Research on the 5-Axis Machining of Blisks
The machining of blisks (bladed disks), integral components in modern aerospace engines, represents a pinnacle of advanced manufacturing technology. Blisks, which combine a rotor disk and blades into a single unit, are critical in jet engines and gas turbines due to their enhanced aerodynamic efficiency, reduced weight, and elimination of mechanical joints found in traditional blade-and-disk assemblies. The complexity of their geometry, coupled with the use of high-strength, difficult-to-machine materials like titanium alloys and nickel-based superalloys, necessitates the use of 5-axis machining—a sophisticated process that allows simultaneous control of five degrees of freedom to achieve precise, intricate cuts. Research into 5-axis machining of blisks has evolved significantly since the technology’s adoption in the 1980s, driven by demands for improved performance, efficiency, and cost-effectiveness in aerospace manufacturing. This article explores the history, methodologies, tools, strategies, challenges, and recent advancements in this field, supported by detailed comparative tables.
Historical Development of Blisk Machining
The concept of the blisk emerged as a response to the limitations of traditional turbine rotor designs, where individual blades were mechanically attached to a disk via dovetail or fir-tree joints. These joints, while effective, introduced weight penalties, aerodynamic inefficiencies, and potential failure points due to fretting fatigue. The blisk, first introduced in the mid-1980s by Sermatech-Lehr (now GKN Aerospace) for the T700 helicopter engine’s compressors, offered a monolithic alternative. Early manufacturing relied on basic milling techniques, but the complexity of blisk geometries—featuring twisted, thin-walled blades with tight tolerances—quickly outstripped the capabilities of 3-axis machining.
The advent of 5-axis machining in the late 20th century marked a turning point. Unlike 3-axis systems, which move a tool along the X, Y, and Z axes, 5-axis machines add two rotational axes (typically A and B or A and C), enabling the tool or workpiece to tilt and rotate. This flexibility allowed manufacturers to access difficult-to-reach areas of the blisk, such as the narrow channels between blades, and to maintain optimal cutting angles. Initial research focused on adapting existing CNC (computer numerical control) systems to handle 5-axis operations, with companies like General Electric and Rolls-Royce pioneering its use in high-pressure compressor stages.
By the 1990s, 5-axis machining had become the standard for blisk production, supported by advancements in CAD/CAM (computer-aided design/computer-aided manufacturing) software. Early studies emphasized toolpath generation, cutter selection, and machine dynamics, laying the groundwork for modern research into efficiency, precision, and surface integrity.
Principles of 5-Axis Machining
5-axis machining involves the simultaneous movement of a cutting tool or workpiece along five axes: three linear (X, Y, Z) and two rotational (e.g., A rotating about X, and C about Z, in a trunnion-style machine). This configuration contrasts with 3+2 machining, where the rotational axes are fixed during cutting, limiting continuous motion. For blisks, simultaneous 5-axis motion is essential to navigate the complex, freeform surfaces of blades and hubs.
The process begins with a solid billet—typically titanium (e.g., Ti-6Al-4V) or a nickel alloy (e.g., Inconel 718)—which is progressively machined into the final blisk shape. Key stages include roughing (removing bulk material), semi-finishing (refining the shape), and finishing (achieving final tolerances and surface quality). Each stage requires tailored toolpaths, cutters, and parameters to optimize material removal rates (MRR), tool life, and part accuracy.
The primary advantage of 5-axis machining for blisks is its ability to maintain the tool’s cutting edge perpendicular to the workpiece surface, reducing deflection and improving surface finish. This is particularly critical for thin-walled blades, where vibration and distortion are significant concerns. Research has focused on optimizing these parameters to balance productivity and quality, often leveraging simulation tools like VERICUT or PowerMill to predict outcomes before cutting begins.
Tooling and Cutter Technologies
The choice of cutting tools is a cornerstone of 5-axis blisk machining research. Blisks’ materials—characterized by high hardness, low thermal conductivity, and work-hardening tendencies—demand tools with exceptional durability and heat resistance. Common cutter types include:
- Solid Carbide End Mills: Widely used for roughing and finishing due to their rigidity and precision. Variants with multiple flutes and variable helix angles (e.g., Iscar’s Chatterfree tools) reduce vibration and enhance MRR.
- Ball Nose End Mills: Traditional for finishing, these tools excel at contouring curved surfaces but require more passes due to their small effective cutting radius.
- Barrel Cutters: A newer innovation, barrel cutters feature a large-radius cutting edge, allowing wider stepovers and fewer passes, significantly reducing cycle times. Studies by Starrag and Autodesk report up to 75% time savings in blade finishing.
- Tapered Tools: Combining stability and reach, these are ideal for deep channels and thin blades, minimizing deflection.
Tool coatings, such as titanium aluminum nitride (TiAlN) or diamond-like carbon (DLC), enhance wear resistance, while coolant strategies (e.g., high-pressure through-tool coolant) manage heat and chip evacuation. Research continues to explore hybrid tools and custom geometries tailored to specific blisk designs.
Machining Strategies
Several strategies have emerged to address the unique challenges of blisk machining, each with distinct advantages and trade-offs. These include:
Plunge Milling
Plunge milling involves axial tool entry to remove material from deep, narrow channels—a common feature in open blisks. Research demonstrates its superiority over traditional flank milling for roughing, with studies showing up to 50% higher MRR due to reduced lateral forces. The technique uses a ruled surface to approximate blade contours, followed by toolpath generation via double-point offset methods.
Trochoidal Milling
Trochoidal milling employs circular toolpath patterns to maintain constant tooth load, ideal for rough-slotting nickel alloys. Starrag’s optimized strategy uses three trochoidal passes, improving tool life and reducing cycle times by up to 25% compared to linear milling.
Spiral Milling
For finishing thin-walled blades, spiral toolpaths link tool center curves and axis drive curves, accounting for residual stress-induced distortion. Experimental validation shows improved surface uniformity and reduced chatter, critical for aerodynamic performance.
Multi-Milling
A hybrid approach, multi-milling combines disc milling (for bulk removal), plunge milling (for channel shaping), and side milling (for corner finishing). Research using UG software on a fan blisk reported a threefold efficiency increase over traditional methods.
Electrochemical Machining (ECM) Integration
While not purely 5-axis, ECM is sometimes paired with milling for finishing. Studies on titanium alloys (e.g., Ti60) show ECM achieving surface finishes of 0.05 Ra without thermal damage, complementing 5-axis roughing.
Challenges in 5-Axis Blisk Machining
Despite its advantages, 5-axis machining of blisks faces several challenges:
- Geometric Complexity: Twisted blades and narrow inter-blade gaps limit tool access, requiring long, slender tools prone to deflection.
- Material Properties: Titanium and nickel alloys generate high cutting forces and heat, accelerating tool wear and risking workpiece damage.
- Vibration and Chatter: Thin blades are susceptible to vibration, degrading surface quality and accuracy.
- Toolpath Optimization: Generating collision-free, efficient toolpaths demands advanced CAM software and skilled programmers.
- Cost and Time: High material costs and long machining times (often 100+ hours per blisk) drive research into cycle time reduction.
Recent studies address these through adaptive machining (adjusting toolpaths based on measured geometry), hybrid processes (e.g., milling with laser cladding), and machine learning for predictive maintenance.
Recent Advancements
Advancements in 5-axis blisk machining reflect interdisciplinary innovation:
- Barrel Cutter Adoption: Autodesk’s 2021 study reduced machining time by 74% using barrel cutters and optimized toolpaths, validated on a titanium blisk.
- Multi-Spindle Machines: A 2020 design featuring eight radially arranged spindles improved efficiency by machining multiple blades simultaneously, with kinematic analysis showing enhanced workspace flexibility.
- Adaptive Machining: Techniques using in-process measurement (e.g., ZEISS PRISMO) adjust toolpaths to compensate for distortion, achieving tolerances below 80 microns.
- Software Enhancements: PowerMill’s Blade, Blisk, and Impeller (BBI) module offers collision avoidance and smoothing algorithms, cutting programming time by 30%.
- Hybrid Processes: Combining 5-axis milling with abrasive flow machining (AFM) or EDM (electrical discharge machining) improves surface integrity, with research showing roughness reductions from 0.8 Ra to 0.2 Ra.
Comparative Analysis
Tables below compare key aspects of 5-axis blisk machining strategies and tools, based on recent research findings.
Table 1: Comparison of Machining Strategies
Strategy | Material Removal Rate (MRR) | Cycle Time Reduction | Surface Finish (Ra) | Tool Life | Applications |
---|---|---|---|---|---|
Plunge Milling | High (50% > flank milling) | Moderate (20–30%) | 0.8–1.2 μm | Moderate | Roughing deep channels |
Trochoidal Milling | High | High (25–40%) | 0.6–1.0 μm | High | Rough-slotting Ni-alloys |
Spiral Milling | Moderate | Low (10–15%) | 0.2–0.4 μm | High | Finishing thin blades |
Multi-Milling | Very High (3x traditional) | High (50–60%) | 0.6–0.8 μm | Moderate | Full blisk processing |
ECM Integration | Low | Low (5–10%) | 0.05–0.1 μm | Very High | Finishing Ti-alloys |
Table 2: Comparison of Cutting Tools
Tool Type | Cutting Speed (m/min) | Stepover (mm) | Depth of Cut (mm) | Wear Rate | Best Use Case |
---|---|---|---|---|---|
Solid Carbide | 50–100 | 0.5–1.0 | 1–3 | Moderate | Roughing/F finishing |
Ball Nose | 30–80 | 0.1–0.5 | 0.5–2 | High | Finishing curved surfaces |
Barrel Cutter | 60–120 | 1.0–2.0 | 3–4 | Low | High-efficiency finishing |
Tapered Tool | 40–90 | 0.5–1.0 | 2–3 | Moderate | Deep channel machining |
Table 3: Performance Metrics Across Materials
Material | MRR (cm³/min) | Tool Life (min) | Surface Finish (Ra) | Machining Time (hr) |
---|---|---|---|---|
Ti-6Al-4V | 20–40 | 60–120 | 0.4–0.8 μm | 70–100 |
Inconel 718 | 15–30 | 40–90 | 0.6–1.0 μm | 80–120 |
Nickel Superalloy | 10–25 | 30–70 | 0.5–0.9 μm | 90–150 |
Future Directions
Research into 5-axis blisk machining continues to evolve, with several promising areas:
- Automation and AI: Machine learning models predict tool wear and optimize parameters in real-time, potentially reducing costs by 20–30%.
- Additive Manufacturing Integration: Hybrid processes combining 3D printing with 5-axis milling could produce near-net-shape blisks, minimizing machining time.
- Sustainability: Efforts to reduce energy consumption and waste (e.g., via dry machining or recycled coolant) align with aerospace’s green initiatives.
- Ultra-Precision: Advances in metrology and control systems aim for tolerances below 10 microns, driven by next-generation engine designs.
Conclusion
The 5-axis machining of blisks exemplifies the intersection of engineering ingenuity and manufacturing precision. From its origins in the 1980s to cutting-edge innovations in the 2020s, research has transformed blisk production into a highly efficient, reliable process. While challenges like tool wear and geometric complexity persist, advancements in tooling, strategies, and software continue to push boundaries. As aerospace demands escalate, ongoing studies will likely yield even greater efficiencies, ensuring blisks remain at the heart of high-performance engines.
Reprint Statement: If there are no special instructions, all articles on this site are original. Please indicate the source for reprinting:https://www.cncmachiningptj.com/,thanks!
3, 4 and 5-axis precision CNC machining services for aluminum machining, beryllium, carbon steel, magnesium, titanium machining, Inconel, platinum, superalloy, acetal, polycarbonate, fiberglass, graphite and wood. Capable of machining parts up to 98 in. turning dia. and +/-0.001 in. straightness tolerance. Processes include milling, turning, drilling, boring, threading, tapping, forming, knurling, counterboring, countersinking, reaming and laser cutting. Secondary services such as assembly, centerless grinding, heat treating, plating and welding. Prototype and low to high volume production offered with maximum 50,000 units. Suitable for fluid power, pneumatics, hydraulics and valve applications. Serves the aerospace, aircraft, military, medical and defense industries.PTJ will strategize with you to provide the most cost-effective services to help you reach your target,Welcome to Contact us ( sales@pintejin.com ) directly for your new project.
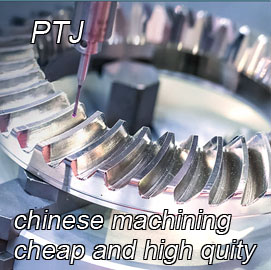
- 5 Axis Machining
- Cnc Milling
- Cnc Turning
- Machining Industries
- Machining Process
- Surface Treatment
- Metal Machining
- Plastic Machining
- Powder Metallurgy Mold
- Die Casting
- Parts Gallery
- Auto Metal Parts
- Machinery Parts
- LED Heatsink
- Building Parts
- Mobile Parts
- Medical Parts
- Electronic Parts
- Tailored Machining
- Bicycle Parts
- Aluminum Machining
- Titanium Machining
- Stainless Steel Machining
- Copper Machining
- Brass Machining
- Super Alloy Machining
- Peek Machining
- UHMW Machining
- Unilate Machining
- PA6 Machining
- PPS Machining
- Teflon Machining
- Inconel Machining
- Tool Steel Machining
- More Material