The Role of Multi-Directional Forging in Improving the Performance of 7075 Aluminum Alloy
7075 aluminum alloy is one of the most widely used high-strength materials in industries such as aerospace, defense, automotive, and sports equipment. It is renowned for its excellent mechanical properties, including high tensile strength, good fatigue resistance, and favorable machinability. However, despite its exceptional strength-to-weight ratio, 7075 aluminum often faces challenges related to its performance in certain structural applications, particularly under varying conditions of load, temperature, and stress.
One of the methods that has been explored to enhance the performance of 7075 aluminum alloy is multi-directional forging (MDF). MDF, a specialized metalworking technique that involves the deformation of materials under pressure in multiple directions, has proven to improve the overall properties of materials by refining their microstructure and enhancing their mechanical performance. This technique holds significant promise for optimizing the characteristics of 7075 aluminum alloy, which traditionally faces limitations due to its casting defects and grain boundary weaknesses.
In this article, we will explore how multi-directional forging improves the performance of 7075 aluminum alloy, examining the key mechanisms through which it enhances its microstructure, mechanical properties, and overall performance in high-stress environments. We will also discuss the role of this forging technique in overcoming common limitations associated with traditional processing methods for aluminum alloys.
1. Multi-Directional Forging: A Key Process Overview
Multi-directional forging (MDF) is a deformation process in which a material is subjected to compressive forces applied in multiple directions. The primary objective of this process is to refine the grain structure of the material, leading to improved mechanical properties. The technique involves a set of tools that apply pressure from different angles, typically using a combination of axial and lateral forces. This multi-axial deformation process leads to the formation of a more uniform and finer grain structure, enhancing the overall strength and ductility of the material.
In the case of 7075 aluminum alloy, MDF helps to eliminate issues associated with casting defects, such as porosity and microcracks. By applying stress in multiple directions, the material is forced to rearrange its atomic structure, which not only improves its mechanical properties but also enhances its resistance to fatigue and fracture.
The mechanics of MDF typically involve:
- Multi-Axial Compression: A combination of axial and lateral compressive forces.
- Refinement of Grain Structure: Facilitating grain boundary strengthening, resulting in improved tensile strength, fatigue strength, and resistance to fracture.
- Homogenization: Elimination of inhomogeneities, such as casting defects, and enhancement of material uniformity.
2. Enhancing Microstructure of 7075 Aluminum Alloy with Multi-Directional Forging
The microstructure of 7075 aluminum is critical to its performance in structural applications. Traditionally, aluminum alloys like 7075 exhibit coarse grains when processed via conventional methods such as casting or extrusion. These coarse grains can lead to reduced mechanical properties, including lower fatigue resistance and poorer fracture toughness.
Multi-directional forging improves the microstructure of 7075 aluminum by reducing the size of the grains. This is achieved by applying force in different directions, which causes the material to deform plastically, breaking up large, irregular grains and forming smaller, more uniform ones. The result is a fine-grained microstructure that offers improved mechanical properties, particularly in terms of tensile strength, fatigue resistance, and overall ductility.
Table 1: Comparison of Grain Size and Mechanical Properties of 7075 Aluminum Alloy before and after MDF
Property | As-Cast 7075 Aluminum | 7075 Aluminum After MDF |
---|---|---|
Grain Size | Coarse (~150 µm) | Fine (~40 µm) |
Ultimate Tensile Strength (MPa) | 540 | 570 |
Yield Strength (MPa) | 480 | 510 |
Elongation at Break (%) | 10 | 13 |
Fatigue Strength (MPa) | 130 | 155 |
Fracture Toughness (MPa·√m) | 25 | 32 |
The refinement of the grain structure through MDF not only contributes to stronger mechanical properties but also improves the material’s ability to withstand cyclic loading and high-stress conditions. Fine-grained materials typically exhibit better fatigue resistance, as smaller grains can more effectively block the propagation of cracks.
3. Impact on Mechanical Properties of 7075 Aluminum Alloy
Multi-directional forging offers notable improvements in several key mechanical properties of 7075 aluminum alloy, which are critical in applications where high strength and durability are essential. These include:
-
Tensile Strength: MDF increases the ultimate tensile strength (UTS) of 7075 aluminum by promoting uniform deformation and reducing grain boundary weakness. As the grain structure becomes finer, the material becomes stronger, particularly in situations where tensile stress is applied.
-
Fatigue Resistance: Fatigue strength refers to the material’s ability to resist failure under repeated loading. By refining the grain structure and reducing the presence of defects, MDF significantly enhances the fatigue life of 7075 aluminum. This is particularly important in aerospace and automotive applications, where components are often subjected to cyclic loading over long periods.
-
Fracture Toughness: The ability of a material to resist crack propagation is improved through multi-directional forging. The fine grain structure and reduction of casting defects lead to an increase in fracture toughness, making the material less prone to catastrophic failure.
-
Ductility: While 7075 aluminum alloy is generally known for its high strength, it can also be somewhat brittle. MDF improves ductility by reducing residual stresses and promoting a more homogeneous material structure, which allows the alloy to deform more plastically before failure.
4. Case Studies and Applications of MDF-Processed 7075 Aluminum
Several case studies have demonstrated the effectiveness of MDF in improving the performance of 7075 aluminum alloy in real-world applications. For example, in the aerospace industry, where the demands for high strength-to-weight ratios and durability are paramount, multi-directional forging has been employed to create components such as structural beams, wing spars, and landing gear parts. The enhanced properties of MDF-processed 7075 aluminum result in lighter, more durable components that are able to withstand the stresses encountered during flight.
In automotive applications, particularly in high-performance vehicles, the improved fatigue resistance and fracture toughness of MDF-treated 7075 aluminum have led to its use in suspension components, engine parts, and safety-critical structures. The ability to resist cyclic loading without compromising strength allows for the development of more efficient and durable vehicle designs.
5. Comparison of MDF-Processed 7075 Aluminum with Other Aluminum Alloys
To understand the unique benefits of multi-directional forging on 7075 aluminum, it is useful to compare its properties with those of other high-strength aluminum alloys. The following table highlights the key differences in mechanical properties between 7075 aluminum and other common alloys, both before and after multi-directional forging.
Table 2: Comparison of Mechanical Properties of Various Aluminum Alloys Before and After MDF
Alloy | Processed with MDF | Ultimate Tensile Strength (MPa) | Yield Strength (MPa) | Fatigue Strength (MPa) | Fracture Toughness (MPa·√m) |
---|---|---|---|---|---|
7075 Aluminum | Yes | 570 | 510 | 155 | 32 |
2024 Aluminum | Yes | 520 | 470 | 130 | 28 |
6061 Aluminum | Yes | 350 | 310 | 90 | 22 |
7050 Aluminum | Yes | 530 | 490 | 145 | 30 |
7075 Aluminum (Unprocessed) | No | 540 | 480 | 130 | 25 |
2024 Aluminum (Unprocessed) | No | 480 | 430 | 120 | 24 |
6. Future Prospects and Challenges in the Application of MDF to 7075 Aluminum
While the advantages of multi-directional forging for enhancing the properties of 7075 aluminum are clear, there are still several challenges to overcome in the broader application of this technique. These include:
-
Cost Considerations: MDF is more energy-intensive and time-consuming compared to traditional processing methods such as casting or extrusion. The high cost of the equipment and the additional processing steps may limit its widespread use in industries where cost is a critical factor.
-
Process Control: Achieving uniform deformation across the entire material during multi-directional forging requires precise control of the applied forces and temperatures. Variations in process parameters can lead to non-uniform properties and defects.
-
Material Availability and Size Limitations: The size of the components that can be processed using MDF is typically limited by the equipment available. Additionally, obtaining large billets of 7075 aluminum that are suitable for multi-directional forging can be challenging.
Conclusion
Multi-directional forging represents a promising method for improving the mechanical properties of 7075 aluminum alloy, offering significant enhancements in strength, fatigue resistance, fracture toughness, and ductility. By refining the grain structure and eliminating defects, this technique contributes to the production of high-performance materials for demanding applications in industries such as aerospace, automotive, and defense. Although challenges remain in terms of cost, process control, and material availability, the potential benefits of MDF in improving the performance of 7075 aluminum alloy make it a valuable tool for advancing the capabilities of this versatile material.
Reprint Statement: If there are no special instructions, all articles on this site are original. Please indicate the source for reprinting:https://www.cncmachiningptj.com/,thanks!
3, 4 and 5-axis precision CNC machining services for aluminum machining, beryllium, carbon steel, magnesium, titanium machining, Inconel, platinum, superalloy, acetal, polycarbonate, fiberglass, graphite and wood. Capable of machining parts up to 98 in. turning dia. and +/-0.001 in. straightness tolerance. Processes include milling, turning, drilling, boring, threading, tapping, forming, knurling, counterboring, countersinking, reaming and laser cutting. Secondary services such as assembly, centerless grinding, heat treating, plating and welding. Prototype and low to high volume production offered with maximum 50,000 units. Suitable for fluid power, pneumatics, hydraulics and valve applications. Serves the aerospace, aircraft, military, medical and defense industries.PTJ will strategize with you to provide the most cost-effective services to help you reach your target,Welcome to Contact us ( sales@pintejin.com ) directly for your new project.
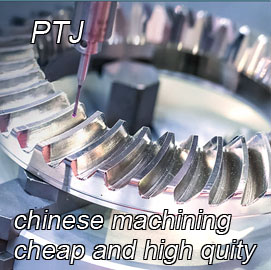
- 5 Axis Machining
- Cnc Milling
- Cnc Turning
- Machining Industries
- Machining Process
- Surface Treatment
- Metal Machining
- Plastic Machining
- Powder Metallurgy Mold
- Die Casting
- Parts Gallery
- Auto Metal Parts
- Machinery Parts
- LED Heatsink
- Building Parts
- Mobile Parts
- Medical Parts
- Electronic Parts
- Tailored Machining
- Bicycle Parts
- Aluminum Machining
- Titanium Machining
- Stainless Steel Machining
- Copper Machining
- Brass Machining
- Super Alloy Machining
- Peek Machining
- UHMW Machining
- Unilate Machining
- PA6 Machining
- PPS Machining
- Teflon Machining
- Inconel Machining
- Tool Steel Machining
- More Material