The impact of 3D laser cutting technology on car body panels
3D laser cutting technology has emerged as a transformative force in the automotive industry, particularly in the fabrication of car body panels. This advanced manufacturing process leverages high-powered lasers guided by computer numerical control (CNC) systems to cut complex three-dimensional shapes with exceptional precision. Unlike traditional two-dimensional (2D) cutting methods, which are limited to flat sheets, 3D laser cutting enables the processing of pre-formed components, intricate geometries, and a wide range of materials used in modern vehicle design. Its adoption has revolutionized the production of car body panels, offering improvements in accuracy, efficiency, material utilization, and design flexibility. This article examines the scientific principles behind 3D laser cutting, its historical development, its specific applications in car body panel manufacturing, and its broader implications for the automotive sector. Detailed comparison tables are included to illustrate its advantages over conventional methods and to highlight its impact on performance metrics.
The origins of laser cutting can be traced back to the 1960s, when the first laser cutting machine was developed by the Western Electric Engineering Research Center in 1965 for drilling holes in diamond dies. Early systems relied on carbon dioxide (CO₂) lasers, which were limited in power and primarily suited for cutting non-metals or thin metal sheets. By the late 1970s, the automotive industry began experimenting with laser cutting for specialized applications, such as prototyping and low-volume production. The introduction of fiber lasers in the early 2000s marked a significant leap forward, offering higher efficiency, smaller focal diameters, and the ability to process reflective metals like aluminum and copper—materials increasingly critical for lightweight vehicle designs. The transition to 3D laser cutting, facilitated by advancements in robotics and CNC technology, allowed manufacturers to move beyond flat sheet processing to directly cut pre-formed or tubular components, a capability that proved particularly valuable for car body panels.
Car body panels, which include exterior components such as doors, hoods, roofs, and fenders, are essential to a vehicle’s structural integrity, aerodynamics, and aesthetic appeal. Traditionally, these panels were fabricated using mechanical methods like stamping, shearing, and punching, often followed by manual trimming or grinding to achieve the desired shape. These processes, while effective for mass production, were labor-intensive, prone to tool wear, and limited in their ability to handle complex geometries or advanced materials. The advent of 3D laser cutting addressed these shortcomings by introducing a non-contact, thermally-based cutting method that uses a focused laser beam to melt, vaporize, or burn through material along a programmed path. The beam, typically generated by a fiber laser with a wavelength of approximately 1.06 micrometers, is directed by a multi-axis cutting head capable of moving in three-dimensional space, allowing it to follow the contours of pre-formed panels with micron-level precision.
The scientific foundation of 3D laser cutting lies in the interaction between the laser beam and the material being processed. When the beam strikes the surface of a car body panel—typically made of steel, aluminum, or composite materials—it delivers a concentrated energy flux, raising the local temperature above the material’s melting or vaporization point. For steel, with a melting point of approximately 1,370°C, a fiber laser operating at 2–6 kilowatts can achieve cutting speeds of up to 20 meters per minute, depending on thickness. An assist gas, such as nitrogen or oxygen, is often injected coaxially with the beam to eject molten material from the kerf (the cut width), ensuring a clean edge. Oxygen enhances cutting speed in ferrous metals by initiating an exothermic reaction, while nitrogen is preferred for aluminum to prevent oxidation and maintain surface quality. The kerf width, typically ranging from 0.1 to 0.5 millimeters, is significantly narrower than that of mechanical cutting methods, reducing material waste and improving dimensional accuracy.
One of the most significant impacts of 3D laser cutting on car body panels is its ability to process complex geometries. Modern vehicle designs increasingly feature aerodynamic curves, sharp angles, and integrated features like window frames or mounting points, which are challenging to produce using traditional stamping alone. For example, a door panel may require precise cutouts for hinges, locks, and wiring channels, all of which must align perfectly during assembly. 3D laser cutting excels in this context because its multi-axis cutting head can tilt and rotate to access hard-to-reach areas, cutting directly into a pre-formed panel without the need for secondary fixtures or manual intervention. This flexibility is enhanced by CAD/CAM integration, where digital models of the panel are translated into cutting paths, ensuring repeatability and minimizing human error.
Material versatility is another key advantage of 3D laser cutting in car body panel production. The automotive industry has shifted toward lightweight materials to improve fuel efficiency and meet stringent emissions standards. Aluminum, with a density of 2.7 g/cm³ compared to steel’s 7.8 g/cm³, is now widely used in body panels for electric vehicles (EVs) and luxury cars. However, aluminum’s high reflectivity and thermal conductivity make it difficult to cut with traditional CO₂ lasers, which operate at a wavelength of 10.6 micrometers. Fiber lasers, with their shorter wavelength and higher absorption rate in metals, overcome these challenges, enabling clean, distortion-free cuts in aluminum panels up to 25 millimeters thick. High-strength steels, such as dual-phase or boron-alloyed varieties, are also increasingly common in safety-critical areas like door frames and roof rails. 3D laser cutting accommodates these materials by adjusting power and assist gas parameters, ensuring consistent quality across diverse alloys.
The precision of 3D laser cutting has profound implications for the structural integrity and safety of car body panels. In crash scenarios, the accuracy of joints and cutouts can influence how energy is dissipated through the vehicle’s frame. For instance, a roof panel with laser-cut mounting holes can be aligned with sub-millimeter precision, reducing gaps that might compromise weld strength. Studies have shown that laser-cut components exhibit tolerances as tight as ±0.1 millimeters, compared to ±0.5 millimeters or more for mechanical methods. This precision minimizes mismatches during assembly, enhancing the vehicle’s rigidity and crashworthiness. Furthermore, the absence of physical contact eliminates tool-induced stresses or micro-cracks, which can weaken panels over time.
Efficiency and cost-effectiveness are additional benefits of 3D laser cutting in car body panel manufacturing. Traditional stamping requires dedicated dies for each panel design, entailing high upfront costs and long lead times—often several months—to produce and refine. In contrast, 3D laser cutting is a tool-less process, relying solely on software adjustments to switch between designs. This agility is particularly valuable for prototyping and low-volume production, such as custom panels for luxury or performance vehicles. For example, a manufacturer can reprogram a 3D laser cutting system to produce a new hood design in hours, compared to weeks for die fabrication. Even in high-volume scenarios, the technology’s speed and minimal setup time reduce production bottlenecks, while its narrow kerf optimizes material usage, lowering scrap rates by up to 20% compared to punching or shearing.
The environmental impact of 3D laser cutting is also noteworthy. By reducing material waste and eliminating the need for consumable tools like punches or blades, the process aligns with the automotive industry’s push toward sustainability. Fiber lasers, which dominate modern 3D cutting systems, are more energy-efficient than their CO₂ predecessors, converting up to 40% of electrical input into usable beam energy compared to 10–15% for CO₂ lasers. Additionally, the ability to nest parts closely on a sheet—facilitated by the laser’s precision—further minimizes raw material consumption. For electric vehicle manufacturers, where lightweighting is critical to extending range, 3D laser cutting supports the use of thinner, stronger panels without sacrificing durability, indirectly reducing the energy required for propulsion.
To quantify the impact of 3D laser cutting on car body panels, consider the following comparison tables, which juxtapose its performance against traditional methods across key metrics:
Table 1: Comparison of Cutting Methods for Car Body Panels
Metric | 3D Laser Cutting | Stamping | Shearing |
---|---|---|---|
Precision (Tolerance) | ±0.1 mm | ±0.5 mm | ±1.0 mm |
Kerf Width | 0.1–0.5 mm | N/A (die-dependent) | 1–3 mm |
Max Thickness (Steel) | 25 mm | 6 mm | 10 mm |
Setup Time | Minutes (software-based) | Weeks (die fabrication) | Hours (tool adjustment) |
Material Waste | 5–10% | 15–25% | 20–30% |
Complex Geometry | High (3D capable) | Limited (2D only) | Very Limited |
Tool Wear | None (non-contact) | High (dies degrade) | Moderate (blades dull) |
Energy Efficiency | 30–40% (fiber laser) | N/A (mechanical) | N/A (mechanical) |
Table 2: Material Processing Capabilities
Material | 3D Laser Cutting Speed (m/min) | Stamping Feasibility | Shearing Feasibility |
---|---|---|---|
Mild Steel (2 mm) | 15–20 | High | High |
High-Strength Steel (2 mm) | 10–15 | Moderate | Low |
Aluminum (2 mm) | 20–25 | Moderate | High |
Stainless Steel (2 mm) | 12–18 | High | Moderate |
These tables underscore the superiority of 3D laser cutting in precision, flexibility, and waste reduction, though stamping retains an edge in sheer throughput for mass production of simple shapes. However, as vehicle designs grow more intricate and material diversity increases, the advantages of 3D laser cutting become more pronounced.
The technology’s impact extends beyond production to influence design and innovation in car body panels. Designers can now explore shapes and features that were previously unfeasible, such as integrated stiffeners or aerodynamic contours, without worrying about manufacturing constraints. For instance, the Tesla Model S features aluminum body panels with laser-cut perforations for weight reduction, a design made possible by 3D laser cutting’s precision. Similarly, high-performance vehicles like the Ferrari 488 employ laser-cut steel reinforcements in their chassis, balancing strength and weight savings. This freedom has spurred a wave of creativity, enabling automakers to differentiate their products in a competitive market.
Despite its advantages, 3D laser cutting is not without challenges. The initial investment in equipment—often exceeding $500,000 for a high-end system—can be prohibitive for smaller manufacturers. Operating costs, including electricity and assist gas, also add to the expense, though these are offset by long-term savings in material and labor. Thermal effects, such as heat-affected zones (HAZs), can alter the microstructure of sensitive alloys, potentially reducing fatigue life if not properly managed. Advanced systems mitigate this by optimizing cutting parameters, such as reducing power near edges or using pulsed beams to limit heat input. Additionally, the technology requires skilled operators and robust maintenance to ensure consistent performance, particularly in 24/7 production environments.
Looking forward, the role of 3D laser cutting in car body panel manufacturing is poised to expand. The integration of artificial intelligence (AI) and Industry 4.0 principles promises to enhance its capabilities further. AI-driven systems can analyze real-time data from sensors to adjust cutting speed, power, and gas flow dynamically, optimizing quality and efficiency. Robotics advancements will likely increase automation, enabling fully autonomous cutting cells that handle everything from material loading to finished part inspection. As electric and autonomous vehicles dominate the market, the demand for lightweight, precisely engineered panels will grow, cementing 3D laser cutting’s status as a cornerstone technology.
In conclusion, 3D laser cutting has fundamentally reshaped the production of car body panels, offering a blend of precision, versatility, and efficiency that traditional methods cannot match. Its ability to handle complex geometries, diverse materials, and stringent tolerances has elevated the quality and safety of modern vehicles while reducing costs and environmental impact. As the automotive industry evolves, this technology will continue to drive innovation, enabling manufacturers to meet the challenges of tomorrow’s mobility landscape. The data presented in the comparison tables highlights its transformative potential, making it an indispensable tool in the quest for better, safer, and more sustainable cars.
Reprint Statement: If there are no special instructions, all articles on this site are original. Please indicate the source for reprinting:https://www.cncmachiningptj.com/,thanks!
3, 4 and 5-axis precision CNC machining services for aluminum machining, beryllium, carbon steel, magnesium, titanium machining, Inconel, platinum, superalloy, acetal, polycarbonate, fiberglass, graphite and wood. Capable of machining parts up to 98 in. turning dia. and +/-0.001 in. straightness tolerance. Processes include milling, turning, drilling, boring, threading, tapping, forming, knurling, counterboring, countersinking, reaming and laser cutting. Secondary services such as assembly, centerless grinding, heat treating, plating and welding. Prototype and low to high volume production offered with maximum 50,000 units. Suitable for fluid power, pneumatics, hydraulics and valve applications. Serves the aerospace, aircraft, military, medical and defense industries.PTJ will strategize with you to provide the most cost-effective services to help you reach your target,Welcome to Contact us ( sales@pintejin.com ) directly for your new project.
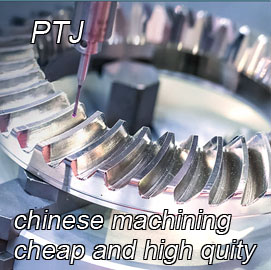
- 5 Axis Machining
- Cnc Milling
- Cnc Turning
- Machining Industries
- Machining Process
- Surface Treatment
- Metal Machining
- Plastic Machining
- Powder Metallurgy Mold
- Die Casting
- Parts Gallery
- Auto Metal Parts
- Machinery Parts
- LED Heatsink
- Building Parts
- Mobile Parts
- Medical Parts
- Electronic Parts
- Tailored Machining
- Bicycle Parts
- Aluminum Machining
- Titanium Machining
- Stainless Steel Machining
- Copper Machining
- Brass Machining
- Super Alloy Machining
- Peek Machining
- UHMW Machining
- Unilate Machining
- PA6 Machining
- PPS Machining
- Teflon Machining
- Inconel Machining
- Tool Steel Machining
- More Material