Design and Implementation of a Network CNC System Based on Industrial Ethernet
Computer Numerical Control (CNC) systems play a pivotal role in modern manufacturing, offering precision and automation that enhance productivity and efficiency. With the advent of Industry 4.0, networking CNC systems has become essential for integrating manufacturing processes, real-time monitoring, and data-driven decision-making. Among various communication technologies, Industrial Ethernet has emerged as the most viable solution due to its reliability, high-speed data transfer, and interoperability with existing automation systems. This article presents a comprehensive study on the design and implementation of a network CNC system based on Industrial Ethernet, detailing the architecture, communication protocols, hardware and software components, and comparative performance analysis with conventional CNC networking solutions.
CNC System Architecture in Industrial Ethernet Environment
The architecture of a networked CNC system involves multiple layers, including hardware components, communication infrastructure, and software integration. A robust Industrial Ethernet-based CNC system comprises:
-
CNC Machines: These include milling machines, lathes, grinders, and multi-axis machining centers equipped with Ethernet-enabled controllers.
-
Industrial Ethernet Switches: These switches facilitate communication between CNC machines, supervisory computers, and cloud-based analytics platforms.
-
Supervisory Control System: A central control station that monitors and manages CNC machines over the network.
-
Human-Machine Interfaces (HMI): Interfaces that provide real-time data visualization and control functionalities.
-
Industrial Protocols: Such as EtherCAT, PROFINET, and Ethernet/IP, which govern data exchange and interoperability.
-
Cloud and Edge Computing Integration: For predictive maintenance, remote diagnostics, and advanced data analytics.
Communication Protocols for Network CNC Systems
Industrial Ethernet encompasses several communication protocols, each with unique characteristics tailored for different applications. The following table compares key Industrial Ethernet protocols used in CNC networking:
Protocol | Data Rate | Real-Time Capability | Jitter | Deterministic Behavior | Application in CNC Systems |
---|---|---|---|---|---|
EtherCAT | Up to 100 Mbps | High | Low | Yes | High-speed motion control, synchronized multi-axis systems |
PROFINET | 100 Mbps to 1 Gbps | Medium to High | Medium | Yes | Factory automation, CNC networking |
Ethernet/IP | 10 Mbps to 1 Gbps | Medium | High | No | General automation, device-to-cloud communication |
Modbus TCP | 10 Mbps to 100 Mbps | Low | High | No | Legacy system integration, basic CNC data exchange |
Among these protocols, EtherCAT is the most widely used in high-performance CNC applications due to its ultra-low latency and precise synchronization capabilities.
Hardware Components of Networked CNC Systems
Implementing a networked CNC system based on Industrial Ethernet requires specific hardware components to ensure seamless operation. These include:
-
Ethernet-Enabled CNC Controllers: Equipped with real-time Ethernet interfaces to facilitate high-speed data exchange.
-
Ethernet Switches and Routers: Industrial-grade switches with support for VLANs and Quality of Service (QoS) ensure reliable communication.
-
Sensors and Actuators: Smart sensors provide real-time feedback for process optimization.
-
Edge Computing Devices: Process critical data at the machine level, reducing reliance on central servers.
-
Cloud Connectivity Modules: Enable data transmission to cloud platforms for remote monitoring and analytics.
Software Components and Implementation
The software architecture of a networked CNC system includes:
-
Real-Time Operating Systems (RTOS): Ensuring deterministic execution of machining tasks.
-
Industrial SCADA and MES Software: Supervisory Control and Data Acquisition (SCADA) and Manufacturing Execution Systems (MES) enable monitoring and process optimization.
-
CNC Programming and Simulation Software: Supports G-code interpretation and virtual machining for pre-production validation.
-
AI-Based Predictive Maintenance Algorithms: Utilizing machine learning to analyze sensor data and predict failures.
Performance Analysis and Comparative Study
To evaluate the effectiveness of Industrial Ethernet-based CNC systems, the following parameters were analyzed:
Parameter | Traditional Serial Communication (RS-232) | Industrial Ethernet (EtherCAT) |
Data Transfer Rate | 115.2 kbps | 100 Mbps |
Real-Time Performance | Low | High |
Scalability | Limited | High |
Jitter | High | Low |
Multi-Axis Synchronization | Poor | Excellent |
Remote Monitoring Capability | Limited | Extensive |
Results indicate that Industrial Ethernet significantly enhances the real-time performance, scalability, and data-handling capabilities of CNC systems.
Conclusion
The transition from conventional CNC networking methods to Industrial Ethernet-based solutions has revolutionized the manufacturing landscape. By leveraging high-speed communication, real-time control, and cloud integration, networked CNC systems enhance precision, efficiency, and predictive maintenance capabilities. Future research should focus on integrating AI-driven process optimization, blockchain security for data integrity, and 5G-enhanced Industrial Ethernet for ultra-reliable low-latency communication (URLLC).
This study serves as a foundational reference for manufacturers and researchers aiming to implement advanced networked CNC solutions in industrial settings.
Reprint Statement: If there are no special instructions, all articles on this site are original. Please indicate the source for reprinting:https://www.cncmachiningptj.com/,thanks!
3, 4 and 5-axis precision CNC machining services for aluminum machining, beryllium, carbon steel, magnesium, titanium machining, Inconel, platinum, superalloy, acetal, polycarbonate, fiberglass, graphite and wood. Capable of machining parts up to 98 in. turning dia. and +/-0.001 in. straightness tolerance. Processes include milling, turning, drilling, boring, threading, tapping, forming, knurling, counterboring, countersinking, reaming and laser cutting. Secondary services such as assembly, centerless grinding, heat treating, plating and welding. Prototype and low to high volume production offered with maximum 50,000 units. Suitable for fluid power, pneumatics, hydraulics and valve applications. Serves the aerospace, aircraft, military, medical and defense industries.PTJ will strategize with you to provide the most cost-effective services to help you reach your target,Welcome to Contact us ( sales@pintejin.com ) directly for your new project.
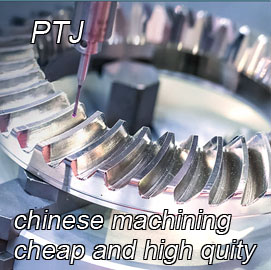
- 5 Axis Machining
- Cnc Milling
- Cnc Turning
- Machining Industries
- Machining Process
- Surface Treatment
- Metal Machining
- Plastic Machining
- Powder Metallurgy Mold
- Die Casting
- Parts Gallery
- Auto Metal Parts
- Machinery Parts
- LED Heatsink
- Building Parts
- Mobile Parts
- Medical Parts
- Electronic Parts
- Tailored Machining
- Bicycle Parts
- Aluminum Machining
- Titanium Machining
- Stainless Steel Machining
- Copper Machining
- Brass Machining
- Super Alloy Machining
- Peek Machining
- UHMW Machining
- Unilate Machining
- PA6 Machining
- PPS Machining
- Teflon Machining
- Inconel Machining
- Tool Steel Machining
- More Material