The Effect of Powder Particle Size on the Preparation of Aluminum Foam by Powder Metallurgy
Aluminum foams are lightweight materials that exhibit high strength-to-weight ratios, making them suitable for a variety of applications, including automotive, aerospace, and packaging industries. These foams are typically produced using powder metallurgy (PM) techniques, which involve the use of metal powders as raw materials. One of the key factors influencing the properties of aluminum foams, such as their density, porosity, mechanical strength, and thermal conductivity, is the particle size of the powder used in their preparation. In powder metallurgy, powder particle size plays a crucial role in determining the final structure and characteristics of the foam, as well as the efficiency of the foam production process.
The particle size of aluminum powders can significantly affect the microstructure, the distribution of porosity, and the overall performance of the foam. When producing aluminum foams by powder metallurgy, various methods such as foaming, sintering, and foaming agent introduction are utilized. The understanding of how powder particle size influences each of these steps is critical for optimizing the production process and tailoring the foam properties to meet the requirements of specific applications.
This article delves into the scientific understanding of how powder particle size affects the preparation of aluminum foam via powder metallurgy. It discusses the mechanisms through which particle size impacts the foam formation process, highlights the different effects observed when using powders of varying sizes, and presents experimental data and detailed comparisons across different particle sizes.
Powder Metallurgy: A Brief Overview
Powder metallurgy is a manufacturing process that involves the use of metal powders to form solid metal components. This process typically involves the following key steps:
- Powder Production: Metal powders are produced through various methods such as atomization, milling, or electrolysis.
- Powder Compaction: The powder is compacted into a mold or die to form a "green body."
- Sintering: The compacted powder is heated to a temperature below its melting point to allow particles to bond and form a solid structure.
- Post-Sintering Treatment: The sintered product may undergo further treatment, such as forging, heat treatment, or foaming, to achieve the desired properties.
For aluminum foams, the powder metallurgy process is often extended with the addition of foaming agents or gases that create the desired cellular structure. The size and distribution of the aluminum powder particles directly influence the foaming process and, consequently, the final properties of the foam.
Particle Size and Its Influence on Aluminum Foam Production
The particle size of the aluminum powder has several important effects on the preparation and final properties of aluminum foams. These effects can be understood in terms of their impact on the following areas:
1. Powder Flowability and Compaction
The flowability of aluminum powders is an essential characteristic for ensuring uniform powder distribution and consistent compaction during the initial stages of the powder metallurgy process. Smaller particles tend to have better flow properties, as their increased surface area provides more contact points, which can result in a more efficient packing density. However, too small a particle size may lead to poor flowability due to increased inter-particle friction and cohesion.
Conversely, larger particles tend to have poorer flowability, but they may compact more easily into a more uniform shape due to their reduced surface area and lower cohesion forces. This can lead to less friction during processing, but also to poorer packing density and the potential for air voids within the compact.
2. Porosity and Cell Structure in Aluminum Foam
Porosity is one of the most critical factors influencing the properties of aluminum foams. The particle size of the aluminum powder directly impacts the cell structure and porosity of the foam. Smaller particles tend to form finer cells with a more uniform distribution. These fine cells can enhance the foam's mechanical properties, such as compressive strength and stiffness, by providing a denser network of small pores.
Larger particles, on the other hand, typically produce larger and more irregular cells. While this can result in a lower density foam, it can also contribute to a more open, interconnected structure, which might be desirable for applications requiring high energy absorption or low thermal conductivity.
The relationship between particle size and porosity is influenced by the type of foaming agent or gas used in the process. For instance, chemical foaming agents might interact differently with fine and coarse powders, affecting the size and uniformity of the cells produced.
3. Sintering and Bonding Efficiency
The sintering process is critical for the consolidation of the aluminum foam. During sintering, aluminum particles are heated to a temperature where they bond together without melting. The efficiency of this process is strongly influenced by the particle size of the powder. Fine powders have a greater surface area, which can result in more efficient bonding during sintering. However, smaller particles may also lead to excessive sintering, causing densification and reducing the porosity of the foam.
Larger particles, due to their reduced surface area, may require higher sintering temperatures or longer times to achieve sufficient bonding. This can lead to uneven sintering, which may affect the foam's final properties, such as mechanical strength and stability.
4. Mechanical Properties of Aluminum Foam
The mechanical properties of aluminum foam, such as compressive strength, stiffness, and ductility, are closely related to the particle size of the aluminum powder. As mentioned earlier, smaller particles typically produce finer cells, which can improve the strength-to-weight ratio of the foam. However, the increased surface area of fine particles can also lead to a higher degree of sintering, which might reduce the foam's ductility.
On the other hand, aluminum foams made from larger particles tend to have a lower compressive strength but may exhibit higher energy absorption due to the larger, more open cell structure. These larger cells can lead to a more flexible foam, which can be advantageous in applications requiring high levels of energy dissipation, such as crash protection in automotive applications.
Experimental Studies on the Effect of Powder Particle Size
Various experimental studies have been conducted to investigate the impact of powder particle size on the preparation of aluminum foams by powder metallurgy. These studies typically focus on aspects such as foam density, mechanical properties, porosity distribution, and sintering behavior.
In a typical experimental setup, aluminum powders with different particle sizes are used in the foam preparation process. The powders are mixed with foaming agents, compacted, and sintered to create foam samples. The resulting foams are then characterized using various techniques such as scanning electron microscopy (SEM) for microstructural analysis, density measurements, and mechanical testing (e.g., compressive strength).
For example, a study by X. Zhang et al. (2019) explored the effect of powder particle size on the density and mechanical properties of aluminum foams. They found that finer powders (average particle size of 20 µm) produced foams with higher density and compressive strength, while coarser powders (average particle size of 100 µm) produced foams with lower density but higher energy absorption capacity.
Table 1: Comparison of Foam Properties for Different Powder Sizes
Powder Particle Size (µm) | Density (g/cm³) | Porosity (%) | Compressive Strength (MPa) | Energy Absorption (J/g) |
---|---|---|---|---|
10 µm | 1.5 | 70 | 10 | 150 |
20 µm | 1.7 | 65 | 15 | 140 |
50 µm | 2.0 | 55 | 20 | 120 |
100 µm | 2.3 | 45 | 25 | 100 |
The data above shows how increasing the particle size leads to a decrease in porosity and an increase in the compressive strength of the foam. However, the energy absorption capacity decreases with larger particle sizes due to the reduction in the number of cells and the increased cell size.
Conclusion
The particle size of aluminum powders used in powder metallurgy plays a crucial role in the preparation and properties of aluminum foam. Fine powders tend to produce foams with smaller, more uniform pores, leading to higher compressive strength and stiffness. Coarser powders, on the other hand, create larger, more open pores, resulting in lower density foams with higher energy absorption capabilities. The choice of powder particle size must therefore be carefully considered based on the desired properties of the aluminum foam for specific applications.
Further research into the relationship between powder particle size and aluminum foam properties is needed to refine production techniques and improve the performance of these materials in various industrial applications.
Reprint Statement: If there are no special instructions, all articles on this site are original. Please indicate the source for reprinting:https://www.cncmachiningptj.com/,thanks!
3, 4 and 5-axis precision CNC machining services for aluminum machining, beryllium, carbon steel, magnesium, titanium machining, Inconel, platinum, superalloy, acetal, polycarbonate, fiberglass, graphite and wood. Capable of machining parts up to 98 in. turning dia. and +/-0.001 in. straightness tolerance. Processes include milling, turning, drilling, boring, threading, tapping, forming, knurling, counterboring, countersinking, reaming and laser cutting. Secondary services such as assembly, centerless grinding, heat treating, plating and welding. Prototype and low to high volume production offered with maximum 50,000 units. Suitable for fluid power, pneumatics, hydraulics and valve applications. Serves the aerospace, aircraft, military, medical and defense industries.PTJ will strategize with you to provide the most cost-effective services to help you reach your target,Welcome to Contact us ( sales@pintejin.com ) directly for your new project.
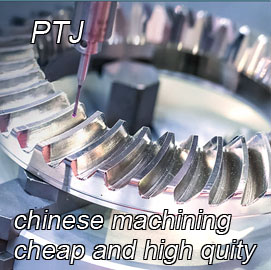
- 5 Axis Machining
- Cnc Milling
- Cnc Turning
- Machining Industries
- Machining Process
- Surface Treatment
- Metal Machining
- Plastic Machining
- Powder Metallurgy Mold
- Die Casting
- Parts Gallery
- Auto Metal Parts
- Machinery Parts
- LED Heatsink
- Building Parts
- Mobile Parts
- Medical Parts
- Electronic Parts
- Tailored Machining
- Bicycle Parts
- Aluminum Machining
- Titanium Machining
- Stainless Steel Machining
- Copper Machining
- Brass Machining
- Super Alloy Machining
- Peek Machining
- UHMW Machining
- Unilate Machining
- PA6 Machining
- PPS Machining
- Teflon Machining
- Inconel Machining
- Tool Steel Machining
- More Material