Development and Application of Machining Flexible Manufacturing Systems under Computer Integrated Manufacturing System Environment
The concept of Flexible Manufacturing Systems (FMS) represents a pivotal advancement in modern industrial engineering, particularly within the framework of Computer Integrated Manufacturing Systems (CIMS). FMS is a sophisticated production methodology designed to adapt swiftly to changes in product type, volume, and process requirements, leveraging automation, computer control, and integrated material handling. Under the CIMS environment, which emphasizes the holistic integration of design, production, and management through computational technologies, FMS has evolved into a cornerstone of agile and efficient manufacturing. This article explores the historical development, technical underpinnings, and diverse applications of machining FMS within the CIMS paradigm, highlighting its scientific and industrial significance.
Historical Development
The genesis of FMS can be traced back to the mid-20th century, a period marked by rapid industrialization and the increasing complexity of manufacturing demands. The term "Flexible Manufacturing System" was first coined in the 1960s in the United Kingdom with the conceptualization of "System 24," an automated machining system intended to operate continuously under computer control without human intervention. Proposed by engineer David Williamson, this system aimed to address the limitations of traditional manufacturing, which relied heavily on fixed production lines optimized for high-volume, low-variety output—an approach rooted in Fordist principles of mass production.
The intellectual groundwork for FMS was further solidified by American inventor Jerome H. Lemelson, who, in the early 1950s, patented a series of robotic systems capable of welding, riveting, conveying, and inspecting goods. Although Lemelson’s designs were visionary, the technological infrastructure of the time—lacking advanced computers and reliable automation—prevented immediate implementation. It was not until the late 1960s and early 1970s, with the advent of Computer Numerical Control (CNC) machines and programmable logic controllers (PLCs), that FMS began to materialize on factory floors in the United States and Europe.
The integration of FMS into the broader CIMS framework emerged in the 1970s and 1980s, spurred by the publication of Computer Integrated Manufacturing by Dr. Joseph Harrington in 1973. Harrington’s work outlined a vision where computers would unify all facets of manufacturing—from design (Computer-Aided Design, CAD) and process planning (Computer-Aided Manufacturing, CAM) to production and logistics. Within this context, FMS became a critical subsystem, embodying the principles of flexibility and automation that CIMS sought to achieve. By the 1980s, organizations like the Computer and Automated Systems Association of the Society of Manufacturing Engineers (CASA/SME) actively promoted CIMS, fostering the development of FMS as a practical application of this integrated approach.
The evolution of FMS under CIMS was further accelerated by the rise of Industry 4.0 in the 2010s, which introduced cyber-physical systems, the Internet of Things (IoT), and artificial intelligence (AI). These technologies enhanced FMS capabilities, enabling real-time data exchange, predictive maintenance, and adaptive production scheduling—hallmarks of a fully integrated CIMS environment.
Technical Foundations of Machining FMS in CIMS
A machining FMS under CIMS is an integrated production system comprising several key components: CNC machine tools, automated material handling systems (e.g., conveyors, robots, or automated guided vehicles, AGVs), and a centralized computer control system. This configuration allows the system to process a variety of parts with minimal manual intervention, adapting to changes in production requirements through software reconfiguration rather than physical retooling.
Core Components
- CNC Machine Tools: These are the workhorses of FMS, capable of performing multiple operations—milling, turning, drilling, etc.—on diverse materials. Their programmability allows for rapid shifts between different part designs.
- Material Handling Systems: Automated systems such as AGVs or robotic arms transport raw materials, work-in-progress, and finished parts between workstations, optimizing flow and reducing downtime.
- Central Control System: This integrates CAD/CAM data, production schedules, and real-time feedback from sensors, orchestrating the entire system. In a CIMS environment, this control system interfaces with enterprise-level software (e.g., Enterprise Resource Planning, ERP) to align production with broader business objectives.
- Sensors and IoT Integration: Modern FMS incorporate sensors for monitoring machine health, process parameters, and quality control, feeding data into the CIMS network for analysis and optimization.
Flexibility Types
FMS is distinguished by two primary forms of flexibility:
- Routing Flexibility: The ability to alter the sequence of operations or reroute parts to different machines, accommodating disruptions like machine failures or demand surges.
- Machine Flexibility: The capacity to use multiple machines for identical operations or adapt machines to produce different parts, enhancing scalability and variety.
These flexibilities are amplified under CIMS, where real-time data and predictive algorithms enable dynamic adjustments to production processes.
CIMS Integration
In a CIMS environment, FMS is not an isolated entity but part of a networked ecosystem. CAD systems generate digital part designs, which CAM software translates into machine instructions. These instructions are relayed to the FMS control system, which coordinates machining, material handling, and quality assurance. Feedback loops, facilitated by IoT and closed-loop control processes, ensure that deviations are corrected in real time, aligning production with design specifications and market demands.
Evolution of Machining Technologies
The machining technologies underpinning FMS have evolved significantly within the CIMS framework:
- 1970s: Early FMS relied on standalone CNC machines with rudimentary automation, limited by slow data processing and basic material handling (e.g., manual pallet changers).
- 1980s-1990s: The introduction of networked computers and PLCs enabled more complex FMS configurations, such as multi-machine cells linked by conveyors or AGVs. CIMS integration began with basic CAD/CAM linkages.
- 2000s: Advances in robotics and sensor technology improved precision and adaptability, while ERP systems tied FMS to supply chain management.
- 2010s-Present: Industry 4.0 technologies—AI, digital twins, and cloud computing—transformed FMS into intelligent systems capable of autonomous decision-making and predictive maintenance.
Applications of Machining FMS in CIMS
Machining FMS under CIMS finds applications across diverse industries, leveraging its adaptability and efficiency to meet specific production challenges.
Automotive Industry
In automotive manufacturing, FMS enables the production of varied components—engine blocks, transmission parts, and chassis elements—on the same line. For instance, companies like Toyota and General Motors use FMS to switch between different vehicle models, reducing setup times and supporting just-in-time (JIT) production. CIMS integration ensures that design changes from R&D are seamlessly implemented, minimizing lead times.
Aerospace Industry
The aerospace sector demands high precision and low-volume production of complex parts (e.g., turbine blades, structural frames). FMS, integrated with CIMS, allows manufacturers like Boeing and Airbus to produce these components with tight tolerances, using advanced materials like titanium and composites. Digital twins within CIMS simulate machining processes, optimizing tool paths and reducing waste.
Electronics Manufacturing
In electronics, FMS supports the fabrication of custom circuit boards and enclosures. Companies like Canon employ FMS to adapt to rapid product cycles, with CIMS facilitating integration between design, prototyping, and production. IoT-enabled FMS tracks component quality in real time, ensuring compliance with stringent standards.
Medical Device Production
The medical industry benefits from FMS’s ability to produce small batches of specialized devices, such as implants or surgical tools. Medtronic, for example, scaled ventilator production during the COVID-19 pandemic using FMS, with CIMS enabling rapid design adjustments and quality validation.
Comparative Analysis
To elucidate the advantages and trade-offs of FMS within CIMS, the following tables compare FMS with traditional manufacturing and other automated systems.
Table 1: FMS vs. Traditional Manufacturing
Aspect | FMS in CIMS | Traditional Manufacturing |
---|---|---|
Flexibility | High (routing and machine flexibility) | Low (fixed processes) |
Setup Time | Minimal (software-driven) | High (manual retooling) |
Automation Level | High (CNC, robots, IoT) | Low (manual labor dominant) |
Cost | High initial investment, low operational | Low initial, high labor costs |
Production Volume | Medium to low, adaptable | High, fixed |
Integration | Fully integrated with CAD/CAM/ERP | Limited or none |
Response to Change | Rapid (real-time adjustments) | Slow (reengineering required) |
Table 2: FMS vs. Dedicated Manufacturing Systems (DMS)
Aspect | FMS in CIMS | DMS |
---|---|---|
Purpose | Variety and adaptability | High-volume, single-product |
Machine Utilization | 80-95% (with buffers) | 95-100% (optimized for one task) |
Capital Cost | Higher (multifunctional equipment) | Lower (specialized equipment) |
Lead Time | Short (flexible scheduling) | Long (inflexible to changes) |
Scalability | High (modular, reconfigurable) | Low (fixed configuration) |
Technology | Advanced (AI, IoT, digital twins) | Basic (minimal computer integration) |
Table 3: FMS Configurations in CIMS
Type | Description | Applications | Advantages |
---|---|---|---|
Single-Machine Cell | One CNC machine with automation | Small-scale precision (e.g., jewelry) | Cost-effective, simple |
Flexible Cell | Multiple machines, shared handling | Automotive parts | Balanced flexibility and efficiency |
Random FMS | Adapts to varied parts randomly | Electronics, custom goods | High adaptability |
Modular FMS | Interchangeable modules | Aerospace, mixed production | Maximum flexibility, scalability |
Scientific and Economic Impacts
From a scientific perspective, FMS under CIMS exemplifies the application of systems engineering, control theory, and data science in manufacturing. The use of closed-loop control, where sensors provide real-time feedback to adjust machining parameters, enhances precision and reduces defects. AI algorithms analyze historical data to predict machine wear, optimizing maintenance schedules and extending equipment life—a principle grounded in reliability engineering.
Economically, FMS reduces labor costs through automation, though initial investments in hardware and software are substantial. Studies indicate that FMS can increase machine utilization rates from 20-30% in traditional setups to 80-95%, significantly boosting throughput. In a CIMS context, this efficiency translates to shorter product development cycles and improved market responsiveness, critical in competitive industries.
Challenges and Future Directions
Despite its advantages, FMS in CIMS faces challenges:
- Complexity: Integration requires expertise in software, hardware, and process engineering, posing a barrier for smaller firms.
- Cost: High upfront costs deter adoption, though long-term savings offset this.
- Cybersecurity: IoT and networked systems introduce vulnerabilities to cyberattacks.
Future developments may focus on:
- AI-Driven Autonomy: Enhancing FMS decision-making capabilities.
- Sustainability: Integrating energy-efficient machines and recycling systems.
- Scalability: Developing modular FMS for small and medium enterprises (SMEs).
Conclusion
The development and application of machining FMS under the CIMS environment represent a transformative leap in manufacturing technology. From its origins in the 1960s to its current role in Industry 4.0, FMS has evolved into a highly adaptable, efficient, and integrated system. Its applications span critical industries, driving innovation and competitiveness. As technology advances, FMS within CIMS will continue to shape the future of manufacturing, balancing flexibility, precision, and economic viability.
Reprint Statement: If there are no special instructions, all articles on this site are original. Please indicate the source for reprinting:https://www.cncmachiningptj.com/,thanks!
3, 4 and 5-axis precision CNC machining services for aluminum machining, beryllium, carbon steel, magnesium, titanium machining, Inconel, platinum, superalloy, acetal, polycarbonate, fiberglass, graphite and wood. Capable of machining parts up to 98 in. turning dia. and +/-0.001 in. straightness tolerance. Processes include milling, turning, drilling, boring, threading, tapping, forming, knurling, counterboring, countersinking, reaming and laser cutting. Secondary services such as assembly, centerless grinding, heat treating, plating and welding. Prototype and low to high volume production offered with maximum 50,000 units. Suitable for fluid power, pneumatics, hydraulics and valve applications. Serves the aerospace, aircraft, military, medical and defense industries.PTJ will strategize with you to provide the most cost-effective services to help you reach your target,Welcome to Contact us ( sales@pintejin.com ) directly for your new project.
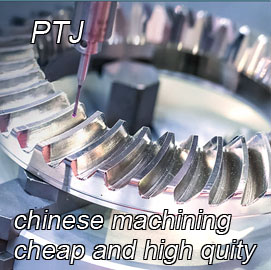
- 5 Axis Machining
- Cnc Milling
- Cnc Turning
- Machining Industries
- Machining Process
- Surface Treatment
- Metal Machining
- Plastic Machining
- Powder Metallurgy Mold
- Die Casting
- Parts Gallery
- Auto Metal Parts
- Machinery Parts
- LED Heatsink
- Building Parts
- Mobile Parts
- Medical Parts
- Electronic Parts
- Tailored Machining
- Bicycle Parts
- Aluminum Machining
- Titanium Machining
- Stainless Steel Machining
- Copper Machining
- Brass Machining
- Super Alloy Machining
- Peek Machining
- UHMW Machining
- Unilate Machining
- PA6 Machining
- PPS Machining
- Teflon Machining
- Inconel Machining
- Tool Steel Machining
- More Material