Positioning accuracy of CNC machine tools
A comprehensive analysis of the positioning accuracy of CNC machine tools is crucial for understanding their role in modern manufacturing processes. CNC (Computer Numerical Control) machines are widely used in industries such as aerospace, automotive, medical devices, and electronics due to their precision, repeatability, and versatility. Positioning accuracy refers to the ability of the machine tool to move its tool or workpiece to a specified location within a defined tolerance range. This article will explore the different factors influencing positioning accuracy, methods of measurement, sources of error, and techniques for improving accuracy in CNC machine tools. Detailed tables will also be provided for comparison.
Introduction to Positioning Accuracy in CNC Machine Tools
Positioning accuracy is the degree to which a CNC machine tool can position its axis or tool in space relative to a given coordinate system. It is a fundamental requirement for high-quality machining operations, especially when dealing with complex parts that require tight tolerances. The positioning accuracy of a CNC machine tool is influenced by multiple factors, including mechanical components, control systems, environmental conditions, and the cutting process itself.
CNC machines, which include vertical and horizontal machining centers, lathes, mills, and grinders, all rely on feedback loops between the machine’s moving components (such as linear axes, rotary axes, and tool changers) and the machine controller. In this context, positioning accuracy becomes a vital measure of the machine’s overall performance.
Key Factors Affecting Positioning Accuracy
-
Mechanical Components: The mechanical structure of the CNC machine, including the frame, spindle, slideways, and ball screws, plays a major role in determining the positioning accuracy. The rigidity and thermal stability of the machine components directly affect the precision with which the tool or workpiece can be moved.
- Spindle: The spindle's stability under load and its rotational accuracy are vital to precise tool positioning.
- Linear Guides and Ball Screws: These components guide the machine’s axes and ensure smooth motion. Their accuracy, wear resistance, and alignment significantly impact positioning performance.
- Ball Screw Backlash: A common source of error is backlash, which refers to the slight movement that occurs when the direction of motion is reversed.
-
Control System: CNC machines are controlled by sophisticated software algorithms and feedback systems that work together to drive the machine’s axes with high precision. The accuracy of these systems is determined by several factors:
- Feedback Systems: CNC machines typically use encoders and resolvers to measure position and send feedback to the controller. The resolution and accuracy of these encoders are crucial for achieving high positioning accuracy.
- Interpolation Algorithms: These algorithms are used to control the motion of the machine tool. The precision with which the controller interprets the tool path and adjusts the machine’s movement can have a direct impact on accuracy.
- Servo Motors: The type of servo motor and the quality of its control system can influence the speed, smoothness, and precision of positioning.
-
Thermal Effects: CNC machines generate heat due to friction, cutting forces, and the operation of electrical components. The thermal expansion of metal components can cause dimensional changes, which in turn affect positioning accuracy. These thermal effects can occur both during the machining process and when the machine is idle.
- Thermal Drift: This is the gradual movement of machine components caused by temperature fluctuations. It is especially noticeable in machines with long operational periods.
- Compensation Systems: Many modern CNC machines are equipped with thermal compensation systems to mitigate the effects of thermal distortion. These systems adjust the machine's movement based on temperature measurements, improving positioning accuracy.
-
Load and Dynamic Effects: When machining parts, the cutting forces and tool interactions can introduce dynamic effects that affect positioning accuracy. The machine's structure must be sufficiently rigid to withstand these forces and maintain precise tool positioning.
- Cutting Forces: The forces generated during the cutting process can cause deflection of the machine tool, which in turn affects positioning accuracy.
- Tool and Workpiece Interaction: The interaction between the tool and the workpiece, including vibrations, can lead to inaccuracies in positioning.
-
Environmental Factors: External environmental conditions, such as humidity, vibration, and air quality, can impact the positioning accuracy of CNC machines. For instance, high humidity levels can cause components to expand or contract, leading to dimensional changes.
- Vibration: Vibrations from the surrounding environment or from within the machine can interfere with precise movements. Anti-vibration systems are often used to mitigate these effects.
- Cleanliness: Dust and particles in the environment can cause wear and tear on moving parts, leading to degraded accuracy over time.
Measuring Positioning Accuracy
To assess the positioning accuracy of a CNC machine tool, several measurement techniques are employed:
-
Laser Interferometry: Laser interferometry is one of the most accurate methods for measuring linear positioning accuracy. It uses the interference of light waves to detect small displacements of the machine’s axes. This method can measure deviations with sub-micron precision, making it ideal for high-accuracy measurements.
-
Ball Bar Testing: The ball bar test involves attaching a ball bar to the CNC machine’s spindle and measuring deviations as the machine moves through a circular motion. This test provides valuable data on the machine’s geometrical accuracy and identifies errors such as backlash, squareness, and straightness deviations.
-
Straightness and Squareness Testing: Straightness and squareness tests are performed using precision measuring instruments such as dial indicators or electronic levels. These tests are crucial for detecting misalignment between machine axes and identifying geometric errors.
-
Heidenhain and Renishaw Systems: Both Heidenhain and Renishaw offer high-precision linear measurement systems that can be used for determining the accuracy of CNC machine tools. These systems rely on optical or inductive technology to provide real-time feedback on positioning accuracy.
Types of Errors and Their Impact on Positioning Accuracy
Several types of errors can degrade the positioning accuracy of CNC machines:
-
Geometric Errors: Geometric errors occur when there are deviations in the ideal machine geometry. These include:
- Straightness Error: This occurs when the machine’s linear axes are not perfectly straight.
- Squareness Error: Misalignment of the machine’s axes can lead to squareness errors.
- Flatness and Parallelism Errors: These errors occur when the machine’s surfaces deviate from perfect flatness or parallelism.
-
Backlash: Backlash is the slight delay in motion when a machine changes direction. It occurs due to the clearance between the ball screw nut and the screw itself. Backlash results in positioning errors, especially during rapid directional changes.
-
Creep and Drift: Creep refers to the gradual movement of the machine tool over time due to thermal or load-induced deformation. Drift is similar but is often caused by the machine’s internal electrical or mechanical systems.
-
Inertia Errors: Inertia errors occur due to the mass of the moving parts. When high speeds or rapid acceleration/deceleration are involved, the inertia of the moving parts can cause overshooting or undershooting of the desired position.
-
Control System Latency: Latency in the control system can introduce errors in positioning, especially in systems with complex algorithms or slow feedback loops. This can cause the machine to slightly overshoot or undershoot its intended position.
Methods for Improving Positioning Accuracy
-
Thermal Management: CNC machines can be equipped with thermal compensation systems that adjust the movement of the machine based on temperature data. These systems help reduce the effects of thermal expansion and improve positioning accuracy.
-
High-Precision Feedback Systems: Upgrading the feedback systems, such as using high-resolution encoders and more accurate laser interferometry, can significantly improve the accuracy of the positioning system.
-
Ball Screw Optimization: Using ball screws with high accuracy, low backlash, and minimal wear can reduce mechanical errors and improve overall positioning precision. Advanced designs, such as preloaded ball screws, can further reduce backlash and improve repeatability.
-
Machine Calibration and Maintenance: Regular calibration and maintenance are essential for ensuring the continued performance of the CNC machine. This includes checking for mechanical wear, recalibrating feedback systems, and ensuring that all components are aligned and functioning optimally.
-
Vibration Isolation: Implementing vibration isolation measures, such as dampers and machine mounts, can help reduce the effects of external vibrations and improve positioning accuracy.
-
Machine Structural Improvements: Enhancing the machine’s structural rigidity can reduce deflection during cutting and improve overall positioning accuracy. This may include using materials with lower thermal expansion coefficients or adding reinforcing structures to the machine frame.
Detailed Tables for Comparison
Table 1: Comparison of CNC Machine Tool Positioning Accuracy Measurement Techniques
Measurement Technique | Accuracy Range | Equipment Required | Applications |
---|---|---|---|
Laser Interferometry | 0.01 µm to 1 µm | Laser interferometer | High-precision measurement in laboratories |
Ball Bar Test | 0.01 mm to 0.1 mm | Ball bar | Identifying geometric and mechanical errors |
Heidenhain System | 0.1 µm to 1 µm | Linear scale system | Real-time feedback on positioning accuracy |
Straightness/Squareness | 0.01 mm to 0.1 mm | Dial indicators, levels | Alignment and geometric error detection |
Table 2: Common Errors Affecting Positioning Accuracy
Error Type | Source | Impact on Accuracy | Mitigation Methods |
---|---|---|---|
Geometric Errors | Misalignment of axes, component wear | Decreased dimensional precision | Regular calibration, machine redesign |
Backlash | Play between moving components | Position overshoot/undershoot | Use of backlash compensation, preloaded ball screws |
Thermal Expansion | Heat generated by cutting process | Dimensional changes over time | Thermal compensation systems, cooling systems |
Control System Latency | Delay in feedback processing | Inaccurate positioning | Faster feedback systems, optimized algorithms |
Inertia Effects | Mass of moving components | Overshoot during rapid movements | Reduce acceleration/deceleration rates, improve rigidity |
Conclusion
Positioning accuracy is a critical factor in the performance of CNC machine tools. It impacts the quality of parts produced, especially in industries where precision is paramount, such as aerospace, automotive, and medical device manufacturing. By understanding the factors that influence positioning accuracy and employing advanced measurement techniques, manufacturers can ensure that their CNC machines operate at optimal levels. Improvements in mechanical design, control systems, thermal management, and regular maintenance all contribute to enhancing the precision and repeatability of CNC machine tools, thus achieving better overall machining performance.
Reprint Statement: If there are no special instructions, all articles on this site are original. Please indicate the source for reprinting:https://www.cncmachiningptj.com/,thanks!
3, 4 and 5-axis precision CNC machining services for aluminum machining, beryllium, carbon steel, magnesium, titanium machining, Inconel, platinum, superalloy, acetal, polycarbonate, fiberglass, graphite and wood. Capable of machining parts up to 98 in. turning dia. and +/-0.001 in. straightness tolerance. Processes include milling, turning, drilling, boring, threading, tapping, forming, knurling, counterboring, countersinking, reaming and laser cutting. Secondary services such as assembly, centerless grinding, heat treating, plating and welding. Prototype and low to high volume production offered with maximum 50,000 units. Suitable for fluid power, pneumatics, hydraulics and valve applications. Serves the aerospace, aircraft, military, medical and defense industries.PTJ will strategize with you to provide the most cost-effective services to help you reach your target,Welcome to Contact us ( sales@pintejin.com ) directly for your new project.
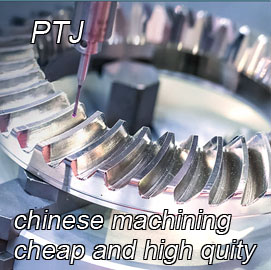
- 5 Axis Machining
- Cnc Milling
- Cnc Turning
- Machining Industries
- Machining Process
- Surface Treatment
- Metal Machining
- Plastic Machining
- Powder Metallurgy Mold
- Die Casting
- Parts Gallery
- Auto Metal Parts
- Machinery Parts
- LED Heatsink
- Building Parts
- Mobile Parts
- Medical Parts
- Electronic Parts
- Tailored Machining
- Bicycle Parts
- Aluminum Machining
- Titanium Machining
- Stainless Steel Machining
- Copper Machining
- Brass Machining
- Super Alloy Machining
- Peek Machining
- UHMW Machining
- Unilate Machining
- PA6 Machining
- PPS Machining
- Teflon Machining
- Inconel Machining
- Tool Steel Machining
- More Material