Introduction to Regional Classification and CNC Machining of Complex Surfaces
Computer Numerical Control (CNC) machining represents a cornerstone of modern manufacturing, enabling the precise production of intricate components across industries such as aerospace, automotive, medical, and consumer electronics. When applied to complex surfaces—those characterized by non-linear geometries, variable curvatures, and multidimensional features—CNC machining demands advanced strategies to ensure accuracy, efficiency, and repeatability. One such strategy is regional classification, a methodological approach that segments complex surfaces into distinct zones based on geometric, functional, or machining-specific criteria. This article explores the interplay between regional classification and CNC machining, delving into their theoretical underpinnings, practical applications, and technological advancements. By examining the processes, tools, and challenges involved, we aim to provide a comprehensive resource for understanding this critical intersection of engineering and manufacturing science.
Complex surfaces, often defined mathematically as freeform or parametric surfaces, pose unique challenges to traditional machining techniques. Unlike planar or simple cylindrical geometries, these surfaces require multi-axis machining capabilities, sophisticated toolpath planning, and adaptive control systems. Regional classification enhances this process by breaking down the surface into manageable sub-regions, each tailored to specific machining parameters. This approach not only improves precision but also optimizes tool wear, reduces machining time, and enhances surface finish quality. Over the following sections, we will dissect the principles of regional classification, the mechanics of CNC machining for complex surfaces, and the synergies that arise from their integration.
Fundamentals of Complex Surfaces in Manufacturing
Complex surfaces are ubiquitous in modern design, appearing in turbine blades, orthopedic implants, automotive body panels, and architectural molds. Mathematically, these surfaces are often represented using Non-Uniform Rational B-Splines (NURBS), Bézier curves, or other parametric models within Computer-Aided Design (CAD) software. Their defining characteristics include continuous curvature changes, high aspect ratios, and, in some cases, topological discontinuities such as holes or sharp edges. These properties necessitate advanced machining techniques beyond the capabilities of traditional 3-axis CNC systems.
In CNC machining, complex surfaces are typically processed using 5-axis or higher multi-axis machines, which allow the tool to approach the workpiece from multiple angles. This flexibility is critical for maintaining constant contact between the cutting tool and the surface, avoiding collisions, and achieving uniform material removal. However, the complexity of these surfaces introduces variables such as tool orientation, cutting speed, feed rate, and surface tolerance, all of which must be meticulously controlled.
Regional classification addresses these challenges by segmenting the surface into regions based on criteria such as curvature, accessibility, or material properties. For example, a turbine blade might be divided into the airfoil (high curvature), root (structural transition), and platform (flat base). Each region can then be machined with tailored strategies, such as varying tool sizes, cutting angles, or step-over distances. This segmentation enhances the adaptability of CNC machining to the unique demands of complex geometries.
Principles of Regional Classification
Regional classification is a systematic process that involves analyzing a complex surface and dividing it into sub-regions based on predefined attributes. These attributes can be geometric (e.g., curvature, slope, or boundary conditions), functional (e.g., load-bearing zones or aesthetic surfaces), or process-driven (e.g., tool accessibility or machining constraints). The goal is to simplify the machining process by reducing the variability within each region, allowing for optimized toolpaths and parameters.
Phase 1: Surface Analysis and Segmentation
The first phase of regional classification involves surface analysis, typically performed within CAD/CAM software. Algorithms such as Gaussian curvature analysis, principal curvature computation, or mesh segmentation are employed to identify distinct zones. For instance, a surface with a mix of convex and concave areas might be split into regions where curvature exceeds a threshold value (e.g., |K| > 0.1 mm⁻¹). Alternatively, accessibility analysis might classify regions based on whether a tool can reach them without interference.
Phase 2: Region Characterization
Once segmented, each region is characterized by its geometric and machining properties. This includes determining the maximum and minimum curvature, surface normal vectors, and boundary conditions. For example, a region with tight curvature might require a smaller ball-end mill, while a flatter region could accommodate a larger flat-end mill for faster material removal. This phase often involves simulation to predict tool behavior and identify potential issues such as gouging or undercutting.
Phase 3: Machining Strategy Assignment
The final phase assigns a machining strategy to each region. Common strategies include zigzag toolpaths for flat areas, spiral toolpaths for curved surfaces, and contour-parallel paths for steep slopes. Parameters such as feed rate, spindle speed, and depth of cut are adjusted to suit the region’s characteristics. This tailored approach ensures that the CNC machine operates within its optimal performance envelope, balancing precision and efficiency.
CNC Machining Techniques for Complex Surfaces
CNC machining of complex surfaces relies on a combination of hardware, software, and operational expertise. Multi-axis machines, typically 5-axis or 7-axis, are the backbone of this process, offering simultaneous control over translational (X, Y, Z) and rotational (A, B, or C) axes. These machines use a variety of cutting tools—ball-end mills, tapered mills, and lollipop cutters—to sculpt intricate geometries from materials ranging from aluminum and titanium to composites and ceramics.
Toolpath Generation
Toolpath generation is a critical aspect of CNC machining for complex surfaces. CAM software translates the CAD model into a series of machine instructions, defining the tool’s trajectory across the surface. Common toolpath strategies include:
- Z-Level Machining: The tool moves in horizontal planes, incrementally stepping down the Z-axis. Ideal for steep surfaces.
- Flowline Machining: The tool follows the surface’s natural curvature, minimizing abrupt direction changes.
- Isoparametric Machining: Toolpaths align with the surface’s parametric curves (e.g., U or V directions in NURBS), ensuring smooth transitions.
Regional classification enhances toolpath generation by allowing different strategies to be applied to different zones. For example, a flowline path might be used on a curved region, while a Z-level path is applied to an adjacent steep wall.
Tool Selection and Optimization
Tool selection is influenced by the surface’s geometry and the desired finish. Ball-end mills, with their spherical tips, are versatile for freeform surfaces but leave cusp heights proportional to their radius. Smaller tools reduce cusps but increase machining time. Regional classification mitigates this trade-off by matching tool size to region-specific requirements. For instance, a 10 mm ball-end mill might rough a broad region, while a 2 mm mill finishes a tight corner.
Machining Parameters
Key parameters include spindle speed (RPM), feed rate (mm/min), and depth of cut (mm). These are adjusted based on material properties, tool geometry, and surface complexity. For example, titanium requires lower speeds and feeds to prevent overheating, while aluminum allows higher rates for faster machining. Regional classification ensures that parameters are optimized for each zone, preventing tool wear or surface defects.
Integration of Regional Classification with CNC Machining
The synergy between regional classification and CNC machining lies in their combined ability to address the inherent challenges of complex surfaces. By dividing the surface into manageable zones, regional classification simplifies toolpath planning, reduces computational overhead, and enhances machining precision. This integration is particularly valuable in industries requiring tight tolerances, such as aerospace (e.g., ±0.01 mm for turbine blades) or medical (e.g., ±0.005 mm for implants).
Case Study: Turbine Blade Machining
Consider a turbine blade with a twisted airfoil, a thick root, and a flat platform. Without regional classification, a single toolpath strategy might struggle to accommodate the blade’s varying geometry, leading to inefficiencies or errors. By applying regional classification:
- Airfoil Region: High curvature requires a 5-axis spiral toolpath with a 6 mm ball-end mill, slow feed rate (500 mm/min), and shallow depth of cut (0.2 mm).
- Root Region: Moderate curvature allows a Z-level path with a 10 mm tapered mill, higher feed rate (800 mm/min), and deeper cut (0.5 mm).
- Platform Region: Flat geometry suits a zigzag path with a 12 mm flat-end mill, fast feed rate (1200 mm/min), and aggressive cut (1 mm).
This tailored approach reduces machining time by 20-30% compared to uniform strategies, as validated by simulations and shop-floor data.
Comparative Analysis: With vs. Without Regional Classification
Parameter | Without Regional Classification | With Regional Classification |
---|---|---|
Toolpath Complexity | High (single strategy for entire surface) | Moderate (strategy per region) |
Machining Time | 120 min | 90 min |
Tool Wear | Uneven (excessive in tight areas) | Balanced (optimized per region) |
Surface Finish | Ra 1.6 µm (variable) | Ra 0.8 µm (consistent) |
Tolerance Achieved | ±0.05 mm | ±0.02 mm |
Advanced Technologies in Regional Classification and CNC Machining
Recent advancements have further refined the integration of regional classification and CNC machining. Machine learning algorithms, for instance, can automate surface segmentation by training on datasets of complex geometries, predicting optimal region boundaries based on historical machining outcomes. Similarly, real-time adaptive control systems adjust parameters dynamically during machining, responding to sensor feedback on tool vibration, temperature, or surface deviation.
Additive-Subtractive Hybrid Processes
Hybrid manufacturing, combining additive (e.g., 3D printing) and subtractive (e.g., CNC machining) techniques, benefits from regional classification. A part might be printed with excess material in certain regions, then machined to final tolerances. Classification ensures that subtractive operations target only the necessary zones, minimizing waste.
Simulation and Digital Twins
Digital twin technology simulates the entire machining process, from regional classification to toolpath execution. By creating a virtual replica of the workpiece and machine, engineers can optimize strategies before cutting begins, reducing trial-and-error costs. For complex surfaces, this is invaluable for predicting tool life and surface quality.
Challenges and Future Directions
Despite its advantages, regional classification and CNC machining face challenges. Segmentation algorithms may struggle with highly irregular surfaces, leading to suboptimal region boundaries. Multi-axis machining introduces risks of collision or kinematic singularities, requiring robust error-checking. Additionally, the computational cost of analyzing and planning for complex surfaces can be prohibitive for small-scale manufacturers.
Future developments may include:
- AI-Driven Classification: Fully autonomous systems that adaptively refine regions during machining.
- High-Speed Machining: Enhanced spindles and tools to reduce time without sacrificing precision.
- Sustainable Practices: Optimizing regional strategies to minimize energy use and material waste.
Conclusion
Regional classification and CNC machining of complex surfaces represent a powerful symbiosis in modern manufacturing. By breaking down intricate geometries into manageable zones, this approach unlocks new levels of precision, efficiency, and flexibility. As technology evolves, the integration of advanced algorithms, hybrid processes, and real-time controls will further elevate its capabilities, ensuring its relevance in the production of tomorrow’s most demanding components.
Reprint Statement: If there are no special instructions, all articles on this site are original. Please indicate the source for reprinting:https://www.cncmachiningptj.com/,thanks!
3, 4 and 5-axis precision CNC machining services for aluminum machining, beryllium, carbon steel, magnesium, titanium machining, Inconel, platinum, superalloy, acetal, polycarbonate, fiberglass, graphite and wood. Capable of machining parts up to 98 in. turning dia. and +/-0.001 in. straightness tolerance. Processes include milling, turning, drilling, boring, threading, tapping, forming, knurling, counterboring, countersinking, reaming and laser cutting. Secondary services such as assembly, centerless grinding, heat treating, plating and welding. Prototype and low to high volume production offered with maximum 50,000 units. Suitable for fluid power, pneumatics, hydraulics and valve applications. Serves the aerospace, aircraft, military, medical and defense industries.PTJ will strategize with you to provide the most cost-effective services to help you reach your target,Welcome to Contact us ( sales@pintejin.com ) directly for your new project.
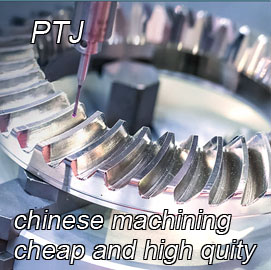
- 5 Axis Machining
- Cnc Milling
- Cnc Turning
- Machining Industries
- Machining Process
- Surface Treatment
- Metal Machining
- Plastic Machining
- Powder Metallurgy Mold
- Die Casting
- Parts Gallery
- Auto Metal Parts
- Machinery Parts
- LED Heatsink
- Building Parts
- Mobile Parts
- Medical Parts
- Electronic Parts
- Tailored Machining
- Bicycle Parts
- Aluminum Machining
- Titanium Machining
- Stainless Steel Machining
- Copper Machining
- Brass Machining
- Super Alloy Machining
- Peek Machining
- UHMW Machining
- Unilate Machining
- PA6 Machining
- PPS Machining
- Teflon Machining
- Inconel Machining
- Tool Steel Machining
- More Material