The Selection And Application Of Large Automobile Panel Die Machining Tools
Large automobile cover molds are critical components in the automotive manufacturing industry, used to shape exterior panels such as hoods, doors, roofs, and fenders. These molds, often referred to as "cover molds" or "panel molds," are characterized by their expansive size, complex geometries, and stringent surface quality requirements. The machine tools employed in their processing must meet high standards of precision, rigidity, and efficiency to accommodate the demands of modern automotive production. This article explores the selection and application of machine tools for processing large automobile cover molds, delving into the technical considerations, machine types, cutting tool choices, and practical applications that define this specialized field.
Overview of Large Automobile Cover Molds
In automotive manufacturing, cover molds are used to form thin steel or aluminum sheets into the curved, aesthetically critical exterior panels of vehicles. These components typically range from 1 to 3 meters in length and width, with thicknesses often less than 1 mm after forming. The molds themselves are significantly larger and heavier, often weighing several tons and requiring substantial machining envelopes. The complexity arises from the need to replicate free-form surfaces with tight tolerances (typically ±0.05 mm) and high surface finishes (Ra 0.8 µm or better), as these panels are visible to consumers and must resist deformation under operational stresses.
The production of cover molds involves multiple machining stages: roughing, semi-finishing, finishing, and sometimes post-processing like polishing or coating. Each stage demands specific machine tool capabilities, influenced by factors such as material properties (commonly tool steel, cast iron, or aluminum), mold size, and production volume. The automotive industry's shift toward lightweight materials, such as high-strength steels and aluminum alloys, further complicates machining requirements, necessitating advanced machine tools capable of handling diverse material behaviors.
Key Considerations in Machine Tool Selection
Selecting machine tools for large automobile cover mold processing involves balancing technical specifications with practical manufacturing needs. The following factors are paramount:
1. Machine Rigidity and Stability
Large molds exert significant cutting forces and vibrations during machining, particularly in roughing operations. Machine rigidity—determined by the bed, column, and spindle design—is essential to minimize deflection and ensure dimensional accuracy. Vibration damping is critical, as oscillations can lead to chatter marks on the mold surface, compromising finish quality. Modern machines often incorporate cast iron or polymer concrete bases to enhance stability, with bridge-type or gantry configurations preferred for their superior rigidity over traditional C-frame designs.
2. Spindle Speed and Power
Spindle characteristics dictate the machine’s ability to handle various cutting conditions. For roughing, high torque at low speeds (e.g., 50–500 RPM) is necessary to remove bulk material efficiently, requiring spindle power upwards of 30–50 kW. Finishing, however, demands high speeds (10,000–20,000 RPM or more) to achieve smooth surfaces with small stepovers, often using ball-end mills. Machines with dual-range spindles or interchangeable heads offer versatility across these operations.
3. Working Envelope and Axis Configuration
The size of large cover molds necessitates expansive X, Y, and Z travel ranges, typically exceeding 2,000 mm × 1,500 mm × 1,000 mm. Three-axis machines suffice for simpler molds, but five-axis configurations are increasingly standard for complex, multi-angle surfaces. Five-axis machining reduces setup times, improves tool access to undercuts, and enhances surface quality by maintaining optimal tool orientation relative to the workpiece.
4. Control Systems and Programming
Advanced CNC systems are integral for processing free-form surfaces. High block look-ahead (e.g., 1,000 blocks) and fast processing speeds ensure smooth toolpath execution, minimizing dwell marks. Systems like Siemens SINUMERIK 840D or FANUC 31i support complex mold programs, often exceeding 100 MB, and integrate with CAM software (e.g., NX, Mastercam) for precise toolpath generation. Thermal compensation features adjust for environmental changes, critical during long machining cycles spanning days.
5. Chip Management and Coolant Systems
Large molds generate substantial chip volumes, especially in roughing. Effective chip evacuation—via conveyors, augers, or high-pressure coolant—prevents recutting and tool wear. Coolant choice impacts thermal stability and surface finish; flood coolant is common, but high-pressure through-spindle coolant (e.g., 70 bar) enhances chip removal and tool life in finishing operations. Minimum quantity lubrication (MQL) is an emerging alternative, reducing thermal shock in high-speed cuts.
6. Tooling Compatibility
Machine tools must accommodate a range of cutting tools, from large-diameter face mills (Ø100–200 mm) for roughing to small ball-end mills (Ø6–12 mm) for finishing. Automatic tool changers (ATC) with capacities of 30–120 tools streamline operations, while tool length and diameter constraints (e.g., max 400 mm length) influence machine selection.
Types of Machine Tools for Cover Mold Processing
Several machine tool types are suited to large cover mold processing, each with distinct advantages and limitations. Below is an overview of the primary options:
CNC Milling Machines
CNC milling machines, particularly vertical machining centers (VMCs) and horizontal machining centers (HMCs), are foundational for mold processing. VMCs offer cost-effective solutions for smaller molds, with typical table sizes of 1,500 mm × 800 mm and spindle powers of 15–30 kW. HMCs, with pallet changers and larger envelopes (e.g., 2,500 mm × 2,000 mm), excel in high-volume production, reducing coolant and tool costs through gravity-assisted chip removal.
Gantry and Bridge-Type Machining Centers
Gantry and bridge-type machines dominate large mold machining due to their expansive working areas (up to 6,000 mm × 3,000 mm) and robust construction. These machines, often five-axis, provide high rigidity via dual-column designs, supporting spindle powers of 40–100 kW and speeds up to 24,000 RPM. Brands like DMG Mori (DMU series) and Makino (MCC series) exemplify this category, offering precision for intricate mold contours.
High-Speed Machining (HSM) Centers
HSM centers prioritize spindle speeds (20,000–40,000 RPM) and feed rates (up to 60 m/min), ideal for finishing operations requiring fine surface finishes. Their lightweight spindles sacrifice some torque, limiting roughing efficiency, but excel in semi-finishing and finishing with small tools. Examples include GF Machining Solutions’ Mikron HSM series.
Electrical Discharge Machines (EDM)
While not traditional cutting tools, EDM systems (e.g., sinker EDM) complement milling by refining intricate details or hard-to-machine areas. They use electrical sparks to erode material, achieving tolerances of ±0.01 mm, but are slower and typically reserved for post-milling finishing.
Cutting Tool Selection
Cutting tools are the interface between the machine and workpiece, directly influencing efficiency and quality. Selection depends on machining stage, material, and desired outcome.
Roughing Tools
- Face Mills: Large-diameter (Ø100–200 mm) face mills with carbide inserts (e.g., Sandvik Coromant R245) remove material rapidly, with cutting depths of 3–6 mm and feed rates of 0.2–0.5 mm/tooth.
- Corn Mills: Tapered tools (Ø20–50 mm) with multiple flutes handle deep cavities, balancing rigidity and chip evacuation.
Semi-Finishing Tools
- Ball-End Mills: Medium-diameter (Ø10–20 mm) carbide ball-end mills smooth transitions, with stepovers of 0.5–1 mm and speeds of 8,000–12,000 RPM.
- Bull-Nose Mills: Flat-bottomed with corner radii, these tools (Ø12–25 mm) offer stability for larger stepovers (1–2 mm).
Finishing Tools
- Small Ball-End Mills: Ø6–12 mm tools with high flute counts (4–6) and coatings (e.g., TiAlN) achieve Ra 0.8 µm finishes at 15,000–20,000 RPM and stepovers of 0.1–0.3 mm.
- PCD Tools: Polycrystalline diamond tools provide exceptional wear resistance for aluminum molds, though at higher cost.
Comparative Analysis of Machine Tools
To aid selection, the following tables compare key machine tool types based on technical specifications and application suitability.
Table 1: Technical Specifications Comparison
Machine Type | Work Envelope (mm) | Spindle Speed (RPM) | Spindle Power (kW) | Axis Config. | Rigidity Rating | Cost Range (USD) |
---|---|---|---|---|---|---|
VMC (e.g., Haas VF-6) | 1,626 × 813 × 762 | 8,000–15,000 | 22–30 | 3-axis | Moderate | 100,000–200,000 |
HMC (e.g., Mazak HCN-6800) | 2,500 × 2,000 × 1,200 | 10,000–18,000 | 30–45 | 4-axis | High | 250,000–400,000 |
Gantry (e.g., DMU 200) | 2,000 × 1,800 × 1,100 | 12,000–24,000 | 40–70 | 5-axis | Very High | 500,000–1,000,000 |
HSM (e.g., Mikron HSM 700) | 700 × 600 × 500 | 20,000–42,000 | 13–20 | 5-axis | Moderate | 300,000–600,000 |
EDM (e.g., AgieCharmilles) | 1,000 × 800 × 600 | N/A | N/A | N/A | N/A | 150,000–300,000 |
Notes: Rigidity rating is qualitative, based on structural design and material. Cost varies with options and region.
Table 2: Application Suitability Comparison
Machine Type | Roughing | Semi-Finishing | Finishing | Complex Geometry | Production Volume |
---|---|---|---|---|---|
VMC | High | Moderate | Low | Low | Low–Moderate |
HMC | Very High | High | Moderate | Moderate | High |
Gantry | Very High | Very High | High | Very High | Moderate–High |
HSM | Low | High | Very High | High | Low–Moderate |
EDM | N/A | Low | High | Very High | Low |
Notes: Suitability reflects efficiency and quality outcomes for large cover molds.
Practical Applications and Case Studies
Roughing Large Steel Molds
A typical process for roughing a 2,500 mm × 1,500 mm P20 steel mold involves a gantry machine like the DMG Mori DMU 200. Using a Ø150 mm face mill at 300 RPM, 4 mm depth of cut, and 0.3 mm/tooth feed, material removal rates exceed 500 cm³/min. The machine’s 50 kW spindle and high-pressure coolant manage heat and chips, completing roughing in 20–30 hours.
Finishing Aluminum Molds
For an aluminum hood mold, a five-axis HSM center (e.g., Mikron HSM 700) employs a Ø10 mm ball-end mill at 20,000 RPM, 0.2 mm stepover, and 15 m/min feed rate. The process achieves Ra 0.6 µm in 10–15 hours, leveraging the machine’s high-speed spindle and precise control for lightweight material efficiency.
Hybrid EDM-Milling
Complex mold features, such as deep ribs, may combine milling with sinker EDM. After semi-finishing on a gantry machine, EDM refines details over 5–10 hours, ensuring tolerances of ±0.02 mm where milling tools cannot reach.
Technological Advancements
Recent innovations enhance machine tool performance:
- Adaptive Control: Real-time adjustment of feed rates and speeds based on cutting forces, reducing tool wear (e.g., Okuma’s OSP-P300A).
- Additive Manufacturing: Hybrid machines (e.g., Mazak INTEGREX) combine milling with 3D printing for mold repair or feature addition.
- Digital Twins: Virtual models predict machine behavior, optimizing setups and reducing trial runs.
Challenges and Solutions
- Thermal Growth: Long cycles cause expansion; chillers and compensation algorithms mitigate this.
- Tool Wear: High-strength steels accelerate wear; ceramic or CBN tools extend life.
- Cost: High initial investment is offset by automation and reduced finishing time.
Conclusion
The selection and application of machine tools for large automobile cover mold processing require a nuanced understanding of machining dynamics, material properties, and production goals. Gantry and bridge-type machines lead in versatility, while HSM and EDM offer specialized finishing capabilities. By aligning machine specifications with mold requirements and leveraging advanced tools and controls, manufacturers can achieve the precision, efficiency, and scalability demanded by the automotive industry.
Reprint Statement: If there are no special instructions, all articles on this site are original. Please indicate the source for reprinting:https://www.cncmachiningptj.com/,thanks!
3, 4 and 5-axis precision CNC machining services for aluminum machining, beryllium, carbon steel, magnesium, titanium machining, Inconel, platinum, superalloy, acetal, polycarbonate, fiberglass, graphite and wood. Capable of machining parts up to 98 in. turning dia. and +/-0.001 in. straightness tolerance. Processes include milling, turning, drilling, boring, threading, tapping, forming, knurling, counterboring, countersinking, reaming and laser cutting. Secondary services such as assembly, centerless grinding, heat treating, plating and welding. Prototype and low to high volume production offered with maximum 50,000 units. Suitable for fluid power, pneumatics, hydraulics and valve applications. Serves the aerospace, aircraft, military, medical and defense industries.PTJ will strategize with you to provide the most cost-effective services to help you reach your target,Welcome to Contact us ( sales@pintejin.com ) directly for your new project.
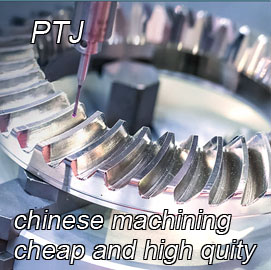
- 5 Axis Machining
- Cnc Milling
- Cnc Turning
- Machining Industries
- Machining Process
- Surface Treatment
- Metal Machining
- Plastic Machining
- Powder Metallurgy Mold
- Die Casting
- Parts Gallery
- Auto Metal Parts
- Machinery Parts
- LED Heatsink
- Building Parts
- Mobile Parts
- Medical Parts
- Electronic Parts
- Tailored Machining
- Bicycle Parts
- Aluminum Machining
- Titanium Machining
- Stainless Steel Machining
- Copper Machining
- Brass Machining
- Super Alloy Machining
- Peek Machining
- UHMW Machining
- Unilate Machining
- PA6 Machining
- PPS Machining
- Teflon Machining
- Inconel Machining
- Tool Steel Machining
- More Material