The generation of high precision aspherical surfaces in glass by CNC machining
The generation of high precision aspherical surfaces in glass by computer numerical control (CNC) machining represents a significant advancement in optical manufacturing technology. Aspherical surfaces, unlike their spherical counterparts, deviate from a simple spherical curvature, offering superior optical performance by reducing aberrations such as spherical aberration and coma. These surfaces are critical in applications ranging from astronomical telescopes and high-resolution cameras to laser systems and medical imaging devices. CNC machining, a process that utilizes computer-controlled tools to shape materials with exceptional accuracy, has emerged as a cornerstone technique for producing these complex geometries in glass, a material prized for its optical clarity and stability but challenging to machine due to its brittleness and hardness.
Historically, the production of aspherical glass surfaces relied on labor-intensive manual grinding and polishing, processes that were time-consuming, costly, and heavily dependent on the skill of individual craftsmen. The advent of CNC machining in the late 20th century revolutionized this field by introducing automation, repeatability, and precision unattainable through traditional methods. This article explores the principles, techniques, challenges, and advancements in generating high precision aspherical surfaces in glass using CNC machining, delving into the material properties of glass, the mechanics of CNC systems, and the evolving technologies that have made this process a standard in modern optical fabrication.
Historical Context of Aspherical Surface Fabrication
The pursuit of aspherical surfaces in optics dates back to the 17th century when scientists like René Descartes and Christiaan Huygens recognized their potential to improve lens performance. However, the practical realization of such surfaces remained elusive until the 20th century. Early attempts involved hand-crafted methods where opticians used specialized tools to grind and polish glass into non-spherical shapes. These techniques, while effective for small-scale production, were impractical for mass manufacturing due to their inconsistency and high labor costs.
The introduction of numerically controlled machines in the 1950s, driven by advancements in computing and automation, marked a turning point. By the 1980s, CNC machining had begun to penetrate the optical industry, with initial applications focused on metals and plastics. Adapting this technology to glass required overcoming significant hurdles, including the material’s propensity for cracking and the need for ultra-fine surface finishes. Pioneering work by researchers such as D.J. Nicholas and J.E. Boon in 1981 demonstrated the feasibility of using CNC machining to generate aspherical glass surfaces, laying the groundwork for subsequent innovations.
Principles of CNC Machining for Aspherical Surfaces
CNC machining operates on the principle of subtractive manufacturing, where material is removed from a workpiece to achieve the desired shape. In the context of aspherical glass surfaces, this involves a series of precisely controlled movements guided by computer programs, typically encoded in G-code, which dictate the position, speed, and path of cutting tools. Unlike traditional machining, which relies on manual adjustments, CNC systems use multi-axis configurations—commonly 3, 4, or 5 axes—to navigate the complex curvatures of aspherical surfaces.
For glass, the process typically employs diamond-based tools due to their hardness and ability to maintain sharp edges under high loads. The machining sequence generally includes rough grinding to approximate the aspherical shape, followed by fine grinding and polishing to achieve optical quality. Key parameters such as tool speed, feed rate, and depth of cut must be optimized to minimize subsurface damage (SSD) and ensure surface accuracy within nanometer tolerances.
Material Properties of Glass in CNC Machining
Glass, as a machining substrate, presents unique challenges and advantages. Optically, it is valued for its transparency, low thermal expansion, and ability to maintain shape under varying conditions, making it ideal for precision optics. Common glass types used in aspherical machining include:
- Borosilicate Glass: Known for its thermal resistance and durability, often used in laboratory and astronomical optics.
- Fused Silica: Offers exceptional optical clarity and resistance to thermal shock, favored in high-precision applications like laser optics.
- Soda-Lime Glass: A cost-effective option for less demanding applications, though less durable than alternatives.
Mechanically, glass is brittle, with a hardness ranging from 5 to 7 on the Mohs scale, necessitating specialized tooling and techniques to prevent cracking or chipping. Its amorphous structure lacks the ductility of metals, meaning material removal occurs through brittle fracture rather than plastic deformation. This property increases the risk of SSD—microcracks beneath the surface that can degrade optical performance if not removed through subsequent polishing.
Table 1 compares the properties of common optical glasses relevant to CNC machining:
Glass Type | Hardness (Mohs) | Thermal Expansion (10⁻⁶/K) | Refractive Index | Typical Applications |
---|---|---|---|---|
Borosilicate | 5.5–6 | 3.3 | 1.47 | Telescopes, Lab Equipment |
Fused Silica | 6–7 | 0.55 | 1.46 | Laser Optics, UV Systems |
Soda-Lime | 5–5.5 | 8.6 | 1.52 | Consumer Optics, Windows |
N-BK7 | 6 | 7.1 | 1.52 | Precision Lenses, Prisms |
CNC Machining Techniques for Aspherical Glass Surfaces
Several CNC-based techniques have been developed to generate aspherical surfaces in glass, each tailored to specific requirements of precision, efficiency, and surface quality.
Diamond Grinding
Diamond grinding is the primary method for shaping aspherical surfaces. Using diamond-impregnated wheels or single-point diamond tools, this technique removes material through abrasive action. Multi-axis CNC machines interpolate tool paths to follow the aspheric profile, with 4- or 5-axis systems enabling complex geometries like off-axis parabolas. The process is divided into:
- Rough Grinding: Uses coarse diamond grits (e.g., 20–40 μm) to rapidly shape the surface, accepting higher SSD levels.
- Fine Grinding: Employs finer grits (e.g., 5–10 μm) to refine the shape and reduce SSD, preparing the surface for polishing.
Ultrasonic Machining
Ultrasonic machining enhances grinding by superimposing high-frequency vibrations (20–40 kHz) on the tool. This reduces cutting forces and SSD, improving surface quality. It is particularly effective for hard glasses like fused silica and ceramics, though it is slower and costlier than conventional grinding.
High-Speed Cutting (HSC)
HSC uses high spindle speeds (up to 100,000 RPM) and small depth-of-cut increments to minimize thermal and mechanical stress. This technique, often paired with diamond tools, achieves near-optical finishes directly from the machining stage, reducing polishing time.
Polishing Post-Machining
While CNC grinding can achieve submicron form accuracy, optical surfaces require nanometer-scale roughness (e.g., <1 nm RMS). Post-machining polishing, often using CNC-controlled bonnet tools or magnetorheological finishing (MRF), removes residual SSD and refines the surface. MRF, for instance, uses a magnetic fluid with abrasive particles to selectively polish high spots, achieving wavefront errors below λ/10.
Challenges in CNC Machining of Aspherical Glass Surfaces
Despite its advantages, CNC machining of aspherical glass surfaces faces several challenges:
Tool Wear
Diamond tools, though exceptionally hard, wear over time due to glass’s abrasiveness. Wear alters tool geometry, compromising precision and necessitating frequent tool changes or in-process compensation algorithms.
Subsurface Damage
Brittle fracture during machining introduces SSD, which can propagate under thermal or mechanical stress, degrading optical performance. Minimizing SSD requires careful control of grinding parameters and extensive polishing, increasing production time.
Thermal Effects
High-speed machining generates heat, risking thermal cracks in glass. Cooling systems using water or oil-based fluids are employed, but their application must balance thermal management with contamination risks.
Metrology
Verifying aspherical surfaces demands advanced metrology, such as interferometry or profilometry, capable of measuring nanometer-scale deviations. Large-diameter or steeply curved surfaces pose additional challenges, often requiring custom fixtures or stitching techniques.
Advancements in CNC Technology for Aspherical Surfaces
Recent decades have seen significant innovations in CNC machining tailored to aspherical glass fabrication:
Multi-Axis Systems
The shift from 3-axis to 5-axis CNC machines has enabled greater flexibility in tool orientation, allowing the machining of steep aspheres and freeform surfaces. True 5-axis systems, with simultaneous control of X, Y, Z, and two rotational axes (A and C), offer unparalleled precision.
Software Integration
Advanced CAD/CAM software translates aspheric designs into executable tool paths, incorporating real-time compensation for tool wear and thermal effects. Simulation tools predict SSD and surface errors, optimizing parameters before machining begins.
Hybrid Processes
Combining CNC grinding with techniques like laser-assisted machining or ion beam figuring enhances efficiency. Laser preheating, for example, softens glass locally, reducing cutting forces, while ion beam figuring provides sub-nanometer corrections post-grinding.
Metrology Integration
On-machine metrology, such as coordinate measuring machines (CMM) or laser interferometers integrated into CNC systems, allows real-time feedback, reducing the need for separate inspection steps and improving throughput.
Applications of CNC-Machined Aspherical Glass Surfaces
CNC-machined aspherical glass surfaces are integral to numerous high-precision applications:
Astronomical Optics
Large telescopes, such as the Hubble Space Telescope, rely on aspherical mirrors to capture faint light from distant galaxies with minimal distortion. CNC machining enables the production of meter-scale optics with submicron accuracy.
Laser Systems
High-power lasers in medical and industrial settings use aspherical lenses to focus beams with minimal aberration, enhancing efficiency and precision. Fused silica aspheres, machined via CNC, are common in these systems.
Consumer Electronics
Smartphone cameras and virtual reality headsets incorporate compact aspherical lenses to improve image quality in small form factors, a feat made scalable by CNC automation.
Medical Imaging
Endoscopes and diagnostic devices use aspherical optics to achieve high-resolution imaging within the body, benefiting from CNC’s ability to produce intricate, biocompatible components.
Table 2 compares CNC-machined aspherical surfaces across applications:
Application | Glass Type | Diameter (mm) | Surface Accuracy (λ) | Roughness (nm RMS) | Key Requirement |
---|---|---|---|---|---|
Astronomical Mirrors | Fused Silica | 500–2000 | λ/20 | <1 | Low Wavefront Error |
Laser Lenses | N-BK7 | 10–50 | λ/10 | <2 | High Damage Threshold |
Smartphone Cameras | Soda-Lime | 5–15 | λ/4 | <5 | Cost-Effectiveness |
Endoscopic Optics | Borosilicate | 2–10 | λ/8 | <3 | Biocompatibility |
Comparative Analysis: CNC Machining vs. Alternative Methods
CNC machining is one of several methods for producing aspherical glass surfaces, each with distinct advantages and limitations:
Precision Glass Molding (PGM)
PGM involves pressing softened glass into an aspheric mold at high temperatures. It excels in mass production, offering short cycle times and low per-unit costs. However, it struggles with large diameters (>50 mm) and ultra-high precision due to mold wear and thermal shrinkage.
Single-Point Diamond Turning (SPDT)
SPDT uses a diamond-tipped lathe to cut aspherical surfaces, achieving exceptional smoothness without polishing. While ideal for small optics and infrared materials, it is less effective for brittle glasses like fused silica and scales poorly for large batches.
Manual Grinding and Polishing
Traditional methods provide unmatched flexibility for custom, low-volume optics but lack repeatability and efficiency, making them obsolete for modern demands.
Table 3 compares these methods:
Method | Precision (λ) | Diameter Range (mm) | Production Rate | Cost per Unit | SSD Depth (μm) |
---|---|---|---|---|---|
CNC Machining | λ/20–λ/4 | 5–2000 | Medium | Moderate | 1–5 |
PGM | λ/10–λ/2 | 5–50 | High | Low | 0.5–2 |
SPDT | λ/50–λ/10 | 5–100 | Low | High | <1 |
Manual Methods | λ/10–λ/2 | 5–500 | Very Low | Very High | 5–10 |
Future Directions in CNC Machining of Aspherical Surfaces
The future of CNC machining for aspherical glass surfaces lies in continued integration of automation, artificial intelligence (AI), and advanced materials. AI-driven process optimization could dynamically adjust machining parameters to minimize SSD and tool wear, while robotic systems might handle larger, more complex workpieces. Developments in diamond tool coatings, such as nanocrystalline diamond, promise extended tool life and finer finishes. Additionally, hybrid CNC systems combining subtractive and additive techniques (e.g., 3D printing of glass preforms) could streamline production, reducing waste and energy use.
Sustainability is another emerging focus, with research into recycling glass swarf and reducing coolant use gaining traction. As optical systems demand ever-higher precision—driven by fields like quantum computing and space exploration—CNC machining will likely evolve to meet tolerances below λ/100, pushing the boundaries of what is mechanically possible.
Conclusion
The generation of high precision aspherical surfaces in glass by CNC machining has transformed optical manufacturing, bridging the gap between theoretical design and practical realization. By leveraging multi-axis control, diamond tooling, and advanced software, this technology achieves unparalleled accuracy and repeatability, making it indispensable across scientific, industrial, and consumer domains. While challenges like tool wear and SSD persist, ongoing innovations in machinery, metrology, and process control continue to refine its capabilities. As CNC machining advances, it will remain a cornerstone of optical engineering, enabling the next generation of high-performance aspherical optics.
Reprint Statement: If there are no special instructions, all articles on this site are original. Please indicate the source for reprinting:https://www.cncmachiningptj.com/,thanks!
PTJ® provides a full range of Custom Precision cnc machining china services.ISO 9001:2015 &AS-9100 certified. 3, 4 and 5-axis rapid precision CNC machining services including milling, turning to customer specifications,Capable of metal & plastic machined parts with +/-0.005 mm tolerance.Secondary services include CNC and conventional grinding, drilling,die casting,sheet metal and stamping.Providing prototypes, full production runs, technical support and full inspection.Serves the automotive, aerospace, mold&fixture,led lighting,medical,bicycle, and consumer electronics industries. On-time delivery.Tell us a little about your project's budget and expected delivery time. We will strategize with you to provide the most cost-effective services to help you reach your target,Welcome to Contact us ( sales@pintejin.com ) directly for your new project.
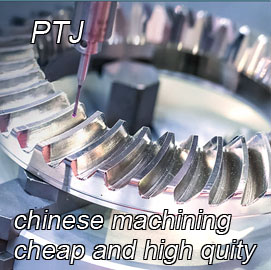
- 5 Axis Machining
- Cnc Milling
- Cnc Turning
- Machining Industries
- Machining Process
- Surface Treatment
- Metal Machining
- Plastic Machining
- Powder Metallurgy Mold
- Die Casting
- Parts Gallery
- Auto Metal Parts
- Machinery Parts
- LED Heatsink
- Building Parts
- Mobile Parts
- Medical Parts
- Electronic Parts
- Tailored Machining
- Bicycle Parts
- Aluminum Machining
- Titanium Machining
- Stainless Steel Machining
- Copper Machining
- Brass Machining
- Super Alloy Machining
- Peek Machining
- UHMW Machining
- Unilate Machining
- PA6 Machining
- PPS Machining
- Teflon Machining
- Inconel Machining
- Tool Steel Machining
- More Material