CNC Micro-Function Optimization Grinding Process
The CNC (Computer Numerical Control) micro-function optimization grinding process represents a sophisticated advancement in precision manufacturing, integrating computer-controlled machinery with advanced grinding techniques to achieve unparalleled accuracy, efficiency, and surface quality at the microscale. Grinding, as a subtractive manufacturing process, involves the removal of material from a workpiece using an abrasive tool, typically a grinding wheel, to produce a finished part with precise dimensions and a smooth finish. The incorporation of CNC technology into this process allows for the automation and optimization of grinding parameters, enabling the production of components with tolerances in the micrometer (μm) range or even sub-micron levels. Micro-function optimization refers to the fine-tuning of this process to address specific functional requirements at a microscopic level, such as minimizing surface roughness, enhancing geometric accuracy, or reducing thermal damage in small-scale components.
This process is particularly significant in industries requiring high-precision parts, such as aerospace, medical device manufacturing, optics, and microelectronics. The ability to optimize grinding at a micro level distinguishes it from traditional grinding methods, which often prioritize bulk material removal over precision at such fine scales. By leveraging CNC systems, manufacturers can program complex tool paths, adjust cutting parameters in real-time, and incorporate feedback mechanisms to ensure consistent quality. The evolution of this technology reflects broader trends in manufacturing toward automation, sustainability, and the production of increasingly miniaturized components.
Historical Context and Development
The origins of grinding as a manufacturing technique date back millennia, with early examples including the manual sharpening of tools using natural abrasives like sandstone. The industrial revolution in the 19th century introduced mechanized grinding machines, significantly improving efficiency and consistency. However, it was the advent of numerical control (NC) in the mid-20th century, followed by the development of CNC in the 1970s, that revolutionized precision machining. CNC technology, driven by advancements in computer programming and microprocessor capabilities, enabled the precise control of machine tools, transforming grinding from a labor-intensive process into a highly automated one.
The concept of micro-function optimization emerged later, in the late 20th and early 21st centuries, as industries demanded components with smaller features and tighter tolerances. Traditional grinding methods struggled to meet these requirements due to limitations in tool precision, thermal management, and process control. The integration of CNC into micro-grinding processes addressed these challenges by allowing for the dynamic adjustment of parameters such as wheel speed, feed rate, and depth of cut. Early research in this field focused on optimizing grinding wheels with finer abrasive grains (e.g., diamond or cubic boron nitride, CBN) and developing mathematical models to predict outcomes at the microscale.
By the 1990s, advancements in sensor technology and real-time monitoring systems further enhanced CNC micro-grinding, enabling adaptive control strategies that respond to variables like tool wear and workpiece temperature. Today, the process is supported by sophisticated software, including computer-aided design (CAD) and computer-aided manufacturing (CAM), which facilitate the simulation and optimization of grinding operations before physical execution.
Principles of CNC Grinding
At its core, CNC grinding relies on the interaction between a rotating abrasive wheel and a workpiece, controlled by a CNC system that interprets programmed instructions (typically in G-code) to dictate tool movements. The grinding wheel, composed of abrasive particles bonded in a matrix, removes material through a combination of cutting, plowing, and rubbing actions. In the context of micro-function optimization, the process is tailored to achieve specific outcomes at a microscopic level, such as reducing surface irregularities or ensuring dimensional accuracy within a few micrometers.
The CNC system provides several key advantages over manual or conventional grinding:
- Precision: Automated control ensures repeatability and accuracy, critical for microscale features.
- Flexibility: Programs can be adjusted to accommodate different workpiece geometries and materials.
- Efficiency: Optimization algorithms reduce cycle times and material waste.
Micro-function optimization builds on these principles by focusing on the fine details of the grinding process. This includes selecting the appropriate abrasive grain size (often below 20 μm), controlling the contact pressure between the wheel and workpiece, and minimizing thermal effects that could distort delicate microstructures. The process often involves multiple stages, such as roughing (bulk material removal) and finishing (surface refinement), each optimized separately to balance speed and precision.
Key Components and Technologies
The CNC micro-function optimization grinding process depends on several critical components and technologies, each contributing to its effectiveness:
CNC Machine Tools
CNC grinding machines vary in design, including surface grinders, cylindrical grinders, and centerless grinders, but all share a common framework: a spindle to hold the grinding wheel, a workpiece holder, and a multi-axis motion system controlled by servo motors. For micro-grinding, machines are often equipped with high-precision spindles capable of speeds exceeding 50,000 RPM and resolution down to nanometers.
Grinding Wheels
The choice of grinding wheel is pivotal in micro-function optimization. Wheels with ultra-fine abrasives (e.g., diamond or CBN with grain sizes of 1-10 μm) are preferred for their ability to produce smooth surfaces and precise geometries. The wheel’s bond type (e.g., vitrified, resin, or metal) and structure (open or dense) also influence performance, affecting factors like heat dissipation and chip clearance.
Control Systems and Software
Modern CNC systems integrate advanced software for process planning and optimization. CAD/CAM software translates design specifications into tool paths, while optimization algorithms (e.g., genetic algorithms or NSGA-II) adjust parameters to minimize cost, time, or environmental impact. Real-time monitoring systems, using sensors for force, temperature, and vibration, enable adaptive control, ensuring stability and quality during grinding.
Coolants and Lubricants
Thermal management is critical in micro-grinding due to the risk of heat-induced damage to small features. Coolants, such as water-based emulsions or minimum quantity lubrication (MQL) systems, reduce friction and heat buildup, preserving workpiece integrity. Optimization often involves balancing coolant flow with environmental considerations, such as reducing fluid waste.
Process Parameters and Optimization Techniques
The success of CNC micro-function optimization grinding hinges on the careful selection and adjustment of process parameters. These parameters interact in complex ways, requiring sophisticated optimization techniques to achieve desired outcomes.
Primary Parameters
- Wheel Speed (RPM): Higher speeds increase material removal rates but may generate excessive heat. Typical micro-grinding speeds range from 10,000 to 100,000 RPM.
- Feed Rate (mm/min): The rate at which the workpiece moves relative to the wheel affects surface finish and cycle time. Micro-grinding often uses low feed rates (e.g., 1-10 mm/min) to ensure precision.
- Depth of Cut (μm): Shallow cuts (e.g., 1-5 μm) are common in micro-grinding to minimize subsurface damage and maintain accuracy.
- Workpiece Speed (RPM): In cylindrical grinding, the workpiece rotation speed influences the grinding zone dynamics.
Optimization Methods
Several techniques are employed to optimize these parameters:
- Taguchi Method: Uses orthogonal arrays to identify the most influential factors with minimal experiments.
- Response Surface Methodology (RSM): Models the relationship between inputs and outputs (e.g., surface roughness, grinding time) to find optimal settings.
- Genetic Algorithms (GA): Mimics natural selection to iteratively improve parameter combinations, balancing multiple objectives like cost and quality.
- Non-Dominated Sorting Genetic Algorithm II (NSGA-II): A multi-objective optimization tool that generates a Pareto front of solutions, allowing trade-offs between conflicting goals (e.g., precision vs. efficiency).
Example Table: Parameter Comparison
Parameter | Traditional Grinding | Micro-Function Optimized Grinding | Impact on Outcome |
---|---|---|---|
Wheel Speed (RPM) | 5,000-20,000 | 20,000-100,000 | Higher precision, heat risk |
Feed Rate (mm/min) | 50-200 | 1-10 | Smoother finish, slower process |
Depth of Cut (μm) | 10-50 | 1-5 | Reduced damage, finer control |
Grain Size (μm) | 20-100 | 1-10 | Improved surface quality |
Applications in Industry
The CNC micro-function optimization grinding process finds applications across diverse sectors, driven by the need for precision and miniaturization.
Aerospace
In aerospace, micro-grinding is used to manufacture turbine blades, fuel injectors, and other components with complex geometries and tight tolerances (e.g., ±2 μm). The process ensures high surface integrity, critical for fatigue resistance in high-stress environments.
Medical Devices
Micro-grinding produces surgical tools, implants, and microfluidic devices with features as small as 10 μm. Optimization ensures biocompatibility by minimizing surface defects that could harbor bacteria.
Optics and Photonics
The production of glass lenses, mirrors, and fiber optic components relies on micro-grinding to achieve sub-micron surface finishes (e.g., Ra < 10 nm). Deterministic grinding techniques, supported by CNC, ensure repeatability in optical quality.
Microelectronics
Semiconductor manufacturing uses micro-grinding to shape wafers and dies, where precision at the nanometer scale is essential. Optimization reduces defects that could impair circuit performance.
Challenges and Limitations
Despite its advantages, CNC micro-function optimization grinding faces several challenges:
- Thermal Management: Heat generation at micro scales can cause burns or distortions, necessitating advanced cooling strategies.
- Tool Wear: Fine abrasive wheels wear quickly, requiring frequent dressing and increasing costs.
- Machine Stiffness: Low stiffness in small tools or machines can lead to deflection, compromising accuracy.
- Complexity: Optimizing multiple parameters for microscale features demands significant computational resources and expertise.
Future Directions
The future of CNC micro-function optimization grinding lies in integrating emerging technologies:
- Artificial Intelligence (AI): Machine learning models can predict optimal parameters and detect anomalies in real-time.
- Sustainability: Low-carbon grinding processes, using energy-efficient machines and eco-friendly coolants, align with global environmental goals.
- Nanogrinding: Advances in abrasives and machine precision may push tolerances into the nanometer range.
Reprint Statement: If there are no special instructions, all articles on this site are original. Please indicate the source for reprinting:https://www.cncmachiningptj.com/,thanks!
PTJ® provides a full range of Custom Precision cnc machining china services.ISO 9001:2015 &AS-9100 certified. 3, 4 and 5-axis rapid precision CNC machining services including milling, turning to customer specifications,Capable of metal & plastic machined parts with +/-0.005 mm tolerance.Secondary services include CNC and conventional grinding, drilling,die casting,sheet metal and stamping.Providing prototypes, full production runs, technical support and full inspection.Serves the automotive, aerospace, mold&fixture,led lighting,medical,bicycle, and consumer electronics industries. On-time delivery.Tell us a little about your project's budget and expected delivery time. We will strategize with you to provide the most cost-effective services to help you reach your target,Welcome to Contact us ( sales@pintejin.com ) directly for your new project.
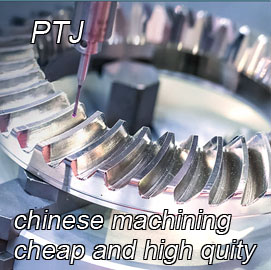
- 5 Axis Machining
- Cnc Milling
- Cnc Turning
- Machining Industries
- Machining Process
- Surface Treatment
- Metal Machining
- Plastic Machining
- Powder Metallurgy Mold
- Die Casting
- Parts Gallery
- Auto Metal Parts
- Machinery Parts
- LED Heatsink
- Building Parts
- Mobile Parts
- Medical Parts
- Electronic Parts
- Tailored Machining
- Bicycle Parts
- Aluminum Machining
- Titanium Machining
- Stainless Steel Machining
- Copper Machining
- Brass Machining
- Super Alloy Machining
- Peek Machining
- UHMW Machining
- Unilate Machining
- PA6 Machining
- PPS Machining
- Teflon Machining
- Inconel Machining
- Tool Steel Machining
- More Material