The Manufacturing Technology Of Martensitic Stainless Steel Medical Device Parts
Martensitic stainless steel is a category of stainless steel alloys characterized by a body-centered tetragonal (BCT) crystal structure, which imparts high strength, hardness, and moderate corrosion resistance. These properties make martensitic stainless steels particularly suitable for manufacturing medical device parts, such as surgical instruments, dental tools, and certain orthopedic implants. The processing technology of martensitic stainless steel for medical applications involves a complex interplay of metallurgy, heat treatment, forming techniques, surface finishing, and quality control measures, all tailored to meet stringent biocompatibility, durability, and performance standards. This article explores the processing technologies employed in fabricating martensitic stainless steel medical device parts, delving into alloy compositions, heat treatment methods, machining processes, surface treatments, and their scientific underpinnings, supported by detailed comparison tables.
Composition and Metallurgical Characteristics
Martensitic stainless steels belong to the 400-series of stainless steels, as designated by the Society of Automotive Engineers (SAE). They typically contain 11.5–18% chromium and 0.1–1.2% carbon, with optional additions of nickel, molybdenum, or other elements to enhance specific properties. The high carbon content enables the formation of martensite—a hard, brittle phase—through rapid cooling from elevated temperatures, while chromium provides corrosion resistance by forming a passive chromium oxide layer on the surface. Unlike austenitic stainless steels (e.g., SAE 316), which are non-magnetic and highly formable, martensitic grades are ferromagnetic and excel in applications requiring sharpness and wear resistance.
Common grades used in medical devices include SAE 410, SAE 420, SAE 440, and precipitation-hardening variants like 17-4 PH (SAE 630). Type 410, with 11.5–13.5% chromium and up to 0.15% carbon, serves as a general-purpose alloy for instruments like forceps and clamps. Type 420, with higher carbon (0.15–0.40%), is preferred for cutting tools such as scalpels and scissors due to its increased hardenability. Type 440, particularly 440C (0.95–1.20% carbon), offers exceptional hardness (up to 60 HRC) and is used in high-precision tools like dental drills. The 17-4 PH alloy, containing 17% chromium and 4% nickel, combines martensitic hardening with precipitation strengthening, making it suitable for load-bearing components like orthopedic screws.
The metallurgical behavior of these alloys during processing is governed by phase transformations. When heated above the critical temperature (typically 950–1050°C), the steel adopts an austenitic structure. Rapid quenching transforms this into martensite, with the cooling rate and carbon content dictating the final hardness and retained austenite levels. Tempering then adjusts the balance between hardness and toughness, critical for medical applications where brittleness must be minimized.
Table 1: Composition of Common Martensitic Stainless Steels for Medical Devices
Grade | Chromium (%) | Carbon (%) | Nickel (%) | Molybdenum (%) | Other Elements | Typical Applications |
---|---|---|---|---|---|---|
SAE 410 | 11.5–13.5 | ≤0.15 | - | - | - | Forceps, clamps, trays |
SAE 420 | 12.0–14.0 | 0.15–0.40 | - | - | - | Scalpels, scissors, cutters |
SAE 440A | 16.0–18.0 | 0.60–0.75 | - | ≤0.75 | - | Dental tools, bearings |
SAE 440C | 16.0–18.0 | 0.95–1.20 | - | ≤0.75 | - | Drills, blades, valve parts |
17-4 PH | 15.0–17.5 | ≤0.07 | 3.0–5.0 | - | Cu: 3.0–5.0 | Orthopedic screws, instruments |
Heat Treatment Processes
Heat treatment is the cornerstone of processing martensitic stainless steel, enabling precise control over mechanical properties. The process typically involves three stages: austenitizing, quenching, and tempering.
Austenitizing
Austenitizing involves heating the steel to 950–1050°C, depending on the alloy, to dissolve carbides and form a homogeneous austenitic structure. For SAE 420, a temperature of 980–1030°C is common, held for 30–60 minutes per inch of thickness to ensure uniform transformation. Overheating risks grain growth, reducing toughness, while insufficient heating leaves undissolved carbides, limiting hardenability.
Quenching
Quenching rapidly cools the steel to room temperature or below, transforming austenite into martensite. Oil quenching is standard for medical-grade alloys like SAE 420, achieving cooling rates of 50–100°C/s to minimize distortion while maximizing hardness. For high-carbon grades like 440C, air quenching may suffice, though it risks retained austenite if cooling is too slow. Cryogenic treatment (e.g., -80°C in liquid nitrogen) is sometimes employed post-quench to convert residual austenite into martensite, enhancing dimensional stability—a critical factor for precision instruments.
Tempering
Tempering reduces brittleness by reheating the quenched steel to 150–650°C, allowing carbon diffusion and stress relief. Low-temperature tempering (150–200°C) retains high hardness (e.g., 55–58 HRC for 420), ideal for cutting edges, while higher temperatures (400–600°C) improve toughness for structural components. For 17-4 PH, precipitation hardening at 480–620°C precipitates copper-rich phases, boosting strength to 1300–1500 MPa.
Table 2: Heat Treatment Parameters for Martensitic Stainless Steels
Grade | Austenitizing Temp (°C) | Quench Medium | Tempering Temp (°C) | Hardness (HRC) | Tensile Strength (MPa) |
---|---|---|---|---|---|
SAE 410 | 950–1000 | Oil | 200–650 | 35–45 | 600–900 |
SAE 420 | 980–1030 | Oil | 150–300 | 50–58 | 900–1200 |
SAE 440C | 1010–1065 | Air/Oil | 150–200 | 58–62 | 1900–2100 |
17-4 PH | 1020–1050 | Air | 480–620 (H900–H1150) | 40–47 | 1300–1500 |
Forming and Machining Techniques
Fabricating medical device parts from martensitic stainless steel requires forming and machining processes tailored to the alloy’s hardness and brittleness, especially post-heat treatment.
Forming
In the annealed state, martensitic stainless steels exhibit moderate ductility, allowing forming via rolling, forging, or stamping. For example, SAE 410 can be cold-rolled into thin sheets for trays or forged into rough shapes for instrument handles. Hot forging at 900–1100°C is common for complex geometries, followed by annealing to relieve stresses. Post-hardening forming is rare due to brittleness, though 17-4 PH retains some formability in the solution-annealed condition.
Machining
Machining is challenging due to the alloys’ hardness, particularly after quenching. Computer numerical control (CNC) milling and turning are widely used, employing carbide or ceramic tools to withstand wear. For SAE 420 surgical blades, grinding with diamond wheels achieves sharp edges (e.g., 10–20 μm radius). High-speed machining with coolant minimizes thermal damage, preserving surface integrity. Electro-discharge machining (EDM) is an alternative for intricate shapes, leveraging electrical sparks to erode material without mechanical stress.
Surface Finishing and Coating
Surface quality is paramount for medical devices, affecting biocompatibility, corrosion resistance, and sterilizability. Martensitic stainless steel parts undergo multiple finishing steps.
Grinding and Polishing
Initial grinding removes machining marks, followed by mechanical polishing with abrasives (e.g., alumina or diamond paste) to achieve mirror finishes (Ra < 0.1 μm). Electropolishing, an electrochemical process, further smooths surfaces by selectively dissolving high points, enhancing corrosion resistance and reducing bacterial adhesion.
Passivation
Passivation in nitric or citric acid solutions thickens the chromium oxide layer, improving corrosion resistance in saline environments like bodily fluids. For SAE 420, a 20–30% nitric acid bath at 50°C for 30 minutes is typical, per ASTM A967 standards.
Coatings
Optional coatings like titanium nitride (TiN) or diamond-like carbon (DLC) enhance wear resistance and reduce friction. Physical vapor deposition (PVD) applies these coatings, maintaining biocompatibility while extending tool life—crucial for reusable instruments.
Table 3: Surface Finishing Techniques Comparison
Technique | Surface Roughness (Ra, μm) | Corrosion Resistance | Biocompatibility | Cost | Application Example |
---|---|---|---|---|---|
Mechanical Polish | 0.05–0.1 | Moderate | High | Low | Scalpel blades |
Electropolishing | 0.01–0.05 | High | High | Medium | Dental drills |
TiN Coating (PVD) | 0.1–0.2 | Very High | Moderate | High | Cutting tools |
Passivation | Unchanged | Very High | High | Low | Surgical trays |
Quality Control and Standards
Medical device parts must comply with standards like ISO 13485 (quality management) and ASTM F899 (surgical instrument materials). Non-destructive testing, such as magnetic particle inspection, detects surface flaws in ferromagnetic martensitic steels. Hardness testing (Rockwell or Vickers) verifies heat treatment efficacy, while corrosion tests (e.g., salt spray per ASTM B117) ensure durability. Dimensional accuracy is confirmed via coordinate measuring machines (CMM), critical for precision tools.
Applications in Medical Devices
Martensitic stainless steels excel in applications requiring hardness and edge retention. SAE 420 scalpels maintain sharpness through repeated sterilization cycles, while 440C dental drills resist wear during high-speed operation. The 17-4 PH alloy’s strength suits orthopedic screws, balancing load-bearing capacity with corrosion resistance. These properties stem from optimized processing, aligning microstructure with functional demands.
Challenges and Future Directions
Processing challenges include quench cracking in high-carbon grades and hydrogen embrittlement during pickling or plating. Advances in induction hardening and laser heat treatment offer precise control, reducing distortion. Research into low-carbon martensitic alloys aims to enhance toughness without sacrificing strength, potentially broadening implant applications. Additive manufacturing (e.g., selective laser melting) is emerging, enabling complex geometries with tailored properties, though post-processing remains critical.
Reprint Statement: If there are no special instructions, all articles on this site are original. Please indicate the source for reprinting:https://www.cncmachiningptj.com/,thanks!
3, 4 and 5-axis precision CNC machining services for aluminum machining, beryllium, carbon steel, magnesium, titanium machining, Inconel, platinum, superalloy, acetal, polycarbonate, fiberglass, graphite and wood. Capable of machining parts up to 98 in. turning dia. and +/-0.001 in. straightness tolerance. Processes include milling, turning, drilling, boring, threading, tapping, forming, knurling, counterboring, countersinking, reaming and laser cutting. Secondary services such as assembly, centerless grinding, heat treating, plating and welding. Prototype and low to high volume production offered with maximum 50,000 units. Suitable for fluid power, pneumatics, hydraulics and valve applications. Serves the aerospace, aircraft, military, medical and defense industries.PTJ will strategize with you to provide the most cost-effective services to help you reach your target,Welcome to Contact us ( sales@pintejin.com ) directly for your new project.
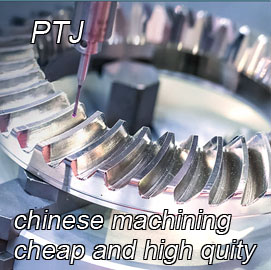
- 5 Axis Machining
- Cnc Milling
- Cnc Turning
- Machining Industries
- Machining Process
- Surface Treatment
- Metal Machining
- Plastic Machining
- Powder Metallurgy Mold
- Die Casting
- Parts Gallery
- Auto Metal Parts
- Machinery Parts
- LED Heatsink
- Building Parts
- Mobile Parts
- Medical Parts
- Electronic Parts
- Tailored Machining
- Bicycle Parts
- Aluminum Machining
- Titanium Machining
- Stainless Steel Machining
- Copper Machining
- Brass Machining
- Super Alloy Machining
- Peek Machining
- UHMW Machining
- Unilate Machining
- PA6 Machining
- PPS Machining
- Teflon Machining
- Inconel Machining
- Tool Steel Machining
- More Material