol’s rapid gelation enabled a shell-building cycle of 20 hours, with a defect rate of 4.2%. The gears achieved dimensional tolerances of CT5, reducing machining requirements.
Outcome: The supplier increased production capacity by 30%, lowered energy costs by 15%, and improved on-time delivery rates, strengthening its market position.
Comparative Analysis of SKP-27 and Alternative Binders
To fully appreciate SKP-27’s advantages, it is useful to compare it with other binders used in precision casting, such as water glass (sodium silicate), ethyl silicate, and silicone resin.
Water Glass (Sodium Silicate)
Water glass is a cost-effective binder widely used in precision casting, particularly for less demanding applications. However, it has several limitations:
-
Surface Quality: Produces rougher surfaces (Ra 6.3–12.5 µm) compared to SKP-27 (Ra 3.2 µm).
-
Dimensional Accuracy: Lower precision (CT7–CT10) versus SKP-27’s CT4–CT6.
-
Environmental Impact: Generates sodium salt and acid mist pollutants, unlike SKP-27’s eco-friendly formulation.
-
Drying Time: Requires 8–12 hours per layer, slower than SKP-27’s 2–4 hours.
While water glass is suitable for large, simple components, it cannot match SKP-27’s performance in high-precision applications.
Ethyl Silicate
Ethyl silicate is an alcohol-based binder used in some precision casting processes. Its advantages include fast drying and high shell strength, but it has significant drawbacks:
-
Cost: Higher material and processing costs compared to SKP-27.
-
Environmental Concerns: Emits volatile organic compounds (VOCs), requiring specialized ventilation systems.
-
Handling: Flammable and hazardous, posing safety risks.
-
Shell Quality: Produces shells with good strength but less consistent surface finish than SKP-27.
SKP-27’s water-based composition and rapid drying make it a safer, more cost-effective alternative.
Silicone Resin
Recent advancements have introduced silicone resin as a binder for high-strength ceramic shells. A study published in ScienceDirect demonstrated that silicone resin-based shells achieve a green strength of 4.81 MPa and a sintered strength of 9.89 MPa, surpassing SKP-27’s 4.5–5.0 MPa green strength. However, silicone resin has limitations:
-
Drying Time: Requires 2 hours per layer, comparable to SKP-27, but the overall process is more complex.
-
Cost: Higher raw material costs and processing complexity increase production expenses.
-
Porosity: Generates gaseous molecules during pyrolysis, introducing pores that may affect shell integrity.
SKP-27 remains the preferred choice for applications prioritizing speed, cost, and surface quality.
Comparative Table of Binders
Binder |
Drying Time per Layer (h) |
Green Strength (MPa) |
Surface Roughness (Ra µm) |
Environmental Impact |
Cost |
---|---|---|---|---|---|
SKP-27 Silica Sol |
2–4 |
4.5–5.0 |
3.2 |
Low (Water-based) |
Moderate |
Water Glass |
8–12 |
2.5–3.5 |
6.3–12.5 |
High (Pollutants) |
Low |
Ethyl Silicate |
1–3 |
4.0–4.5 |
4.0–6.0 |
High (VOCs) |
High |
Silicone Resin |
2 |
4.8–5.0 |
3.5–5.0 |
Moderate (Gas Emissions) |
High |
Source: Compiled from industry reports and ScienceDirect studies.
Challenges and Limitations of SKP-27
Despite its advantages, SKP-27 is not without challenges. These include:
-
Cost: SKP-27 is more expensive than water glass, which may deter cost-sensitive manufacturers.
-
Environmental Sensitivity: While less sensitive than traditional silica sols, SKP-27’s drying process is still affected by temperature and humidity fluctuations, requiring controlled conditions.
-
Bubble Formation: Improper slurry mixing can introduce bubbles, affecting shell quality. Careful addition of defoamers and wetting agents is necessary.
-
Production Scale: SKP-27 is optimized for medium to large-scale production. Small-scale operations may not fully realize its cost-saving benefits due to setup costs.
To address these challenges, manufacturers can invest in automated slurry management systems, climate-controlled drying rooms, and staff training to ensure consistent process control.
Future Trends and Innovations
The success of SKP-27 has spurred research into next-generation silica sols and binders for precision casting. Emerging trends include:
-
Nanotechnology: Developing silica sols with smaller particle sizes (<10 nm) to further improve surface finish and shell density.
-
Hybrid Binders: Combining silica sol with organic-inorganic hybrids, such as polysiloxane, to enhance strength and reduce drying time.
-
Sustainable Formulations: Formulating silica sols with recycled materials or bio-based additives to reduce environmental impact.
-
Automation and AI: Integrating AI-driven process control to optimize slurry composition, drying parameters, and defect detection, maximizing SKP-27’s efficiency.
These innovations promise to build on SKP-27’s foundation, further revolutionizing precision casting.
Conclusion
SKP-27 quick-drying silica sol represents a significant advancement in precision casting, offering reduced drying times, enhanced shell strength, improved surface finish, and lower defect rates. Its application across industries such as aerospace, medical, and automotive has demonstrated its ability to improve production efficiency and product quality while aligning with environmental regulations. By optimizing slurry preparation, drying conditions, and shell-building techniques, manufacturers can fully leverage SKP-27’s benefits, achieving cost savings and competitive advantages.
While challenges such as cost and environmental sensitivity remain, ongoing research and technological advancements are poised to address these limitations, ensuring SKP-27’s continued relevance in the evolving landscape of precision casting. As industries demand increasingly complex and high-performance components, SKP-27 stands as a cornerstone of modern investment casting, bridging the gap between efficiency and excellence.
Reprint Statement: If there are no special instructions, all articles on this site are original. Please indicate the source for reprinting:https://www.cncmachiningptj.com/,thanks!
PTJ® provides a full range of Custom Precision cnc machining china services.ISO 9001:2015 &AS-9100 certified. 3, 4 and 5-axis rapid precision CNC machining services including milling, turning to customer specifications,Capable of metal & plastic machined parts with +/-0.005 mm tolerance.Secondary services include CNC and conventional grinding, drilling,die casting,sheet metal and stamping.Providing prototypes, full production runs, technical support and full inspection.Serves the automotive, aerospace, mold&fixture,led lighting,medical,bicycle, and consumer electronics industries. On-time delivery.Tell us a little about your project's budget and expected delivery time. We will strategize with you to provide the most cost-effective services to help you reach your target,Welcome to Contact us ( sales@pintejin.com ) directly for your new project.
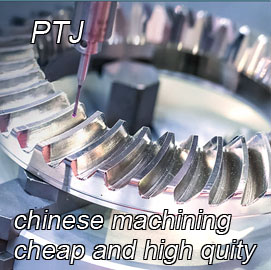
- 5 Axis Machining
- Cnc Milling
- Cnc Turning
- Machining Industries
- Machining Process
- Surface Treatment
- Metal Machining
- Plastic Machining
- Powder Metallurgy Mold
- Die Casting
- Parts Gallery
- Auto Metal Parts
- Machinery Parts
- LED Heatsink
- Building Parts
- Mobile Parts
- Medical Parts
- Electronic Parts
- Tailored Machining
- Bicycle Parts
- Aluminum Machining
- Titanium Machining
- Stainless Steel Machining
- Copper Machining
- Brass Machining
- Super Alloy Machining
- Peek Machining
- UHMW Machining
- Unilate Machining
- PA6 Machining
- PPS Machining
- Teflon Machining
- Inconel Machining
- Tool Steel Machining
- More Material