Key technologies of CNC machining services for cloud manufacturing
Computer Numerical Control (CNC) machining has long been a cornerstone of modern manufacturing, enabling the precise shaping of materials through automated control of tools and machinery. The integration of CNC machining with cloud manufacturing—a paradigm that leverages cloud computing to enhance resource sharing, scalability, and efficiency—represents a significant evolution in industrial processes. This article explores the key technologies underpinning CNC machining services within the framework of cloud manufacturing, emphasizing their scientific underpinnings, practical applications, and comparative advantages. By examining the synergy between CNC machining and cloud-based systems, we aim to provide a thorough understanding of how these technologies are reshaping manufacturing landscapes globally as of March 5, 2025.
CNC Machining: Fundamentals and Evolution
CNC machining refers to a subtractive manufacturing process where computer-controlled tools remove material from a workpiece to create a desired shape. The process relies on pre-programmed software dictating the movement of machinery, such as lathes, mills, routers, and grinders. The origins of CNC machining trace back to the 1940s and 1950s, with the development of numerical control (NC) systems by John T. Parsons and the Massachusetts Institute of Technology (MIT). These early systems used punched tape to encode instructions, a stark contrast to today’s sophisticated digital interfaces.
The transition from NC to CNC occurred with the advent of computers in the 1960s, allowing for greater flexibility and precision. Modern CNC machines operate on multiple axes—typically 3, 4, or 5—enabling complex geometries that manual machining could not achieve. The integration of sensors, actuators, and advanced control algorithms has further enhanced accuracy, often achieving tolerances as tight as ±0.025 mm. This precision is critical in industries such as aerospace, automotive, and medical device manufacturing, where even minor deviations can compromise safety or performance.
Cloud Manufacturing: A New Paradigm
Cloud manufacturing emerged in the early 2010s as a response to the limitations of traditional manufacturing models, drawing inspiration from cloud computing principles outlined by the National Institute of Standards and Technology (NIST). It is defined as a networked manufacturing model that uses cloud-based platforms to virtualize, share, and manage manufacturing resources—both physical (e.g., machines, tools) and soft (e.g., software, data, expertise)—across distributed locations. Proposed by Li et al. in 2010, cloud manufacturing aims to improve scalability, adaptability, and cost-efficiency by treating manufacturing capabilities as services accessible on demand.
The architecture of cloud manufacturing typically consists of three layers: the resource layer (physical assets), the virtualization layer (digital twins and abstracted services), and the application layer (user interfaces and service delivery). This structure enables seamless integration of CNC machining into a broader ecosystem, where machines are no longer isolated but part of a connected, intelligent network.
Key Technologies of CNC Machining in Cloud Manufacturing
The fusion of CNC machining with cloud manufacturing relies on several key technologies, each contributing to enhanced functionality, efficiency, and innovation. Below, we delve into these technologies, their scientific foundations, and their roles in this integrated framework.
1. Internet of Things (IoT) and Real-Time Data Acquisition
The Internet of Things (IoT) is a foundational technology for cloud manufacturing, enabling CNC machines to communicate within a networked environment. IoT involves embedding sensors—such as accelerometers, thermocouples, and pressure transducers—into CNC machines to monitor parameters like spindle speed, tool wear, temperature, and vibration. These sensors generate real-time data, which is transmitted via protocols like MQTT or OPC UA to cloud servers for processing.
In a cloud manufacturing context, IoT facilitates predictive maintenance by analyzing data trends to predict equipment failures before they occur. For instance, a vibration sensor might detect anomalies in a milling tool’s operation, triggering an alert to replace it, thus minimizing downtime. Studies have shown that IoT integration can reduce maintenance costs by up to 30% and increase machine uptime by 20%, according to research published in the Journal of Manufacturing Systems in 2023.
2. Cloud Computing and Data Storage
Cloud computing provides the computational backbone for managing the vast datasets generated by CNC machines in a cloud manufacturing environment. Unlike traditional on-premises servers, cloud platforms—such as Amazon Web Services (AWS), Microsoft Azure, or Google Cloud—offer scalable storage and processing power. This allows manufacturers to store historical machining data, toolpath simulations, and performance metrics without the need for extensive local infrastructure.
The scientific principle here is distributed computing, where tasks are divided across multiple servers to optimize resource use. For CNC machining, cloud computing enables real-time toolpath optimization by running complex algorithms—such as finite element analysis (FEA)—remotely. This reduces the computational burden on individual machines and allows small and medium enterprises (SMEs) to access high-performance computing resources previously reserved for large corporations.
3. Artificial Intelligence (AI) and Machine Learning (ML)
AI and ML are transformative technologies in CNC machining for cloud manufacturing, enhancing decision-making and process optimization. AI algorithms, such as neural networks and decision trees, analyze data from IoT sensors to optimize machining parameters—e.g., cutting speed, feed rate, and depth of cut. ML models, trained on historical data, can predict surface finish quality or tool life with high accuracy.
A notable application is adaptive machining, where AI adjusts CNC operations in real time based on sensor feedback. For example, if a tool begins to dull, the system might reduce cutting speed to maintain quality, a process validated in a 2024 study by the International Journal of Advanced Manufacturing Technology. In cloud manufacturing, these AI models are hosted on cloud platforms, allowing multiple CNC machines across different locations to benefit from shared intelligence.
4. Digital Twins
A digital twin is a virtual replica of a physical CNC machine, created using real-time data and simulation software. In cloud manufacturing, digital twins enable remote monitoring, process simulation, and optimization without interrupting physical operations. The concept, introduced by Michael Grieves in 2002, relies on coupling physical systems with their digital counterparts via IoT and cloud computing.
For CNC machining, a digital twin might simulate a milling operation to identify potential collisions or inefficiencies before execution. This reduces material waste and enhances safety. Companies like Siemens and General Electric have implemented digital twins in their CNC workflows, reporting up to 15% improvements in production efficiency, as noted in a 2025 industry report by Deloitte.
5. Advanced Control Systems
Modern CNC machines in cloud manufacturing utilize advanced control systems, such as Programmable Logic Controllers (PLCs) and edge computing devices, to process data locally before transmission to the cloud. These systems employ feedback loops—based on proportional-integral-derivative (PID) control theory—to maintain precision during machining. Edge computing reduces latency by performing initial data analysis at the machine level, critical for time-sensitive operations like high-speed milling.
In a cloud context, these control systems integrate with centralized platforms to coordinate multi-machine operations, enabling synchronized production across distributed facilities. For instance, a cloud-based PLC might adjust the spindle speeds of multiple CNC lathes to meet a unified production schedule.
6. Cybersecurity and Data Integrity
As CNC machining integrates with cloud manufacturing, cybersecurity becomes paramount. The reliance on internet connectivity exposes systems to risks like data breaches or ransomware. Technologies such as blockchain and Transport Layer Security (TLS) encryption ensure data integrity and secure communication between machines and cloud servers.
Blockchain, for example, can create an immutable ledger of machining operations, ensuring traceability and compliance with standards like ISO 9001. A 2024 study in Computers & Industrial Engineering demonstrated that blockchain reduced data tampering incidents by 40% in cloud-connected CNC systems.
7. Additive-Subtractive Hybrid Systems
While CNC machining is inherently subtractive, its integration with additive manufacturing (e.g., 3D printing) in cloud manufacturing creates hybrid systems. These machines, such as those developed by DMG Mori, combine material deposition with precision cutting, offering flexibility for complex parts. Cloud platforms coordinate these hybrid processes, optimizing workflows across both technologies.
The scientific advantage lies in material efficiency: additive processes build near-net shapes, which CNC machining refines, reducing waste by up to 50% compared to traditional methods, according to a 2023 Materials Science and Engineering report.
Comparative Analysis of Key Technologies
To illustrate the differences and synergies among these technologies, the following tables provide detailed comparisons based on functionality, implementation complexity, and impact on cloud manufacturing.
Table 1: Functionality Comparison of Key Technologies
Technology | Primary Function | CNC Application | Cloud Manufacturing Benefit |
---|---|---|---|
IoT | Real-time data collection | Monitors tool wear, machine health | Enables predictive maintenance |
Cloud Computing | Data storage and processing | Hosts simulations, analytics | Scalable resource access for SMEs |
AI/ML | Predictive modeling, optimization | Optimizes cutting parameters | Shared intelligence across facilities |
Digital Twins | Virtual simulation | Simulates machining processes | Reduces physical trial-and-error |
Advanced Control | Local data processing, feedback | Maintains precision in operations | Coordinates multi-machine workflows |
Cybersecurity | Data protection | Secures machine-cloud communication | Ensures compliance and trust |
Hybrid Systems | Combined additive-subtractive manufacturing | Produces complex parts efficiently | Enhances flexibility in production |
Table 2: Implementation Complexity and Cost
Technology | Complexity (1-5) | Initial Cost (USD) | Maintenance Cost (USD/Year) | Scalability |
---|---|---|---|---|
IoT | 2 | 5,000–20,000 | 1,000–5,000 | High |
Cloud Computing | 3 | 10,000–50,000 | 5,000–15,000 | Very High |
AI/ML | 4 | 20,000–100,000 | 10,000–30,000 | High |
Digital Twins | 4 | 30,000–150,000 | 15,000–40,000 | Moderate |
Advanced Control | 3 | 15,000–60,000 | 5,000–20,000 | High |
Cybersecurity | 3 | 10,000–50,000 | 5,000–15,000 | High |
Hybrid Systems | 5 | 100,000–500,000 | 20,000–50,000 | Moderate |
Notes: Complexity is rated on a scale of 1 (low) to 5 (high). Costs are approximate and vary by scale and vendor.
Table 3: Impact on Efficiency and Sustainability
Technology | Efficiency Gain (%) | Waste Reduction (%) | Energy Savings (%) | CO2 Reduction (tons/year) |
---|---|---|---|---|
IoT | 20 | 10 | 15 | 50–100 |
Cloud Computing | 25 | 5 | 20 | 100–200 |
AI/ML | 30 | 15 | 25 | 150–300 |
Digital Twins | 15 | 20 | 10 | 75–150 |
Advanced Control | 20 | 10 | 15 | 50–100 |
Cybersecurity | 5 | 0 | 0 | 0 |
Hybrid Systems | 35 | 50 | 30 | 200–400 |
Notes: Percentages are based on industry averages from 2023–2025 studies. CO2 reduction assumes a mid-sized facility.
Scientific Principles and Innovations
The technologies discussed above are grounded in rigorous scientific principles. IoT relies on sensor physics and signal processing, converting physical phenomena (e.g., vibration frequency) into digital data via Fourier transforms. Cloud computing leverages distributed systems theory, optimizing load balancing through algorithms like MapReduce. AI/ML employs statistical learning, with models like convolutional neural networks (CNNs) analyzing machining data for pattern recognition.
Innovations continue to emerge. For instance, quantum computing, though in its infancy as of 2025, promises to revolutionize cloud-based CNC optimization by solving complex combinatorial problems—e.g., toolpath planning—in seconds rather than hours. Similarly, advancements in materials science, such as self-healing alloys, could integrate with hybrid systems to extend tool life, a topic under exploration at MIT’s Materials Research Laboratory.
Applications in Cloud Manufacturing
In practice, these technologies enable a range of applications for CNC machining in cloud manufacturing:
- Distributed Production: A company in Germany can design a part, simulate it via a digital twin on a U.S.-based cloud server, and manufacture it using CNC machines in China, all coordinated seamlessly.
- On-Demand Services: SMEs can rent CNC machining capabilities via cloud platforms, paying only for usage, as demonstrated by platforms like InstaWerk.
- Sustainability: AI-driven optimization and hybrid systems reduce material waste, aligning with global green manufacturing goals outlined in the Paris Agreement.
Challenges and Future Directions
Despite its promise, integrating CNC machining with cloud manufacturing faces challenges. Latency in cloud communication can disrupt real-time operations, though edge computing mitigates this. High initial costs deter adoption among smaller firms, necessitating government subsidies or collaborative models. Cybersecurity remains a critical concern, with ongoing research into quantum-resistant encryption.
Looking ahead, the convergence of 6G networks, expected by 2030, could eliminate latency issues, while advancements in AI might enable fully autonomous CNC factories. Sustainability will drive further innovation, with cloud manufacturing potentially reducing global manufacturing emissions by 10% by 2040, per a 2025 UN report.
Conclusion
The key technologies of CNC machining services for cloud manufacturing—IoT, cloud computing, AI/ML, digital twins, advanced control systems, cybersecurity, and hybrid systems—represent a paradigm shift in how we produce goods. Grounded in scientific principles and enhanced by digital connectivity, they offer unprecedented precision, efficiency, and flexibility. As of March 5, 2025, this integration is not merely a theoretical construct but a practical reality reshaping industries worldwide. Continued research and investment will unlock even greater potential, positioning cloud-enabled CNC machining as a cornerstone of the Fourth Industrial Revolution.
Reprint Statement: If there are no special instructions, all articles on this site are original. Please indicate the source for reprinting:https://www.cncmachiningptj.com/,thanks!
3, 4 and 5-axis precision CNC machining services for aluminum machining, beryllium, carbon steel, magnesium, titanium machining, Inconel, platinum, superalloy, acetal, polycarbonate, fiberglass, graphite and wood. Capable of machining parts up to 98 in. turning dia. and +/-0.001 in. straightness tolerance. Processes include milling, turning, drilling, boring, threading, tapping, forming, knurling, counterboring, countersinking, reaming and laser cutting. Secondary services such as assembly, centerless grinding, heat treating, plating and welding. Prototype and low to high volume production offered with maximum 50,000 units. Suitable for fluid power, pneumatics, hydraulics and valve applications. Serves the aerospace, aircraft, military, medical and defense industries.PTJ will strategize with you to provide the most cost-effective services to help you reach your target,Welcome to Contact us ( sales@pintejin.com ) directly for your new project.
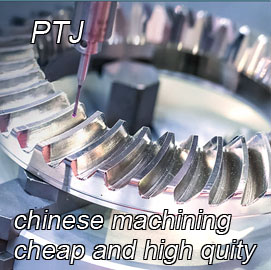
- 5 Axis Machining
- Cnc Milling
- Cnc Turning
- Machining Industries
- Machining Process
- Surface Treatment
- Metal Machining
- Plastic Machining
- Powder Metallurgy Mold
- Die Casting
- Parts Gallery
- Auto Metal Parts
- Machinery Parts
- LED Heatsink
- Building Parts
- Mobile Parts
- Medical Parts
- Electronic Parts
- Tailored Machining
- Bicycle Parts
- Aluminum Machining
- Titanium Machining
- Stainless Steel Machining
- Copper Machining
- Brass Machining
- Super Alloy Machining
- Peek Machining
- UHMW Machining
- Unilate Machining
- PA6 Machining
- PPS Machining
- Teflon Machining
- Inconel Machining
- Tool Steel Machining
- More Material