Interference Checking in CNC Machining of Impellers
In the context of CNC machining, impellers are critical components used in various applications, such as pumps, turbines, and compressors, where fluid movement is required. Impellers are typically made from materials such as aluminum, stainless steel, titanium, and other high-performance alloys, depending on their operating environment and mechanical demands. The precision with which these components are manufactured is vital, as even slight deviations can lead to inefficiency, noise, or mechanical failure. One of the key challenges in machining impellers is interference checking—ensuring that there are no collisions or issues during the manufacturing process, particularly when machining complex geometries.
Definition of Interference Checking
Interference checking in CNC machining refers to the process of identifying and resolving potential conflicts between the toolpath, cutting tools, and part geometry during machining. It ensures that tools do not collide with the part or with fixtures, and that all necessary cutting movements are feasible given the constraints of the machine. In the case of impellers, interference checking also involves ensuring that the cutting tool can reach all necessary features of the part without violating tool constraints or machine limits. This is particularly important because impellers often feature intricate, multi-axis geometries that require precision and careful handling to achieve the desired shape.
The Importance of Interference Checking in CNC Machining of Impellers
The primary goal of interference checking is to optimize the efficiency of the machining process while preventing tool damage, part deformation, and production downtime. Impellers often have complex curves, blades, and other delicate features that are difficult to machine with traditional methods. CNC machining provides the precision required for these components, but also introduces the challenge of ensuring the machining tools do not interfere with the geometry of the part or its support structures.
CNC Machining Process for Impellers
CNC machining of impellers typically involves several stages, including material preparation, rough machining, semi-finishing, and finishing. During each stage, interference checking plays a critical role in preventing errors that could lead to costly rework or tool damage. CNC machines can be programmed to automatically check for interference by using specialized software or by manually inspecting the toolpath and part geometry.
Software for Interference Checking
Many modern CNC systems and CAM (Computer-Aided Manufacturing) software suites are equipped with interference checking functions. These software tools simulate the machining process to detect any potential collisions between the cutting tool, part, and fixture. The most common types of software used for interference checking include:
- CATIA
- Mastercam
- Siemens NX
- Autodesk Fusion 360
These tools create a 3D model of the entire machining process, which allows engineers to virtually check for interference before physical machining begins. In addition, these software programs allow for optimization of the machining strategy to avoid tool conflicts and improve the overall efficiency of the process.
Types of Interference in CNC Machining of Impellers
Interference can occur in various forms during CNC machining of impellers, and understanding these potential sources of conflict is essential for developing effective mitigation strategies.
-
Tool-to-Part Interference This type of interference occurs when the cutting tool collides with the part being machined. For impellers, this typically happens due to the complex shape of the blades and the tight tolerances required in the finished part. Improper tool selection, incorrect toolpath programming, or insufficient tool offset can cause this issue.
-
Tool-to-Fixture Interference When machining complex parts like impellers, the fixture holding the part may obstruct the cutting tool's movement. Improper fixture design or incorrect positioning can lead to collisions between the cutting tool and fixture, resulting in tool damage or part deformation.
-
Tool-to-Tool Interference In some cases, interference can occur between different cutting tools. This is particularly true when multi-tool setups are used or when tools are switched in the middle of the machining process. Proper sequencing of tool changes and optimal toolpath strategies are essential to minimize this type of interference.
-
Axis Limitation Interference CNC machines often have specific axis limits (e.g., X, Y, Z, A, B, C) within which the tools can move. Interference can occur when the toolpath exceeds these limits, causing the tool to hit the machine’s physical components or reach areas it cannot access. This type of interference is particularly relevant in multi-axis machining, where the part and tool are rotated during machining.
-
Part-to-Part Interference In high-volume production, multiple impellers may be machined simultaneously. If these parts are too close together or improperly spaced in the fixture, collisions can occur between parts. This is a common issue in the production of identical parts using multi-part fixtures.
Techniques for Interference Checking in CNC Machining of Impellers
Several techniques are employed in the CNC machining process to avoid interference:
- Toolpath Simulation: Before starting the actual machining process, toolpath simulation is used to virtually detect any collisions. This process allows operators to verify the tool's trajectory and make adjustments to avoid interference.
- Use of Specialized Software: Advanced CAM software provides a more accurate interference checking process by simulating the entire machining cycle, taking into account the specific tool, part geometry, and machine constraints.
- Manual Inspection: For smaller shops or when advanced software is unavailable, manual inspection of toolpaths may be performed using visual inspection methods, or through the use of physical models or mock-ups to check for potential issues.
- Collision Detection Sensors: Some CNC machines are equipped with built-in sensors that detect and stop the machine if an impending collision is detected. This provides an additional layer of safety, particularly in cases where a part or tool might move unexpectedly.
Common Issues Encountered During Impeller Machining
Despite thorough interference checking, several common issues can still arise during the CNC machining of impellers. These include:
- Vibration and Chatter: High-speed machining of impellers can lead to vibrations that affect tool accuracy and finish quality. Excessive vibration can cause interference between the tool and part, leading to dimensional inaccuracies or surface imperfections.
- Tool Wear: Due to the complex geometries of impellers, cutting tools are subjected to significant wear. Over time, worn-out tools can cause collisions with the part or fixture, leading to errors in machining.
- Tool Deflection: High cutting forces can cause tool deflection, particularly when machining large impellers with thin blades. This deflection can result in interference, especially when tight tolerances are required.
- Thermal Expansion: The heat generated during the cutting process can cause the material to expand. If not compensated for, this thermal expansion can lead to interference between the part and tool, affecting part geometry and fit.
Tables for Comparison
Below are detailed tables comparing various interference checking methods, their advantages, and their limitations.
Method | Advantages | Limitations |
---|---|---|
Toolpath Simulation |
- Highly accurate - Allows early detection of issues - Saves time and cost in production |
- Requires high-performance software - Dependent on accurate CAD models |
Specialized Software |
- Advanced features for multi-axis machining - Can simulate complex geometries and tool paths |
- Expensive licensing - Requires trained operators |
Manual Inspection |
- Low cost - Can be done with minimal equipment |
- Time-consuming - Prone to human error |
Collision Detection Sensors |
- Immediate feedback and prevention of damage - Improves safety |
- Expensive - May not detect all types of interference |
Conclusion
Interference checking is a crucial part of CNC machining, particularly when producing complex parts like impellers. The use of advanced simulation software, proper tool selection, and careful process planning can significantly reduce the likelihood of interference and improve machining efficiency. With the continued development of software and sensor technologies, the ability to predict and avoid interference in CNC machining will only improve, leading to higher-quality impellers and more efficient manufacturing processes.
Reprint Statement: If there are no special instructions, all articles on this site are original. Please indicate the source for reprinting:https://www.cncmachiningptj.com/,thanks!
3, 4 and 5-axis precision CNC machining services for aluminum machining, beryllium, carbon steel, magnesium, titanium machining, Inconel, platinum, superalloy, acetal, polycarbonate, fiberglass, graphite and wood. Capable of machining parts up to 98 in. turning dia. and +/-0.001 in. straightness tolerance. Processes include milling, turning, drilling, boring, threading, tapping, forming, knurling, counterboring, countersinking, reaming and laser cutting. Secondary services such as assembly, centerless grinding, heat treating, plating and welding. Prototype and low to high volume production offered with maximum 50,000 units. Suitable for fluid power, pneumatics, hydraulics and valve applications. Serves the aerospace, aircraft, military, medical and defense industries.PTJ will strategize with you to provide the most cost-effective services to help you reach your target,Welcome to Contact us ( sales@pintejin.com ) directly for your new project.
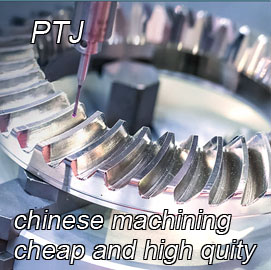
- 5 Axis Machining
- Cnc Milling
- Cnc Turning
- Machining Industries
- Machining Process
- Surface Treatment
- Metal Machining
- Plastic Machining
- Powder Metallurgy Mold
- Die Casting
- Parts Gallery
- Auto Metal Parts
- Machinery Parts
- LED Heatsink
- Building Parts
- Mobile Parts
- Medical Parts
- Electronic Parts
- Tailored Machining
- Bicycle Parts
- Aluminum Machining
- Titanium Machining
- Stainless Steel Machining
- Copper Machining
- Brass Machining
- Super Alloy Machining
- Peek Machining
- UHMW Machining
- Unilate Machining
- PA6 Machining
- PPS Machining
- Teflon Machining
- Inconel Machining
- Tool Steel Machining
- More Material