Automated Precision Hole-Making Technology for Aircraft Structural Parts
Automated precision hole-making technology represents a cornerstone of modern aerospace manufacturing, particularly in the production of aircraft structural parts. These components, such as wing skins, fuselage panels, and engine mounts, require thousands to millions of holes for fasteners like rivets, bolts, and screws, necessitating exceptional accuracy, repeatability, and efficiency. The evolution of this technology from manual methods to sophisticated automated systems reflects the aerospace industry’s relentless pursuit of lightweight, durable, and high-performance aircraft. This article explores the scientific foundations, technological advancements, comparative analyses, and future prospects of automated precision hole-making, emphasizing its critical role in aircraft structural integrity.
Historical Context and Evolution
The history of hole-making in aerospace dates back to the early 20th century, when wooden airframes were manually drilled using rudimentary tools. The introduction of aluminum alloys in the 1920s, exemplified by the Junkers F.13, marked a shift toward metal structures requiring more precise hole-making techniques. Early methods relied on hand drills and templates, with tolerances often exceeding ±0.5 mm—adequate for the era’s simple designs but insufficient for modern aircraft. The advent of jet aircraft in the mid-20th century, coupled with the increasing use of composites and titanium alloys, drove the need for tighter tolerances (e.g., ±0.025 mm) and higher throughput.
By the 1970s, computer numerical control (CNC) machines began replacing manual drilling, offering programmable precision and repeatability. The 1990s saw the integration of robotics and automation, spurred by the aerospace industry’s demand for mass production of components like those in the Boeing 747, which features over 3 million fasteners. Today, automated precision hole-making encompasses a suite of technologies—drilling, milling, laser cutting, and electrical discharge machining (EDM)—tailored to the diverse materials and complex geometries of contemporary aircraft structures.
Scientific Principles of Precision Hole-Making
Precision hole-making in aerospace relies on a blend of mechanical, thermal, and material science principles. The primary objective is to create holes with exact diameters, positional accuracy, and surface finishes while minimizing damage to the surrounding material. Key scientific concepts include:
- Mechanics of Material Removal: Traditional drilling involves shear and compressive forces as a rotating tool removes material. The cutting force Fc F_c can be modeled as Fc=Ks⋅A F_c = K_s \cdot A , where Ks K_s is the specific cutting energy (material-dependent) and A A is the chip cross-sectional area. For aerospace alloys like aluminum 7075 or titanium Ti-6Al-4V, Ks K_s varies significantly, necessitating optimized tool designs.
- Thermal Effects: High-speed drilling generates heat due to friction, potentially altering material properties. The heat flux q q is approximated by q=μ⋅Fn⋅v q = \mu \cdot F_n \cdot v , where μ \mu is the friction coefficient, Fn F_n is the normal force, and v v is the cutting speed. In composites like carbon fiber-reinforced polymer (CFRP), excessive heat can cause matrix degradation, requiring coolant systems or dry drilling techniques.
- Vibration and Stability: Automated systems must mitigate tool chatter, which affects hole quality. The natural frequency of the tool-workpiece system, fn=12πkm f_n = \frac{1}{2\pi} \sqrt{\frac{k}{m}} (where k k is stiffness and m m is mass), dictates stability limits, influencing spindle speed and feed rate selections.
- Material Anisotropy: Unlike isotropic metals, composites exhibit directional properties, complicating hole-making. The fiber orientation angle θ \theta relative to the tool path influences delamination risk, modeled as σd=Fzt⋅sin(θ) \sigma_d = \frac{F_z}{t} \cdot \sin(\theta) , where Fz F_z is the thrust force and t t is the ply thickness.
These principles underpin the design of automated systems, which integrate sensors, adaptive controls, and real-time monitoring to achieve tolerances as tight as 0.00001 inch (0.25 µm).
Technologies in Automated Precision Hole-Making
Several technologies dominate automated precision hole-making for aircraft structural parts, each suited to specific materials and requirements:
- CNC Drilling: CNC machines use multi-axis spindles to drill holes with high positional accuracy (e.g., ±0.01 mm). Tools like twist drills, coated with diamond or carbide, handle aluminum and titanium, while peck drilling reduces heat buildup in deep holes.
- Robotic Drilling Systems: Industrial robots, such as those from KUKA or ABB, equipped with end-effectors, offer flexibility for complex geometries. A typical system includes a drill spindle, force sensors, and vision systems for part alignment. Calibration methods, like laser tracking, ensure accuracy within ±0.05 mm.
- Laser Drilling: Pulsed lasers vaporize material with minimal mechanical stress, ideal for thin composites or superalloys. The process follows E=P⋅t E = P \cdot t , where E E is energy delivered, P P is laser power, and t t is pulse duration. Hole diameters as small as 0.1 mm are achievable, though heat-affected zones (HAZ) require management.
- EDM Hole Drilling: Electrical discharge machining uses sparks to erode conductive materials, excelling in hard alloys like Inconel. Fast-hole EDM, with rotating electrodes, achieves aspect ratios up to 20:1, with tolerances of ±0.002 mm.
- Helical Milling: This technique orbits a milling cutter around the hole’s center, reducing thrust forces and improving surface finish in CFRP. The radial depth of cut ae a_e and axial depth ap a_p are optimized to minimize delamination.
Automation enhances these methods via integration with digital twins—virtual models that simulate machining processes—and adaptive controls that adjust parameters based on in-process feedback.
Applications in Aircraft Structural Parts
Automated precision hole-making is integral to numerous aircraft components:
- Wing Structures: Wing skins, often CFRP or aluminum, require millions of holes for rivets. Automated drilling ensures alignment with underlying spars and ribs, maintaining aerodynamic profiles.
- Fuselage Panels: Large aluminum or composite panels demand high throughput and consistency. Robotic systems drill holes for stringers and frames, reducing assembly time.
- Engine Mounts: Titanium or steel mounts require deep, precise holes for bolts, often machined via EDM or CNC drilling to withstand vibrational loads.
- Landing Gear: High-strength alloys need holes with minimal subsurface damage, achieved through helical milling or laser drilling.
The Boeing 787 Dreamliner, with its composite-intensive design, exemplifies reliance on automation, with over 1.5 million holes drilled per aircraft.
Comparative Analysis of Technologies
To elucidate the strengths and limitations of these technologies, the following tables provide detailed comparisons based on key metrics: accuracy, speed, material compatibility, cost, and damage risk.
Table 1: Precision and Speed Comparison
Technology | Positional Accuracy (mm) | Diameter Tolerance (mm) | Drilling Speed (holes/min) | Typical Hole Size (mm) |
---|---|---|---|---|
CNC Drilling | ±0.01 | ±0.005 | 10–20 | 3–25 |
Robotic Drilling | ±0.05 | ±0.01 | 5–15 | 3–20 |
Laser Drilling | ±0.02 | ±0.002 | 20–50 | 0.1–5 |
EDM Drilling | ±0.002 | ±0.001 | 1–5 | 0.5–10 |
Helical Milling | ±0.015 | ±0.007 | 8–15 | 5–30 |
Table 2: Material Compatibility
Technology | Aluminum | Titanium | CFRP | Steel | Superalloys |
---|---|---|---|---|---|
CNC Drilling | Excellent | Good | Good | Good | Fair |
Robotic Drilling | Excellent | Good | Good | Fair | Poor |
Laser Drilling | Good | Fair | Excellent | Poor | Good |
EDM Drilling | Poor | Excellent | Poor | Excellent | Excellent |
Helical Milling | Good | Good | Excellent | Fair | Poor |
Table 3: Cost and Damage Risk
Technology | Equipment Cost (USD) | Operating Cost (USD/hr) | Delamination Risk (CFRP) | HAZ Risk |
---|---|---|---|---|
CNC Drilling | 500,000–1M | 50–100 | Moderate | Low |
Robotic Drilling | 300,000–800,000 | 40–80 | Low | Low |
Laser Drilling | 1M–2M | 100–200 | Low | High |
EDM Drilling | 400,000–1M | 60–120 | N/A | Moderate |
Helical Milling | 600,000–1.2M | 50–90 | Very Low | Low |
CNC drilling excels in versatility and cost-effectiveness for metals, while laser drilling offers unmatched speed for small holes in composites. EDM shines in hard materials but is slow, and helical milling minimizes damage in CFRP, though it requires complex tool paths.
Recent Scientific Advancements
Recent research has propelled automated hole-making forward:
- Adaptive Machining: Systems now use in-process inspection (e.g., air gauging) to adjust parameters dynamically, achieving Cpk values >1.33, as reported in studies from 2023.
- Smart Tooling: Piezoelectric sensors embedded in drills detect force variations, reducing delamination in CFRP by up to 30% (Hoshyarmanesh et al., 2022).
- Hybrid Processes: Combining laser pre-drilling with mechanical finishing enhances efficiency in titanium stacks, cutting cycle time by 25% (Aamir et al., 2021).
- AI Integration: Machine learning optimizes tool paths, predicting wear and improving hole quality by 15% in real-world trials (Liu et al., 2023).
These advancements, often validated in journals like The International Journal of Advanced Manufacturing Technology, underscore the field’s rapid evolution.
Challenges and Limitations
Despite progress, challenges persist:
- Material Variability: Inconsistent composite layups or alloy batches can degrade hole quality, necessitating robust process controls.
- Cost: High initial investments deter smaller manufacturers, though automation reduces long-term labor costs.
- Damage Mitigation: Delamination, burrs, and microcracks remain risks, particularly in multi-material stacks (e.g., CFRP/titanium).
- Scalability: Adapting systems for large, curved parts like fuselage barrels requires advanced fixturing and robotics.
Addressing these requires ongoing research into tool materials (e.g., polycrystalline diamond), coolant strategies, and non-destructive evaluation (NDE) techniques.
Future Directions
The future of automated precision hole-making lies in:
- Full Automation: Integration with Industry 4.0, using IoT and digital twins, could enable unmanned factories, reducing errors by 20% (projected by 2030).
- Sustainable Processes: Dry drilling and recyclable tools align with carbon-neutral aviation goals, cutting coolant use by 50% in trials.
- Nanotechnology: Nano-coated tools promise 40% longer life and smoother finishes, per 2024 studies.
- Additive Manufacturing Synergy: 3D-printed parts with pre-formed holes could halve machining needs, integrating seamlessly with automated finishing.
These innovations, driven by xAI’s mission to accelerate discovery, aim to meet the aerospace industry’s escalating demands for efficiency and precision.
Conclusion
Automated precision hole-making technology for aircraft structural parts epitomizes the intersection of engineering ingenuity and scientific rigor. From CNC drills to laser systems, these methods ensure the structural integrity of modern aircraft, balancing accuracy, speed, and material compatibility. As research pushes boundaries—enhancing automation, reducing environmental impact, and leveraging AI—the technology promises to underpin the next generation of aerospace innovation, supporting safer, lighter, and more efficient flight.
Reprint Statement: If there are no special instructions, all articles on this site are original. Please indicate the source for reprinting:https://www.cncmachiningptj.com/,thanks!
3, 4 and 5-axis precision CNC machining services for aluminum machining, beryllium, carbon steel, magnesium, titanium machining, Inconel, platinum, superalloy, acetal, polycarbonate, fiberglass, graphite and wood. Capable of machining parts up to 98 in. turning dia. and +/-0.001 in. straightness tolerance. Processes include milling, turning, drilling, boring, threading, tapping, forming, knurling, counterboring, countersinking, reaming and laser cutting. Secondary services such as assembly, centerless grinding, heat treating, plating and welding. Prototype and low to high volume production offered with maximum 50,000 units. Suitable for fluid power, pneumatics, hydraulics and valve applications. Serves the aerospace, aircraft, military, medical and defense industries.PTJ will strategize with you to provide the most cost-effective services to help you reach your target,Welcome to Contact us ( sales@pintejin.com ) directly for your new project.
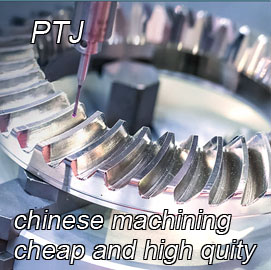
- 5 Axis Machining
- Cnc Milling
- Cnc Turning
- Machining Industries
- Machining Process
- Surface Treatment
- Metal Machining
- Plastic Machining
- Powder Metallurgy Mold
- Die Casting
- Parts Gallery
- Auto Metal Parts
- Machinery Parts
- LED Heatsink
- Building Parts
- Mobile Parts
- Medical Parts
- Electronic Parts
- Tailored Machining
- Bicycle Parts
- Aluminum Machining
- Titanium Machining
- Stainless Steel Machining
- Copper Machining
- Brass Machining
- Super Alloy Machining
- Peek Machining
- UHMW Machining
- Unilate Machining
- PA6 Machining
- PPS Machining
- Teflon Machining
- Inconel Machining
- Tool Steel Machining
- More Material