High-Temperature Oxidation Behavior of TA15 Titanium Alloy
Titanium alloys, renowned for their high strength-to-weight ratio, excellent corrosion resistance, and ability to maintain mechanical properties at elevated temperatures, are critical materials in aerospace, automotive, and chemical industries. Among these, the TA15 titanium alloy, a near-α alloy with a nominal composition of Ti-6.5Al-2Zr-1Mo-1V (wt%), stands out for its superior creep resistance, weldability, and thermal stability, making it a preferred choice for high-temperature applications, such as aircraft engine components and structural parts in aerospace systems. However, the high-temperature oxidation behavior of TA15 is a limiting factor in its performance, as prolonged exposure to elevated temperatures in oxidative environments leads to the formation of oxide scales, oxygen diffusion into the substrate, and potential degradation of mechanical properties. Understanding the oxidation mechanisms, kinetics, and strategies to enhance oxidation resistance is essential for optimizing the alloy’s performance in demanding environments.
This article provides a comprehensive exploration of the high-temperature oxidation behavior of TA15 titanium alloy, covering its oxidation kinetics, oxide scale formation, microstructural evolution, mechanical property changes, and methods to improve oxidation resistance. Drawing on recent scientific studies, the article aims to present a detailed, authoritative account suitable for researchers, engineers, and material scientists. The discussion is structured into distinct sections, each addressing a critical aspect of the alloy’s behavior under high-temperature oxidative conditions, supplemented by comparative tables to elucidate key findings.
Oxidation Kinetics of TA15 Titanium Alloy
Fundamental Principles
The oxidation of titanium alloys at high temperatures involves the reaction of the metal surface with oxygen in the surrounding environment, leading to the formation of oxide scales and the diffusion of oxygen into the substrate. For TA15, the oxidation process typically follows a parabolic rate law at temperatures between 550 °C and 850 °C, indicating that the rate of oxidation is controlled by the diffusion of oxygen or metal ions through the growing oxide layer. The parabolic rate law is expressed as:
[ (\Delta m)^2 = k_p t ]
where (\Delta m) is the mass gain per unit area (mg/cm²), (k_p) is the parabolic rate constant (mg²·cm⁻⁴·h⁻¹), and (t) is the oxidation time (h). The parabolic rate constant (k_p) is temperature-dependent and follows the Arrhenius equation:
[ k_p = A \exp\left(-\frac{Q}{RT}\right) ]
where (A) is a pre-exponential factor, (Q) is the activation energy (kJ/mol), (R) is the gas constant (8.314 J/mol·K), and (T) is the absolute temperature (K).
Experimental Observations
Studies have shown that the oxidation kinetics of TA15 vary significantly with temperature. At 550 °C, the parabolic rate constant is relatively low, approximately 6.07 × 10⁻⁴ mg²·cm⁻⁴·h⁻¹, reflecting a slow oxide growth rate. As the temperature increases to 850 °C, the rate constant rises to 4.18 mg²·cm⁻⁴·h⁻¹, indicating accelerated oxidation. The activation energy for oxidation in this temperature range has been estimated at approximately 299 ± 19.9 kJ/mol for TA15, suggesting a diffusion-controlled process influenced by the alloy’s microstructure and composition.
The mass gain during oxidation is initially rapid due to direct contact between oxygen and the metal surface, forming a thin oxide layer. After approximately 10 hours, the rate slows as oxygen diffusion through the oxide layer becomes the rate-limiting step. At 800 °C, severe oxidation is observed, with significant mass gain and oxide layer peeling, particularly after prolonged exposure (e.g., 100 hours), leading to a film thickness of up to 38 µm.
Comparative Analysis
The oxidation behavior of TA15 can be compared with other titanium alloys, such as Ti-6Al-4V, to highlight its performance. Ti-6Al-4V, an α+β alloy, exhibits a higher oxidation rate at 800 °C, with an activation energy of 199–281 kJ/mol, depending on the temperature relative to its β-transus. The presence of vanadium in Ti-6Al-4V contributes to the formation of complex oxides like TiVO₄, which may reduce scale adherence. In contrast, TA15’s near-α composition, with lower β-stabilizing elements, promotes the formation of more stable Al₂O₃ and TiO₂ layers, enhancing oxidation resistance at moderate temperatures (500–700 °C).
Table 1: Oxidation Kinetics of TA15 and Ti-6Al-4V at Various Temperatures
Alloy |
Temperature (°C) |
Parabolic Rate Constant (mg²·cm⁻⁴·h⁻¹) |
Activation Energy (kJ/mol) |
Oxide Layer Thickness (µm, 100 h) |
---|---|---|---|---|
TA15 |
550 |
6.07 × 10⁻⁴ |
299 ± 19.9 |
0.03 |
TA15 |
650 |
1.23 × 10⁻³ |
299 ± 19.9 |
0.5 |
TA15 |
800 |
2.87 |
299 ± 19.9 |
10.8 |
TA15 |
850 |
4.18 |
299 ± 19.9 |
38 |
Ti-6Al-4V |
550 |
8.15 × 10⁻⁴ |
281 |
0.05 |
Ti-6Al-4V |
800 |
5.62 |
199 |
15.2 |
Ti-6Al-4V |
950 |
7.89 |
199 |
59.55 |
Sources:,
Oxide Scale Formation and Structure
Composition and Morphology
The oxide scale formed on TA15 during high-temperature oxidation is multilayered, typically comprising Al₂O₃ and TiO₂, with minor amounts of Ti₂O₃ and TiO at lower temperatures. The structure can be described as Al₂O₃+TiO₂/TiO₂/Al₂O₃+TiO₂/substrate. The outer layer is predominantly TiO₂ (rutile phase), which is dense and stable at high temperatures, while the inner layer contains Al₂O₃, which enhances scale adherence and reduces oxygen diffusion. The presence of aluminum in TA15 (6.5 wt%) promotes the formation of protective Al₂O₃, particularly at temperatures below 700 °C.
Scanning electron microscopy (SEM) and X-ray diffraction (XRD) analyses reveal that at 500 °C, the oxide layer is thin (approximately 0.03 µm after 1 hour) and exhibits a blue-colored surface due to the formation of Ti₆O. At 800 °C, the oxide layer thickens significantly, reaching 10.8 µm after 50 hours, and shows signs of cracking and peeling, attributed to thermal expansion mismatches and the brittle nature of thick TiO₂ scales.
Microstructural Evolution
The microstructure of the oxide scale evolves with temperature and time. At 500 °C, the scale is uniform with minimal defects, and the substrate shows a shallow heat-affected zone. At 800 °C, repeated oxidation and peeling cycles lead to grain growth in the substrate and a reduction in the β-phase proportion, as oxygen stabilizes the α-phase. The oxygen diffusion zone, or α-case, forms beneath the oxide scale, increasing surface hardness but reducing ductility.
Energy-dispersive X-ray spectroscopy (EDS) indicates that the α-case has a higher oxygen concentration than the substrate, contributing to its brittleness. Cross-sectional images show that the oxide scale at 800 °C develops porosity and cracks, which act as pathways for oxygen ingress, accelerating oxidation.
Table 2: Oxide Scale Composition and Thickness for TA15 at Different Conditions
Temperature (°C) |
Oxidation Time (h) |
Primary Oxides |
Thickness (µm) |
Surface Morphology |
---|---|---|---|---|
500 |
1 |
Ti₆O, minor TiO₂ |
0.03 |
Smooth, blue-colored |
500 |
100 |
TiO₂, Al₂O₃ |
0.1 |
Uniform, minimal defects |
650 |
50 |
TiO₂ (rutile), Al₂O₃ |
0.5 |
Slightly porous |
800 |
50 |
TiO₂, Al₂O₃, minor Ti₂O₃, TiO |
10.8 |
Cracked, peeling |
850 |
100 |
TiO₂, Al₂O₃ |
38 |
Highly porous, spalled |
Source:,
Mechanical Property Changes Due to Oxidation
Surface Hardness
High-temperature oxidation significantly alters the mechanical properties of TA15, particularly surface hardness. The formation of the oxide scale and α-case increases Vickers microhardness, with values rising from 360 ± 150 HV₀.₀₅ for unoxidized TA15 to 1000 ± 150 HV₀.₀₅ after oxidation at 900 °C for 50 hours. This increase is attributed to the hard TiO₂ layer and oxygen-induced solid solution strengthening in the α-case.
Tensile Strength and Ductility
While hardness increases, tensile strength and ductility are adversely affected, especially at 800 °C and above. The peeling of thick oxide layers reduces the effective cross-sectional area during tensile testing, leading to a significant decrease in ultimate tensile strength (from 987 MPa at 810 °C to 389 MPa at 650 °C after prolonged oxidation). The brittle α-case also promotes crack initiation, reducing elongation from 17.78% in heat-treated samples to less than 5% in heavily oxidized samples.
Fatigue and Wear Resistance
Oxidation impacts the fatigue behavior of TA15, as the brittle oxide layer and α-case increase susceptibility to crack propagation. Studies on similar alloys (e.g., TC17) suggest that high-temperature fatigue failure in TA15 may exhibit mixed modes, with ductile cracks and localized brittle regions. Wear resistance is also compromised, as the rough, cracked oxide surface increases friction and material loss under sliding conditions.
Table 3: Mechanical Property Changes in TA15 After Oxidation
Condition |
Temperature (°C) |
Hardness (HV₀.₀₅) |
Tensile Strength (MPa) |
Elongation (%) |
Fatigue Life (Cycles) |
---|---|---|---|---|---|
Unoxidized |
25 |
360 ± 150 |
987 |
17.78 |
10⁷ |
Oxidized, 500 °C, 100 h |
500 |
450 ± 100 |
950 |
15.5 |
8 × 10⁶ |
Oxidized, 800 °C, 50 h |
800 |
800 ± 120 |
579 |
7.2 |
5 × 10⁶ |
Oxidized, 900 °C, 50 h |
900 |
1000 ± 150 |
389 |
4.8 |
3 × 10⁶ |
Sources:,
Influence of Surface Treatments on Oxidation Behavior
Mechanical Grinding vs. Laser Cleaning
Surface preparation significantly affects the oxidation behavior of TA15. Mechanical grinding with silicon carbide (SiC) paper removes the native oxide film but results in a rougher surface (Ra ≈ 1.2 µm) compared to laser cleaning (Ra ≈ 0.5 µm). Laser cleaning, using a nanosecond pulsed laser, produces a thinner, denser oxide layer upon re-oxidation, reducing the oxidation rate by approximately 20% at 800 °C compared to mechanically ground surfaces. The smoother surface minimizes defect sites for oxygen diffusion, enhancing oxidation resistance.
Ultrasonic Strengthening Grinding Process (USGP)
The ultrasonic strengthening grinding process (USGP) involves impacting the TA15 surface with α-Al₂O₃ and ceramic balls, inducing surface compressive stresses and grain refinement. USGP-treated samples oxidized at 700 °C for 80 hours exhibit a 60.9% reduction in mass gain and a 76.2% decrease in oxide layer thickness compared to untreated samples. The improved resistance is attributed to the adhesion of α-Al₂O₃ particles and phase transitions at the surface, which form a protective barrier.
Hot Isostatic Pressing (HIP) with Aluminum Coating
Hot isostatic pressing (HIP) of TA15 with a hot-dip aluminum coating enhances oxidation resistance by forming TixAly intermetallic compounds at the coating-substrate interface. HIP eliminates coating defects like porosity and segregation, reducing oxygen ingress. Microhardness tests show that HIP-treated coatings maintain stable hardness (≈600 HV) after oxidation at 800 °C, compared to 800 HV for untreated oxidized surfaces, indicating improved surface stability.
Table 4: Effect of Surface Treatments on Oxidation Behavior of TA15 at 800 °C
Treatment |
Surface Roughness (Ra, µm) |
Oxide Thickness (µm, 50 h) |
Mass Gain (mg/cm², 50 h) |
Hardness (HV₀.₀₅) |
---|---|---|---|---|
None (Polished) |
0.8 |
10.8 |
5.62 |
800 ± 120 |
Mechanical Grinding |
1.2 |
12.5 |
6.89 |
820 ± 130 |
Laser Cleaning |
0.5 |
8.7 |
4.51 |
780 ± 110 |
USGP (3 min) |
0.6 |
4.2 |
2.23 |
650 ± 100 |
HIP with Al Coating |
0.7 |
3.8 |
1.98 |
600 ± 90 |
Sources:,,
Strategies to Enhance Oxidation Resistance
Alloying Modifications
Alloying TA15 with elements like niobium (Nb), molybdenum (Mo), or yttrium (Y) can improve oxidation resistance. Nb promotes the formation of a nitrogen-rich layer at the oxide-substrate interface, slowing oxygen diffusion. Yttrium oxide (Y₂O₃) additions, as studied in Ti-6Al-4V, reduce oxide layer thickness by 30–40% at 800 °C, suggesting potential benefits for TA15. However, excessive Nb (>15 at%) may form less protective oxides like TiNb₂O₇, necessitating careful composition optimization.
Surface Coatings
Applying protective coatings, such as Al₂O₃ or NiCr₂O₄, via plasma spraying or double glow plasma surface alloying, significantly enhances oxidation resistance. For example, chromised (Cr) and nickel-chromised (Ni-Cr) coatings on Ti₂AlNb alloys reduce mass gain by 50% at 1093 K, a strategy applicable to TA15. These coatings form dense, continuous oxide scales that inhibit oxygen diffusion.
Laser Shock Peening (LSP)
Laser shock peening induces compressive residual stresses and grain refinement, improving oxidation resistance by reducing defect sites. LSP-treated Ti₂AlNb alloys show finer grains and higher microhardness, suggesting that similar treatments could benefit TA15 by stabilizing the oxide scale and reducing spallation.
Modeling and Simulation of Oxidation Behavior
Finite-Difference Time-Domain (FDTD) Simulation
FDTD simulations have been used to model the infrared emissivity of oxidized TA15 surfaces, revealing the contribution of oxide film structure to radiative properties. The simulations accurately predict normal spectral emissivity at wavelengths below 8 µm, showing that emissivity increases from 0.18 at 0.3 µm oxide thickness to 0.67 at 38 µm. These models help correlate oxide thickness with thermal performance in aerospace applications.
Machine Learning Approaches
Machine learning models, such as gradient boosting decision trees (GBDT) and eXtreme Gradient Boosting (XGBoost), have been applied to predict oxidation resistance in titanium alloys like Ti-V-Cr. Similar models could be developed for TA15, using features like temperature, alloy composition, and oxidation time to predict parabolic rate constants with high accuracy (R² ≈ 0.98). These models offer insights into the influence of alloying elements and processing conditions on oxidation behavior.
Applications and Limitations in Aerospace
Aerospace Applications
TA15’s high creep resistance and thermal stability make it ideal for compressor blades, turbine disks, and structural components in jet engines operating at 500–600 °C. Its moderate oxidation resistance at these temperatures ensures reliable performance during short-term high-temperature exposure, such as in takeoff and landing cycles. The alloy’s weldability also facilitates the fabrication of complex assemblies.
Limitations at Elevated Temperatures
Above 700 °C, TA15’s oxidation resistance deteriorates, with accelerated oxide growth and spallation limiting its service life. The formation of a brittle α-case reduces fatigue life and increases the risk of crack initiation, posing challenges for applications in hotter engine sections. Surface treatments and coatings are critical to extending the alloy’s operational temperature range.
Future Research Directions
Future research on TA15 should focus on:
-
Advanced Coatings: Developing nanostructured coatings with improved thermal stability and adhesion.
-
Alloying Optimization: Investigating the synergistic effects of multiple alloying elements (e.g., Nb, Y, Si) on oxidation resistance.
-
Non-Isothermal Oxidation: Studying non-isothermal oxidation behavior to simulate real-world engine conditions.
-
Machine Learning Integration: Expanding machine learning models to predict long-term oxidation behavior and guide alloy design.
-
Hybrid Processing: Combining surface treatments like LSP and HIP to achieve synergistic improvements in oxidation resistance.
Conclusion
The high-temperature oxidation behavior of TA15 titanium alloy is a complex interplay of kinetics, oxide scale formation, microstructural changes, and mechanical property evolution. While TA15 exhibits good oxidation resistance at 500–600 °C, severe oxidation above 700 °C necessitates advanced surface treatments and alloying strategies to enhance performance. Through detailed experimental studies and modeling, researchers have elucidated the mechanisms governing oxidation, paving the way for optimized applications in aerospace and beyond. Continued advancements in coatings, alloy design, and predictive modeling will further expand the utility of TA15 in high-temperature environments, ensuring its role as a cornerstone material in modern engineering.
Reprint Statement: If there are no special instructions, all articles on this site are original. Please indicate the source for reprinting:https://www.cncmachiningptj.com/,thanks!
PTJ® provides a full range of Custom Precision cnc machining china services.ISO 9001:2015 &AS-9100 certified. 3, 4 and 5-axis rapid precision CNC machining services including milling, turning to customer specifications,Capable of metal & plastic machined parts with +/-0.005 mm tolerance.Secondary services include CNC and conventional grinding, drilling,die casting,sheet metal and stamping.Providing prototypes, full production runs, technical support and full inspection.Serves the automotive, aerospace, mold&fixture,led lighting,medical,bicycle, and consumer electronics industries. On-time delivery.Tell us a little about your project's budget and expected delivery time. We will strategize with you to provide the most cost-effective services to help you reach your target,Welcome to Contact us ( sales@pintejin.com ) directly for your new project.
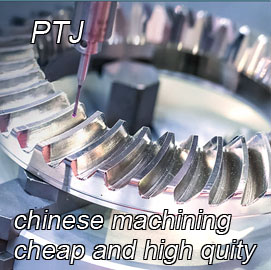
- 5 Axis Machining
- Cnc Milling
- Cnc Turning
- Machining Industries
- Machining Process
- Surface Treatment
- Metal Machining
- Plastic Machining
- Powder Metallurgy Mold
- Die Casting
- Parts Gallery
- Auto Metal Parts
- Machinery Parts
- LED Heatsink
- Building Parts
- Mobile Parts
- Medical Parts
- Electronic Parts
- Tailored Machining
- Bicycle Parts
- Aluminum Machining
- Titanium Machining
- Stainless Steel Machining
- Copper Machining
- Brass Machining
- Super Alloy Machining
- Peek Machining
- UHMW Machining
- Unilate Machining
- PA6 Machining
- PPS Machining
- Teflon Machining
- Inconel Machining
- Tool Steel Machining
- More Material