The Effect Of Shear Temperature On Turning Of GH4169 Nickel-Based Superalloy
The effect of shear temperature on the turning of GH4169 nickel-based superalloy is a critical aspect of machining science, influencing tool wear, surface integrity, and overall machinability. GH4169, commonly referred to as Inconel 718, is a precipitation-hardened nickel-chromium superalloy known for its exceptional strength, corrosion resistance, and high-temperature performance. These properties, while advantageous for aerospace, nuclear, and automotive applications, pose significant challenges in machining due to work hardening, low thermal conductivity, and high cutting forces.
Shear temperature, which arises from plastic deformation and friction between the cutting tool and workpiece, plays a crucial role in determining the cutting process's efficiency and quality. During turning operations, the heat generated in the primary, secondary, and tertiary deformation zones affects chip formation, tool wear mechanisms, and the microstructural evolution of the machined surface.
Influence of Shear Temperature on Tool Wear
Tool wear is a major concern when machining GH4169 due to its tendency to cause rapid degradation of cutting tools. Shear temperature exacerbates this issue by accelerating diffusion, oxidation, and adhesive wear mechanisms. At elevated temperatures, the diffusion of elements such as cobalt, titanium, and aluminum from the superalloy into the cutting tool material leads to reduced tool life. Carbide tools, commonly used for turning GH4169, experience crater wear and flank wear due to excessive heat, necessitating the use of coated tools or advanced tool materials such as polycrystalline cubic boron nitride (PCBN) or ceramic inserts.
Effect on Chip Morphology and Formation
Shear temperature significantly influences chip morphology in the turning of GH4169. Due to its work-hardening nature, GH4169 often produces serrated or segmented chips, which are a direct consequence of localized shear banding. The high shear temperature softens the material in certain regions, leading to periodic shearing and chip segmentation. This phenomenon affects cutting forces, tool vibrations, and surface finish. Proper control of cutting parameters, such as speed, feed rate, and depth of cut, is essential to mitigate the adverse effects of excessive shear temperature on chip formation.
Surface Integrity and Microstructural Evolution
The surface integrity of machined GH4169 components is highly sensitive to shear temperature. Elevated temperatures induce tensile residual stresses, phase transformations, and grain refinement in the subsurface layer. The presence of heat-affected zones (HAZ) can lead to microstructural changes, such as the dissolution of precipitates or formation of undesirable phases, which may compromise mechanical properties. Therefore, optimizing cutting conditions to balance heat generation and dissipation is critical for achieving high-quality surfaces.
Thermal Management Strategies
To control shear temperature during turning, several strategies can be employed. High-pressure coolant systems effectively reduce cutting zone temperature and improve chip evacuation. Additionally, the use of minimum quantity lubrication (MQL) with nano-lubricants has shown promise in reducing tool wear and enhancing surface quality. Cryogenic machining, wherein liquid nitrogen or carbon dioxide is used as a coolant, further minimizes heat buildup and mitigates thermal softening of the workpiece material.
Advanced Modeling of Shear Temperature
Finite element modeling (FEM) is widely used to predict shear temperature distribution in machining GH4169. These models incorporate material properties, thermal conductivity, strain hardening, and cutting tool geometry to simulate temperature gradients and stress fields. Experimental validation of FEM predictions using infrared thermography or thermocouples provides deeper insights into optimizing machining parameters for reduced thermal damage.
Conclusion
The effect of shear temperature on the turning of GH4169 nickel-based superalloy is a multifaceted problem involving tool wear, chip formation, surface integrity, and thermal management. Understanding and controlling shear temperature is essential to improving machinability and extending tool life. Further research into advanced cooling techniques, tool coatings, and process modeling will enhance the efficiency of machining GH4169 for critical applications.
Reprint Statement: If there are no special instructions, all articles on this site are original. Please indicate the source for reprinting:https://www.cncmachiningptj.com/,thanks!
3, 4 and 5-axis precision CNC machining services for aluminum machining, beryllium, carbon steel, magnesium, titanium machining, Inconel, platinum, superalloy, acetal, polycarbonate, fiberglass, graphite and wood. Capable of machining parts up to 98 in. turning dia. and +/-0.001 in. straightness tolerance. Processes include milling, turning, drilling, boring, threading, tapping, forming, knurling, counterboring, countersinking, reaming and laser cutting. Secondary services such as assembly, centerless grinding, heat treating, plating and welding. Prototype and low to high volume production offered with maximum 50,000 units. Suitable for fluid power, pneumatics, hydraulics and valve applications. Serves the aerospace, aircraft, military, medical and defense industries.PTJ will strategize with you to provide the most cost-effective services to help you reach your target,Welcome to Contact us ( sales@pintejin.com ) directly for your new project.
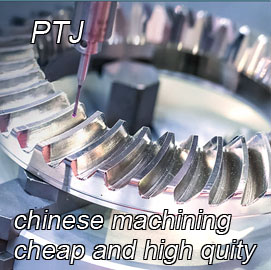
- 5 Axis Machining
- Cnc Milling
- Cnc Turning
- Machining Industries
- Machining Process
- Surface Treatment
- Metal Machining
- Plastic Machining
- Powder Metallurgy Mold
- Die Casting
- Parts Gallery
- Auto Metal Parts
- Machinery Parts
- LED Heatsink
- Building Parts
- Mobile Parts
- Medical Parts
- Electronic Parts
- Tailored Machining
- Bicycle Parts
- Aluminum Machining
- Titanium Machining
- Stainless Steel Machining
- Copper Machining
- Brass Machining
- Super Alloy Machining
- Peek Machining
- UHMW Machining
- Unilate Machining
- PA6 Machining
- PPS Machining
- Teflon Machining
- Inconel Machining
- Tool Steel Machining
- More Material